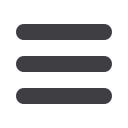
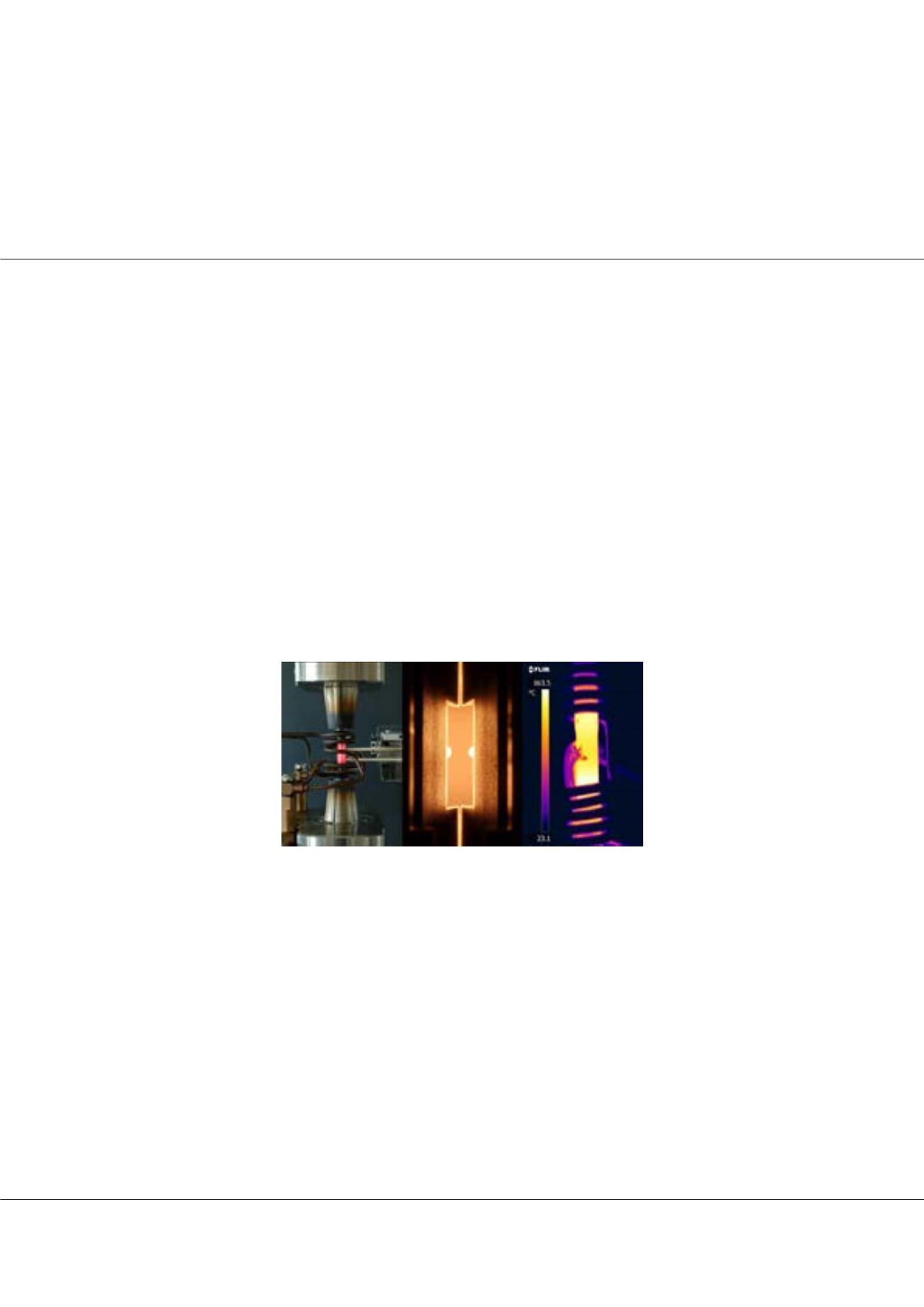
Page 51
Notes:
conferenceseries
.com
Volume 5, Issue 5
Res. Rev. J Mat. Sci. 2017
ISSN: 2321-6212
Advanced Materials 2017
September 07-08, 2017
September 07-08, 2017 | Edinburgh, Scotland
Advanced materials & Processing
11
th
International Conference on
Testing methodologies for thermo-mechanical fatigue evaluation in advanced aerospace materials
Mark Whittaker, Jonathan Jones, Ashley Dyer
and
Jennie Palmer
Swansea University, UK
F
atigue failures are common within structural components used throughout a range of industrial sectors, and are often a critical
design criterion during the specification and development stage of a new product. However, most mechanical testing is performed
under isothermal conditions whichmay not be truly representative of in service conditions.Thermo-mechanical fatigue (TMF) testing
offers the opportunity for the evaluation of a range of advanced material under more appropriate thermal cycles, hence providing
more appropriate lifing approaches to ensure component integrity. TMF tests however, are complicated and difficult to perform, with
much consideration necessary to understand the complex interactions of issues such as the heating/cooling method, the phase angle
between thermal and mechanical strains/stresses, temperature measurement techniques and cycle frequencies. Over the past 15 years,
the Institute of Structural Materials at Swansea University has devoted significant effort in a number of developmental programmes
which have led to internationally recognised expertise in experimental setup and lifing approaches. Consideration in this paper is
given to the experimental difficulties associated with using traditional techniques for temperature and crack length measurements
(thermocouples and direct current potential difference techniques) and the possibility of utilising more innovative approaches such
as thermography is discussed. Research has shown that it is difficult to design a single solution for TMF testing due to the numerous
testing requirements that include peak cycle temperature, heating/cooling rate, and the impact of electromagnetic fields associated
with induction coils. As such, TMF experiments are often by their very nature, bespoke. Future developments such as the generation
of a validated code of practice for crack growth measurements under TMF loading are also discussed.
Biography
Dr Whittaker joined Swansea University in 2003 and has produced over 60 publications including an invited book chapter and 40 papers in leading international
journals on topics including High Temperature Lifing, Thermo-Mechanical Fatigue and Modern Creep Lifing Approaches. He is also a Board Member of the
IOM3 Structure and Properties of Materials Committee. Current research programmes involve sponsorship from EU Clean Skies, Rolls-Royce, EPSRC and
ATI. Dr Whittaker has over 15 years of experience in a wide range of alloys and is leading the development of a code of practice for thermo-mechanical fatigue
crack propagation testing. He is also heavily involved in creep lifing of alloys for the power generation/aerospace sectors, with particular expertise in property
extrapolation using the recently developed 'Wilshire equations'.
m.t.whittaker@swansea.ac.ukMark Whittaker et al., Res. Rev. J Mat. Sci. 2017, 5:5
DOI: 10.4172/2321-6212-C1-005