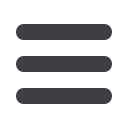
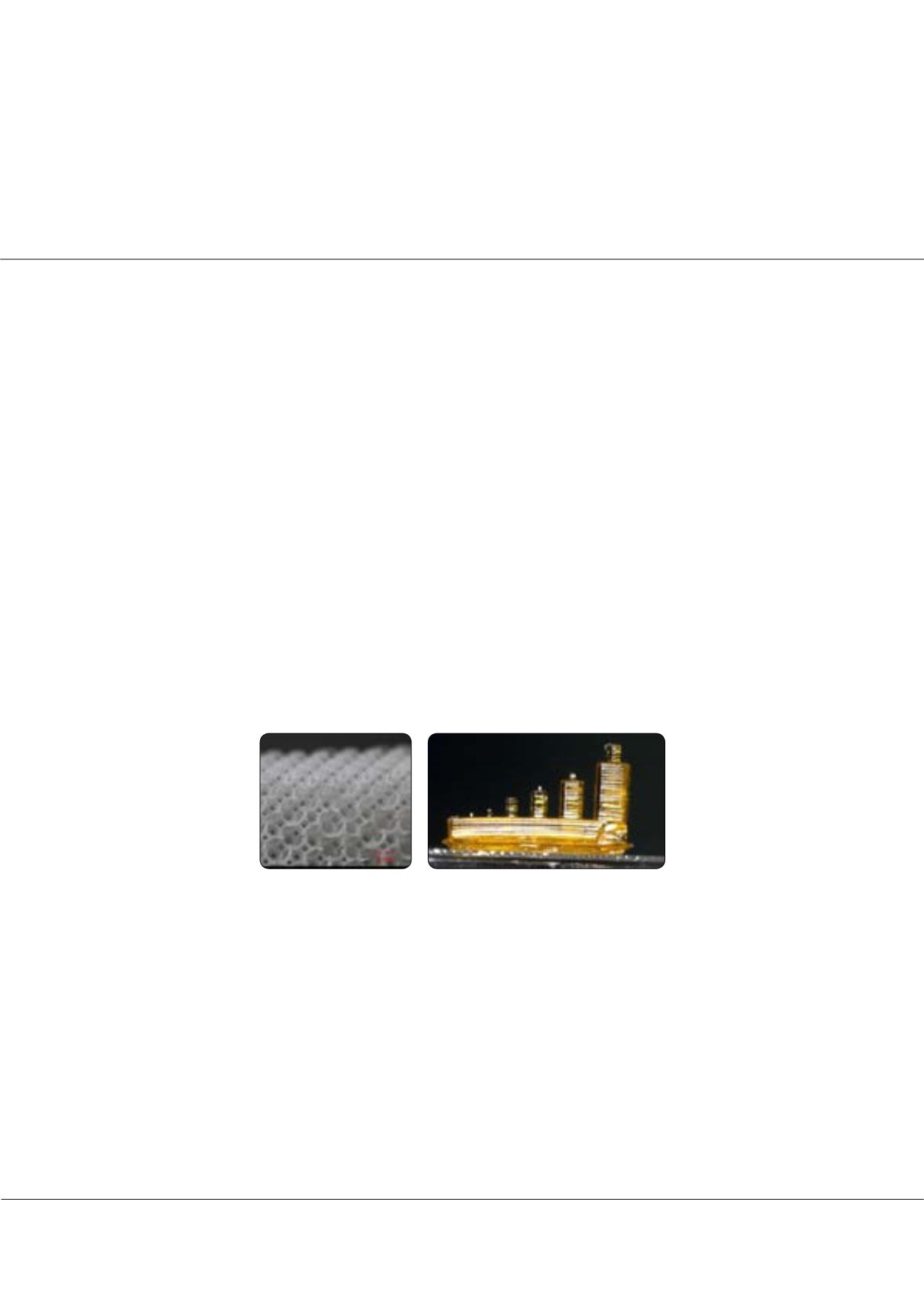
Page 55
conferenceseries
.com
Volume 6
Research & Reviews: Journal of Material Sciences
ISSN: 2321-6212
Ceramics 2018
May 14-15, 2018
May 14-15, 2018 | Rome, Italy
4
th
International Conference and Expo on
Ceramics and Composite Materials
3D-printing of ceramic-based porous structures using stereolithography
A. Dieraert
1
, S. Chupin
1
, C. Sanchez
2
and
Ph. Belleville
1
1
CEA, DAM, LE RIPAULT, France
2
Université Pierre et Marie Curie (Paris VI), France
S
tereolithography-based additive manufacturing (AM) is increasingly becoming the technology of choice for the small series
or single unit production. It also allows the material-by-design fabrication, prime concern for most material chemists.
