Keywords
|
Active power filter (APF), power angle control (PAC), power quality, reactive power compensation, unified power quality conditioner (UPQC), voltage sag and swell compensation. |
INTRODUCTION
|
The modern power distribution system is becoming highly vulnerable to the different power quality problems [1], [2]. The extensive use of nonlinear loads is further contributing to increased current and voltage harmonics issues. Furthermore, the penetration level of small/large-scale renewable energy systems based on wind energy, solar energy, fuel cell, etc., installed at distribution as well as transmission levels is increasing significantly. This integration of renewable energy sources in a power system is further imposing new challenges to the electrical power industry to accommodate these newly emerging distributed generation systems [3]. To maintain the controlled power quality regulations, some kind of compensation at all the power levels is becoming a common practice [5]–[9]. At the distribution level, UPQC is a most attractive solution to compensate several major power quality problems [7]–[9], [14]–[28]. The general block diagram representation of a UPQC-based system is shown in Fig. 1. It basically consists of two voltage source inverters connected back to back using a common dc bus capacitor. This paper deals with a novel concept of optimal utilization of a UPQC. |
Since the series inverter of UPQC in this case delivers both active and reactive powers, it is given the name UPQCS (S for complex power). The key contributions of this paper are outlined as follows. |
1) The series inverter of UPQC-S is utilized for simultaneous voltage sag/swell compensation and load reactive power compensation in coordination with shunt inverter. |
2) In UPQC-S, the availableVAloading is utilized to its maximum capacity during all the working conditions contrary to UPQC-VAmin where prime focus is to minimize the VA loading of UPQC during voltage sag condition. |
3) The concept of UPQC-S covers voltage sag as well as swell scenario. |
In this paper, a detailed mathematical formulation of PAC for UPQC-S is carried out. The feasibility and effectiveness of the proposed UPQC-S approach are validated by simulation as well as experimental results. |
The phasor representation of the PAC approach under a rated steady-state condition is shown in Fig. 2 [15]. According to this theory, a vector _VSrwith proper magnitude VSr and phase angle ÃÂÃâ¢Sr when injected through series inverter gives a power angle δ boost between the source VS and resultant load V _ L voltages maintaining the same voltage magnitudes. This power angle shift causes a relative phase advancement between the supply voltage and resultant load current I_ L , denoted as angle β. In other words, with PAC approach, the series inverter supports the load reactive power demand and thus, reducing the reactive power demand shared by the shunt inverter. |
Unified Power Quality Conditioner
|
The provision of both DSTATCOM and DVR can control the power quality of the source current and the load bus voltage. In addition, if the DVR and STATCOM are connected on the DC side, the DC bus voltage can be regulated by the shunt connected DSTATCOM while the DVR supplies the required energy to the load in case of the transient disturbances in source voltage. The configuration of such a device (termed as Unified Power Quality Conditioner (UPQC)) is shown in Fig. 2. This is a versatile device similar to a UPFC. However, the control objectives of a UPQC are quite different from that of a UPFC. |
