Keywords
|
Keywords: Zigbee network, mechanical vibration, temperature sensor, MEMS sensor, Potentiometer |
INTRODUCTION
|
Wind power has become the world’s fastest growing renewable energy resource. The worldwide wind power installed capacity has exceeded 120 GW. The United States has set a target of 20% wind-based electricity generation— over 300 GW—by 2030. As wind power becomes a major utility source, it is crucial to ensure the reliable operation of these power systems in order to improve both quantity and quality of wind power generation. Wind turbines are subject to different sort of failures. Therefore, before exploring condition monitoring and fault diagnostic methods in wind turbines, the different kinds of failures, as well as their downtime consequences, are reviewed. |
Of course, obtaining reliable power from wind turbine generators, which are complex electromechanical systems, requires high performance monitoring systems. Analysis of wind farm maintenance costs has shown that up to 40% of the cost can be related to unexpected failures of wind turbine components that then lead to unscheduled corrective maintenance actions. Unscheduled corrective maintenance is the most costly type of maintenance, and it is always at high risk for consequential damages resulting in extensive downtimes. To avoid these problems, the focus of most wind farms is shifting to predictive maintenance. Predictive maintenance by condition-based monitoring of electrical machines is a scientific approach that is becoming the new strategy for maintenance management. |
SMALL TURBINES
|
The need for electricity supply increases with population growth and with the evolution human increasingly developed technology for its own benefit and convenience. The constant appeal to minimization of environmental impacts and the reduction of greenhouse increasingly result in expanding the use of expanding alternative energy supply and diversifying the Brazilian energy matrix. Highlighting the inclusion of wind generation to have low environmental impact and the wind regime possess complementary characteristics the rainfall regime. By definition wind generation is the generation of energy electricity through wind turbines connected to generators that convert the kinetic energy of the wind to mechanical energy by displacement of the blades and the consequent turning of the rotor. |
MECHANICAL VIBRATION AND TEMPERATURE
|
Rotating machines ideal transform all their energy in working, not producing any kind of destructive energy. However, the interaction of various elements of a machine under cyclic culminates in the dissipation of energy in the form vibration, noise or temperature. Monitor the vibration a machine means increase revenue and mainly extend the life thereof, given that the Vibration causes accelerated wear and the occurrence of failures. |
WIND TURBINE FAILURES AND FAULT DETECTION
|
A wind turbine consists of thousands of components and is subject to different sorts of failures. Some of them are more frequent than others but in order to compare among them it is necessary to consider the downtime they could force for the whole system. In practice, the resultant economic loss which is directly caused by the downtime of a particular component is the most important industry metric for determining the criticality of a machine component. |
RELATED WORK
|
Wind turbine condition monitoring systems collect data from the main components of a wind turbine such as the generator, the gearbox, the main bearing, the shaft, and the yaw system. The purpose of this data-gathering is to minimize downtime and maintenance costs while increasing energy availability and the lifetime service of wind turbine components. An ideal condition monitoring system would monitor all the components using a minimum number of sensors. There have been a few literature reviews on wind turbine condition monitoring. As renewable energies have gained dramatically increasing attention from industries and academia, a great deal of new research has been reported with regard to condition monitoring and fault diagnosis . This chapter aims to review the most recent advances in condition monitoring and fault diagnostic techniques with a focus on wind turbines and their subsystems related to mechanical fault. This section summarizes the monitoring and diagnostic methods for the major subsystems in wind turbines such as gearbox, bearing, and generator which are the primary focus of this study. |
