Keywords
|
Multiwall Carbon Nanotube(MWCNT), Al6061 powder, Sintering, Extrusion |
INTRODUCTION
|
Many engineering applications in the field of aerospace engineering,automobiles,electronic equipment etc require very light material with good mechanical properties. Aluminium based metal matrix composites with carbon nanotube reinforcement can be a solution for such applications.It can satisfy the requirement of light weight with very good strength.This study focuses on preparing aluminium metal matrix composites with CNT reinforcements for various composition for it‘s mechanical properties. Al6061 alloys have been widely used as structural materials in aeronautical industries due to their attractive comprehensive properties, such as low density, high strength, ductility, toughness and resistance to fatigue. Yufeng Wu et.al [1].have studied Semi-solid powder processing (SPP) is a promising technology that combines the benefits of semi-solid forming and powder metallurgy. In this study, carbon nanotube (CNT) reinforced aluminium alloy 6061 (Al6061) composite was synthesized by SPP for the first time. Mechanical alloying was used to disperse the CNTs in the matrix phase. The effects of the processing temperature (6000C, 6200C and 6400C)on the microstructure, hardness, fracture surface and composition of the Al6061–CNT composite were investigated. A.M.K. Esawi et.al.[2,3,4] .have investigated that Powder metallurgy techniques have emerged as promising routes for the fabrication of carbon nanotube (CNT) reinforcedmetal matrix composites. In thiswork, planetary ball millingwas used to disperse 2 wt% MWCNT in aluminum (Al) powder. Despite the success of ball milling in dispersing CNTs in Al powder, Both un-annealed and annealed Al–2 wt% CNT composites were investigated. It was found that, ball-milled and extruded (un-annealed) samples of Al–2 wt% CNT demonstrated high notch-sensitivity and consistently fractured outside the gauge length during tensile testing. Jinzhi Liao et.al. [5,6] have studied carbon nanotube (CNT) reinforced aluminum (Al) composite was fabricated by powder metallurgy (P/M) technique. Small addition of CNTs (0.5 wt.%) evidently improved the tensile strength and hardness of the composite by comparing with the pure matrix. Mechanical property enhancements of the Al- 0.5CNT composites from PBA and high energy ball milling were superior to that mixed by low energy ball milling. K T Kashyap et.al.[7] have studied Carbon nanotubes (CNTs) were discovered by Iijima in 1991 as the fourth form of carbon. Carbon nanotubes are the ultimate carbon fibres because of their high Young‘s modulus of ≈ 1 TPa which is very useful for load transfer in nanocomposites. In the present work, CNT/Al nanocomposites were fabricated by the powder metallurgy technique and after extrusion of the nanocomposites bright field transmission electron microscopic (TEM) studies were carried out. From the TEM images so obtained, a novel method of ascertaining the Young‘s modulus of multi-walled carbon nanotubes is worked out in the present paper which turns out to be 0⋅9 TPa which is consistent with the experimental results. T. Laha et.al [9,10]have investigated Al-based nanostructured composite with carbon nanotubes as second phase particles has been synthesized by plasma spray forming technique. Optical microscopy, scanning electron microscopy, X-ray diffraction,transmission electron microscopy has been carried out to analyze the composite structure and to verify the retention of carbon nanotubes. I. Sridhar et.al.