Keywords
|
Wind, Power, Generation, Estimation, Storage, Efficiency |
INTRODUCTION
|
Green energy in recent times has become the most interesting focus of power provision by several nations of the world, and will continue to be so especially for the non-depleting renewable energy sources such as solar, wind, and tidal. The spread of this development is increasing daily and gradually influencing the demand and choice of energy usage in most developing countries. Apart from hydropower systems being used in most African countries, solar power development is more visible among other renewable sources due to the abundant energy from the sun. However, the heating effect of the sun has also created wind in some areas which can be tapped if maximum energy is to be derived. Alhough wind is an erratic source of energy; it is a very feasible source of energy if supplemented with other sources to form a hybrid system or with storage to cater for low wind periods. As the provision of power is tending towards micro-grid and personal supply systems, several options on how to store excess power produced and further retrieve it back in the time of need are being considered and more emerging. |
To further support the green energy philosophy, efficient storage systems that are environment-friendly must be used. Batteries have been used over the years for this purpose but are not green enough due to acid fumes pollution, and cost. Recently, greater focus has been placed on the use of new technologies such as fuel cell and the potential power of water pumped to a height. Excess power produced from a solar or wind system can be used to pump water to a height which in turn can be used to generate electricity from hydro-turbines. On the other hand, fuel cell employs a technology that produces a direct current (DC) voltage from the combination of hydrogen and oxygen. This combination is very efficient as a source of energy and only produces pure water as a byproduct. Of course, oxygen is naturally available but hydrogen can be produced through a process known as electrolysis. Hence, excess power generated from solar or wind sources can be used to produce hydrogen which can be stored for power generation at down times. |
To derive the required alternating current (AC) power from the fuel cell however, a power converting unit most be used. This converter is generally referred to as an inverter. An inverter is an electronic device that converts DC power to AC power and comes in different power ratings. The rating of an inverter selected for use basically depends on the amount of load it is to carry. In this paper we present an estimation model for maximum output power derivation from a wind—hydrogen—fuel-cell—inverter system given the system’s efficiency and wind speed. |
RELATED WORKS
|
Wind is energy in motion caused basically by differential heating of the earth’s surface and partially by earth’s rotation [1]. This moving energy is very unstable in a fixed location with respect to time and exists variably within a day, season, year, etc. This notwithstanding, various wind power extraction technologies have been developed to meet with the wind’s erratic behavior leading to wind prediction for economic improvement [2][3]. This is done specifically in two ways which are hybrid system development and/or the use of storage technology to support down times. |
Wen-Jei and Orhan [4] presented a wind-energy—hydrogen storage hybrid power generation system and analyzed how useful energy can be derived from the theoretically available wind energy. Their work evaluates wind mill models in terms of components efficiency to determine losses and useful energy from a wind mill. They further discussed the process of hydrogen production through electrolysis and explained the effect of temperature and pressure on the efficiency of electrolyzers. In conclusion they proposed the storage of hydrogen in its compressed gaseous form to reduce loss of energy in the wind—hydrogen system. Xiangjun Li et al [5] presented several models for power quality control in a wind—fuel-cell—battery—hydrogen electrolyzer