PROPOSED SYSTEM
|
The core objectives of this proposed management of small wind turbine system are to detect the present health condition of the machine, to prevent catastrophic failures caused by rotor imbalance, to improve the power quality before the problem is corrected, to predict the severity level of fault, and to estimate the useful life of the machine. The use of this type of health monitoring system helps to reduce the failure frequency and amount of downtime, maximize the utilization of the wind turbine, and minimize the maintenance overhead and cost due to production lost. Moreover, under the wireless sensor network system, there is no need to install wiring for data collecting and monitoring, thus eliminating the cost of installation and maintenance that would be required by communication cables. |
CONDITION BASED MONITORING SYSTEM FOR WIND TURBINES
|
Condition based monitoring, which is generally referred to as a predictive or proactive maintenance, is a reliable and cost-effective approach in maintaining and running expensive equipment and machines. It is important to identify which technologies for monitoring machine condition will be the most useful and cost-effective in achieving goals and objectives. In this work, we mainly focus on the monitoring of wind turbines, as mechanical components or electrical machines account for the majority of wind turbine equipment, and vibration monitoring is thus a key component of this condition based monitoring system. |
VIBRATION SENSOR EQUIPMENT
|
In the wind power industry, vibration monitoring is used primarily to detect faults in mechanical components such as the bearings and gears installed inside the wind turbine nacelle. The monitoring and fault prediction functions of a condition based monitoring system are based on robust sensor equipment for continuous measurements, and this system performs online evaluation of characteristic fault indicators by use of modern digital signal processing methods. |
MACHINE VIBRATION ANALYSIS
|
Vibration analysis is a proven and effective technology being used in condition monitoring. For the measurement of vibration, different vibration transducers are applied, according to the frequency range. Vibration measurement is commonly done in the gearbox, turbines, bearings, and shaft. For wind turbine application, the measurement is usually done at critical locations where the load condition is at maximum, for example, wheels and bearings of the gearbox, the main shaft of turbine, and bearings of the generator. Different types of sensors are employed for the measurement of vibration: acceleration sensors, velocity sensors, and displacement sensors. |
WIRELESS NETWORK COMMUNICATION
|
ZIGBEE/IEEE 802.15.4 STANDARD |
The IEEE 802.15.4 standard defines the protocol and interconnection of devices via radio communication in a personal area network (PAN). It operates in the ISM (Industrial, Science and Medical) radio bands, at 868 MHz in Europe, 915 MHz in the USA and 2.4 GHz worldwide. The purpose is to provide a standard for ultra -low complexity, ultra-low cost, ultralow power consumption and low data rate wireless connectivity among inexpensive devices. |
BLOCK DIAGRAM OF PROPOSED SYSTEM
|
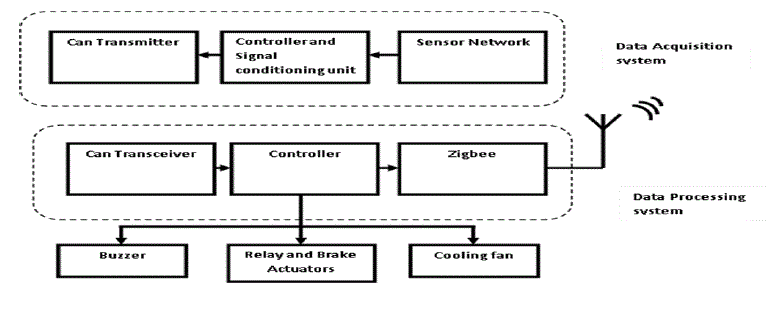 |
Block diagram of Node Station |
MAIN COMPONENTS OF PROPOSED SYSTEM
|
Can Controller Mcp2510 |