[11] have investigated that Metal matrix composites comprising aluminum matrix and multi-wall carbon nanotubes (MWCNTs) as reinforcements are fabricated using cold uniaxial compaction followed by sintering and cold extrusion as secondary processes. The effect of sintering temperature on the microstructure is explored using differential scanning calorimetric spectrum. The tensile yield and ultimate strength of Al- MWCNTs increased to 90% with 2 wt% addition of MWCNTs. Various theories for the strengthening and stiffening of Al- MWCNTs composites are explored. |
Chunfeng Deng et.al[13,14,15,16] have fabricated 2024Al matrix composite reinforced with 1 wt.% carbon nanotubes (CNTs) was fabricated by cold isostatic pressing, followed hot extrusion techniques. The microstructure characteristics and the distribution of carbon nanotubes in the aluminum matrix were investigated. . The damping behaviors of the composite were investigated with frequency of 0.5, 1.0,5.0, 10, 30 Hz, at a temperature of 25–400 °C. The experimental results show that the frequency significantly affects the damping capacity of the composite when the temperature is above 230 °C; meanwhile, the damping capacity of the composite with a frequency of 0.5 Hz reaches 975×10−3, and the storage modulus is 82.3 GPa when the temperature is 400 °C.Jinzhi Liao et.al[17].have investigated, carbon nanotubes (CNTs) reinforced aluminum matrix composites (AMCs) have attracted increasing attention. The quality of dispersion, however, is a crucial factor which determines the homogeneity and final mechanical properties of these composites. The Al-CNTs mixture was subsequently consolidated by powder metallurgy (PM) technique. Small addition of CNTs (0.5 wt.%) evidently improved the tensile strength and hardness of the composite by comparing with the pure matrix. Mechanical property enhancements of the Al-0.5CNT composites from PBA and high energy ball milling were superior to that mixed by low energy ball milling. This showed good dispersion effect in PBA and high energy ball milling technique.Maohui GE et.al.[18,19,20] have investigated Nanotubes of carbon can be produced by vapor condensation of carbon on a flat graphite surface. Nanometer-sired carbon cones were generated by vapor condensation of carbon atoms on a graphite substrate and were analyzed by scanning tunneling microscopy (STM). |
