Keywords
|
Fuzzy Logic Controller, Conical Tank, Nonlinear Process, PI controller, MATLAB . |
INTRODUCTION
|
In most of the chemical plants, level control is extremely important because desired production rates and inventories are achieved through proper control of flow and level. At this point it is clear that level control is an important issue. PID controller and other linear controllers were the most popular control schemes that have been widely implemented to control the liquid level in the process tank. These technique is highly appreciated by many researchers [7,8] because of the adjustments will be made in controller parameters with minimum attempt. The PID control was first placed in the market in 1939 and has remained the most widely used controller in process control until today. Proportional-Integral (PI) controllers have remained as the most commonly used controllers in the industry since its inauguration many decades ago. The main reason behind its popularity among engineers is its simplicity in tuning the parameters to achieve satisfactory performance in industrial applications. Many tuning approaches have evolved in tuning the controller since 1942 when Ziegler and Nichols [1] pioneered a unified systematic tuning approach in tuning the PI controller. For this control loop to function properly, the PID loop must be properly tuned. Standard methods for tuning include Ziegler- Nichols Ultimate-cycle tuning [1], Cohen-Coon?s [3], Astrom and Hagglund[2] and many other traditional techniques. |
A level Control of conical tank is a challenging problem because of its non-linearity and changing in area of cross section . Hence fuzzy logic controller is highly preferred. Benefits of Fuzzy logic controller include simplicity and flexibility. Fuzzy logic can handle problems with imprecise and incomplete data. A linguistic variable is a variable whose values are linguistic terms. The concept of linguistic variable is very useful in dealing with situations which are too complex or too ill-defined to be reasonably described in conventional quantitative expressions. These linguistic variables can also be represented by fuzzy numbers. Accuracy is higher and high effort is not needed. Fast response, small overshoot and good robustness can be obtained through fuzzy. Fuzzy controllers have a relatively small computation cost. They are also very simple to implement in that the user can easily observe and check each step in the workings of the software implementation. Since the introduction of the theory of fuzzy sets by Zadeh in 1965 [5] and the industrial application of the first fuzzy controller by E. H. Mamdani in 1974 [4], fuzzy systems have obtained a major role in engineering systems and consumer products in the 1980s and 1990s. Georgescu et al. [6] have demonstrated the application of fuzzy predictive PID controllers to a heating control system. |
Here, a inverted non linear structured conical process tank is taken. Generally conical tanks are highly preferred for industrial storage process because of gravity discharge in its shape and it is difficult to maintain the level of the liquid at desired point. It has non linear structure which leads the liquid in the tank rises with respect to the inclination angle through which the tank is designed. So effective control essential for the process to maintain the liquid level at particular point. A pressure acting in the conical tank is different at each point, and in this article, a fuzzy logic controller is implemented and results were compared with Direct synthesis control technique. The process setup is considered as single input and single output i.e a tank has inlet upstream valve and outlet downstream valve. |
