In many pulse width modulated DC-DC converter topologies, the controllable switches are operated in switch mode where they are required to turn the entire load current on and off during each switching cycle. Under these conditions, the switches are subjected to high switching stresses and power losses. Recently there is an increased interest in the use of resonant type DC-DC converters due to the advantages of high frequency of operation, high efficiency, small size, light weight, reduced Electro Magnetic Interference (EMI) and low component stresses.A novel PFC (Power Factor Corrected) Converter using Zeta DC-DC converter feeding a PMSM drive using a single voltage sensor is proposed for variable speed applications. A single phase supply followed by an uncontrolled bridge rectifier and a Zeta DC-DC converter is used to control the voltage of a DC link capacitor which is lying between the Zeta converter and a VSI (Voltage Source Inverter). The voltage of a dc-link capacitor of zeta converter is controlled to achieve the speed control of PMSM Drive. The zeta converter is working as a front end converter operating in DICM (Discontinuous Inductor Current Mode) and thus using a voltage follower. A sensor less control of PMSM is used to eliminate the requirement of Hall Effect position sensors. Using MATLAB/ Simulink 7.13 environment the model can be simulated to achieve a wide range of speed control with high power factor.
Keywords |
Adjustable Speed drives, DC-DC
Converter, PI Control, PMSM drive, Zeta Converter |
INTRODUCTION |
Modern electronic systems require high quality,[7] small,
lightweight, reliable, and efficient power supplies. Linear
power regulators, whose principle of operation is based on
a voltage or current divider, are inefficient. They are
limited to output voltages smaller than the input voltage. Also, their power density is low because they require
low-frequency (50 or 60 Hz) line transformers and filters.
Linear regulators can, however, provide a very high
quality output voltage. Their main area of application is
at low power levels as low drop-out voltage
(LDO)regulators. Electronic devices in linear regulators
operate in their active (linear) modes. At higher power
levels, switching regulators are used. Switching
regulators use power electronic semiconductor switches
in on and off states. Since there is a small power loss in
those states (low voltage across a switch in the on state,
zero current through a switch in the off state),
switchingregulators can achieve high energy conversion
efficiencies. Modern power electronic switches can
operate at high frequencies. The higher the operating
frequency, the smaller and lighter the transformers, filter
inductors, and capacitors. In addition, dynamic
characteristics of converters improve with increasing
operating frequencies. |
The bandwidth of a control loop is usually
determined by the corner frequency of the output filter.
Therefore, high operating frequencies allow for achieving
a faster dynamic response to rapid changes in the load
current and/or the input voltage. High-frequency
electronic power processors are used in dc–dc power
conversion. |
PROPOSED SPEED CONTROL SCHEME OF
SENSORLESS PMSM DRIVE |
The proposed scheme for the Sensor less PMSM drive
fed by a Zeta based PFC converter operating in DICM
mode is shown in Fig.2.1.The front end Zeta DC-DC
converter maintains the DC link voltage to a set reference
value. Switch of the Zeta converter is to be operated at
high switching frequency for effective control and small
size of components like inductors. A sensor less
approach [12] is used to detect the rotor position for
electronic commutation.A high frequency MOSFET of suitable rating is used in the front end converter for its
high frequencyoperation whereas an IGBT’s (Insulated
Gate Bipolar Transistor) are used in the VSI for low
frequency operation. |
The proposed scheme maintains high power factor and
low THD[10] of the AC source current while controlling
rotor speed equal to the set reference speed. A voltage
follower approach is used for the control of Zeta DC-DC
converter operating in DICM. |
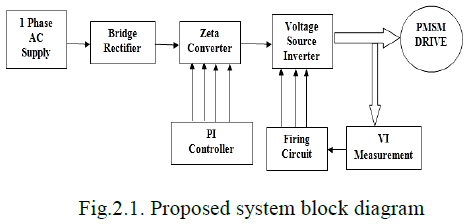 |
The DC link voltage is controlled by a single voltage
sensor. Vdc (sensed DC link voltage) is compared with
Vdc* (reference voltage) to generate an errorsignal which
is the difference of Vdc* and Vdc. The error signal is given
to a PI (Proportional Integral) controller to give a
controlled output. Finally, the controlled output is
compared with the high frequency saw tooth signal to
generate PWM (Pulse Width Modulation) pulse for the
MOSFET of the Zeta converter. |
PRINCIPLE OF OPERATION OF PROPOSED ZETA
CONVERTER |
Vast majority of power converters used nowadays
employ front-end diode bridge rectifiers. Such rectifiers
draw pulsating currents which leave behind a great
amount of harmonics, and considerably low power factor.