The CAN Controller MCP2510 is a Full Controller Area Network (CAN) protocol controller implementing CAN specification V2.0 A/B. It supports CAN1.2, CAN 2.0A, CAN 2.0B Passive, and CAN 2.0BActive versions of the protocol, and is capable of trans-mitting and receiving standard and extended messages. It is also capable of both acceptance filtering and message management. It includes three transmit buffers and two receive buffers that reduce the amount of microcontroller (MCU) management required. The MCU communication is implemented via an industry standard Serial Peripheral Interface (SPI) with data rates up to 5 Mb/s. |
Can Transceiver Mc2551
|
The MCP2551 is a high-speed CAN, fault-tolerant device that serves as the interface between a CAN protocol controller and the physical bus. The MCP2551 provides differential transmit and receive capability for the CAN protocol controller and is fully compatible with the ISO-11898 standard, including 24V requirements. It will operate at speeds of up to 1 Mb/s. Typically, each node in a CAN system must have advice to convert the digital signals generated by a CAN controller to signals suitable for transmission over the bus cabling (differential output). It also provides a buffer between the CAN controller and the high-voltage spikes that can be generated on the CAN bus by outside sources (EMI, ESD, electrical transients, etc.) |
Thermocouple
|
The thermocouples are temperature sensors which have at its terminals, an analog voltage in milli volts generated by the effect derived from the behaviorSeebek some thermoelectric materials. The effect of drift Seebek Thomas J. Seeback noted that in 1821 a circuit Closed formed by two dissimilar metals, is traversed by an electric current when your joints are subjected to a temperature difference .Over time has combined the different elements thermoelectric aiming to obtain sensors that can measure as accurately as possible, increasing temperatures higher. |
Mems Accelerometer
|
The MEMS Accelerometer is a complete three-axis acceleration measurement system on a single monolithic IC. it has a measurement range of ±3 g. It contains a micro-machined sensor and signal conditioning circuit to implement the open loop acceleration measurement architecture. The output signals are analog voltages that are proportional to acceleration. The accelerometer can measure the static acceleration of gravity in tilt sensing applications as well as dynamic acceleration resulting from motion, shock, or vibration. |
BASE STATION
|
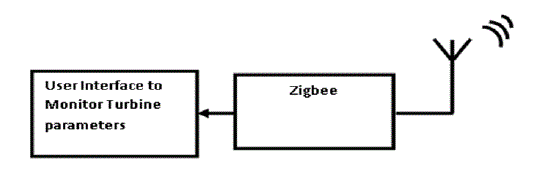 |
Block diagram of Base Station |
The base station includes the network coordination and a personal computer. Thenetwork coordination is primarily responsible for distributing the network address to new rode, notarizing the physical address, and transmitting test data. The network coordination can connect and send the data and information to PC through RS232 or USB port. |
Description of Operation
|
The accelerometer and thermocouple make signal acquisition vibration and temperature respectively, converting them to analog electrical signals, these signals are read and constrained by hardware which subsequently sends through the serial port of the microcontroller. The data packet is sent over the serial read by the ZigBee module which in turn relays them via wireless being picked up by another module that is coupled to the USB port computer. Upon receipt of the signal by the computer, the supervisor executes the first algorithm that separates the package received data and then displays them. |
The interface visualization of the results shows trend graphs that plot measurements for each axis accelerometer and as thermocouples individually presenting the user a single view enabling the rapid operator, the immediate decision making. The interface also provides an instant diagnosis based on limits provided by the user, and command buttons to lock and release the wind turbine acting directly on hardware. To make the software even more versatile, were embedded storage functions and data query historical that allows monitoring of the evolution of failures allowing the application of technical maintenance, which facilitate the programming stops reducing costs operational, and other advantages. |