CONTROL OBJECTIVES OF UPQC
|
The shunt connected converter has the following control objectives |
1. To balance the source currents by injecting negative and zero sequence components required by the load |
2. The compensate for the harmonics in the load current by injecting the required harmonic currents |
3. To control the power factor by injecting the required reactive current (at fundamental frequency) |
4. To regulate the DC bus voltage. |
VOLTAGE SAG
|
Voltage sags and momentary power interruptions are probably the most important PQ problem affecting industrial and large commercial customers. These events are usually associated with a fault at some location in the supplying power system. Interruptions occur when the fault is on the circuit supplying the customer. But voltage sags occur even if the faults happen to be far away from the customer's site. Voltage sags lasting only 4-5 |
cycles can cause a wide range of sensitive customer equipment to drop out. To industrial customers, voltage sag and a momentary interruption are equivalent if both shut their process down. A typical example of voltage sag is shown in fig 1. The susceptibility of utilization equipment to voltage sag is dependent upon duration and magnitude of voltage sags and can be define |
POWER QUALITY IN POWER DISTRIBUTION SYSTEMS
|
Most of the more important international standards define power quality as the physical characteristics of the electrical supply provided under normal operating conditions that do not disrupt or disturb the customer’s processes. Therefore, a power quality problem exists if any voltage, current or frequency deviation results in a failure or in a bad operation of customer’s equipment. However, it is important to notice that the quality of power supply implies basically voltage quality and supply reliability. Voltage quality problems relates to any failure of equipment due to deviations of the line voltage from its nominal characteristics, and the supply reliability is characterized by its adequacy (ability to supply the load), security (ability to withstand sudden disturbances such as system faults) and availability (focusing especially on long interruptions). Power quality problems are common in most of commercial, industrial and utility networks. Natural phenomena, such as lightning are the most frequent cause of power quality problems. Switching phenomena resulting in oscillatory transients in the electrical supply, for example when capacitors are switched, also contribute substantially to power quality disturbances. Also, the connection of high power non-linear loads contributes to the generation of current and voltage harmonic components. Between the different voltage disturbancesthat can be produced, the most significant and critical power quality problems are voltage sags due to the high economic losses that can be generated. Short-term voltage drops (sags) can trip electrical drives or more sensitive equipment, leading to costly interruptions of production. For all these reasons, from the consumer point of view, power quality issues will become an increasingly important factor to consider in order satisfying good productivity. On the other hand, for the electrical supply industry, the quality of power delivered will be one of the distinguishing factor for ensuring customer loyalty in this very competitive and deregulated market. To address the needs of energy consumers trying to improve productivity through the reduction of power quality related process stoppages and energy suppliers trying to maximize operating profits while keeping customers satisfied with supply quality, innovative technology provides the key to costeffective power quality enhancements solutions. However, with the various power quality solutions available, the obvious question for a consumer or utility facing a particular power quality problem is which equipment provides the better solution. |