For a single converter of this type used with a singlephase
load such as in consumer electronic equipment, the
problems may not seem serious. However, a great number
of those equipment’s in parallel connection at a point of
common coupling (PCC) to draw power simultaneously
introduce some serious effects concerning reactive power
and harmonic. The situations are quite common in offices
and industries. |
winding fly back converter, and the zeta converter.
Among those, the zeta converter, which is originally the
buck-boost type, can be regarded as a fly back type when
an isolated transformer is incorporated. An isolated zeta
converter has some advantages including safety at the
output side, and flexibility for output adjustment. |
Fig.3.1 depicts the circuit diagrams of the
isolated zeta converter such that its operation principle in
the CCM could be readily explained. Fig.3.2 represents
the 1st region of operation in which the switch S is “on”,
and the diode D is “off”. This region takes the time from
0 to d1Ts seconds. |
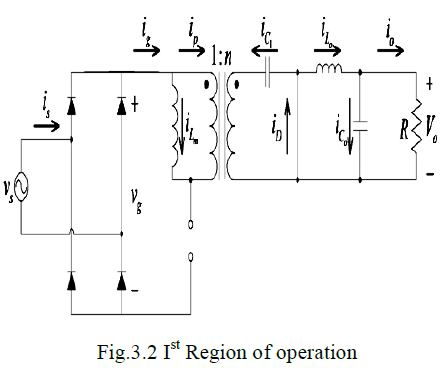 |
The inductor Lm stores the energy received from
the rectifier. The capacitor C1 supplies energy to the load
(R) via the inductor Lo, and the capacitor Co. the currents
through the inductors Lm and Lo increase linearly, while
no current flows through the diode. |
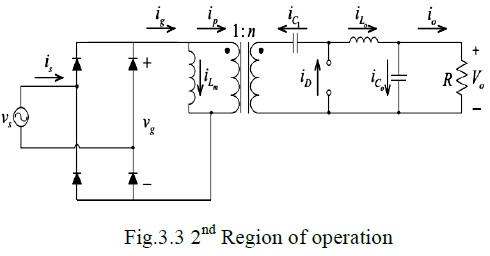 |
Fig.3.3 represents the 2nd operation region in
which the switch S is “off”, and the diode D is “on”. This
region begins at the time d1Ts seconds, and ends by d2Ts
seconds. The diode D is forward biased due to the
voltage across the inductor Lm has reversed polarity,
while the currents iLm and iLo decrease linearly. The
stored energy in the inductor Lm is transferred to the
capacitor C1. The load R receives energy from the
inductor Lo. Hence, the current iD=iC1+iLo. |
STATE SPACE AVERAGED MODEL OF PROPOSED ZETA
CONVERTER |
Considering the operation of the converter during the
on- and off-time intervals denoted aston or d1Ts, and toff or (1-d1) Tsrespectively, the state equations in on switching
cycle can be written as |
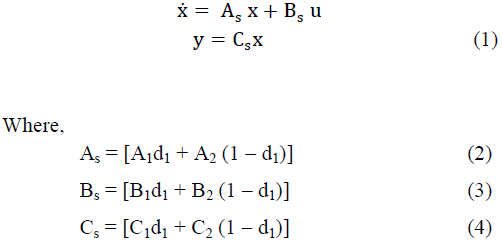 |
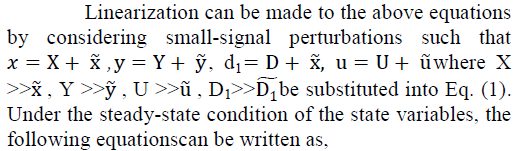 |