hybrid system for micro-grid power generation. In their work they considered the production of hydrogen mainly from a wind power source, stored in hydrogen tanks and to be reconverted to electricity in a proton exchange membrane fuel cell. They then proposed that energy storage technology would resolve random variations in renewable power sources. Results from simulations carried out shows that the use of proportional integral (PI) and fuzzy controllers can well compensate the power fluctuations in micro-grid power systems. They also show that power quality improvement can be achieved with the use of load-controllable electrolyzer system. Pyle et al [6] described how hydrogen can be produced from a solar source and stored for home power usage. The work demonstrated how hydrogen will serve as a resource that complements solar energy for home needs and as a utility grid backup. Colt and Gilbert [7] presented an economic analysis of an integrated wind-hydrogen energy system for small Alaska community where they proposed that an integrated wind-hydrogen supply of electricity, heat, and transportation fuel could serve the power need of isolated communities at lower cost compared to a collection of separate systems. Sarkar et al [8] presented an improved wind turbine blade efficiency and power calculation by identifying critical components, their failure mode, and determination of the root cause of failure in order to design a wind power generation system. |
WIND-HYGROGEN-FUEL CELL- INVERTER HYBRID MODEL
|
Here, we present a wind—hydrogen—fuel-cell—inverter model as shown in Figure 1 to enable us investigate the flow of power to a connected load. A wind energy generation system may be composed of one or more wind turbines coupled together to produce the require amount of power. The power produced is used in this model to either power any connected load, produce hydrogen, or do both at the same time. Hydrogen produced is stored and converted to electrical energy for running the load through a fuel-cell—inverter system. Several factors determine the amount of power available to the load and how long the system can run without winds. These factors which include wind speed, air density, size of turbine blades, turbine transmission and generator efficiency, rate of hydrogen production, electrolyzer efficiency, hydrogen storage capacity, fuel cell size and fuel cell efficiency, inverter rating and its efficiency, and the system’s autonomy. |
A. Mathematical Model for Power Estimation Analysis |
With the forgoing, we estimate the total derivable power from a wind power generation system using the wind—hydrogen—fuel-cell—inverter model as a function of wind power given system’s component efficiencies. Hence, we analyze the model as follows using the representation shown in Figure 2. |
LP = Load power, TPn = Turbine n power, GP = Total generated power from farm, GEP = Excess power generated, HV = Hydrogen volume produced, HPL = Power loss in hydrogen production, EINL = Power loss in inverter, FCL = Fuel Cell losses, FCE = Energy produced by fuel cell, PINV = Inverter output power From Figure 2, for the load to be directly powered from the farm then, |
(1) |
And |
(2) |
Therefore, |
(3) |
Now, power produced in a single wind turbine is given by |
(4) |
Where, |
P = power (watt), ρ = air density (kg/m3), A = swept area of turbine blades (m), V = wind velocity (m/s) If we assume n turbine of equal blade sizes and swept area with air flowing in the same direction such that all turbines rotate at the same speed. Then the total generated power will be given as: |
(5) |
Where, |
TP = P = single turbine output power |
TPL = power loss in a single turbine due to efficiency |
Assuming x% efficiency for a single turbine, percentage power loss will be (1 – x)%. Therefore, |
(6) |
Hence, putting (6) into (5) |
(7) |
Substituting (4) into (7) therefore, |
(8) |
Note that: x = CP.?T.?G |
Where CP = coefficient of performance or turbine efficiency |
?T = turbine transmission efficiency |
?G = turbine generator efficiency |