S. R. Malik et.al.[21] have investigated Carbon nano-tubes (CNTs) are hollow cylinders of graphite carbon atoms. These tubes are on the nanoscale (10-9 m), which is so small that 10,000 of them could fit within the diameter of one human hair.Carbonnano-tubes are a new form of carbon with unique electrical and mechanical properties. They can be considered as the result of folding graphite layers into carbon cylinders. These single shell single wall carbon nano-tubes (SWCNTs), or of several shells multi-wall carbon nano-tubes (MWCNTs). Kazuyoshi Tanaka al et.al.[22] have investigated that the electronic properties of purified carbon nanotube The purified nanotube examined in the present study is a ?clean‘ semiconductor almost without magnetic impurity and is doping inactive. G. Overney et.al.[23] have studied the low frequency vibrational modes and the structural rigidity of long graphitic carbontubules consisting of 100, 200, and 400 atoms. Zhe Zhang et.al.[24]have investigated that Scanning tunneling microscopy (STM) has been used to investigate the structure and electronic properties of carbon nanotubes produced from a discharge between graphite electrodes. In addition, bias-voltage dependent imaging studies indicate that the nanotubes studied are semiconductors. The implications of these new data to the application of nanotubes in structural composites and nanoelectronics is discussed. Rodney S.Ruoff et.al.[25] discusses e mechanical and thermal properties of carbon nanotubes.The tensile and bending stiffness constants of ideal multi-walled and single-walled carbon nanotubes are derived in terms of the known elastic properties of graphite. C.-H. Kiang et.al.[26] have investigated that a variety of carbon structures are produced in an electric arc discharge with an anode composed of carbon, cobalt,andsulfur. Single and multiple layered carbon nanotubes, as well as partially filled nanowires and bamboo-shaped carbon compartments, are found in different regions of the soot inside the chamber. Sulfur plays an important role in forming these carbon nanomaterials. Henk W et.al.[27] have investigated that Room-temperature single-electron transistors are realized within individual metallic single-wall carbon nanotube molecules. Jean-Paul Salvetat et.al.[28] have investigated that a condensed review of mechanical properties of carbon nanotubes is given. Theory as well as experiments is examined with a view to extracting the fundamental elements that should allow the reader to build his own perspective of the subject. R. Byron Pipesa et.al[29] have investigated that an investigation of the effective mechanical properties of large arrays of carbon nanotubes assembled in helical geometries of circular cross-section is undertaken following two approaches. Ray H. Baughman et.al.[30] have investigated that Many potential applications have been proposed for carbon nanotubes, including conductive and high-strength composites; energy storage and energy conversion devices; sensors; field emission displays and radiation sources; hydrogen storage media; and nanometer-sized semiconductor devices, probes, and interconnects.Suneel D et.al.[8] have investigated that Aluminum structural components find numerous applications in aerospace and defense industries. |
The study involves preparation of CNT reinforced Al6061metal matrix Composites by Powder metallurgy technique. |
II. MATERIALS AND METHODS
|
