Keywords
|
Temperature Parameter, PIC Microcontroller, Control valve, LCD. |
INTRODUCTION
|
Power plant section is one of most important department in the industry. There it is having number of boiling section. This boiling section produces the high temperature water of the steam level temperature. This steam level temperature is used for power generation and the steam waters are applied to the turbine section. After the power is generated, steam waters are supplied to various plants for reuses. If the supply of the high temperature is reduced to low temperature, it will be used for all other plants which needs the low temperature. |
This paper describes the present study involves the separation of water at various different temperatures depending on the needs. In all the industries, water is an in-dispensable major requirement and the water is consumed at different steps. In some industries, the water is obtained along with the final product but at high temperature, which is of NO use. This high temperature water cannot be discharged directly to the soil, as it will make the soil sterile. Hence, this water should be changed to normal conditions before discharged out. The water can also be used when it is normal physical and chemical properties. The Boiled Water Temperature Measurement System is used to measure the temperature of water at various points and to collect the water at different temperatures, which can be used for several purposes. |
EXPERIMENTAL DESCRIPTION
|
A. Materials: Boiler I (14.5 inch height & 11.5 inch diameter), Boiler II (15 cm height, 6 inch diameter), Boiler III (10 cm height, 5 inch diameter), Test tubes (10 inch, 1 cm),Connecting tube I (1 m length), Connecting tube II(1/2 m length), GI metal pipe I (2 feet length, 1.5 inch diameter), GI metal pipe II (2 feet length, 1 inch diameter), Plastic tube (3 m), Control Valve I,II,III,IV (1.15 feet height, 1 cm diameter), Water heater (230 V, 50 Hz, 5 A), Solenoid valve (230 V, 50 Hz, 5 A), Sump motor (230 V, 50 Hz, 5 A), Temperature Sensors I,II LM35, PIC microcontroller 18F452, PIC microcontroller manual kit. |
B. Mechanical Setup: The outlet of the Boiler I is connected to the inlet of the GI metal pipe I through a Solenoid valve as shown in figure. Boiler I has Water heater device and temperature sensor instrument. GI pipe II is connected to GI pipe I through four Control Valves of same length as shown below. One end of the control valve, which is connected to the GI pipe II contains a nozzle like arrangement, which can be adjustable. Boiler II is kept at the outlet of the GI pipe |
I. Boiler II has temperature sensor instrument. Boiler III has a motor, which is connected to one end of the GI pipe II through a plastic tube. |
The other end of the GI pipe II is connected to a plastic tube in such a way that the end of the plastic tube will let into the Boiler III. |
A. Design of Block Diagram: There are three Boilers in this system, namely B1, B2 & B3. The first Boiler contains water heater element and temperature sensor. The second boiler contains a temperature sensor. The third boiler has a sump motor to spray the cool water while processing. As soon as we switch on the PIC Microcontroller hardware circuit, the water of first boiler will be heated, the temperature of the water is measured using temperature sensor. When the temperature at the water reaches at a particular temperature (as we fixed) ex. 90ºC, the solenoid valve is opened. |
The heated water in the first boiler will goes to the second boiler through the connecting tube (CT 1), metal pipe (GI 1) and connecting tube (CT 2). The second boiler again measures the temperature at the collected hot water, which got from the first boiler. |
Here, our aim is to reduce the high temperature to maintain the constant temperature. The constant temperature will be fixed as we wish. To maintain the constant temperature, the third boiler automatically sprays the water through small nozzles arrangement as we set in the programmed. For example we set the constant temperature 50ºC and the first boiler outlet temperature is 90ºC(high temperature). |
When the high temperature reaches the second boiler, the third boiler having sump motor switch on as soon as switched on the sump motor. The third boiler, which contains cool water, will be flowed through the metal pipe GI 2, the outlet at GI 2 again connected to the third boiler. Because of not to dry the third boiler. If it gets dry, the sump motor as getting fault. |
B. Operation of Control Valves: The metal pipe GI 2 having four control valves (CV1, CV2, and CV3 &CV4). Which is connected with metal pipe GI1, each control valves have time gradient. If the temperature of the second boiler goes below (50ºC) the spray of cool water process is stopped. |
If the temperature of second boiler is above the constant temperature (50ºC), the spray of cool water process continues. That means the third boiler contains sump motor will be switched ON and OFF. This process continues for neat cycle. |
HARDWARE DESCRIPTION
|
A. Hardware Setup: PIC microcontroller 18F452 of operating volt of 5V and frequency of 8MHz is used for this study. It contains five ports A, B, C, D and E. Port A is an analog channel, which is connected to the temperature sensors. Port C is connected to ULN 2003 (operating volt-12 V) relay driver IC that is further connected to the relay. Port B is connected to the LCD. PIC microcontroller port pin Rx & TX is connected to a serial communication driver IC Max 232 which is further connected to serial port connector. This serial port connector can be connected to the computer. |