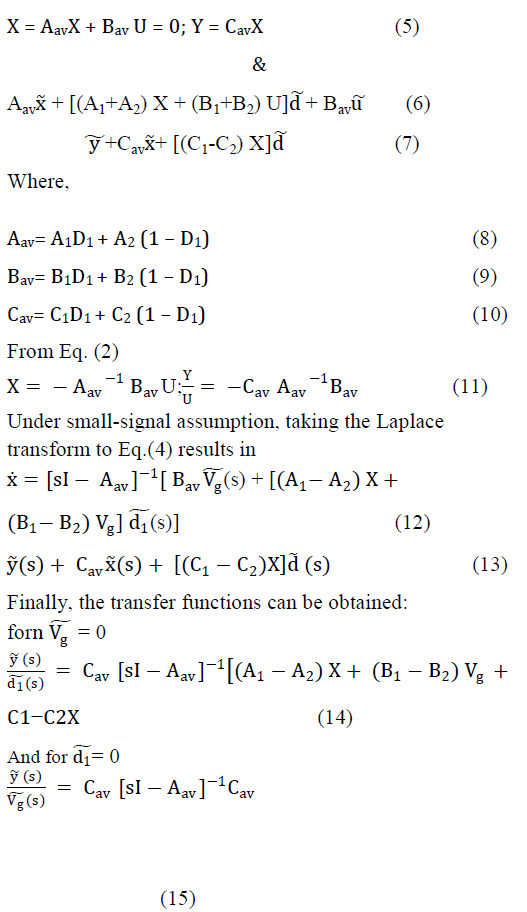 |
MATHEMATICAL MODEL OF THREE PHASE
VOLTAGE SOURCE INVERTER AND PMSM |
1.Mathematical Model of Three Phase VSI |
The PMSM armature winding is to be supplied
from a 3 phase VSI whose power electronics devices
(switches) would be switched according to the rotor
position information for achieving VectorControl. The
power circuit of a typical 3 phase, 2 level VSI [7]
catering to a 3 phase armature winding of a 3 phase AC
motor is shown in Fig.5.2 The inverter devices marked as
T1 , T2 , T3 , T4 , T5 , T6 are to be switched to achieve
Vector-Control as per a Sinusoidal Pulse Width
Modulation (SPWM) strategy. |
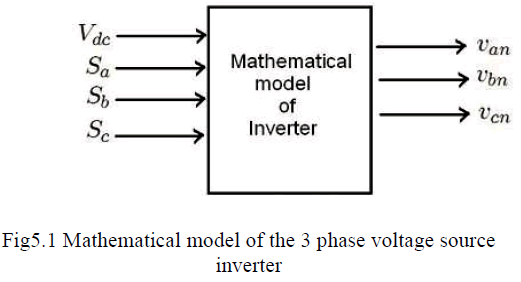 |
The mathematical model of the 3 phase VSI, as
shown in Fig 5.1 as a block, should have the DC link
voltage (Vdc ), the 3 switching functions (Boolean
variables) Sa , Sb and Sc as input variables and should
have the 3 phase voltages van , vbn and vcn as output
variables. The output variables of the inverter will form
as the input phase voltages to be fed to the PMSM
armature winding (Star connected). |
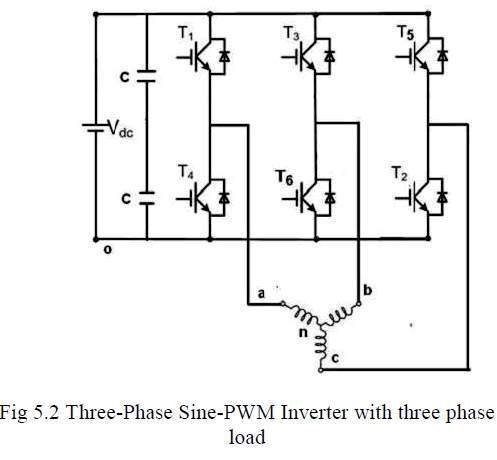 |
Voltages Vao, Vbo and Vco may be represented in terms of
the switching functions as |
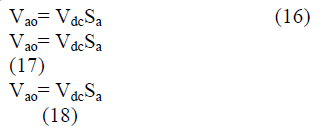 |
Where, Vao is the voltage of point `a' with respect to -
ve DC link bus. Similar nomenclature is also applicable
for other two phases. [7]The 3 phase voltage impressed on
the star connected armature winding of PMSM (these are
output voltage of the inverter) can be represent as, |
 |
where Vno = The voltage of the neutral point `n' with
respect to the point `o' of the DC bus. Van + Vbn + Vcn =
Vao + Vbo + Vco – 3Vno assuming that the machine being
balancedVan + Vbn + Vcn = 0. Hence inverter phase
voltages can be expressed as, |
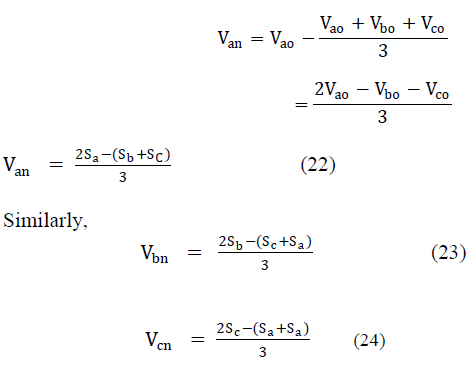 |
II.Mathematical Model of PMSM: |
The stator of the PMSM and the wound rotor
synchronous motor (SM) with armature in stator are
similar. In addition there is no difference between the
backEMF produced by a permanent magnet in a PMSM
[3]and that produced by an excited coil in a SM. Hence
the mathematicalmodel of a PMSM is similar to that ofthe
wound rotor SM. The rotor frame of reference is chosen
