INDEXTERMS
|
Doubly Fed Induction Generator (DFIG), Fault Ride Through, Wind Turbine, Power system fault. |
INTRODUCTION
|
In recent years, wind energy has become one of the most important and promising sources of renewable energy. With increasing demand of electrical energy and the consequent depletion of fossil fuels worldwide interest for wind energy has increased. The development of wind energy for electrical power generation increased in the early decades of twentieth century. Currently, there are five countries – Germany, USA, Denmark, India and Spain which concentrate more than 83% of worldwide wind energy production. However, the utilisation of this renewable source of power is fast spreading in other areas of the world also. |
The development of wind power in India began in the 90s, and it has significantly increased in the last few years. Although a newcomer to the wind industry compared with Denmark or the United States, India has the fifth largest installed wind power capacity in the world with 19051.46 MW. In 2009-10 India's growth rate was highest among the other top four countries. With peak wind power generation at close to 7162.18 MW, Tamil Nadu is one of the wind power hubs in South Asia. Tamil Nadu generates 40% of the India's total wind power. |
With increased penetration of wind power into electrical grids, DFIG wind turbines are largely deployed due to their variable speed feature and hence influencing system dynamics. Doubly fed induction generator (DFIG) is a popular wind turbine (WT) system due to its high energy efficiency, reduced mechanical stress on the WT, and relatively low power rating of the connected power electronics converter of low costs. This has created an interest in developing suitable models for DFIG to be integrated into power system studies. The continuous trend of having high penetration of wind power, in recent years, has made it necessary to introduce new practices. For example, grid codes are being revised to ensure that wind turbines would contribute to the control of voltage and frequency and also to stay connected to the host network following a disturbance. |
Low voltage ride through (LVRT), or fault ride through (FRT), is the capability of wind generators to operate during lower grid voltage. As the power electronics converters in the DFIG system have relative lower power rating compared with the WT with fully rated converters, the LVRT capability of the DFIG WT is of special interest with respect to the stability issue of such system. |
Among the available control strategies, the crowbarprotection is the mostly used. During the faults, the rotor side converter will be blocked, and the crowbar circuit,installed across the rotor terminals, will be triggered to damp the over-current in the rotor circuit. Consequently, the generator operates as a conventional induction machine, which absorbs reactive powerfrom the faulted grid [1]. The chopper circuit, with a resistoracross the DC bus, is usually used along with the crowbar tosmooth the DC-link voltage by dissipating the excessive powerover the DC bus [2], [3]. |
This paper presents an innovative control strategy for boththe rotor and grid side converters to enhance the LVRT capacity of the DFIG WT, without the need of additional current and voltage protections. The key idea is to increase the generatorrotor speed through proper control of the rotor side converter during a grid voltage dip. Different from conventional methods, the proposed control strategy is based on a simple concept to transform the unbalanced energy into the kinetic one, rather than being dissipated otherwise. For the grid side control scheme, a compensation item, which reflects the variation of the DC-link current of the rotor side converter, is added during the fault to smooth the fluctuations of the DC-link voltage. Compared withthe LVRT solution in [4], the proposed control strategy for the grid side controller can effectively reduce the extremely high transient when the stator voltage dips to zero during faults. Simulation studies using Matlab/Simulink have been conducted on a 1.5-MW DFIG WT to validate the effectiveness of the proposed control strategy. |
