A MEMS electro-thermal microgripper has been designed and discussed in this paper. The electro thermally actuated gripper consists of “hot-and-cold-arm” actuators. The micro-grippers are used to maneuver small delicate objects with nanometer scale precision and accuracy. Design parameters strongly influencing the performance of the gripper such as length of the hot arm, length and shape of the cold arm has been considered in order to optimize the performance. The gripper has a thickness of 25m. Simulation of the device has been done using the COMSOL Multiphysics software.
Keywords |
MEMS, Electro thermal
microgripper, Thermal Expansion. |
INTRODUCTION |
Microgrippers are microscopic tools which are designed
specifically for handling objects in the range of
micrometers to nanometers. They are ideal for variety of
applications including sample handling, micro assembly,
micro-factories, biological and biomedical research and
parts handling in scanning electron microscopes. In
microgrippers for providing the gripping force, actuating
principle based on electrostatic forces is highly desirable.
However they have small deflections and require large
voltage to obtain large deflection. On the other hand
actuation mechanism based on thermal expansion effect
can provide a large force and displacement. The operating
principle of thermally driven actuator is the expansion of a microstructure with variable cross sections. Electrothermal
actuation is the preferred mechanism since it is
able to produce large deflections at low activation
voltages [1]. |
CONCEPT DESIGN |
Micro grippers consist of a pair of tweezers to grab the
objects and pair of actuators to provide the required force.
The micro actuator consists of |
1. hot arm (which is narrow ) |
2. cold arm (which is wide) |
3. flexure |
The resistance of the hot arm is higher than the cold arm
since it is narrower. When voltage is applied to the
anchors, current passes from one anchor to another
through the hot and cold arms of the actuator. The hot arm
gets more heated than the cold arm according to the
relations: |
 |
where , |
R – Resistance |
L – Length |
A – Area of the cross section of the arm |
H – Joule heat produced in the arm |
I – Current flowing through the arm |
As a result of more heated hot arm, it deflects more than
the cold arm. The arms are jointed at the free end which
causes the tip of the actuator to move laterally towards the
cold arm side [2,3]. Fig. 1 shows the schematic view of
the electro thermal actuator. |
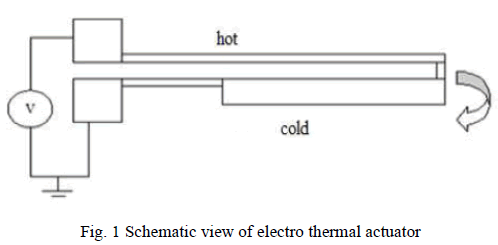 |
STRUCTURE AND DIMENSIONS |
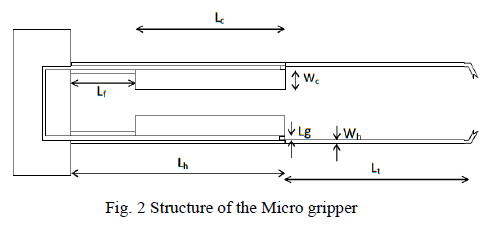 |
The micro gripper consists of a pair of electro thermal
actuators driving a pair of tweezers. The microgripper
consists of major parts as hot arm, cold arm, anchors
and tweezers. When the tips of the actuators move
laterally because of the voltage applied, the tweezers