VOLTAGE SAG/SWELL COMPENSATION UTILIZING UPQC-PAND UPQC-Q
|
Consider that the UPQC system is already working under PAC approach, i.e., both the inverters are compensating the load reactive power and the injected series voltage gives a power angle δ between resultant load and the actual source voltages. If a sag/swell condition occurs on the system, both the inverters should keep supplying the load reactive power, as they were before the sag. Additionally, the series inverter should also compensate the voltage sag/swell by injecting the appropriate voltage component. In other words, irrespective of the variation in the supply voltage the series inverter should maintain same power angle δ between both the voltages. However, if the load on the system changes during the voltage sag condition, the PAC approach will give a different δ angle. The increase or decrease in new δ angle would depend on the increase or decrease in load reactive power, respectively. |
Let us represent a vector _VSr1 responsible to compensate the load reactive power utilizing PAC concept and vector _VSr2 responsible to compensate the sag on the system using active power control approach. Thus, for simultaneous compensation, as noticed from Fig. 3, the series inverter should now supply a component which would be the vector sum of _VSr1 and _VSr2. This resultant series inverter voltage _V _ Sr will maintain the load voltage magnitude at a desired level such that the drop in source voltage will not appear across the load terminal. Furthermore, the series inverter will keep sharing the load reactive power demand. |
To support the active power required during voltage sag condition, the source delivers the extra source current The phasor representation for PAC of UPQC-S during a voltage swell on the system is shown in Fig. 4. Let us represent a vector VSr3 responsible to compensate the swell on the system using active power control approach. For simultaneous compensation, the series inverter should supply the _VSr1 component to support the load reactive power and _VSr3 to compensate the swell on the system. The resultant series injected voltage _V __ Sr would maintain the load voltage magnitude at a desired level while supporting the load reactive power. For voltage swell compensation using active power control approach. |
UPQC-S CONTROLLER
|
A detailed controller for UPQC based on PAC approach is described in [15]. In this paper, the generation of reference signals for series inverter is discussed. Note that, as the series inverter maintains the load voltage at desired level, the reactive power demanded by the load remains unchanged (assuming load on the system is constant) irrespective of changes in the source voltage magnitude. Furthermore, the power angle δ is maintained at constant value under different operating conditions. Therefore, the reactive power shared by the series inverter and hence by the shunt inverter changes as given by (47) and (54). The reactive power shared by the series and shunt inverters can be fixed at constant values by allowing the power angle δ to vary under voltage sag/swell condition. |
