Keywords
|
PLC; Traffic Light; Automation; Sensors |
INTRODUCTION
|
In the conventional traffic control system it may be observed that the time of Green light glowing for a particular road will be always constant. Sometimes it may happen that, one particular road may be crowded more than any other. In such cases the conventional traffic control system will fail to give priority to the heavy traffic roads. Hence in this paper an adaptive intelligent traffic control system using PLC is proposed. |
The modern traffic light was invented in America. New York had a three color system in 1918 that was operated manually from a tower in the middle of the street. Other cities soon adopted the idea of having someone on the scene to control the lights. Garrett Morgan, inventor of the gas mask, also developed traffic signaling devices. Having witnessed an accident between a car and a carriage, Morgan felt compelled to devise a system to prevent such collisions at street intersections. In 1923 he patented an electric traffic light system using a pole with a cross section on which the words STOP and GO were illuminated. These basic designs were soon improved. In 1926 the first automatic signals were installed in London; they depended on a timer to activate them. Today, traffic is automatically routed onto limited access highways courtesy of a computer activated guidance system that determines traffic volume on the highway. |
RELATED WORK
|
The PLC based traffic controller [1] is proposed which sense the presence and absence of the vehicle within range. The system using PLC is proposed to read the meter of electricity using power line communication [2]. The proposed system is implemented to send non voice data only. It has advantages in safety; real time measuring and time saving as well as it has a better user interface and digital data analysis. Data is send over existing carrier that reduces the complexity and cost of system. FPGA based advanced traffic light controller simulation is discussed in [3]. An FPGA design of a 24-hour traffic light controller system of a four roads structure with six traffic lights has been simulated using infrared sensor. The system has been designed using VHDL, simulated on Xilinx 9.1. |
The control of traffic light was designed around conventional contact elements and devices such as timers, relays, and contactors etc. The critical timing operation is required to be carried out under the existence of heavy traffic conditions. The requirement of fast automation of mentioned process and effective optimization of traffic light control system is described [4]. The paper introduces an execution and implementation of required program to achieve the solution of mentioned problem by using developed software Simatic Manager-Step 7. |
OVERVIEW OF PLC
|
The PLC is an industrial computer. It is capable of storing instructions to implement control functions such as sequencing, timing, counting, arithmetic, data manipulation and communication. The I/O interfaces provide the connection between the PLC and the information providers (inputs like pushbuttons, sensors) and the controllable devices (outputs like valves, relays, lamps). PLCs are specifically designed to survive the harsh conditions of the industrial environment. A well designed PLC can be placed in an area with substantial amounts of electrical noise, electromagnetic interference, mechanical vibration, and non condensing humidity [5]. The hardware interfaces for connecting field devices are actually part of the PLC itself and are easily connected. |
There are different types of PLC like Indra Logic L10, L20, and L25 etc. Indra Logic L20 PLC has been used. The Indra logic 20 has been shown in Fig 1. |
The proposed ITCS system consist of PLC (LM-20) with RS232 serial communication, compact flash card, on board I/O (DI8 /DO8) and power supply, Sensors (IR). RS 232 is a standard for serial communication transmission of the data. It is used to connect external devices like motor controllers etc to the PLC. Compact Flash Card has 3 partitions. First part is for firmware or OS, second part is for program and data memory and third part can be used as a pen drive. It is the memory of PLC. The power supply of 24 V DC for CPU, Onboard I/Os, inline module. |