attached to the actuators also move. This movement is
used to grab the object. The entire structure is made up
of silicon. The initial dimensions of the electro
thermally actuated gripper are as given in the Table I. |
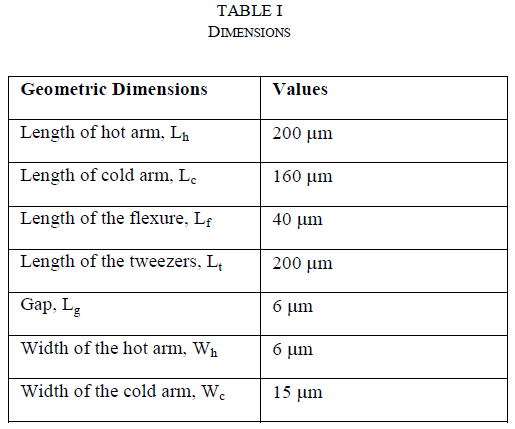 |
ANALYTICAL MODELING |
The resistivity is a function of temperature and the
formula is given by [4] |
 |
where, |
ρ0 – Resistivity at a reference temperature |
αR – Temperature coefficient of resistivity |
T0 – Reference temperature |
Thermal expansion of solids is modeled by [4] |
 |
where, |
αE – Linear thermal expansion coefficient |
ΔL – Change in length from L0 |
ΔT – Change in temperature that causes the
expansion |
The lateral movement of the tip of the tweezers
attached to the actuators can be estimated by [5] |
 |
where, |
A – Cross-sectional area of the hot arm |
I – Moment of inertia of the hot arm |
L – Length of the actuator |
a – Ratio of the length of the flexure to the length
of the hot arm |
α – Coefficient of thermal expansion |
r – Gap between the hot arm and the flexure |
ΔT – Net temperature difference. |
Temperature distribution along the arm of the actuator
is given by [6] |
 |
where, |
x – Position along the arm |
V – Applied voltage |
L – Length of the arm |
ρ – Resistivity |
kp – Thermal conductivity of the material |
FEM SIMULATION |
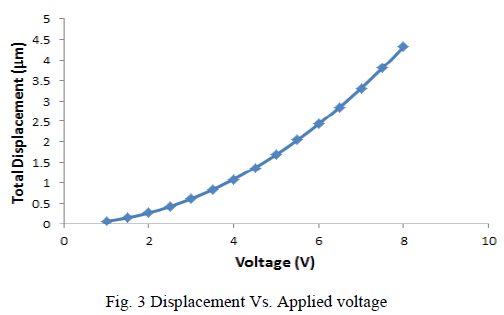 |
Simulation of the device has been done using the
COMSOL Multiphysics tool. The joule heating and
thermal expansion physics has been used to model the
design. According to the principle described in the section
II the hot arm gets more heated than the cold arm and
moves laterally. Electric potential is applied to one of the
anchors and the other is grounded. The total displacement
increases with increase in the applied voltage and is
shown in the Fig. 3. The displacement for the applied
voltage of 8v is shown in the Fig. 4. |
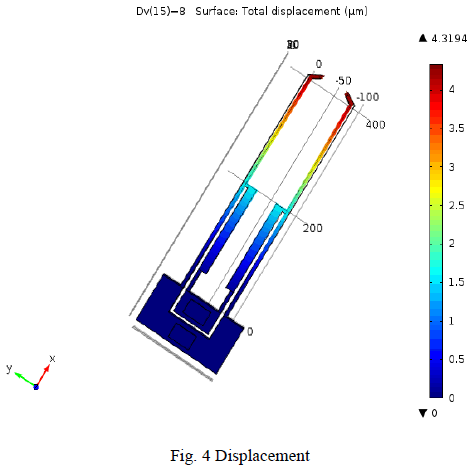 |
Von mises stress of the gripper is shown in Fig. 5. The
maximum von mises stress of the structure is lesser
than the maximum with stand-able stress i.e., yield
strength of the material which is being used. |
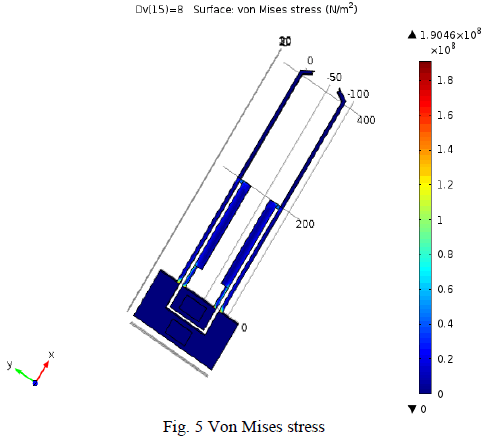 |
OPTIMIZATION |
The microgripper has been optimized for the
improvement in its performance. The design
parameters used to optimize the performance are the
length of the hot arm and tweezers, shape of the cold
arm and metal coating on c old arm. |
A. Length of the hot arm and tweezers |
The amount of deflection depends majorly on the
geometry of the gripper [7]. Length of the hot arm is
varied from 400m to 500m and the displacement has
been observed. Table II Shows the variation of displacement with respect to the length of the hot arm
and tweezers |
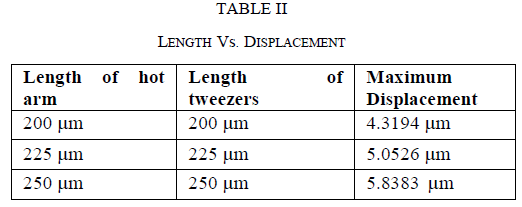 |
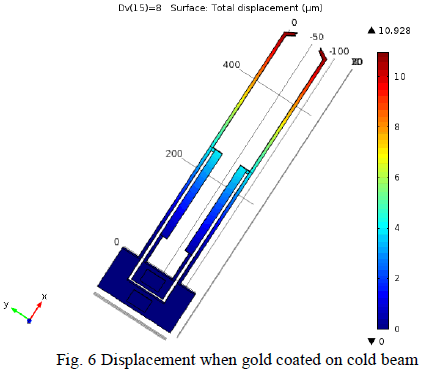 |
Displacement can be increased further by having a