The control block diagram for series inverter operation is shown in Fig. 5. The instantaneous power angle δ is determined using the procedure give in [15]. Based on the system rated specifications, the value of the desired load voltage is set as reference load voltage k. The instantaneous value of factors kfand nOis computed by measuring the peak value of the supply voltage in real time. The magnitudes of series injected voltage VSr and its phase angle ÃÂÃâ¢Sr are then determined using (15) and (17). A phase locked loop is used to synchronize and to generate Instantaneous time variable reference signals v Sr,a, v Sr,b, v Sr,c.The reference signals thus generated give the necessary series injection voltages that will share the load reactive power and compensate for voltage sag/swell as formulated using the proposed approach. The error signal of actual and reference series voltage is utilized to perform the switching operation of series inverter of UPQC-S. |
SIMULATION RESULTS
|
The performance of the proposed concept of simultaneous load reactive power and voltage sag/swell compensation has been evaluated by simulation. To analyze the performance of UPQC-S, the source is assumed to be pure sinusoidal. Furthermore, for better visualization of results the load is considered as highly inductive. The supply voltage which is available at UPQC terminal is considered as three phase, 60 Hz, 600 V (line to line) with the maximum load power demand of 15 kW + j 15 kVAR (load power factor angle of 0.707 lagging). The simulation results for the proposed UPQC-S approach under voltage sag and swell conditions are given in Fig. 11. Before time t1 , the UPQC-S system is working under steadystate condition, compensating the load reactive power using both theinverters. |
Fig. 6. Simulation results: performance of the proposed UPQC-S approach under voltage sag and swell conditions. (a) Supply voltage. (b) Load voltage. (c) Series inverter injected voltage. (d) Self-supporting dc bus voltage. (e) Enlarged power angle δ relation between supply and load voltages during steady-state condition. (f) Supply current. (g) Load current. (h) Shunt inverter injected current. (i) Enlarged power angle δ during voltage sag condition.(j) Enlarged power angle δ during voltage swell condition. |
A power angle δ of 21° is maintained between the resultant load and actual source voltages. The series inverter shares 1.96 kVAR per phase (or 5.8 kVAR out of 15 kVAR) demanded by the load. Thus, the reactive power support from the shunt inverter is reduced from 15 to 9.2 kVAR by utilizing the concept of PAC. In other words, the shunt inverter rating is reduced by 25% of the total load kilovoltampere rating. At time t1 = 0.6 s, a sag of 20% is introduced on the system (sag last till time t = 0.7 s). Between the time period t = 0.7 s and t = 0.8 s, the system is again in the steady state. A swell of 20% is imposed on the system for a duration of t2 = 0.8–0.9 s. The active and reactive power flows through the source, load, and UPQC are given in Fig. 6. The distinct features of the proposed UPQC-S approach are outlined as follows. |
From Fig.6(a) and (b), the load voltage profile is maintained at a desired level irrespective of voltage sag (decrease) or swell (increase) in the source voltage magnitudes. During the sag/swell compensation, as viewed from Fig. 6(f), to maintain the appropriate active power balance in the network, the source current increases during the voltage sag and reduces during swell condition. |