State-of-the-art of three-dimensional (3D) structured organic-inorganic hybrid materials will be described and focus onto
combined 3D printing technology and sol-gel ceramic-based material preparation will be emphasized. Although the spectrum
of available 3D-printed materials has been widened in recent years, there is still a lack of ceramic-based materials which can
be processed with stereolithography on a routine basis. The extremely high melting point of many ceramics adds challenges
to additive manufacturing as compared with metals and polymers. Because ceramics cannot be cast or machined easily, three-
dimensional (3D) printing enables a big leap in geometrical flexibility and microstructured architecture. We report work on
synthesis new ceramics from preceramic monomers or inorganic nanopowder loaded resins that are cured with ultraviolet
light in a stereolithography 3D printer. After a thermal debinding and sintering step the part turns into a dense ceramic open
structure and gains its final properties, with uniform shrinkage and porosity control. The paper discusses the critical process
parameters that influence polymerization uniformity and structure quality. Currently it is possible to print 3D-structures
with a spatial resolution down to 40 μm, with complex shape and cellular architecture. The photosensible resin formulation
is a key parameter to control the printing resolution, so the geometry of the final ceramic. Highly complex three-dimensional
open microstructures have been theoretically designed to lead to the best agreement between thermal insulation properties
and mechanical toughness. Experimental characterization and performances of the AM ceramic parts will be discussed with
regard to high temperature super insulation material application, exhibiting high-stiff properties. Finally, scale-up of this
combined approach is carefully considered.
Recent Publications
1. Eckel, Z. C., et al.,
Additive manufacturing
of polymer-derived ceramics. Science 2016, 351, 6268.
2. Hundley, J. M., et al., Geometric Characterization of Additively Manufactured Polymer Derived Ceramics.
Additive
Manufacturing
2017.
3. Zanchetta, E., et al., Stereolithography of SiOC Ceramic Microcomponents. Advanced Materials 2016, 28, (2), 370-376.
4. DeHazan,Y.; Penner,D., SiCandSiOCceramicarticlesproducedbystereolithographyof acrylatemodifiedpolycarbosilane
systems.
Journal of the European Ceramic Society
2017.
5. Schmidt, J.; Colombo, P., Digital light processing of ceramic components from polysiloxanes. Journal of the European
Ceramic Society 2017.
Biography
Axel Dieraert obtains his Master’s degree in inorganic chemistry in 2016 at the University of Montpellier, in France (major of promotion, specialty “Porous materials, divided
systems and thin layers”). Since 2017, he’s PhD student at CEA Le Ripault (“Commissariat à l’Energie Atomique et aux Energies Alternatives”), under the direction of
Philippe Belleville (CEA Le Ripault – PhD director) and Clement Sanchez (UPMC Paris - scientific adviser). The purpose of this thesis is to develop new materials for high
temperature insulation based on stereolithography of ceramic materials.
axel.dieraert@cea.frA. Dieraert et al., Res. Rev. J Mat. Sci. 2018, Volume 6
DOI: 10.4172/2321-6212-C1-014