MODELLING OF DFIG WIND TURBINE
|
A. Turbine Model |
1) Aerodynamic model |
The power contained in the wind is given by the kineticenergy of the flowing mass per unit time, |
P0 = ρAVα/2 (1) |
Where air density ( ρ=1.225 kg/m3), Vα is the wind speed, A is the area swept by the turbine. |
The theoretical maximum power extractable from wind is 16/27 times the power contained in the wind. This limit is provided by Albert Betz in 1919 and is known as Betz limit [5]. |
(1) |
The power coefficient of a wind turbine is the ratio of the mechanical power and the power contained in the wind, |
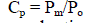 |
The power coefficient which is a function of both tip speed ratio , and blade pitch angle, [deg] is given by an empirical formula, |
(4)
|
Where, |
(5) |
(6) |
λis the tip speed ratio, a dimensionless quantity which can have an maximum value as 9 for aerodynamic type wind turbines. The power coefficient Vs the Tip speed ratio of a wind turbine is an important yardstick in the characterization of wind energy converters. The torque and power are related by |
(7) |
(8) |
Therefore the mathematical relation of the mechanical power extraction from the wind can be expressed as, |
(9) |
B. Machine Model |
The voltage equations of the stator and rotor circuits of the induction generator can be given in a d-q reference frame rotatingat the synchronous speed [6], [7] |
Stator voltage equations (10) |
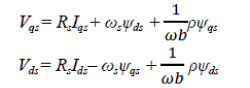 |
Rotor voltage equations (11) |
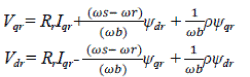 |
Stator flux linkage equations (12) |
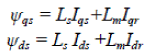 |
Rotor flux linkage equations (13) |
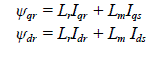 |
whereIs = Ids + j Iqsand Ir = Idr + j Iqrare the stator and rotor current vectors respectively; Vs = Vds + j Vqsand Vr = Vdr + j Vqrare the stator and rotor voltage vectors. Similarly the flux linkages.The electrical torque is given by |
(14) |
Power Equations corresponding to the transformations is given by |
(15) |
(16) |
C. Drive Train |
In power system studies, drive trains are modeled as a seriesof rigid disks connected via massless shafts. For small-signal analysis of synchronous generators (SG) in conventional power plants, the one-mass or lumped-mass model is used because the drive train behaves as a single equivalent mass (the mode of interest is non-torsional, with nearly equal participation of all inertias) . This results from the fact that the mechanical stiffness (between the generator, turbine and between adjacent turbine segments) is much higher than the equivalent electrical stiffness (between the generator and the infinite bus) . In this case, the mode of interest is often referred interchangeably as “system mode,” “non-torsional-mode,” or “electromechanical mode”. |
When it comes to DFIG in wind power plants, the mechanical parameters are such that those terms cannot be used interchangeably. The presence of a gearbox makes the shaft more slender, resulting in a mechanical stiffness of the same order as the equivalent electrical stiffness. The lower shaft stiffness combined with the fact that the generator is relatively much lighter than the turbine results in a dynamic behavior where there is no “system mode.” In other words, there is no mode for which the drive train behaves as a single equivalent mass. As a result, a multi mass drive train mustbe considered for stability studies of WECS with DFIG [8]. In general, it is sufficient to consider the two-mass model (one for the turbine, the other for the generator) because the modes associated with the blades and the hub is either well damped or out of the frequency range of interest. The dynamic equations are obtained from Newton’s equations of motion for each mass (rotational speed) and shaft (torsion or twist angle), |
(17) |
(18) |
(19) |
The shaft torque is given by, |
(20) |
PROPOSED CONTROL STRATEGY
|
