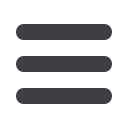

Page 47
conferenceseries
.com
Volume 6
Research & Reviews: Journal of Material Sciences
ISSN: 2321-6212
Ceramics 2018
May 14-15, 2018
May 14-15, 2018 | Rome, Italy
4
th
International Conference and Expo on
Ceramics and Composite Materials
Process development for the ceramic injection molding of oxide short fiber reinforced CMCs
Metin Tülümen, Benjamin Ehreiser, Thomas Hanemann, Rainer Oberacker
and
Volker Piotter
Karlsruhe Institute of Technology, Germany
C
eramic matrix composites (CMCs) are created by adding fibers with variety of fiber structure into various ceramic materials
to provide condition / task adapted properties. On the other hand, ceramic injection molding is an automated net shaping
process that can produce the ceramic parts with complex geometry and good surface quality without the requirement for a
post-processing step. In this study, we produced aluminum oxide CMCs (Al
2
O
3
powder: TMDAR, Taimicron; Al
2
O
3
chopped
fibers: 3M Nextel 610) by using ceramic (μ-) injection molding process. Each step such as feedstock preparation, molding
step, debinding or sintering, has significant effect on the final properties of the CMCs parts. Measurement of density as a
function of time, temperature, fiber content or -orientation coupled with the examination of the final microstructure is a useful
method to evaluate the ceramic parts. The relative density of sintered CMC parts (sintered from 1150 to 1350 2h) decreased
at about 35% with increasing amount of oxide chopped fibers from 0 to 25 Vol. % in feedstock including polymer binding
system. The reason of such a low sintering temperature for aluminum oxide based material is to prevent the grain growth
in the fibers [1]. In addition, the form of the injection mold design defines the fiber orientation that differentiate the density
and mechanical properties of the sintered parts. The difference between tensile specimen (higher orientation) and disc form
(random orientation) is about from 1 to 10% depending on temperature and the amount of fiber in the feedstock. On the other
hand, whether it is hard to define the mechanical characteristic because of highly deformed sintered parts, our first impression
on the results is that the fiber reinforced injection molded parts have lower fracture toughness than common CMC parts with
endless fibers or fabric.
Figure 1:
Fiber orientation and distribution in the neck region of a sintered (at 1250 °C) tensile specimen.
Recent Publications
1. TülümenM, Hanemann T, HoffmannM, Oberacker R, Piotter V. (2017). Process Development for the Ceramic Injection
Molding of Oxide Chopped Fiber Reinforced AluminumOxide. Key Engineering Materials. 742. 231-237. DOI: 10.4028
2. Piotter, V., Hanemann, T., Heldele, R. Mueller, M., Mueller, T., Plewa, K., Ruh, A. (2010) Metal and Ceramic Parts
Fabricated by Microminiature Powder Injection Molding, Int. Journal of Powder Metallurgy, Vol. 46, 2, 21-28.
3. Piotter, V., Bauer, W., Knitter, R., Mueller, M., Mueller, T., Plewa, K. (2010) Powder injection molding of metallic and
ceramic microparts, Microsystem Tech., 17, 251-263
4. Piotter, V., Prokop, J., Ritzhaupt-Kleissl, H.-J., Ruh, A., Hausselt, J. (2010) Multi-component microinjection moulding-
trends and developments; International Journal of Advanced Manufacturing Technology 47, 63-71.
5. Ruh, A., Hanemann, T., Heldele, R., Piotter, V., Ritzhaupt-Kleissl, H.-J., Haußelt, J. (2011) Development of Two-
Component Micropowder Injection Molding (2C MicroPIM): Characteristics of Applicable Materials; Int. J. Appl.
Ceram. Technol. 8, 194-202.
Metin Tülümen et al., Res. Rev. J Mat. Sci. 2018, Volume 6
DOI: 10.4172/2321-6212-C1-014