2) As illustrated by enlarged results, the power angle δ between the source and load voltages during the steady state [see Fig. 6(e)], voltage sag and voltage swell is maintained at 21°. |
3) The UPQC-S controller maintains a self-supporting dc link voltage between two inverters [see Fig. 6(d)]. |
4) From Fig. (c) and (d), the reactive power supplied by the series inverter during the voltage sag condition increases due to the increased source current. As load reactive power demand is constant, the reactive power supplied by the shunt inverter reduces accordingly. On the other hand, during the voltage swell condition, the reactivepower shared by the series inverter reduces and the shunt inverter increases. The reduction and increment in the shunt compensating current magnitude, as seen from Fig. 6(h), also confirm the aforementioned fact. Although the reactive power shared by the series and shunt inverters is varied, the sum of their reactive powers always equals the reactive power demanded by the load. |
Thus, the aforementioned simulation study illustrates that with PAC of UPQC-S, the series inverter can compensate the load reactive power and voltage sag/swell simultaneously. The shunt inverter helps the series inverter to achieve the desired performance by maintaining a constant self-supporting dc bus. |
Table I gives the power losses associated with UPQC with and without PAC approach under different scenarios. The power loss is computed as the ratio of losses associated with UPQC to the total load power. The rms values of current flowing through shunt and series inverters and series injection voltage are also given in Table I. Initially, it is considered that the shunt inverter alone supports the load reactive power and the series inverter is assumed to be in OFF condition. The series injection transformer is also short circuited. This operating condition gives the losses in the shunt part of UPQC, which are found as 0.74% of the rated load power. In the second condition, the series inverter is turned on as well. The percent power losses, when both the inverters of UPQC are in operation, are noticed as 1.7%. Under this condition when UPQC is controlled as UPQC-S to support the load reactive power using both shunt and series inverters, controlled by the PAC approach, losses are observed as 1.2%. The power loss in the UPQC system with PAC approach thus is lower than the normal UPQC control. This is an interesting outcome of the PAC approach even when the series inverter deals with both active and reactive powers due to δ shift between source and load voltages. One may expect to increase the power loss with the UPQC-S system. The reduction in the power loss is mainly due to the reduction in the shunt inverter rams current from 20.20 A (without PAC approach) to 13.18 A (with PAC approach). Second, the current through the series inverter (which is almost equal to the source current) remains unchanged. Similarly from the Table I, the power losses utilizing the PAC approach, during voltage sag and swell conditions, are observed lower than those without PAC approach. This study thus suggests that the PAC approach may also help to reduce the power loss associated with UPQC system in addition to the previously discussed advantages. The significant advantage of UPQC-S over general UPQC applications is that the shunt inverter rating can be reduced due to reactive power sharing of both the inverters. |