BLOCK DIAGRAM
|
The overall setup consists of PLC LM20, Sensors, and Green, Red, Yellow lights. PLC is connected to the PC through RS232 (serial communication), Sensors are connected to PLC, Power supply is 24V DC. |
PROPOSED METHODOLOGY
|
Four sensors have been placed on the roads 2A, 2B, 2C and 2D as show in Fig 3. The sensor is placed at a distance away from the junction so that it doesn’t get disturbed by the vehicles stopping at the signal. These sensors are connected to the PLC, which counts the pulses coming from the sensors. There are four counters per sensor so that the counters can compare the count with four different preset values [6]. Each counter gives a high when the count reaches the value assigned to them. So, when the time for giving green signal for a lane comes, each counter is checked for a high value and corresponding timer will be activated. In prototype design capacitive sensors are used. These sensors work well for insulators (plastic) as well as for metals. |
SIMULATION RESULTS
|
The programming language used is "Ladder Logic". It consists of timers, counters, inputs (switches) and outputs (coils). Fig 4 and Fig 5 shows the snapshot of the ladder diagram of the logic. The program is downloaded in the PLC and tested. |
When the vehicle count reaches the preset value (say 5) for a particular lane (Lane 1) the Green signal will be ON for 10 time units and simultaneously Red signal of the other three lanes (Lane 2,3,4) will be ON, as shown in Fig 4. Then Yellow signal will be ON for 3 time units, and then Red signal will be ON and counter gets reset. |
When the vehicle count of any particular lane reaches the preset value Green signal of that particular lane gets ON, at the same time Red signal of the remaining lanes will be ON. |
CONCLUSION AND FUTURE WORK
|
The method will help to reduce congestion on roads and would help in coping with accidents as the heavy vehicles and light vehicles will be in different lanes. Resultantly, then a solution to a much critical problem of traffic congestion and fatal accidents is possible using this system. Thus the proposed system would make our roads a safer place to travel. |
In future work, we will use real dynamic road section to estimate the unknown traffic volumes and apply to real traffic. When emergency arises then the system fails. In ITSC system, this problem is solved by giving red signal to all traffic and only emergency cars will pass the signal for particular time period. |
Figures at a glance
|
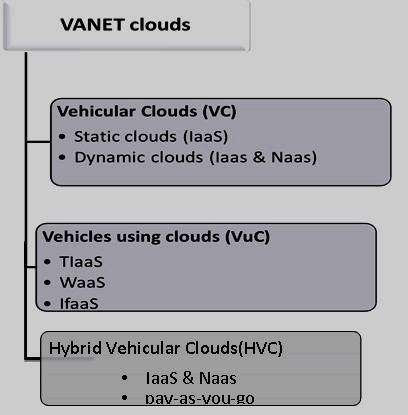 |
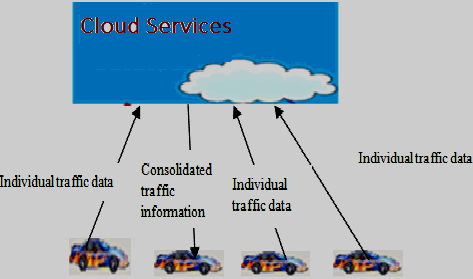 |
 |
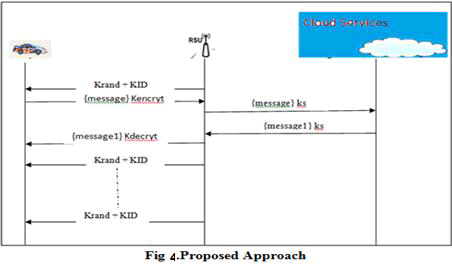 |
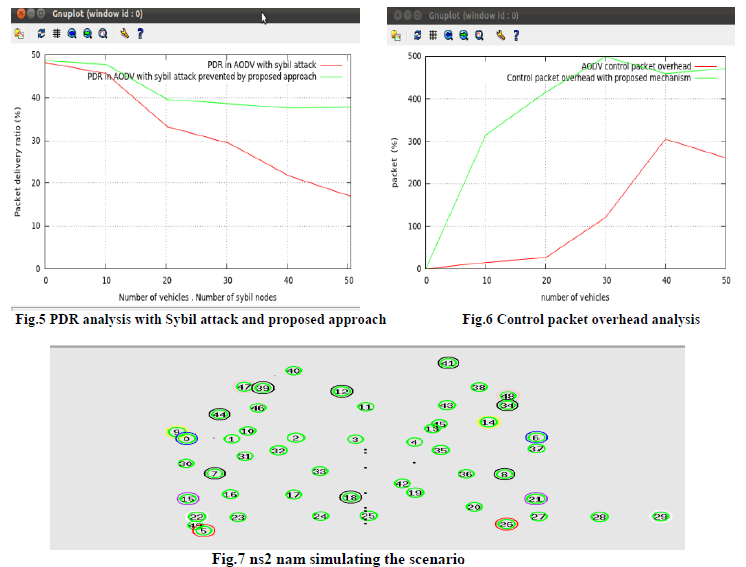 |
Figure 1 |
Figure 2 |
Figure 3 |
Figure 4 |
Figure 5 |
|
|
References
|
- Muhammad ArshadKhattak “PLC Based Intelligent Traffic Control System”, International Journal of Electrical & Computer Sciences IJECSIJENS Vol: 11 No: 06 © December 2011
- PoonamBorle, AnkitaSaswadkar, DeepaliHiwarkar, Rupali S. Kad, “Automatic Meter Reading for Electricity Using Power Line Communication”, International Journal of Advanced Research in Electrical, Electronics and Instrumentation Engineering Vol. 2, Issue 3, March 2013.
- Parasmani, ShriGopalModani, “FPGA-Based Advanced Traffic Light Controller Simulation”, International Journal of Scientific & Engineering Research, Volume 4, Issue 9, September-2013. Pages 2314-2317.
- Carlo Y. Makdisie, “Automation Development of Traffic Light Control via PLC based Simatic Manager”, International Journal of Electronics Engineering, 4 (1), 2012, pp. 85– 88.
- L. A. Bryan, E A .Bryan, “Programmable Controllers, theory and implementation”, second edition, An Industrial Text Company Publication Atlanta • Georgia • USA
- Schmitt, Neil M.; Farwell, Robert F., Understanding Automation Systems (Understanding Library), Published by Sams, Indianapolis, IN, U.S.A. (1986) ISBN 10: 0672270145 ISBN 13: 9780672270147
|