Keywords
|
Energy audit, energy conservation opportunities, Energy saving. |
INTRODUCTION
|
To run equipment use in industrial, commercial, residential and utility application, ac supply is required as input. In the world energy crisis is one of the major problems. In developing countries like India, where electrical energy resources are scarce and production of electricity is very costly, energy conservation studies are of great importance. In order to reduce energy consumptions for sustainable and energy-efficient manufacturing, continuous energy audit and process tracking of industrial machines are essential. Energy Audit involves proper planning, directing and controlling of supply and input – output ratio of consumption of energy to maximize productivity and minimize energy costs [1]. As per the energy Conservation Act. 2001 “ Energy Audit” is define as the verification, monitoring and analysis of use of energy including submission of technical report containing, recommendation for improving energy efficiency with cost benefit analysis and an action plan to reduce energy consumption [2]. Systematic approach, to monitor industrial energy consumption and to pin point source of wastage, is known as energy audit. The process for energy audit is shown in Fig.1. |
The main objectives of energy audit are, to minimize energy cost/waste without affecting production and quality, minimize environmental effect/changes, optimize utilization and procurement of energy for all organization, reduce energy requirement per unit of output etc. |
LITERATURE SURVEY
|
A case study has been done in reference [1] which says that audit was conducted and suitable strategies of adjusting and optimizing energy were suggested so as to reduce energy requirements and hence, the total cost spent towards energy consumption. In reference [2] a case study of energy audit on an industrial unit was presented which discusses the common aspects of electrical energy management in small- and medium-sized industries. It contains the findings and the analysis of the results obtained from the electrical energy audit program employed in an industrial unit, Loknayak J.P.Narayan Shtekari Sahakari Sootgirni, Untawad Hol, Shahada.Dist.-Nandurbar. The electrical energy audit was carried out under three major heads: (i) lighting audit, (ii) power load audit (motors, meters, etc.), and (iii) harmonic analysis. In reference [3] standard design practice to assist engineers in evaluating electrical options from an energy standpoint has been presented. It establishes engineering techniques and procedures to allow efficiency optimization in the design and operation of an electrical system considering all aspects (safety, costs, environment, those occupying the facility, management needs, etc.). Reference [4] presents the results of a preliminary energy audit carried out on 8 large industrial buildings of a famous car manufacturing holding in Italy. Energy demand for heating varied from 6 to just over 74 kWh/m3year among the buildings of the site. In reference [5] a physically based model and formulation for industrial load management has been presented. |
NEED OF ENERGY AUDIT
|
Energy Audit will help to understand more about the ways energy and fuel are used in any industry, and help in identifying the areas where waste can occur and where scope for improving efficient utilization of resources. The Energy Audit would identify quantity and cost of various energy forms, and understand which type of fuel/energy is being used in particular process and product which are vital for production and utility activities. Energy audit gives preventive maintenance .Such an audit will help to keep focus on variations which occur in the energy costs, monitoring energy consumption at various levels, availability and reliability of supply of energy, highlighting wastage by relating energy input and production output, identify energy conservation technologies, retrofit for energy conservation equipment etc [3,4]. |
The primary objective of Energy Audit is to recommending appropriate policies for bringing down energy consumption per unit of product output or to lower operating costs. Energy Audit provides a "bench-mark" (Reference point) for managing energy in the organization and also provides the basis for planning a more effective use of energy throughout the organization [5]. |
ENERGY AUDIT TEAM
|
The energy audit team may comprise: |
• Works Manager (Team Leader) |
• Material Manager |
• Electrical or Electronics Engineer |
• Mechanical Engineer |
• Civil Engineer |
• Accountant |
• Technician bearing knowledge of electrical / electronic / mechanical Engineering and Computer awareness |
TYPES OF AUDIT PHASE
|
The type of Energy audit to be performed depends on various factors: |
• Type of industry |
• Type of Fuel/energy is being used. |
• Depth to which final audit is needed. |
• Function are performed in the industry |
• Investment and time availability |
• Potential and magnitude of cost reduction desired. |
Most of energy Audit falls into the three categories: |
1. Walk through: It involves going round the plant and identifying visible losses and negligence in operation and maintenance. Its require one or three days for energy audit. |
2. Mini audit: It involves collection of basic data, drawings, blue prints etc along with visual classifications. It requires one to three month for energy audit depending upon size of the plant. |
