Keywords
|
Photovoltaic Power Generating System; Three-stage charging method; MPPT; PI |
INTRODUCTION
|
These days, sustainable development of the natural resources has become the common sense of all the countries over the world. Among all the natural resources, photovoltaic technology has become more and more popular. Power generation based on photovoltaic technology has been widely studied. With the development of the photovoltaic technology, the efficiency is becoming higher, and the manufacture cost is becoming lower, so the cost and life-span of battery becomes more important in system. However, because of the non-linear characteristics of the photovoltaic (PV) module, there are lots of problems associated with the rechargeable battery used in PV generation system, and these problems have become the constraints of the whole system performance. The batteries used in the PV system are not specially designed for the PV system, take Valve-Regulated Lead Acid Battery (VRLA) for instance, it has been widely used in PV generation system due to its low cost, stable voltage and low pollution. While in practice, the life-span of the VRLA has been extremely reduced to only 3-5 years (Normally the life span of VRLA is about 10-15 years), in some extreme cases, the battery wears out in just one year, and even leads to great cost loss. After studying the characteristics of the VRLA, it is found among all the possible reasons which cause the damage of the VRLA, unreasonable control of the battery charge is probably the prominent one. The early stage loss of the capacitance of VRLA, uncontrollable heat and drying of the electrolyte all have something to do with the uncontrolled battery [1]. In addition, efficiency of the photovoltaic module varies with the temperature and duration of the sunshine since altitude, latitude, time and atmosphere all influence the performance of the PV system. Simple control is very hard to make the most of the efficiency of the system and at the same time increase the life-span of the rechargeable battery. In order to solve these problems, this paper introduces three-stage charging method and sets up a medium size charging control system based on the chip of PIC16F877A. Experimental results show the system works on well based on the control scheme. |
SYSTEM CONFIGURATION
|
Power stage in PV system mainly consists of rechargeable battery, main converter circuit, controller, seen in Figure 1. As the power stage block, the rechargeable battery plays an important role in the whole system since it supplies the power to the load side. The main converter circuit is a DC/DC buck converter and the controller is designed based on the chip of PIC16F877A from Microchip. By proper control of the output voltage and current, the controller can realize better outcome under the different control scheme. |
MAIN CONVERTER CIRCUIT
|
The three-state charging method is achieved by changing the operating point of the converter, which is done by changing the duty cycle of the power device of the converter. The main circuit is shown in Figure 2, the buck converter is made up of power MOSFET G, free-wheeling diode, anti-power diode D2, choke L, output filter capacitor C2 and input filtering capacitor C1, which is paralleled with the PV array, provides the pass for the high frequency input current, so that the voltage over the capacitor can be maintained stable. |
The main power device in the converter is chosen as IRFP150N based on the consideration of current, voltage and frequency. The inductance in system is used to eliminate the high switching frequency and the high order harmonics of current so as to improve the output waveform. Compared to the capacitor impedance, the impedance of the inductance should not be lower. In order to obtain a good output waveform, it is required that in one sampling time interval, the variation value of current within the inductance must be below than the current ripple that is allowed. The filter capacitor is added to the circuit to eliminate the high order harmonic distortion with the help of the filtering inductor. The bigger the capacitance of the capacitor, the less Total Harmonic Distortion (THD) it can be. Within the THD standard, the capacitance of the capacitor should be chosen as small as possible. CBB capacitor [2], due to its good performance in high frequency and low loss, is recommended here. The switching frequency in system is 20KHz, taking the gain margin of the system, C1 is then chosen to be 220uF, L is chosen to be 0.8mH, C2 is 100uF. |
PV MODULE CHARACTERISTICS AND BATTERY CHARGING CHARACTERISTICS
|