because the PMSM three phase armature winding is fed
from a 3 phase voltage source inverter (VSI), whichis
switched in synchronism with the rotor position
information of the PMSM. |
Hence the frequency of the voltage or current in
the PMSM armature winding atall instants is same as the
electrical speed of the machine; electrical speed
beingrelated to mechanical speed through the no. of poles
of the machine. The following assumptions are
madewhich deriving the D-Q model of the PMSM in rotor
reference frame.[3] |
1. Saturation is neglected. |
2. The back EMF is sinusoidal. |
3. Eddy currents and hysteresis losses are negligible. |
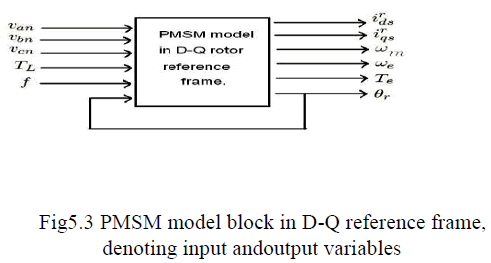 |
The mathematical model is presented as a block in Fig.
5.3, where the three armature phase voltages (machine
assumed to be star connected),[3] load torque parameters
are input variables to the motor; and the armature current,
electromagnetic torque, electrical speed, mechanical
speed and rotor position are considered output variables.
The rotor position is fed back as an input variable to the
motor model. |
SIMULATION RESULTS & DISCUSSION OF A
PROPOSED ZETA CONVERTER |
A PMSM system of 2300 rpm, 300 V, 14.3 N-m
is taken for proposed speed control scheme using Zeta
Converter. The proposed zeta converter has designed
with the voltage output range from 0 to 500 V. A PI
controller has used for voltage regulation and Speed
Controller with proportionality and integral constant
values of 0.013, 16.61 and 139.7290, 54.6363
respectively. The Proposed Scheme has implemented
using MATLAB/SIMULINK shown in Fig 6.1& Fig 6.2. |
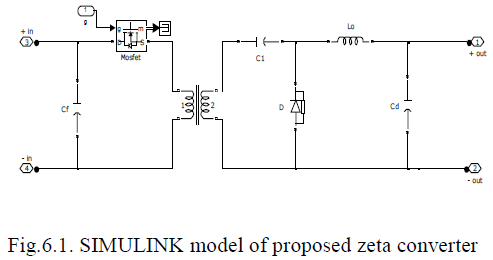 |
II .Simulation Results |
Fig. 6.3 shows the simulated speed response of
PMSM with the set value of 2200 rpm and torque T= 5
N-m.The speed response obtained as the settling time less
than 0.1s |
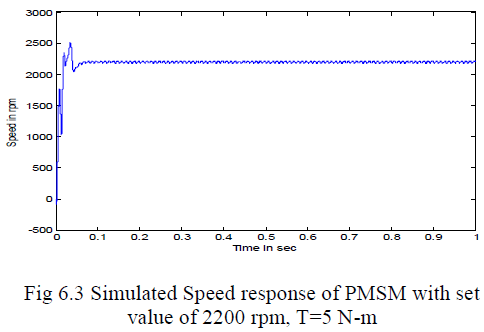 |
The simulated torque response of zeta converter
fed PMSM with the set value of 2200 rpm and torque
value can be obtained as T= 5 N-m can be shown in
Fig.6.4The simulated rotor current response of zeta
converter fed PMSM with the set value of 2200 rpm with
T= 5 N-m can be shown in Fig.6.5 |
The simulated output voltage & inverter output