The proposed control strategy cantransform the additional output power into the WT kinetic energyby temporarily increasing the generator rotor speed duringthe grid faults, thus effectively limiting the oscillations in thecurrents. If the rotor speed increases above the rated value, thepitch control will be triggered to decrease the power extractionfrom the wind. This can restrict the over-speed of the rotor andtherefore limit the excessive mechanical stress applied to theturbine system. Moreover, a compensation item, which reflectsthe variation of the DC-link current of the rotor side converter,is added to the grid side control scheme during the fault so as tosmooth the fluctuation of the DC-link voltage. |
The proposed control strategy makes full use of existingresources within the DFIG WT system to realize the LVRTwithout the need of additional components like the crowbar. It can effectively protect the power electronics devices againstcurrent and voltage fluctuations during grid faults to ensure the LVRT of the DFIG. Several advantages can be achieved byusing the new control strategy. From the energy perspective,the new control strategy can absorb the additional output power during the faults that will be otherwise dissipated in the crowbarbased control. Notably, the increased kinetic energy of the WTcan be released into the grid slowly after the fault clearance.From the control perspective, the new control strategy can erasurethe back-to-back converters well connected to the DFIGas well as the grid without loss of the controllability duringthe faults. This potentially can enable both active and reactivesupports to the faulted grids from WT which is difficult forthe crowbar based control. The detailed control scheme willbe illustrated in Sections III-A and III-B, and the simulationvalidation will be given in Section IV. |
A. Control of RSC Model |
In order to decouple the electromagnetic torque and the rotor excitation current, the induction generator is controlled in the stator-flux oriented reference frame, which is a synchronously rotating reference frame, with its d-axis oriented along the stator-flux vector position[9]. This will result in |
(21) |
(22) |
therefore, |
(23) |
(24) |
(25) |
(26) |
(27) |
substituting we get, |
(28) |
(29) |
(30) |
Therefore the above equations show that active and reactive powers of the stator can be controlled independently.Using stator flux orientated approach, implementation with current controlled PWM inverter requires decoupling scheme. It means that any changes on the voltage component in d or q axes results in changes in both current components. In order to combat this problem, equations will be re-developed in order to compensate for these cross coupling between d and q axes. Let us first define the following parameter called the leakage factor of the induction machine as: |
(31) |
compensating terms, |
(32) |
(33) |
Adding these compensating terms to the corresponding uncompensated voltage terms makes it possible to achieve decoupled performance of the stator flux oriented control of the RSC. |
In normal operation, the control scheme of the RSC is illustrated in Fig. 2. The typical proportional integral (PI) controllers are used for regulation in the rotor speedand reactive power (outer) control loops as well as the rotor current (inner) control loops. When a short-term low-voltage fault occurs, the incoming power from the wind and the power flowing into the grid are imbalanced instantaneously, resulting in the transient excessivecurrents in the rotor and stator circuits. Therefore from the energy balance point of view, the key point of suppressing theover-currents in the rotor and stator circuits is to reduce the imbalanced energy flowing through the DFIG WT system. When at least one of the monitored parameters, including therotor current, stator current, DC-link voltage, and grid voltage,exceeds its respective protection setting due to the grid fault,the proposed LVRT control strategy will be triggered.With this control strategy, the rotor side controller will increase the generator rotor speed by reducing the generator torque to zero duringthe fault, in order to absorb and convert the incoming energyfrom the wind into the kinetic energy in the WT inertia. The increased kinetic energy can be transformed and released into thegrid after the fault clearance. The control scheme of the RSC against grid faults is illustrated in Fig. 3. |