A. Mathematical Modeling |
The conical tank system shown in Fig 1 is essentially a system with nonlinear dynamics[10,12]. Its nonlinear dynamics described by the first – order differential equation. It is derived according to Law of conservation of mass, |
Inflow rate - Outflow rate = Accumulation |
 |
 |
 |
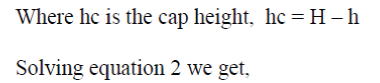 |
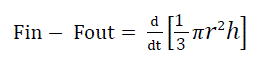 |
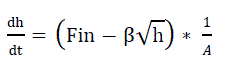 |
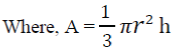 |
The equation (4) describing the mathematical model for single conical tank level control, this equation is implemented in MATLAB SIMULINK and a response is obtained by disturbing a process, step change in inlet flow rate represents a process as first order transfer function with zero dead time. Where process gain (Kp), dead time , time constant. |
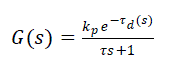 |
A. Direct synthesis method |
Direct Synthesis(DS) is a model based tuning technique. It uses an identified process model in conjunction with a user specified closed loop response characteristics[10]. This is a model based tuning technique. It uses an identified process model in conjunction with a user specified closed loop response characteristic. An advantage of this approach is that it provides insight into the role of the „model? in control system design. The overall transfer function for set point change assuming, |
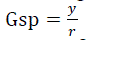 |
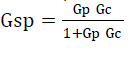 |
On rearranging the equation (7), we get, |
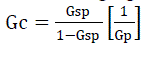 |
B. Fuzzy logic controller |
The block diagram of a fuzzy controller is shown in Fig.3. The design of the fuzzy control system consists of several steps. First, the variables for the fuzzy control system are determined[9]. The universes of discourse for all the variables involved are then set. Here, the fuzzy controller is designed with two input variables, rate of change of error and error in level, and one output variable, valve opening. The universe of discourse for these parameters are -50 to +50 cm, -25 to +25 cm., and 0 to 100% for error, change in error and valve opening respectively. |
The fuzzy sets are designed such that the starting point of a particular fuzzy set is set to the summit of the previous set and the ending point is set to the summit of the next fuzzy set. This is done for the sake of simplicity. The rule base is usually developed based on expert knowledge. The rule base is developed by an understanding of the system and some trial and error manipulations. |
The centre of gravity method is used for defuzzification. In order to get good control in the nonlinear regions, divided the whole set up into different zones and implement Fuzzy controller. Four models were obtained 0-1.44cm as model- 1, 1.44-5.76cm as model-2, 5.76-12.83cm as model-3 and 12.83-23.04 cm as model-4 with process gain 0.0218, 0.0654, 0.109, 0.155 and time constant 0.041, 0.24, 1.97, 11.75 respectively. The above four models were represented as first order transfer function with zero delay time. |