RESULT
|
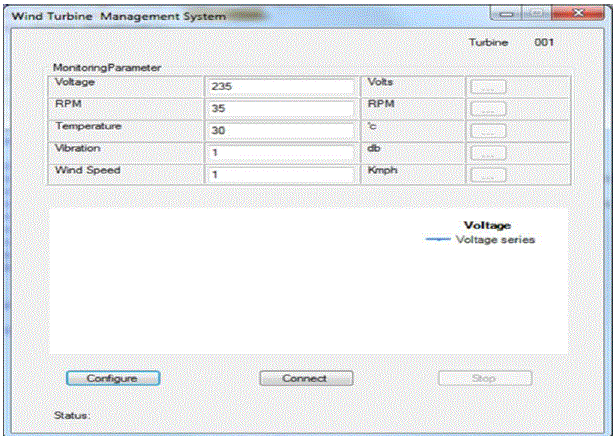 |
Base station - User Interface |
The proposed system enables the management of vibration mechanical as well as the rise in temperature of the turbine using the methodology developed. The software allows user interactivity with the system proposed by a friendly graphical interface, assisting in making Decision to avoid catastrophic effects on the vibration cyclic regime (resonance effect), and excessive temperature the windings and rotating mechanical couplings (Effect Joule) can cause the small wind turbines. The focus of this project is to develop a system effective and robust, easy operation and mainly low cost which permits to manage the vibration indicators and temperature elevation to maximize the life of turbines contributing to the increase of reliability and improve power quality. |
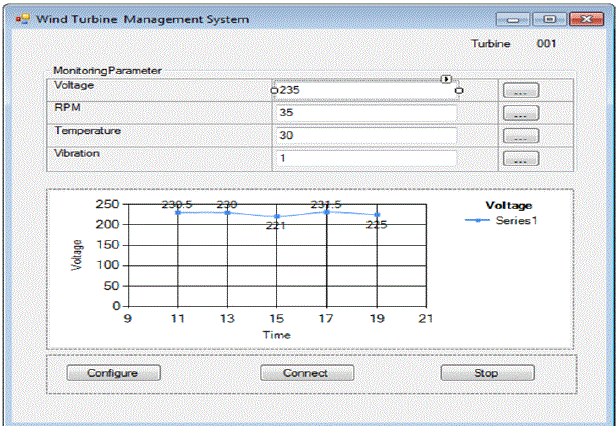 |
Monitoring GUI |
CONCLUSION
|
One of the most serious problems in wind turbines is the possibility of mechanical failure caused by rotor imbalance conditions especially for rotating parts of gears and generators. Therefore, a machine health management system is a very important tool in wind turbines. Moreover, wireless sensor technologies make it possible to measure and control the vibrations of the machine during operation. |
By using an MEMS accelerometer which is low cost, light in weight, compact in size and low in power consumption, a vibration detection method is proposed in this dissertation. Machine vibration Analysis in time and frequency domain has been analyzed and a severity detection technique is also established. These are the essential components for an advance health monitoring system. |
The implementation of a rotor imbalance indicator can be used to estimate the range of severity levels, which makes it possible to detect the abnormalities before failure. It is very useful part of the condition based predictive maintenance. |
|
References
|
- Ren C. Luo, Fellow, ?Wireless and Pyroelectric Sensory Fusion System for Indoor Human/Robot Localization and Monitoring?, IEEE, and Ogst Chen IEEE/ASMETRANSACTIO ONMECHATRONICS, VOL. 18, NO. 3, JUNE 2013
- BojanMrazovac, Milan Z. Bjelica, D raganKukolj, Senior Member, IEEE,Branislav M. Todorovic, Member, IEEE and Nikola Teslic, Member, IEEERT-RK Computer Based Systems, Novi Sad, SerbiaA?Human Detection Method for Residential Smart Energy Systems Based on Zigbee?, RSSI Changes,2012
- M. Weiss, D. Guinard, ?Increasing Energy Awareness ThroughWebenabled Power Outlets?, in proc. of MUM 2010 (9th ACM Inter.Conf. on Mobile and Ubiquitous Multimedia), Limassol, Cyprus,
- J. Han, H. Lee, K.R. Park, ?Remote-Controllable and Energy-SavingRoom Architecture based on ZigBee Communication?, IEEE Trans. onConsumer Electronics, Vol. 55, No. 1, pp. 264-268, 2009
- C. Chao-Chun, W. Ding-Chau, H. Yon-Ming, ?A Novel Method for Unstable-signal Sensor Localization in Smart Home Environments?, International Journal of Smart Home, vol. 2, no. 3, July 2008
- L. Vachhani, A. D. Mahindrakar, and K. Sridharan, ?Mobile robot navigation through a hardware-efficient implementation for control-lawbased construction of generalized Voronoi diagram,? IEEE/ASME Trans.Mechatronics, vol. 16, no. 6, pp. 1083–1095, Dec. 2011.
- M. Collotta, G. Nicolosi, E. Toscano, and O. Mirabella, ?A ZigBee-based network for home heating control,? in Proc. 34th Annu. Conf. IEEE Ind. Electron. Soc., Nov., 2008, pp. 2724–2729.
- K. C. Lee and H. H Lee, ?Network-based fire-detection system via con-troller area network for smart home automation,? IEEE Trans. Consumer Electron., vol. 50, no. 4, pp. 1093–1100, Nov. 2004.
- M. Hazas, J. Scott, and J. Krumm, ?Location-aware computing comes of age,? IEEE Computer, vol. 37, no. 2, pp. 95–97, Feb. 2004.
- K. Lorincz, M. Welsh, ?Motetrack: A robust, decentralized approach to RF-based location tracking,? Personal Ubiquitous Comput., vol. 11, no. 6, pp. 489–503, 2007
|