CONCLUSION
|
In this paper, a new concept of controlling complex power (simultaneous active and reactive powers) through series inverter of UPQC is introduced and named as UPQC-S. The proposed concept of the UPQC-S approach is mathematically formulated and analyzed for voltage sag and swell conditions. The developed comprehensive equations for UPQC-S can be utilized to estimate the required series injection voltage and the shunt compensating current profiles (magnitude and phase angle), and the overall VA loading both under voltage sag and swell conditions. The simulation and experimental studies demonstrate the effectiveness of the proposed concept of simultaneous voltage sag/swell and load reactive power sharing feature of series part of UPQC-S. The significant advantages of UPQC-S over general UPQC applications are: 1) themultifunction ability of series inverter to compensate voltage variation (sag, swell, etc.) while lagging power factor; DC bus: dc bus capacitor = 1100μF/220 V, reference dc bus voltage = 150 V; UPQC: shunt inverter coupling inductance = 5mH, shunt inverter switching type = analog hysteresis current controller with average switching frequency between 5 and 7 kHz, series inverter coupling inductance = 2mH, series inverter ripple filter capacitance = 40μF, series inverter switching type = analog triangular carrier pulse width modulation with a fixed frequency of 5 kHz, series voltage injection transformer turn ratio = 1:3, DSP sampling time = 0μs. |
Tables at a glance
|
 |
Table 1 |
|
Figures at a glance
|
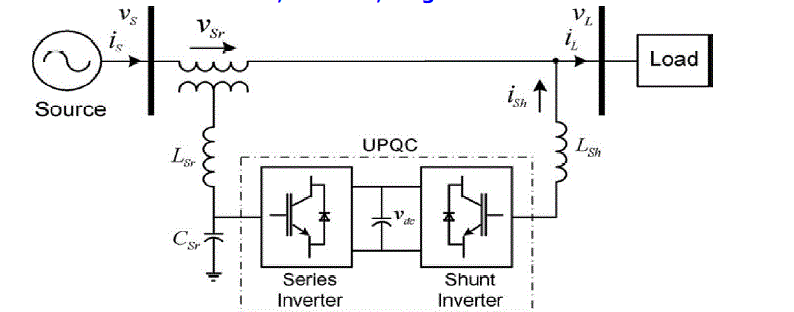 |
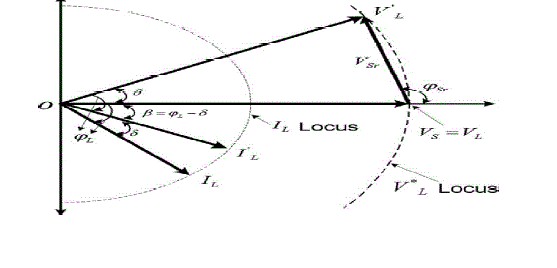 |
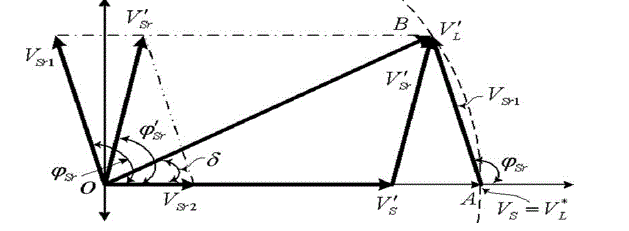 |
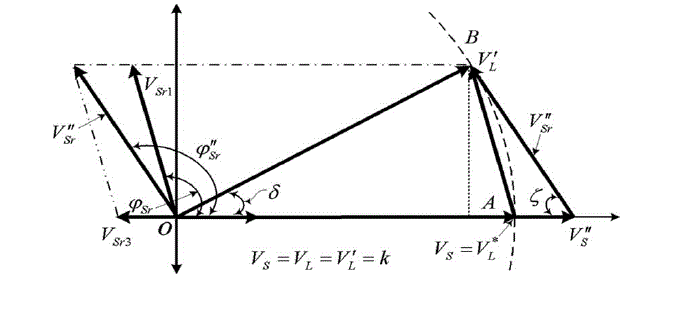 |
Figure 1 |
Figure 2 |
Figure 3 |
Figure 4 |
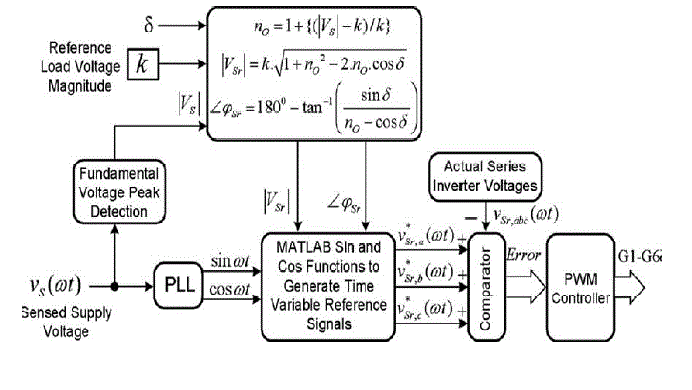 |
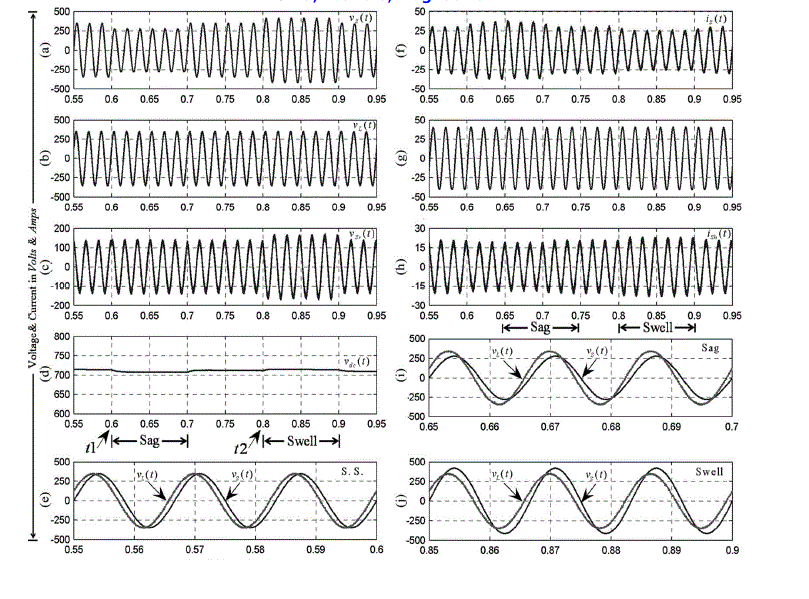 |
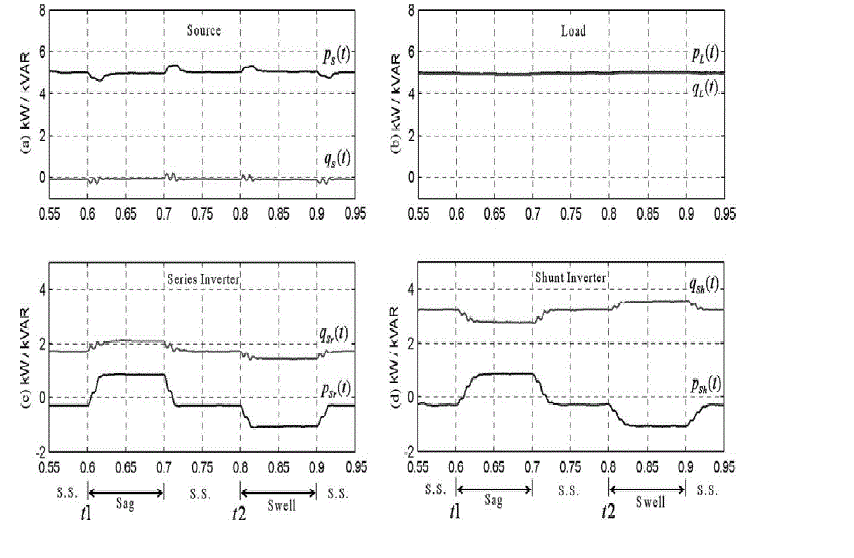 |
Figure 5 |
Figure 6 |
Figure 7 |
|
References
|
- R. C. Dugan, M. FMcGranaghan, and H. W. Beaty, Electrical PowerSystems Quality.. New York: McGraw-Hill, 1996, p. 265.
- C. Sankaran, Power Quality. Boca Raton, FL: CRC Press, 2002, p. 202.
- R. A. Walling, R. Saint, R. C. Dugan, J. Burke, and L. A. Kojovic, “Sum-mary of distributed resources impact on power delivery systems,”IEEETrans. Power Del., vol. 23, no. 3, pp. 1636–1644, Jul. 2008.
- L. Gyugyi, “Unified power-flow control concept for flexible AC transmis-sion systems,” IEE – C Gene. Trans. Distr., vol. 139, no. 4, pp. 323–331, Jul. 1992.
- N. G.Hingorani and L. Gyugyi, Understanding FACTS: Concepts andTechnology of Flexible AC Transmission Systems.NewYork:IEEEPress,2000p.432.6.
- V. K. Sood, HVDC and FACTS Controllers – Applications of Static Con-verters in Power Systems. Boston, MA: Kluwer, 2004, p. 295.
- A. Ghosh and G. Ledwich, Power Quality Enhancement Using CustomPower Devices. Boston, MA: Kluwer, 2002, p. 460.pp. B. Singh, K. Al-Haddad, and A. Chandra, “A review of active power filters for power quality improvement,” IEEE Trans. Ind. Electron., vol. 45, no. 5, 960–971, Oct. 1999.
- M. El-Habrouk, M. K. Darwish, and P. Mehta, “Active power filters: A review,” IEE Electr. Power Appl., vol. 147, no. 5, pp. 403–413, Sep.2000.
- Doncker, C. Meyer, R. W. De, W. L. Yun, and F. Blaabjerg, “Optimized control strategy for a medium-voltage DVR—Theoreticalinvestigations and experimental results,” IEEE Trans. Power Electron., vol. 23, no. 6,pp. 2746–2754, Nov. 2008.