After the tuning process is done through direct synthesis method and fuzzy logic controller, analysis was done for their responses to a unit step input, with the help of MATLAB simulink environment application for the conical tank. The performance comparison for the obtained time domain analysis with the designed controllers is presented in Tables 2 for setpoints 10 cm and 22 cm. The fig 4 shows the simulation results for set point 10 cm and 22 cm. The fuzzy logic controller yields a better response the direct synthesis method. Fuzzy logic controller provides faster rise time and settling time than Direct synthesis control technique. |
CONCLUSION
|
In this work, a rule based fuzzy control scheme was developed for level control of conical tank. An implementation was carried out in simulation environment and the developed controller tuning for various set points can be suitably tracked by providing a program which can allow the system to choose that value based on the set point selected.The results are clearly favour to fuzzy control scheme and it is concluded that the developed rule base fuzzy control technique is works well for non linear systems. |
Tables at a glance
|
 |
 |
Table 1 |
Table 2 |
|
|
Figures at a glance
|
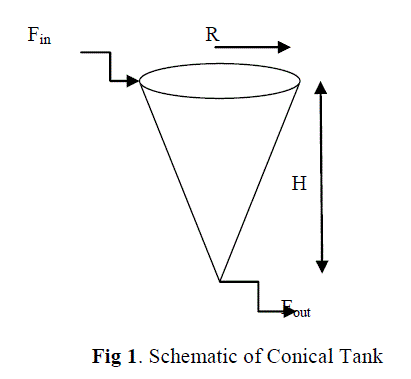 |
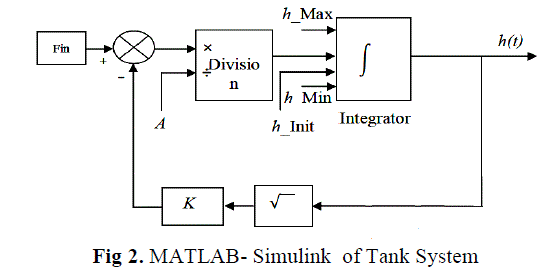 |
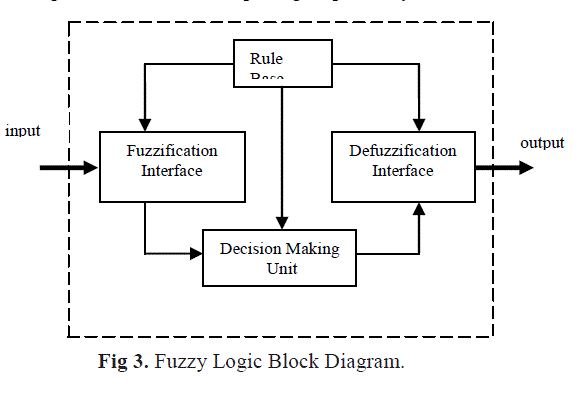 |
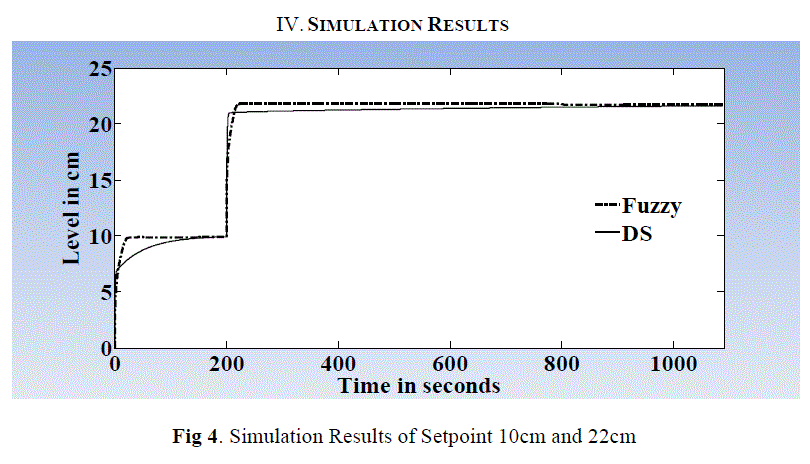 |
Figure 1 |
Figure 2 |
Figure 3 |
Figure 4 |
|
|
References
|
- Ziegler, G. and Nichols, N. B,”Optimum settings for automatic controllers”, Trans. ASME, 64,759-768, 1942.
- Astrom, K J.;.Hagglund .T, , “ Automatic tuning of simple regulators with specifications on phase and amplitude margins”, Automatica, 20,645- 651, 1984.
- G.H Cohen and G.A Coon: “Theoretical Consideration of Retarded Control “, Trans ASME 75,pp.827/834,1953.
- Mamdani EH, “Application of fuzzy algorithm for control of simple dynamic plant”, Proc IEE, 121, 1974, pp.1585-1588.
- Zadeh LA, Fuzzy sets,”Information and Control”, 8(3), 1965 , pp. 339-353.
- C. Georgescu, A. Afshari and G. Bornard,” Fuzzy predictive PID controllers, A heating control application “, Proc. of 2nd IEEE Conf. on Fuzzy Systems, pp.1091-1098, 1993.
- Yonghong Tan Xuanju and Dang Achiel Van Cauwenberghe, “Generalised nonlinear PID controller based on neural networks”, IEEE, Information decision and control,1999.
- S. Skogestad, “Simple analytical rules for model reduction and PID controller tuning”. J. Proc. Cont, Vol 13, pp .291 – 309, 2003.
- S. Nithya, N. Sivakumaran, T. K. Radhakrishnan and N. Anantharaman, “Soft Computing Based Controllers Implementation for Nonlinear Process in Real Time,” Proceedings of the World Congress on Engineering and Computer Science (WCECS ), vol. 2, Oct 2010.
- Ravi V.R., Thyagarajan T. , “Application of Adaptive Control Technique to Interacting Non Linear Systems”, Electronics Computer Technology (ICECT), 2011 3rd International Conference, 386 – 392.2011.
- P.Aravind, M.Valluvan2, S.Ranganathan,”Modelling and Simulation of Non linear Tank”, International Journal of Advanced Research in Electrical, Electronics and Instrumentation Engineering, Vol. 2, Issue 2, February 2013.
- Aravind P., Valluvan M., Saranya M.,” Simulation based Modeling and Implementation of Adaptive Control Technique for Non Linear Process Tank”, International Journal of Computer Applications (0975 – 8887) Volume 68– No.16, 2013.
- P.Aravind, S.M.GirirajKumar,” Performance Optimization of PI Controller in Non Linear Process using Genetic Algorithm”, International Journal of Current Engineering and Technology,Vol.3, No.5, 2013.
- S. M. GiriRajkumar, Dr. K. Ramkumar, Sanjay Sarma O.V," Real time application of Ants Colony Optimization," International Journal of ComputerApplications (0975 - 8887) Vol 3 - No.8, June 2010.
|