Again, hydrogen production will only take place when excess power output is produced by the generators. That is |
(9) |
Therefore, |
(10) |
Assuming total excess power generated is used to produce hydrogen, then: |
(11) |
If the electrolyzer has an efficiency of h%, percentage power loss during hydrogen production is (1- h)%. Hence, |
(12) |
Substituting (12) into (11) therefore, |
(13) |
Putting (8) and (13) into (10) we have that, |
 |
From this expression, |
(14) |
Assuming hydrogen production is run for a time t, energy EH stored and derivable from hydrogen volume HV is, |
EH=HVT |
Therefore, |
(15) |
This stored energy is converted into useful electrical power at the fuel cell unit. If the fuel cell has an efficiency of y%, then percentage energy loss at the fuel cell is (100 – y)%. From figure 2, |
(16) |
But, |
(17) |
Substituting (15) into (17) produce. |
(18) |
Substituting (15) and (18) into (16) therefore, |
(19) |
If this energy is used to produce required load power from the inverter with an efficiency of z%, energy loss will be, |
(20) |
Putting (19) into (20) yields, |
(21) |
From figure 2, we have that, |
(22) |
Where T is the hydrogen—fuel cell—inverter system autonomy. |
Therefore, |
 |
Equation (23) gives the maximum power that can be derived from the Wind—Hydrogen—Fuel-cell—Inverter system when run for a period of time T (autonomy) on a specified load power LP. |
At moments where, LP< GP it is desirable to produce hydrogen with GP and it is therefore assumed that LP is zero in equation (23) for this condition thus, derivable power from the system will be |
 |
B. Power Distribution and Control |
As presented in section IV, certain conditions must be met in order to power the applied load directly from the generated power as well as produced hydrogen at any given time. This power distribution process must utilize some control measures to ensure power stability in the system since wind power is randomly erratic. Using Figure 3 therefore, we present an algorithm for system power control both for hydrogen production and load activation. |
PT = Power transducer, HVT = Hydrogen volume transducer, DCS = Distribution control Signal |
PT = Power transducer, HVT = Hydrogen volume transducer, DCS = Distribution control Signal |
For the system to effectively control and distribute power in the model, the control unit must determine the following conditions: (1) is GP < LP?, (2) is EH < FCL + EINL or HV < (FCL + EINL)/t ? |
To find these conditions, GP is sensed with PT and HV is sensed with HVT and fed to the control unit. Using these signals, power distribution and inverter output control could be affected in the following algorithm. |
START
|
Initialize |
DO FOREVER |
IF (GP > LP) or (GP = LP) |
Power load directly from generator (DCS = ON) |
WHILE (GP > LP) |
Supply power for hydrogen production |
END WHILE |
ELSE IF (GP < LP) |
Do not power load from generator (DCS = OFF) |
Supply generated power for hydrogen production |
IF (HV > (FCL + EINL)/t) |
Power load from Inverter (ICS = ON) |
ELSE IF (HV < (FCL + EINL)/t) or (HV = (FCL + EINL)/t) |
Do not power load from Inverter (ICS = OFF) |
END IF |
END IF |
END DO |
This algorithm is further represented with a flowchart of Figure 4. |
SIMULATIONS AND RESULTS
|
In order to simulate the estimation model presented, we used the MATLAB/SIMULINK wind variation model presented in [5] as shown in Figure 5 to generate a wind pattern as an input to the model. |
Next, the model to represent equation (4) is built in MATLAB/SIMULINK as shown in Figure 6 to determine power extracted from the wind by a single turbine (n = 1) with a given swept area (A = 5m), air density (=1.293) and turbine efficiency (x = CP.?T.?G = 59.26%) given by the Betz coefficient [8]. |