The new control strategy will not cause excessive mechanical stress to the WT system. When the DFIG WT is operatingat or close to the rated speed, the acceleration due to the proposed control scheme during the fault may accelerate the windturbine speed above its rated value. This can increase the thrust and centrifugal forces, applied to the rotor construction that may endanger the wind turbine mechanical system [10]. However, the over-speed of the WT can be effectively restrained by the pitchcontrol, which will be activated immediately when the rotorspeed becomes higher than the rated value. Moreover, the duration of the over-speed is short, due to the short duration andrare occurrence of grid faults. According to the expressions ofthe thrust and centrifugal forces in [10], the negative impacts due to the proposed control strategy can be little to the safe operation of WTs. |
B. Control of GSC Model |
In order to obtain the independent control of active and reactive power flowing between the grid and the GSC, the converter control operates in the grid-voltage oriented reference frame, which is a synchronously rotating reference frame, with its daxis oriented along the grid-voltage vector position. Aligning the d-axis of the reference frame along the stator-voltage positionvq is zero, and, since the amplitude of the supply voltage is constant vdis constant. The active and reactive power will be proportional to idsand iqsrespectively. |
(34) |
(35) |
In normal operation, when the power flowing through the grid and rotor side converters is balanced,ios is equal toior , so the DC-link voltage is constant. The equation which describes the dynamic behavior of the DC-link capacitor can be expressed as |
(36) |
When the grid voltage dips, may not be equal to due to the instantaneous unbalanced power flow between the grid and rotor side converters, and therefore the DC-link voltage may fluctuate. In [11] in order to reduce thefluctuation of the DC-link voltage, the item (Pr/ Vds) reflecting the instantaneous variation of the output power of the rotor sidecontroller is directly set as the reference of theidl during the grid fault. However, the stator voltage may reduce to zero during the grid fault. This will introduce an extremely high transient value of idl. |
In this paper, when the rotor current, stator current, DC-link voltage, or grid voltage exceeds its respective relay setting due to the grid voltage dip, the term (Pr/ Vdc) describingioris represented as a disturbance to compensate the instantaneous rotor power in the control scheme. In such a way, theidl can be regulated smoothly during a grid fault. The detailed control scheme of the GSC during the grid fault is shown in Fig. 5. |
RESULTS AND DISCUSSION
|
Simulation is carried out for a three phase fault for a period of 100 ms.The wind machines Fault Ride through capability is assessed with the proposed control strategy. The behavior of the DFIG-WT during the fault has been discussed below. |
The simulation results of the DFIG WT with the crowbar protection and of the proposed control strategy are shown in Fig. |
7 and Fig. 8. The crowbar resistor value is chosen as . 40Rr The detailed scheme of the crowbar protection is described in [10].Fig. 8 presents the LVRT behavior of the proposed control scheme. During the fault the rotor speed increases above its rated value, which will trigger the pitch control immediately. This can limit the transformation of the electric energy into the kinetic one. |
The rotor speed slightly exceeds the rated value. However, the maximum over-speed is only 6% and the period of the whole violation is 100 ms when the voltage at the PCC drops to 0 for 100 ms, and the over-speed duration is short, indicating a very little impact on the wind turbine construction. The variation of the rotor speed during the fault under the proposed control scheme is shown in Fig. 6. |