Figure 3 is the I-V and P-V curves of photovoltaic module, the left figure is the I-V curve of photovoltaic module, and the right one is the P-V curve [3]. According to the I-V curve, during the most working voltage range, the output current of PV array changes a little when the voltage varies. Once the output voltage exceeds a certain value, the output current will drop sharply with the output voltage rising. The P-V curve of photovoltaic module is similar to a parabola of direction downward. When the module voltage lies in the maximum value (Vm ), the output power of photovoltaic module will be the maximum value ( Pm ). It is observed that the PV module is neither a constant voltage source, nor a constant current source, but a kind of non-linear DC power supply. Thus it can not provide large enough power to load, and its output is affected by sunshine intensity, environmental temperature and load. The PV module can achieve maximum output power only at one output voltage. In order to make PV module output maximum power, it is necessary to apply the MPPT technology in the charging control of photovoltaic system, so as to ensure the effective use of energy of PV module conversion. |
The battery can be equivalent to a voltage source of little internal resistance. If the battery and PV module connected directly, the I-V characteristics curve of battery can hardly intersects with the PV module in its MPP of I-V characteristics all the time. The I-V characteristics curve of the battery should be changed during the running process to intersect with PV module in the MPP. In addition, in the general photovoltaic systems, the charging rate of batteries are little, and the rechargeable time is limited, which often make battery in own-charging status and accelerate the negative plate of the battery sulfuric acid salinization, even causing battery capacity loss and influencing its life-span. Based on the analysis, the chip of PIC16F877A is used to monitor and control the process of battery charge, adopting three-stage method to optimize the charging process. The charging characteristics curve of battery is shown in Figure 4. |
STRATEGY OF CHARGE CONTROL
|
For an independent PV system, due to the non-linear characteristics of the PV module, the unpredictable duration of sunshine, it is really hard to make the full use of the PV module. In order to improve the efficiency of the PV module, MPPT technology is introduced. In addition, to prolong the life-span of battery, a three-stage charging method is introduced thus. During the stage of constant current charging, if the charging current is lower than the rated value, otherwise the duty cycle is increased to insure that the charging current reaches rated current value. This stage requires that 80-90% of the capacitance of the battery should be reached so as to make the most use of the battery. In the stage of constant voltage charging, if the output voltage is bigger than the rated voltage, the duty cycle is then reduced, or so increased. During this stage, 97% of the charging capacitance can be reached. In the stage of float charging, PI control is used to make sure a very small amount of current is injected to battery compensating the loss of the battery owndischarge |
A. MPPT control in constant current charging stage |
In the light of the fixed curve of PV system, the slope is zero at the maximum power point [4]. Hence, we can obtain these equations as follows: |
(1) |
(2) |
(3) |
Here, max P is the value of maximum power, V is the output voltage of PV array and I is the output current of PV array. Equation (3) is where the maximum power point is, namely when the conductivity change rate equals negative conductivity value, PV module works in its maximum power point. If not so, it is needed to judge if the value of dP / dV is zero or above zero, the flow chart of this method is shown in Figure 5. |
Where, Vn and In is the newly detected voltage value and current value, Vb and Ib is the previous value. The newly detected value is compared with the previous value. If the error is zero, current error is then calculated as the same. If both the voltage error and the current error are zero, the disturbance Duty cycle (D) value doesn’t change. When the voltage error is zero and the current error is not zero, if the current error is positive, the disturbance D value increases. If the current error is negative, the disturbance D value reduces. Then, if the voltage error is not zero, it is a key whether (3) will correct or not. If (3) is attained, the slope of power curve is zero(reaches the MPP).If the conductivity change rate is more than negative conductivity value, the slope of power curve is positive and the D value increases, conversely, the D value reduces. It is very important that a highly sensitive sensor is needed in this method, in this case, a Hall-effect sensor is used sample the voltage and the current. Above all, this method is accurate, with high dynamic response and suitable for those environments where weather changes dramatically. |
B. PI control in the constant voltage charging and float charge stages |