Reinforced Al6061-CNT composites were manufactured by using Powder metallurgy technique.Al6061 powders of 200 mesh size as a matrix and Multiwalled Carbon NanoTubes as reinforcement. The properties of as supplied MWCNTs (Nanoshel LLC USA) are given in Table.1. |
A. Methods |
Al6061 powder (200 mesh) and multiwalled carbon nano tubes (Nanoshell.,USA)(10-30 nm) were procured from different sources available in the market. The two materials were properly mixed for different composition by using ball mill to mix uniformly CNT‘s with Al6061 powder. Compacting die was used to compact the powder by using 40Ton capacity hydraulic press, after compacting the powder in to solid billet. |
B. Preparation of composite |
The CNT powder was initially purified by mixing it in concentrated Nitric acid, filtering and washing with de-ionized water and drying at 1200 C. This is done to remove the impurities such as graphitic particles, amorphous carbon or any other impurities present. MWNT of 0 wt%, 0.5wt %,1 wt%,1.5wt%,2 wt % of carbon nano tubes weight percentage was mixed with Al6061 powder in ethanol solution. Use ballmill, the process of mixing is continued for duration of 10 min at 200 rpm in order to get uniform mixing. The mixture of a particular weight percentage of MWNT and Al6061 was compacted in the die assembly using a 40 Ton capacity universal testing machine. The standardized load (200 KN) was applied at the rate of 2 Ton/min. |
A low cost sintering furnace was designed and fabricated for current research work. Samples were prepared for various compositions and the samples were investigated for microstructure, using optical microscope and SEM Apparatus. Sintered billets were hot extruded using hot extrusion set up. Samples were tested for strength.The same procedure was repeated to produce specimens of round and rectangular extruded strips of different weight percent content of MWNT with Al6061matrix. While compacting Al6061 matrix based composite, a compaction load of 200KN and a sintering temperature of 5250 C were used. |
III. EXPERIMENTATION RESULTS AND DISCUSSIONS
|
A. Microstructure The above structure shows that micro structure under unetched condition reveals porosity upto 12 to 15% in the matrix of grains of Al powder. |
The above fig.4 and fig.5 structure shows that micro structure under unetched condition reveals porosity upto 40% in the matrix of grains of Al powder. The compactness of the material is quiet non uniform due to porosity distribution foming few clusters.SEM image fig.6 and fig.7 shows that fusion of aluminium grain were observed. There are non uniform grains of fused aluminium. Porosity is between the grains observed. Since grain boundary along the porosity and fused aluminium grains makes the component brittle SEM image shows that white portion are the carbon nono tubes, black portion is the aluminium powder.fusion of aluminium grains are quiet uniform. Few porosities observed. No inter-granular porosities observed. |
B. Hardness |