However, the transient behaviors of the active and reactive power, stator and rotor current in the case of the proposed control strategy are still observed better than with the conventional crowbar protection. Especially, the proposed control strategy can suppress the transient stator and rotor currents lower than the crowbar threshold; thus, the DFIG can maintain uninterrupted control of active and reactive power, potentially enabling the grid supporting services during the fault. |
CONCLUSIONS
|
This paper proposes a new and efficient control strategy for both the rotor and grid side converters to improve the LVRT capability of the DFIG WT. The new control strategy enables the DFIG to continue the electricity production, and absorb theexcessive energy by increasing the generator rotor speed temporarily when a fault occurs at, e.g., the PCC. The new strategy also introduces a compensation item to the grid side controller in order to suppress the DC-link over-voltage during the faults. The simulation results show that the proposed control strategy is able to effectively suppress the transients in the rotor circuit current. Compared with the conventional crowbar protection, the DFIG WT installed with the proposed control strategy gives a better transient behavior in event of short-term grid voltage dip. |
APPENDIX
|
The parameters of the DFIG WT system is as follows: |
Wind turbine rated wind speed: 12 m/s |
DFIG: |
rated power : 1.5MW; |
rated voltage : 575 V; |
rated current : 1505A; |
rated rotor speed : 1.1 p.u. |
|
Figures at a glance
|
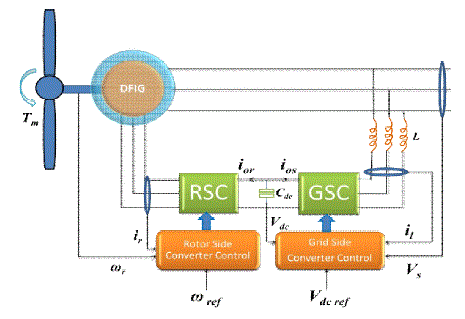 |
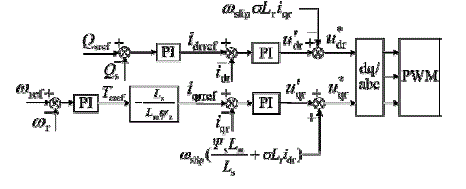 |
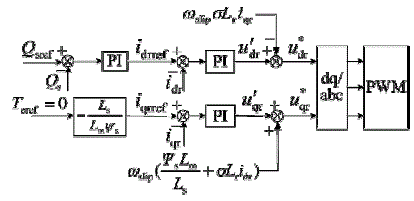 |
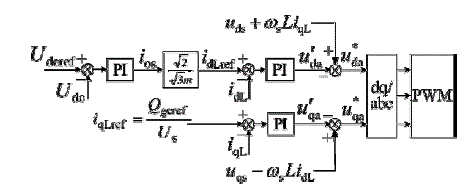 |
Figure 1 |
Figure 2 |
Figure 3 |
Figure 4 |
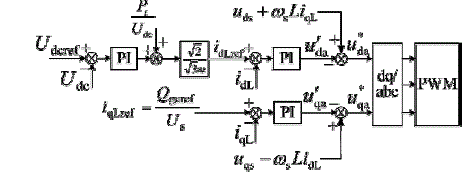 |
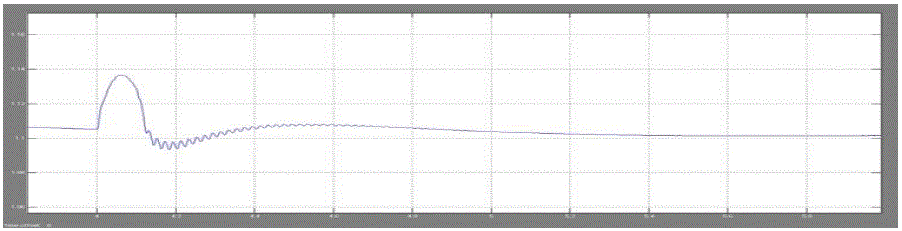 |
 |
 |
Figure 5 |
Figure 6 |
Figure 7 |
Figure 8 |
|
|
References
|
- A. Hansen and G. Michalke, “Fault ride-through capability of DFIG wind turbines,” Renew. Energy, vol. 32, no. 9, pp. 1594–1610, Jul. 2007.
- Erlich, J. Kretschmann, J. Fortmann, S. Mueller-Engelhardt, and H. Wrede, “Modeling of wind turbines based on doubly-fed induction generatorsfor power system stability studies,” IEEE Trans. PowerSy st., vol. 22, no. 3, pp. 909–919, Aug. 2007.
- J. Yang, J. E. Fletcher, and J. O’Reilly, “A series dynamicresistor based converter protection scheme for doubly-fedinduction generator duringvarious fault conditions,” IEEE Trans. Energy Convers., vol. 25, no. 2, pp. 422–432, Jun. 2010.
- J. Yao, H. Li, Y. Liao, and Z. Chen, “An improved control strategy of limiting the DC-link voltage fluctuation for a doubly fed induction windgenerator,” IEEE Trans. Power Electron., vol. 23, no. 3, pp. 1205–1213, May 2008.
- 5 S. N. Bhadra, D. Kastha and S. Banerjee, “Wind Electrical Systems”, Oxford university press, 2005.
- F. Mei and B. C. Pal, “Modal analysis of grid-connected doubly fed induction generators,” IEEE Trans. Energy Convers., vol. 22, no. 3, pp. 728–736, Sep. 2007.
- F. Wu, X. P. Zhang, K. Godfrey, and P. Ju, “Small signal stability anal-ysis and optimal control of a wind turbine with doubly fed inductiongenerator,” IET Gen., Transm., Distrib., vol. 1, no. 5, pp. 751–760, Sep. 2007.
- F. Mei and B. C. Pal, “Modal analysis of grid-connected doubly fed induction generators,” IEEE Trans. Energy Convers., vol. 22, no. 3, pp. 728–736, Sep. 2007.
- R. Pena, J. C. Clare, and G. M. Asher, “Doubly fed induction generator using back-to-backPWMconverters and its application to variable speedwind-energy generation,” Proc. Inst. Elect. Eng., Elect. Power Appl., vol. 143, no. 3, pp. 231–241, May 1996.
- V. Akhmatov, Induction Generators for Wind Power. Brentwood, CA: Multi-Science, 2005.
- J. Yao, H. Li, Y. Liao, and Z. Chen, “An improved control strategy of limiting the DC-link voltage fluctuation for a doubly fed induction windgenerator,” IEEE Trans. Power Electron., vol. 23, no. 3, pp. 1205–1213, May 2008.
- L. Yang1, G.Y. Yang, Z. Xu, Z.Y. Dong, K.P. Wong, X. Ma1, “Optimal controller design of a doubly-fed induction generator wind turbine systemfor small signal stability enhancement,” IET Gener. Transm. Distrib., 2010, Vol. 4, Iss. 5, pp. 579–597.
|