metal coating [8]. When gold is applied on the cold
beam with the length of the hot beam and tweezers as
250 m the displacement obtained is 10.928 m as
shown in Fig. 6. |
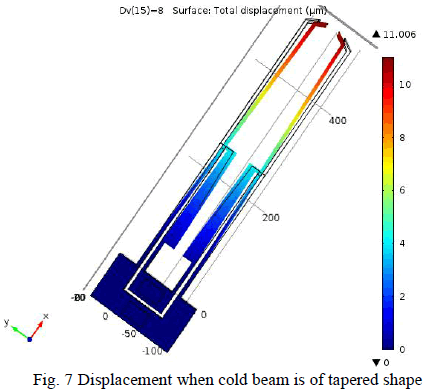 |
Another design parameter that affects the displacement is
the shape of the cold beam. When cold beam has the
tapered shape instead of the rectangular one, the
displacement can be improved little further. With the
tapered beam the displacement of 11.006 m is being
achieved. The displacement of the microgripper with
tapered beam is shown in Fig. 7. |
CONCLUSION |
Electro thermally actuated microgripper with actuators
has been designed. The design has been optimized in
order to increase the displacement. When the size of the
arms and tweezers are increased the displacement
increases. The shape of the cold arm also affects the
displacement. The tapered beam results in larger
displacement than the rectangular beam. Metals coating
provides a considerable amount of increment in the
displacement. Further improvements can be realized by
varying other dimensions of the design and also different
materials can be used. |
ACKNOWLEDGMENT |
Authors thank the National MEMS Design Centre at Anna
University, Chennai sponsored by NPMASS program for
providing the necessary facilities and simulation tools for
modeling the concepts. |
References |
- R. Voicu, C. Tibeica, R. MÃÆÃ¼ller, "Design and optimization studyfor a new SU-8 electro-termally actuated microgripper,"Proceedings of the 3rd International Conference onManufacturing Engineering (ICMEN), 1-3 October 2008,Chalkidiki, Greece
- Crosby and Guvench, "Experimentally Matched Finite Elementof Thermally Actuated SOI MEMS Micro Gripper UsingCOMSOL Multiphysics," COMSOL Conference 2009, Boston,1-9 (2009)
- H. Qing-An and N. K. S. Lee, "Analysis and design of polysiliconthermal flexure actuator", J. Micromech. Microeng., vol.9, pp.64 -70 1999
- John V. Crosby, and Mustafa G. Guvench (2009),"Experimentally Matched Finite Element Modeling of ThermallyActuated SOI MEMS Micro-Grippers Using COMSOLMultiphysics," Proceedings of the COMSOL ConferenceBouston, pp. 1-9
- N. Chronis, and L. P. Lee, "Electrothermally activated SU-8microgripper for single cell manipulation in solution," J.Microelectromech. Sys., vol.14(4), pp. 857- 863, 2005.
- Suma,N.;Nagaraja,V.S.; Pinjare,S.L.; Neethu,K.N.; Sudharshan,K.M. "Design and Characterization of MEMS Thermal Actuator,"Devices, Circuits and Systems (ICDCS), 2012 InternationalConference, pp 638-642
- Q.-A. Huang and N. K. S. Lee, "Analytical modeling andoptimization for a laterally-driven polysilicon thermal actuator, "Microsystem Technologies 5, 133-137 (1999).
- R. Kalaiarasi and S. HosiminThilagar, "Modeling andcharacterization of a SOIMUMPâÃâ¬Ãâ¢s hybrid electro thermalactuator, " Journal of Microsystem Technologies, 19(1), pp. 113-120, 2013.
|