Hardness of specimen of Al6061 and MWNT reinforced composites were determined by using Brinell Hardness Testing apparatus as per ASTM B-925. The results are tabulated in Table. 3 It is inveatigated that Al6061 alloy and CNT MMC composites, the hardness increases with the addition of MWNT upto 3 wt % of MWNT and then the hardness decreases This is due to the contribution of metallurgical composition and structure of Al6061- CNT Metal Matrix Composites. |
The Fig.8 shows the bar chart of comparison of hardness of matrix alloy and the composites. The composite found to be harder than the matrix alloy due to higher hardness of dispersoid particles there in percentage of hardness increases with increase in percentage of Carbon Nano Tube (CNT). |
From the Table.4 it has been the observed that Theoretical and Experimental density increases with an increase in weight percentage of MWCNT in the composites. This is due to agglomeration of MWCNT in theAl6061 matrix. Tensile strength increases remarkably with an increase in weight percentage of MWCNT in the composites. It is also observed that young‘s modulus increases remarkably with an incrase in weight percentage of MWCNT in the composite. |
From the Fig.9 it has been observed that the compressive strength remarkably decreases with anincrase in weight percentage of MWCNT in the composite. Density measurement results indicate that lighter Metal matrix composites(MMC) have been obtained with the addition of CNTs. Previous studies show that with the addition of ceramic particles such as SiCp[2] and Al2O3 [7] as reinforcements, the density of Aluminium composites will increase. This is not desirable because of the lightweight applications of Aluminium composites. the density of Al6061–3.0 wt.% MWCNT, which shows the best mechanical properties of the Al6061–MWCNT nanocomposites fabricated .The incorporation of MWCNTs into the Al6061 matrix has minimal effect on the macrohardness of the nanocomposites until the threshold of 3 wt.% MWCNT. The tensile strengths and ductility are observed in the Al6061– wt.% MWCNT nanocomposite. This phenomenon of increasing yield strength with higher volume fraction of MWCNTs is applicable only until 3wt.% of MWCNT, above which, the yield strength starts to degenerate due to higher amount of porosity in the Al6061 matrix.The increase in tensile strength up to an addition of 3 wt.% MWCNT is due to the restriction of dislocation movement by the MWCNTs. An increase in ductility has been observed in Al6061 reinforced with up to 3 wt.% of MWCNTs. The maximum improvement of ductility was observed to be 69% in Al6061–3 wt.% MWCNT nanocomposite. |
The above fig .10 and fig.11 shows the Al6061-MWCNT MMC.The uniform grains fused with Al6061 and Porosity is between the grains were observed. Since grain boundary along the porosity seen and fused aluminium grains makes the MMC. SEM images shows that white portion observed as carbon nono tubes, black portion as aluminium .Crack after compression shows significantly aluminium grains are quiet uniform, few porosities were observed and no inter-granular porosities seen. |
IV. CONCLUSION
|