3. Maxi audit: It involves preparation of total energy balance sheet, drawing energy flow charts etc Energy audit can broadly be classified as |
1. Preliminary energy audit |
2. Detailed audit |
A. PRELIMINARY ENERGY AUDIT
|
i. Gather records for the last 12 month of the establishment’s energy bills and the corresponding financial statements. |
ii. Relate energy consumption to profitability of the establishment, such as energy cost to profit ratio, energy cost to revenue ratio, to establish the importance of energy in its operation. |
iii. Familiarize on how these energy bills are computed to determine the composition of the charges. |
iv. List all energy consuming equipment with detail of size, percent loading during the period, and hours of operation during the period. |
v. Identify major energy consuming equipments. |
vi. Inspect the major energy consuming equipment in the order of priority. |
vii. Identify energy conservation opportunities (ECOs) by determining what condition may be modified / corrected to reduce the energy input to the equipment? |
viii. What are the expected results in modifying / correcting these conditions? |
ix. What are the steps necessary to modify / correct these conditions? |
x. What is the cost involved? |
xi. Perform a cost benefit analysis on the ECOs |
xii. List priorities depending on the net return expected from the proposed investment. |
xiii. Write and describe these priorities in to an energy audit report. |
xiv. Prepare a presentation of the energy audit report for the management. |
xv. Present the energy audit report to the management for approval. |
xvi. Organize the implementation of the energy conservation programme. |
xvii. Implement no cost energy conservation measure. |
B. DETAILED ENERGY AUDIT
|
i. Prepare detailed audit and engineering study on approved energy conservation measures requiring additional investment. |
ii. Review cost benefit analysis based on the updated figures. |
iii. Revise energy conservation programme as required. |
iv. Work out the payback period. |
v. Secure management approval and funding |
vi. Organize the implementation of the revised energy conservation programme. |
vii. Implement the energy conservation programme |
viii. Monitor and analyze the progress of the energy conservation measures. |
ix. Report the progress of the energy conservation measure to management and determinate result to all concern. |
EXAMPLE OF ENERGY AUDIT
|
Energy saving for fume exhaust system blower in cold rolling mill: |
Motor rating : 3 –phase AC induction motor of 50 HP, 415 V, 1460 RPM |
Previous System: |
• Star delta starter for motor operation |
• Belt pulley system for power transmission to fan |
Observation: |
• Blower fan kept working continuously at a constant speed. |
• Blower fan working at full speed irrespective of fumes generated or not at rolling mill. |
Process Study and Experimentation: |
• Fume generation was very low during first pass rolling. |
• No fumes generation during coil handling. |
• Actual rolling duration at full and hence maximum fume generation takes place only 60% of the total duration of mill operation. |
• Manual control of inlet valve of blower fan was impractical. |
Present System: |
• AC electronics speed variable drive installed. |
• Drive operation studied and software designed accordingly, optimize the power consumption during idling of mill. |
• Further optimization done to reduce the power consumption in accordance with fumes generation. |
Merit of new system: |
• Smooth start resulting in increases life of motor and mechanical system. |
• Energy saving due to speed / voltage variation during idling mill. |
Cost benefits Analysis: |
Previous System (Without drive): Speed= 50 Hz, kW (Consumption) = 30 |
Present System (With drive): Speed = 0-20-45 Hz, kW (consumption) =15 |
Energy saving per year investment: 15 kW*20*300 = 90,000 kWh |
Investment: Rs. 1,50,000 |
Saving in rupee terms / year : 90,000*4=Rs.3,60,000 |
CONCLUSION
|
Energy audit may be considered as similar to the monthly closing statement of an accounting system. One series of entries consist of amounts of energy which were consumed during the month in the form of electricity, gas, fuel oil, coal etc. and the second series lists how the energy was used how much energy was used in lighting, in air conditioning, in heating, in process etc. Energy audit process must be carried out accurately enough to identify and quantify energy cost saving that are likely to be realized through investment in energy saving measure. |
Figures at a glance
|
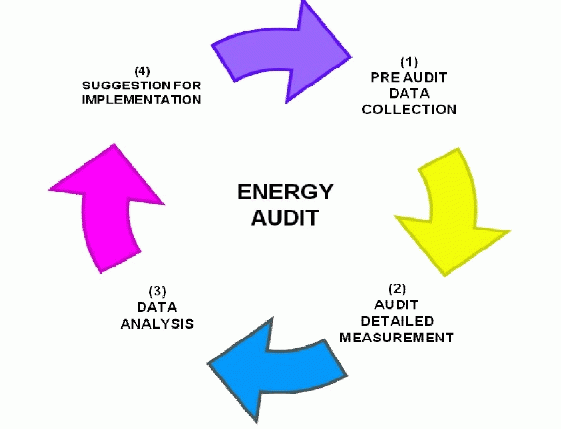 |
Figure 1 |
|
|
References
|
- K. R. Chowdhury, M. Di Felice, “Search: a routing protocol for mobile cognitive radio ad hoc networks,” Computer Communication Journal,vol. 32, no. 18, pp. 1983-1997, Dec.20
- S. U. Kulkarni, KalpanaPatil “Energy Audit of an Industrial Unit- A Case Study” International Journal of Emerging Science and Engineering,Vol.2, pp.22-26, November 2013
- "IEEE Recommended Practice for Energy Management in Industrial and Commercial Facilities", Recognized as an American National Standard (ANSI) IEEE Standard, pp. 739, 1995.
- Matteo Dongellini, CosimoMarinosci, Gian Luca Morini “Energy audit of an industrial site: a case study”, 68th Conference of the Italian Thermal Machines Engineering Association, ATI2013, Vol.45, pp. 424-433, 2014.
- Malkiat Singh, Gurpreet Singh, Harmandeep Singh, “Energy Audit: A Case Study to Reduce Lighting Cost” , Asian Journal of Computer Science and Information Technology, Vol.2, No.5, pp.119-122, 2012.
|