- C. N. Ho and H. S. Chung, “Implementation and performance evaluation of a fast dynamic control scheme for capacitor-supported interline DVR,” IEEE Trans. Power Electron., vol. 25, no. 8, pp. 1975–1988, Aug. 2010.
- Y. Chen, C. Lin, J. Chen, and P. Cheng, “An inrush mitigation technique of load transformers for the series voltage sag compensator,” IEEE Trans.Power Electron., vol. 25, no. 8, pp. 2211–2221, Aug. 2010.
- S. Subramanian and M. K. Mishra, “Interphase AC–AC topology for voltage sag supporter,” IEEE Trans. Power Electron., vol. 25, no. 2, pp. 514–518, Feb. 2010.
- H. Fujita and H. AkagiIEEE Trans. Power Electron., vol. 13, no. 2, pp. 315–322, Mar. 1998.
- V. Khadkikar and A. Chandra, “A new control philosophy for a uni-fied power quality conditioner (UPQC) to coordinate load-reactive power demand between shunt and series inverters,” IEEE Trans. Power Del., vol. 23, no. 4, pp. 2522–2534, Oct. 2008.
- M. Vilathgamuwa, Z. H. Zhang, and S. S. Choi, “Modeling, analysis and control of unified power quality conditioner,” in Proc. IEEE Harmon.Quality Power, Oct. 14–18, 1998, pp. 1035–1040.
- M. Gon, H. Liu, H. Gu, and D. Xu, “Active voltage regulator based on novel synchronization method for unbalance and fluctuation compensation,” in Proc. IEEE Ind. Electron. Soc (IECON), Nov. 5–8,, 2002, pp. 1374–1379.
- M. S. Khoor and M. Machmoum, “Simplified analogical control of a unified power quality conditioner,” in Proc. IEEE Power Electron. Spec.Conf. (PESC), Jun., 2005, pp. 2565–2570.
- V. Khadkikar, A. Chandra, A. O. Barry, and T. D. Nguyen, “Analysis of power flow in UPQC during voltage sag and swell conditions for selection of device ratings,” in Proc. IEEE Electr. Computer Eng. (CCECE), May 2006, pp. 867–872.
- B. Han, B. Bae, H. Kim, and S. Baek, “Combined operation of uni-fied power-quality conditioner with distributed generation,” IEEE Trans.Power Del., vol. 21, no. 1, pp. 330–338, Jan. 2006.
- H. R. Mohammadi, A. Y. Varjani, and H. Mokhtari, “Multiconverteruni-fied power-quality conditioning system: MC-UPQC,” IEEE Trans. PowerDel., vol. 24, no. 3, pp. 1679–1686, Jul. 2009.
- I. Axente, J. N. Ganesh, M. Basu, M. F. Conlon, and K. Gaughan, “A 12-kVA DSP-controlled laboratory prototype UPQC capable of
- V. Khadkikar and A. Chandra, “A novel control approach for unified power quality conditioner Q without active
- M. Yun, W. Lee, I. Suh, and D. Hyun, “A new control scheme of unified power quality compensator-Q with minimum power injection,” inProc.IEEE Ind. Electron. Soc. (IECON), Nov. 2–6,, 2004, pp. 51–56.
- Y. Y. Kolhatkar and S. P. Das, “Experimental investigation of a single-phase UPQC with minimum VA loading,” IEEE Trans. Power Del., vol. 22, no. 1, pp. 373–380, Jan. 2007.
- D. O. Kisck, V. Navrapescu, and M. Kisck, “Single-phase unified power quality conditioner with optimum voltage angle injection for minimum VA requirement,” in Proc. IEEE Power Electron. Spec. Conf. (PESC), Jun. 17–21, 2007, pp. 574–579.
- G. S. Kumar, P. H. Vardhana, B. K. Kumar, and M. K. Mishra, “Mini-mization of VA loading of unified power quality conditioner (UPQC),” in Proc. IEEE Powereng, Mar. 18–20, 2009, pp. 552–557.
|