Al6061 powder as matrix mixed with MWCNT in weight percentages of 0, 0.5, 1, 1.5 ,2,2.5 and 3%(wt) as reinforcement were produced through powder metallurgy route. The specimens were Sintered and extruded successfully . Specimens were subjected to evaluate the behavior of microstructure and mechanical properties of MMc‘s. From the investigation, following points are concluded. |
? Hardness of Al6061-MWCNT composite is greater than Al6061. |
? Micrograph shows good bonding between matrix and reinforcement. |
? Al6061-MWCNT composite showed ductile property where as Al6061 were brittle. |
? Young‘s Modulus increases remarkably with the increase in Reinforced particulate (MWCNT). |
? Tensile strength increases with the addition of MWCNT but compressive strength decreases with the addition of MWCNT. |
ACKNOWLEDGMENT
|
The author wish to thank Dr.R.P.Reddy, Principal, HOD mechanical and Management of Reva ITM, Bangalore and Principal , HOD and Management of MSRIT ,for encouragement and support. |
Tables at a glance
|
 |
 |
 |
 |
Table 1 |
Table 2 |
Table 3 |
Table 4 |
|
|
Figures at a glance
|
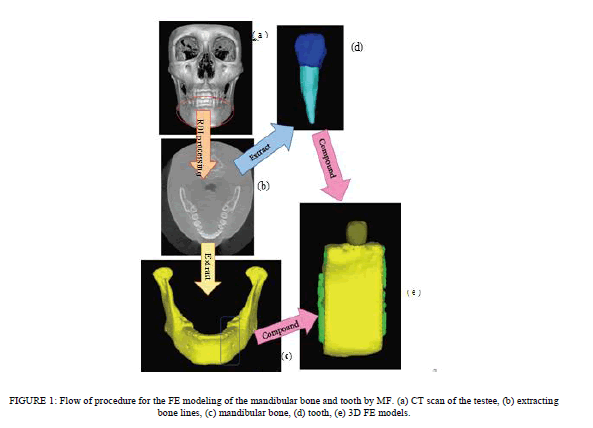 |
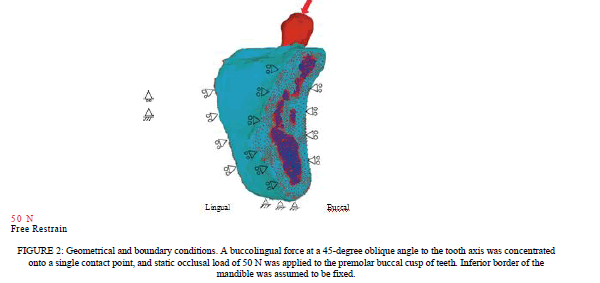 |
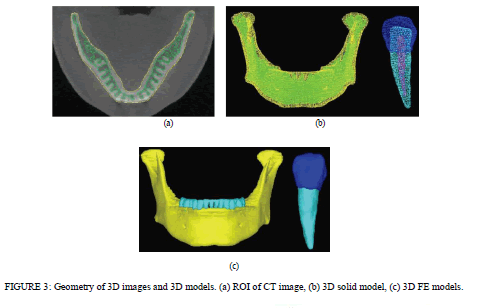 |
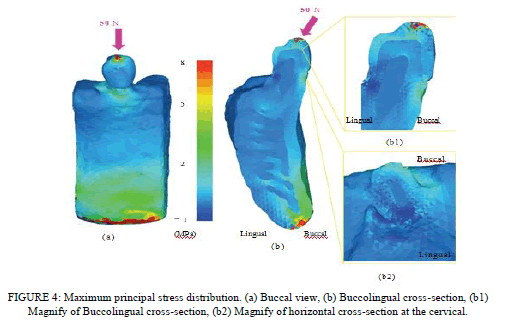 |
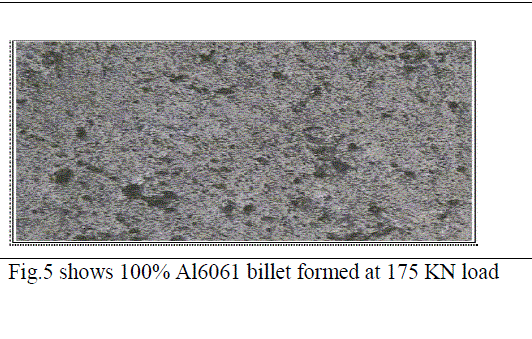 |
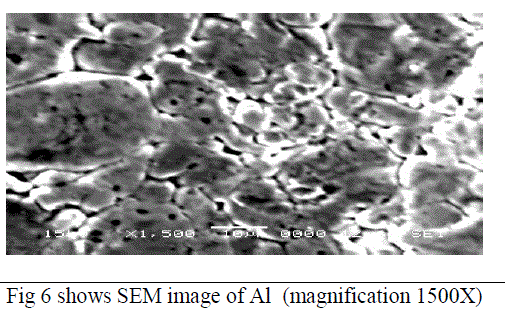 |
Figure 1 |
Figure 2 |
Figure 3 |
Figure 4 |
Figure 5 |
Figure 6 |
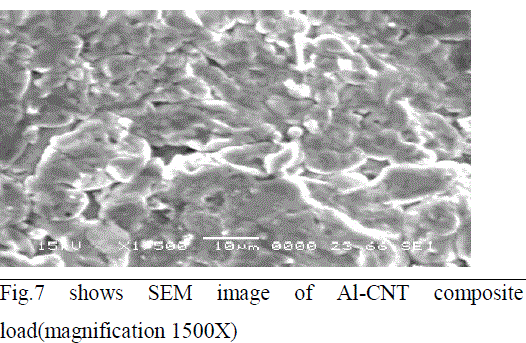 |
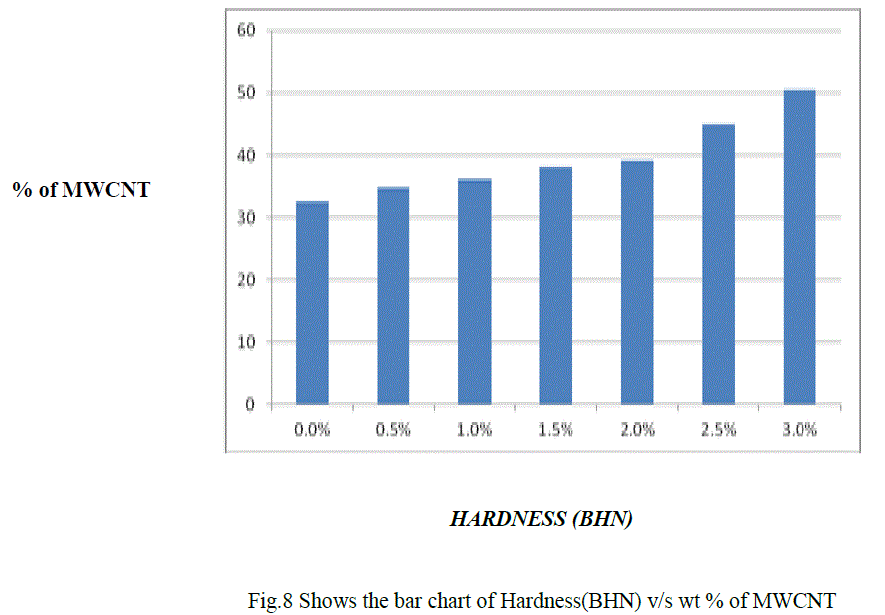 |
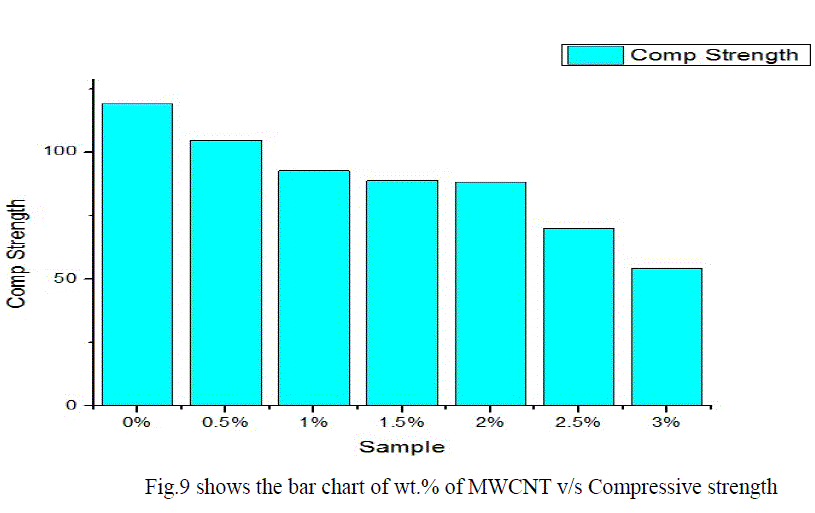 |
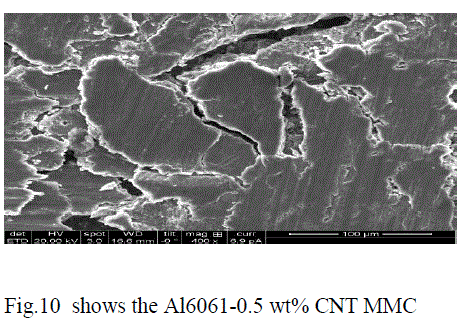 |
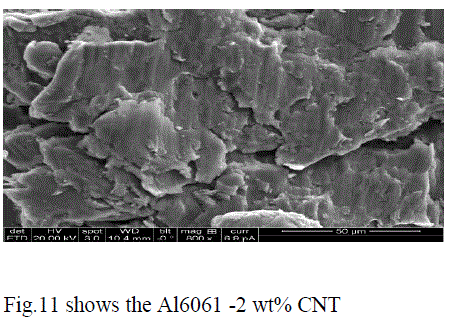 |
Figure 7 |
Figure 8 |
Figure 9 |
Figure 10 |
Figure 11 |
|
|
References
|
- Yufeng Wu1, Gap-Yong Kim ? Carbon nanotube reinforced aluminum composite fabricated by semi-solid powder processing? Journal of Materials Processing Technology 211 (2011) 1341–1347.
- A.M.K. Esawi , K. Morsi , A. Sayed , M. Taher , S. Lanka ? Effect of carbon nanotube (CNT) content on the mechanical properties of CNT-reinforced aluminium composites? Composites Science and Technology 70 (2010) 2237–2241.
- A.M.K. Esawi, K. Morsi, A. Sayed, A. Abdel Gawada, P. Borah ? Fabrication and properties of dispersed carbon nanotube–aluminum composites? Materials Science and Engineering A 508 (2009) 167–173.
- A. Esawi , K. Morsi ?Dispersion of carbon nanotubes (CNTs) in aluminumpowder?Composites: Part A 38 (2007) 646–650.
- Jinzhi Liao, Ming-Jen Tan, Raju V. Ramanujan, ShashwatShukla ?Carbon nanotube evolution in aluminum matrix during composite fabrication process?Materials Science Forum Vol. 690 (2011) pp 294-297.
- Jinzhi Liao, Ming-Jen Tan ?Mixing of carbon nanotubes (CNTs) and aluminum powder for powder metallurgy use? Powder Technology 208 (2011) 42– 48.
- K T Kashyap and R G Patil ?On Young‘s modulus of multi-walled carbon nanotubes? Bull. Mater. Sci., Vol. 31, No. 2, April 2008, pp. 185–187.
- Suneel D. NageswaraRao D. SatyanarayanaChPawan Kumar Jain ?Estimation of Cavitation Pressure to Disperse Carbon Nonatubes in Aluminium Metal Matrix Nanocomposites? AIJSTPME (2009) 2(1):53-60.
- T. Laha , S. Kuchibhatla, S. Seal, W. Li, A. Agarwal, ?Interfacial phenomena in thermally sprayed multiwalled carbon nanotube reinforced aluminumnanocomposite? ActaMaterialia 55 (2007) 1059–1066.