Finally, a MATLAB/SIMULINK representation was built as shown in Figure 7 for the estimation model in a unit time of hydrogen production and autonomy (i.e. t = T =1) with h = 85%, y = 90% and z = 65% to determine how much power can be stored and derived from the Wind—Hydrogen—Fuel-cell—Inverter system at any given wind speed. Table 1 shows the simulated results output data. The results show that an increased non-linear amount of power could be generated from the turbine at increased wind speed. The non-linearity results from the properties of the turbine components leading to the general cut-in and cut-out speed behaviour of turbines. At wind speed values less than 1m/s, no significant output power is generated. A wind speed shift of 0.76m/s between the two lowest values from 0.33m/s to 1.09m/s (columns 12 and 27) produced an output difference of 2.4W from 0.07W (at 0.33m/s) to 2.47W (at 1.09m/s). |
CONCLUSION
|
The result of our simulations show that the output proportional deviation kept increasing until the cut-in speed (the speed at which the least expected power output is produced) was reached and up to the rated output. The output then remained constant as stated in [9] till the cut-out speed is reached where the turbine must be shutdown to avoid possible breakdown. |
As shown in the plot of Figure 8, the power available at the inverter output at an assumed inverter efficiency of 65%, fuel-cell efficiency of 90% and electrolyzer efficiency of 85% is approximately half of total turbine output. Present day electrolyzers and fuel-cells are still at low efficiencies [10][11][12] which are being improved upon. Hence, more than half of power derived from the wind could be lost to hydrogen production and electrical power conversion. However, when run for a long period of time, more energy can be derived and stored in large hydrogen volume that could sustain load at down times. |
Tables at a glance
|
 |
Table 1 |
|
|
Figures at a glance
|
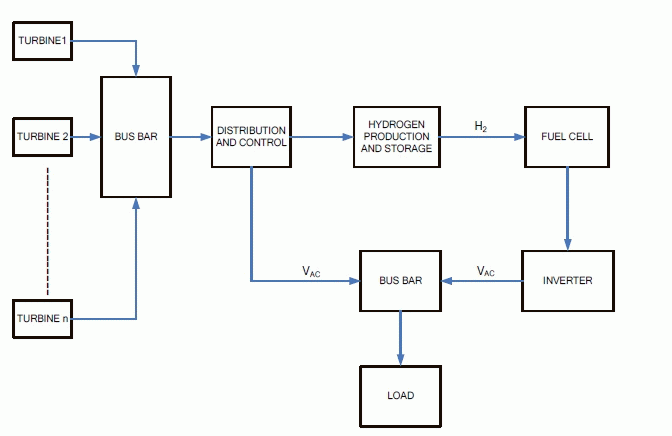 |
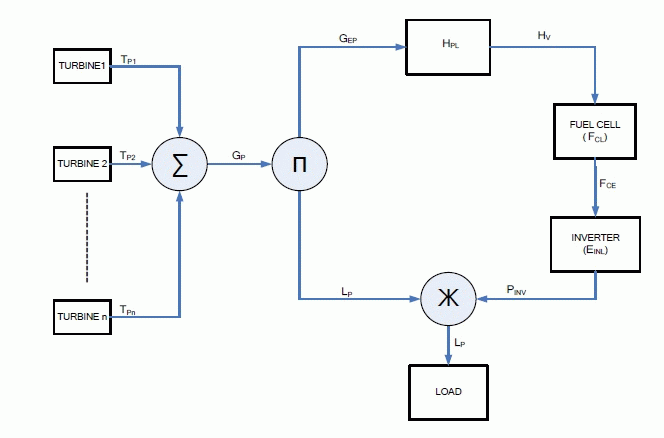 |
 |
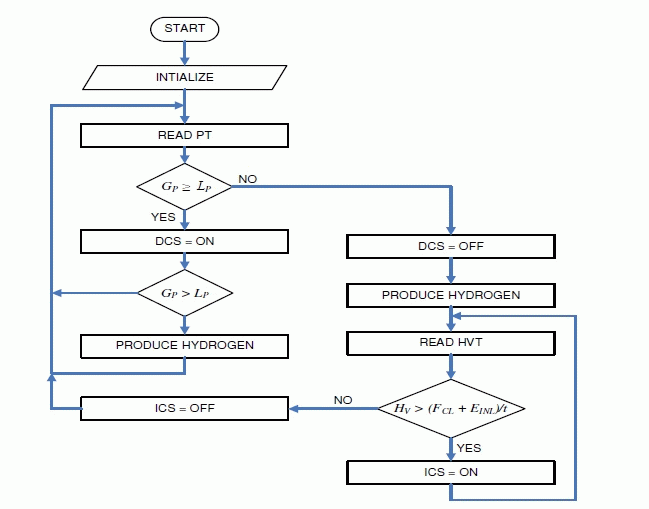 |
Figure 1 |
Figure 2 |
Figure 3 |
Figure 4 |
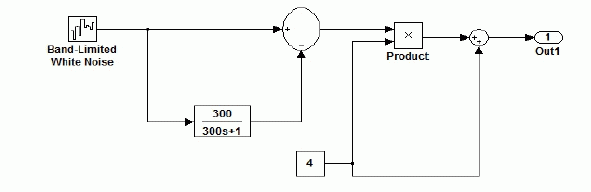 |
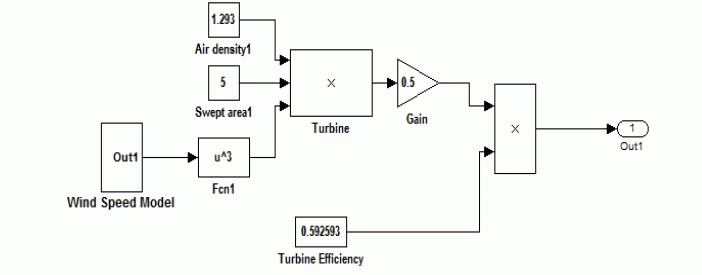 |
 |
 |
Figure 5 |
Figure 6 |
Figure 7 |
Figure 8 |
|
|
References
|
- Fritz A., “Wind Energy: An Emerging Energy Resource”, NDGS Newsletter Vol. 26, No. 1, 2009. https://www.dmr.nd.gov/ndgs/Newsletter/NL99S/PDF/windenergys99.pdf
- Thresher R., Robinson M. and Veers P., “Wind Energy Technology: Current Status and R&D Future”, National Renewable Energy Laboratory Conference Paper, NREL/CP-500-43374, 2008.
- Vladimiro M., “Wind Power, Distributed Generation: New challenges, New Solutions”, Turk J Elec Engin, Vol. 14, No. 3, pp 455-473. 2006.
- Wen-J Y. and Orhan A., “Wind energy-hydrogen storage hybrid power generation”, International Journal of Energy Research, 25: pp449-463, 2001.
- Xiangjun L., Dong H., Xiaokang L. and Tao Y., “Power Quality Control in Wind/Fuel Cell/Battery/Hydrogen Eleb ctrolyzer Hybrid Micro-grid Power System, Applications and Experiences of Quality Control”, Prof. Ognyan Ivanov (Ed.), ISBN: 978-953-307-236-4, InTech, http://www.intechopen.com/books/applications-and-experiences-of-quality-control/power-quality-control-inwind-fuel-cell-battery hydrogenelectrolyzer- hybrid-micro-grid-power-system, 2011.
- Pyle W., Healy J. and Cortez R., “Solar Hydrogen Production by Electrolysis”, Home Power No.39, 1994.
- Steve C. and Steve G., “Economic Analysis of an Integrated Wind-Hydrogen Energy System for a Small Alaska Community”, A Technical Report Task 4,5,6 under the project: A compilation and Review of proposed Alaska Development Projects. www.iser.uaa.alaska.edu, 2008.
- Ragheb M. and Ragheb A., “Fundamental and Advanced Topics in Wind Power”, pp19-35 http://www.intechopen.com 2013.
- Gary L. and Johnson, “Wind Energy Systems”, Kansas State University, 2006.
- Bjørnar K., Sondre G. and Cato B, “Hydrogen”, The Bellona Foundation, http://www.bellona.org/filearchive/fil_Hydrogen_6-2002.pdf 2002.
- U.S. Department of Energy, “Energy Efficiency & Renewable Energy: Fuel Cell Technologies Program”, http://www.eere.energy.gov/informationcenter. 2010.
- Marino S., Lucia S. and Laura M. “Analysis of the Energy Efficiency of Fuel Processor - PEM Fuel Cell Systems, Energy Efficiency”, Jenny Palm (Ed.), ISBN: 978-953-307-137-4, InTech, http://www.intechopen.com/books/energy-efficiency/analysis-of-the-energy-efficiency-offuelprocessor- pem-fuel-cell-systems, 2010.
|