voltage response of zeta converter fed PMSM with the set
value of 2200 rpm with T= 5 N-m can be shown in
Fig.6.6 & 6.7 respectively. |
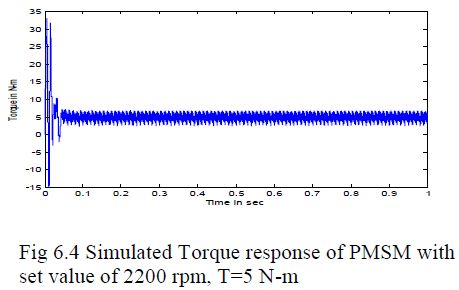 |
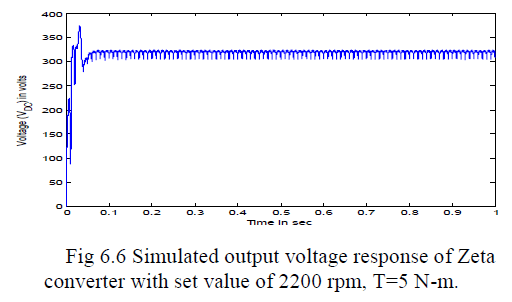 |
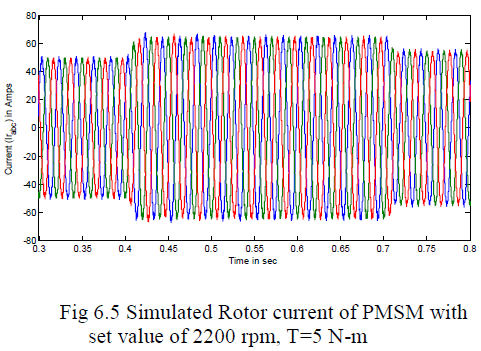 |
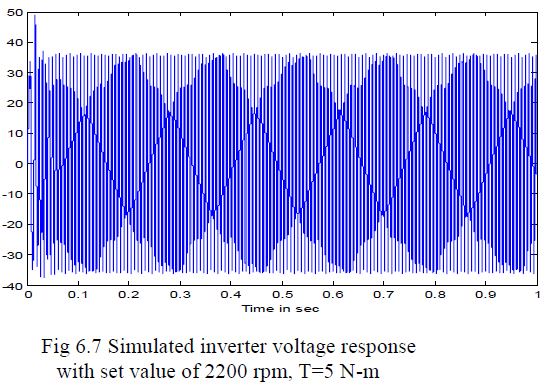 |
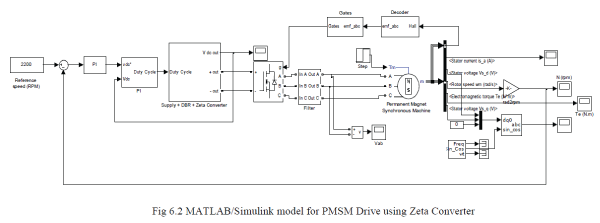 |
CONCLUSION |
A simple control using a voltage follower approach
has been used for voltage control and power factor
correction of a PFC Zeta converter fed PMSM motor
drive. A single stage PFC converter system has been
designed and validated for the speed control with
improved power quality at the AC mains for a wide range
of speed. The performance of the proposed drive system
has also been evaluated for varying input AC voltages and
found satisfactory. The power quality indices for the
speed control and supply voltage variation have been
obtained within the limits by International power quality
standard IEC 61000-3-2.The proposed drive system can
be used in various adjustable speed drives for many low
power applications. |
References |
- Limits for Harmonic Current Emissions (Equipment input currentâÃâ¬ÃÂ16 A per phase), International Standard IEC 61000-3-2, 2000.
- B. Singh, B. N. Singh, A. Chandra, K. Al-Haddad, A. Pandey and D.P. Kothari, âÃâ¬ÃÅA review of single-phase improved power quality AC-DC converters,âÃâ¬Ã IEEE Transactions on Industrial Electronics, vol. 50, no. 5, pp. 962âÃâ¬Ãâ 981, Oct. 2003.
- T. Kenjo and S. Nagamori, Permanent Magnet Brushless DC Motors, Clarendon Press, Oxford, 1985.
- T. J Sokira and W. Jaffe, Brushless DC Motors: Electronic Commutation and Control, Tab Books, USA, 1989.
- J. R. Handershot and T.J.E Miller, Design of Brushless Permanent Magnet Motors, Clarendon Press, Oxford, 1994
- J. F. Gieras and M. Wing, Permanent Magnet Motor Technology Design and Application, Marcel Dekker Inc., New York, 2002
- N. Mohan, T. M. Undeland and W. P. Robbins, Power Electronics: Converters, Applications and Design, John Wiley and Sons Inc, USA, 1995.
- Peres, D. C. Martins and I. Barobo, âÃâ¬ÃÅZeta Converter Applied in Power Factor CorrectionâÃâ¬ÃÂ, in Proc. IEEE PESCâÃâ¬Ãâ¢94, 1994, pp.1152-1157.