- T. Laha , A. Agarwal, Tim McKechnie , S. Seal ?Synthesis and characterization of plasma spray formed carbon nanotube reinforced aluminum composite? Materials Science and Engineering A 381 (2004) 249–258.
- I. Sridhar Æ Karthic R. Narayanan ?Processing and characterization of MWCNT reinforcedaluminum matrix composites?J Mater Sci (2009) 44:1750–1756.
- Ray H. Baughman, Anvar A. ? Carbon Nanotubes—the Route Toward Applications? Zakhidov, Walt A. de HeerScienceVol 297 2 August2002.
- Deng Chunfenga, Zhang Pengb, MA Yanxiaa, Zhang Xuexic, and Wang Dezunc ?Dispersion of multiwalled carbon nanotubes in aluminum powders? Rare MetalsVol. 28, No. 2, Apr 2009, p. 175.
- ChunfengDeng ,XueXi Zhang, Dezun Wang, Qiang Lin, Aibin Li ?Preparation and characterization of carbon nanotubes/aluminum matrix composites?Materials Letters 61 (2007) 1725–1728.
- C.F. Deng , D.Z. Wang, X.X. Zhang, Y.X. Ma ?Damping characteristics of carbon nanotube reinforced aluminum composite? Materials Letters 61 (2007) 3229–3231.
- Jinzhi Liao , Ming-Jen Tan ? Mixing of carbon nanotubes (CNTs) and aluminum powder for powder Metallurgy use? Powder Technology 208 (2011) 42–48.
- R.George,K.T.Kashyap,R.Rahul,S.Yamdagni ?Strenthening in carbon nanotube/ aluminium(CNT/Al)composites Sriptamaterialia 53(2005)1159- 1163.
- Maohui GE and Klaus Sattler ?Scanning tunneling microscopy of vapor-phase grown nanotubes of carbon?Php. Ckm. Solids Vol. 54, No. 12, pp. 1871- 1877, 1993.
- MaohuiGe, Klaus Sattler ?Observation of fullerene cones? Chemical Physics Letters 220 (1994) 192-196.
- MaohuiGe and Klaus Sattler ?Bundles of carbon nanotubes generated by vapor-phase growth? Appl. Phys. Let-t. 64 (S), 7 February 1994.
- S. R. Malik, M. A. Maqbool,S. Hussain, H. Irfan ?carbon Nano-tubes:Description,Properties and Applications? J Pak Mater Soc 2008; 2 (1).
- Kazuyoshi Tanaka al,Tohru Sato, TokioYamabe ,TVK, enjiOkahara , Kunio Uchida ?MotooYumura , Hiroyuki Niino , Satoshi Ohshima , YasunoriKuriki,KiyoshiYase , FumikazuIkazaki ? Electronic properties of carbon nanotube? Chemical Physics Letters 223 (1994) 65-68.
- G. Overney, W. Zhong, D. Tom/mek ?Structural rigidity and low frequency vibrational modes of long carbon tubules? Z. Phys. D 27, 93-96 (1993).
- Zhe Zhang and Charles M. Lieber ?Nanotube structure and electronic properties probed by scanningtunnelingmicroscop?
- Rodney s.Ruoff and Donald C. Lorents? Mechanical and Thermal Properties of Carbon nano tubes? Carbon, Vol. 33, No. 7, pp. 925-930, 1995.
- Kiang , M.S. Dresselhaus , R. Beyers , D.S. Bethune ?Vapor-phase self-assembly of carbon nanomaterials? Chemical Physics Letters 259 (1996) 41- 47C.-H.
- Henk W. Ch. Postma, TijsTeepen, Zhen Yao,MilenaGrifoni,Cees Dekker ?Carbon Nanotube Single-Electron Transistors at Room Temperature?6 july 2001Vol293 Science.
- Jean-Paul Salvetat-Delmottea,b. Angel Rubioc ?M echanical properties of carbon nanotubes: a fiber digest for Beginners? Carbon 40 (2002) 1729–1734.
- R. Byron Pipesa, Pascal Hubert ?Helical carbon nanotube arrays: mechanical properties? Composites Science and Technology 62 (2002) 419–428.
- Ray H. Baughman, Anvar A. ? Carbon Nanotubes—the Route Toward Applications? Zakhidov, Walt A. de HeerScienceVol 297 2 August2002.
|