B. Objective of the Project: The main objective of this project is to measure the boiled water temperature in analog form. A circuit, having IC-LM 35 temperature sensor, measures the temperature of the boiled water. The obtained temperature data is transferred through the PIC microcontroller. The microcontroller read the available data and processed |
The output of PIC microcontroller is sent to LCD display. |
(i). Interface the temperature sensor and LCD with microcontroller, |
(ii). Transfer the parameter values through microcontroller. |
TEMPERATURE MEASUREMENT DESCRIPTIONS
|
A. Principle of Temperature: Temperature is the degree of hotness or coolness of a body. When the temperature changes the internal resistance also changes to the corresponding material. |
B. Sensing Device: A sensor is called transducer. The output of the transducer is in the form of voltage current, resistance, or capacitance. The block diagram summarizes the above discussion. |
In this project, Temperature is measured, temperature measurement is important in industries. In industries, there are different types of temperature measurement, according to the range of temperature. |
For example, LM35 is used to measure the temperature in the range of -55Ãâ¹ÃÅ¡C to +150Ãâ¹ÃÅ¡C. . The LM35 series are precision integrate-circuit temperature sensors whose output voltage is linearly proportional to the Celsius temperature. The LM35 thus has an advantage over linear temperature sensors calibrated in ° Kelvin, as the user is not required to subtract a large constant voltage from its output to obtain convenient Centigrade scaling. If we want to measure temperature greater than 1000Ãâ¹ÃÅ¡C we have to use Thermocouples. |
PCB LAYOUT AND DESCRIPTION
|
A. PCB Design for PIC Micro controller: The PCB was designed by using the EAGLE editions. We can add an auto router module or a schematic editor to the Layout Editor. The Layout Editor, which allows to design Printed Circuit Boards. |
Our PCB board is having the facilities of serial port interface with the LCD display. LM35 temperature sensors and relays interfacing and it is having the feature of all interfaces. |
SOFTWARE DESCRIPTION
|
A. MPLAB: The program is written in Embedded C in MPLAB IDE. |
MPLAB Integrated Development Environment (IDE) is an integrated toolset for the development of embedded application employing Microchip’s PIC and PIC microcontroller. MPLAB is a powerful, feature rich development tool for PIC micro controllers. It’s making to provide the programmer with the easiest possible solution of developing applications for embedded system. |
PIC micro controller is the most popular of 8-bit chip in all over the world, if it's used for wide variety of applications, if the prized for efficiency. It’s the natural choice for developing embedded systems, if the boards are set of hardware components. |
CONCLUSION
|
The project of Boiled Water Temperature Measurement System module is used for temperature measurement is designed and developed in department. In Industries we cannot control the high temperature manually. This project provides simple way to measure the temperature parameters, if it is designed using PIC micro controller. |
In this system it has internally ADC, so it needs not go to external interfacing ADC. The temperature of water is measured using (Semiconductor sensor) temperature sensor. In this system, the control valve is manually controlled and temperature is reduced up to preset valve defined by programmer. In future, the flow of boil water is controlled by an automatic control valve. |
The measured temperature data can transfer through the serial port in a PC and store for further process control. Further the same concept is extended to multiple units of same type with small changes. |
ACKNOWLEDGMENTS
|
Our thanks to the experts who have contributed towards development of the template. |
Tables at a glance
|
 |
 |
Table 1 |
Table 2 |
|
|
Figures at a glance
|
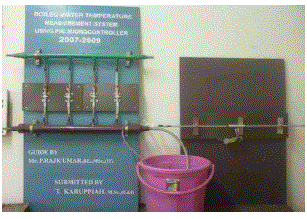 |
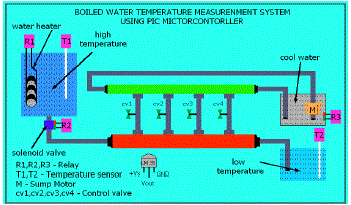 |
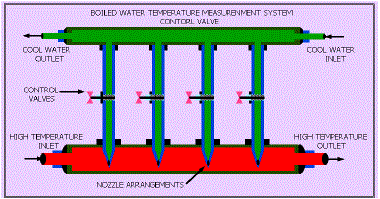 |
Figure 1a |
Figure 1b |
Figure 1c |
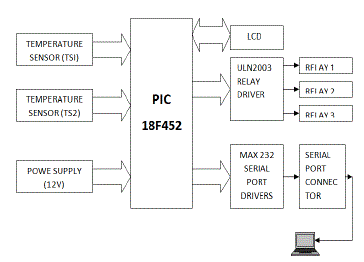 |
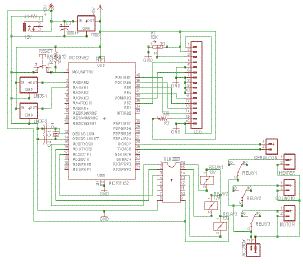 |
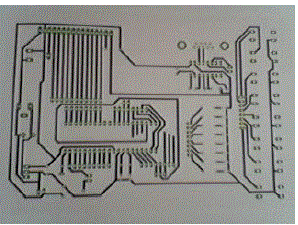 |
Figure 1d |
Figure 1e |
Figure 1f |
|
|
References
|
- Johnathan. w.valvano –Embedded Microcomputer Systems, real time interfacing-Brooks/ Cole, 2000.
- Rajkamal – Embedded Systems Architecture, Programming and Design, TMH, 2008\
- A.Nagoor Kani, Control System, First Edition.
- D.Patranabis, Priciples of Industrial Instrumentation, Second Edition.
- Curtis Johnson, Process Control Instrumentation Technology, Fourth Edition.
- B.G. Liptak âÃâ¬ÃâHandbook of Instrumentation- Process Control
- R.K.Jain, Mechanical and Industrial Measurement, Sixth Edition 2003, Khanan Punlications.
- PIC Microcontrollers - Programming in C,Milan Verle,Number of pages: 336,Publisher: mikroElektronika; 1st edition (2009),Language: English,ISBN-13: 978-86-84417-17-8.
- PIC18F452 Micro Controller Data Sheet.
- PIC 16F877 DATA Sheet.
|