- S. Singh and B. Singh, "Voltage controlled PFC Zeta converter based BLDC MOTOR drive for an air conditioner," 2010
- International Conference on Industrial and Information Systems (ICIIS), pp.550-555, 29th July 2010- 1st Aug. 2010.
- Bhim Singh, B.P.Singh and SanjeetDwivedi, âÃâ¬ÃÅAC-DC Zeta Converter for Power Quality Improvement of Direct Torque Controlled PMSM DriveâÃâ¬ÃÂ, Korean Journal of Power Electronics, Vol. 6, No. 2, pp.146-162, April 2006.
- J. Uceeda, J. Sebastian and F.S. Dos Reis, âÃâ¬ÃÅPower Factor Preregulators Employing the Flyback and Zeta Converters in FM ModeâÃâ¬Ã in Proceedings of IEEE CIEPâÃâ¬Ãâ¢96, 1996, pp.132-137.
- D.C. Martins, âÃâ¬ÃÅZeta Converter Operating in Continuous Conduction Mode Using the Unity Power Factor TechniqueâÃâ¬ÃÂ, in Proceedings of IEE PEVSDâÃâ¬Ãâ¢96, 1996, pp.7-11.
- Paul P. Acarnley and John F. Watson, âÃâ¬ÃÅReview of Position- Sensorless Operation of Brushless Permanent-Magnet MachinesâÃâ¬ÃÂ, IEEE Transactions on Industrial Electronics, Vol. 53, no. 2, April 2006.
- James P. Johnson, M. Ehsani and YilcanGuzelgunler, âÃâ¬ÃÅReview of Sensorless Methods for Brushless DCâÃâ¬Ã Industry Applications Conference, 34th IAS Annual Meeting, 1999, Vol. 1, pp. 143- 150.
- F. Wu, S. A. Ljang and Y. M. Chen, âÃâ¬ÃÅDesign Optimization for Asymmetrical ZVS-PWM Zeta ConverterâÃâ¬ÃÂ, IEEE Trans. On Aerospace and Electronic Systems vol. 39, no.2, pp. 521-532, April 2003.
- M.H. Rashid, Power Electronics: Circuits, Devices and Applications (3rd edition.). Pearson-Prentice Hall, pp.186-203, 2004.
- E. Vuthchhay, C. Bunlaksananusorn, and H. Hirata, âÃâ¬ÃÅDynamic modeling and control of a zeta converter,âÃâ¬Ã International Symposium, Communications and Information Technologies, ISCIT. pp.498-503, 2008
- C. Sudhakarababu, and M. Veerachary, âÃâ¬ÃÅZeta converter for power factor correction and voltage regulation,âÃâ¬Ã IEEE Region 10 Conference, TENCON, vol.4, pp.61-64, 2004
- D. Cismasiu, V. Popescu, and D. Lascu, âÃâ¬ÃÅSingle-stage PFC power supply with universal input and automatic voltage clamping,âÃâ¬Ã 11th WSEAS International Conference on Circuits, pp. 109-114, 2007.
- E. Niculescu, D-M. Purcaru, and M.C. Niculescu, âÃâ¬ÃÅA steadystatemanalysis of PWM Sepic converter,âÃâ¬Ã 10th WSEAS International Conference on Circuits, pp. 217-222, 2006.
- E. Niculescu, M.C. Niculescu, and D-M. Purcaru, âÃâ¬ÃÅModeling the PWM Sepic converter in discontinuous conduction mode,âÃâ¬Ã 11th WSEAS International Conference on Circuits, pp. 98-103, 2007.
- C. Wu, âÃâ¬ÃÅEvaluation and implementation of the optimum magnetic design of the Cuk converter in comparison to the conventional buck-boost converter,âÃâ¬Ã IEEE Trans.Magnetics, vol.18, pp.1728-1730, 1982.
- J.J. Jozwik, and M.K. Kazimierczuk, âÃâ¬ÃÅDual sepic PWM switching-mode DC/DC power converter,âÃâ¬Ã IEEE Trans. Industrial Electronics, vol.36, pp.64-70, 1986.
- D.C. Martins, and A.H. de Oliveira, âÃâ¬ÃÅIsolated three-phase rectifier using a Sepic DC-DC converter in continuous conduction mode for power factor correction,âÃâ¬Ã WSEAS Trans Circuits, vol. 2, no. 1, pp. 13-19, 2003.
|