When the voltage reaches the constant voltage charging voltage value, the sub-program is then introduced. Constant voltage charging is set off after the constant current charging stage in order to make the battery reaches its maximum capacitance. At this stage, the voltage of the battery should be measured all the time to make it stable. So a voltage feedback loop is necessary. In order to improve both the steady state and dynamic state performance, a digital PI controller is designed. After sampling, the sampled voltage is compared with the reference voltage value and an error (ΔU) is then generated. After PI control, the duty cycle of the MOSFET is obtained and a stable battery voltage can be achieved. |
During the constant voltage charging stage, the current is observed. If current value reaches its threshold value, the constant voltage charging stage will stops. At this time, it is believed that the constant voltage charging is stopped and the float charging begins. The purpose of float charging is to inject a small amount of current to compensate the loss because of own-discharge of the battery. In the float charging stage, PI makes sure that the voltage stays in the range of the float charging voltage. A precise control of the float charging voltage is vital to the system, so the voltage variations must be constrained to certain value. Take 12V VRAL battery for instance, 14.5V is set to be constant voltage value, while float voltage is set to be 13.8V, the whole process is shown in Figure 6. |
C. Temperature compensation |
In the period of battery charging, the temperature of electrolyte is rising. When the temperature changes the voltage threshold value of battery will change accordingly. In order to extend the life-span of lead-acid batteries, the voltage value of constant voltage charging and the float charge voltage value must be compensated. |
When the range of battery temperature fluctuation exceed the rated temperature ±5 caused by the influence of external condition. Then the given voltage value of constant voltage charging of battery urgently needs be changed accordingly. The needs are more urgent especially for all kinds of VRLA, because this kind of storage battery is very sensitive to constant voltage charging. After using temperature compensation, it can be fully filled even in cold winter, and the decline of battery life-span caused by constant voltage charging will not happen in summer. Take the mono-case for example, if the effective range of temperature compensation is 10~35 , the coefficient range of VRLA temperature compensation value is 0.1~5.0 V/ _>_@. In the process of temperature compensation, the temperature values are collected by temperature sensors. The given voltage value of constant voltage charging and float charging can be worked out according to the current compensation formula, and the voltage will be benchmark of PI control in the constant voltage charging and float charging stage. |
EXPERIMENTAL RESULTS AND ANALYSIS
|
Panasonic VRAL battery LC-R127 is used in this experiment, its rated voltage is 12V and the rated capacity is 7Ah. In the experiment, the temperature is 25 , the constant voltage charging voltage is set to be 14.5V and the float charging voltage is set to be 13.8V. Table 1 is the experimental data. From table 1, after five hours of constant current charging, the stage is changed to be the constant voltage charging. The range of current in the constant current charging stage is between 1.24~1.16A. The current has no significant changes in the constant current charging stage, and the current has good stability. During the constant voltage charging stage, the voltage value of battery changes from 14.4V to 14.5V, which changes scarcely in the constant voltage charging stage, and the stability is good. After seven hours of charging, the float charging stage is reached, the actual measurement of float charging voltage is 13.7 V and the given voltage is set to be 13.8 V, the error(0.1V meets the requirement. By the table and the analysis, it can be found that the controller is very good for photovoltaic module to achieve the three-stage charging, and has good accuracy of constant voltage charging and float charging. |
CONCLUSION
|
Nowadays, as the environmental pollution and energy crisis is increasing seriously, photovoltaic power generating system will become more and more popular. However, in the photovoltaic system, the output energy of PV module is uncertain and condition of using the battery is particular, which makes battery become an important part in affecting the life-span of the whole photovoltaic power generating system. It is also an important factor preventing the development of photovoltaic industry. This requires a reasonable charge control strategy, to make full use of the output energy of PV module and to manage the battery efficiently, and to extend the life-span of the battery. This charging control strategy meets the above requirements, and the hardware of control system structure is simple and high performance, and has prominent advantages in the small and medium-sized PV systems. |
Tables at a glance
|
 |
Table 1 |
|
|
Figures at a glance
|
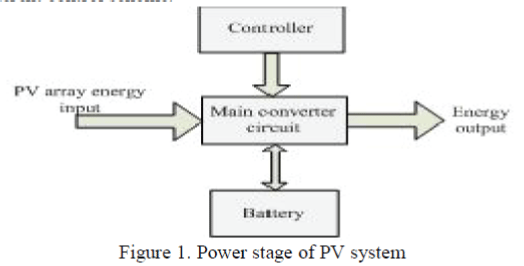 |
 |
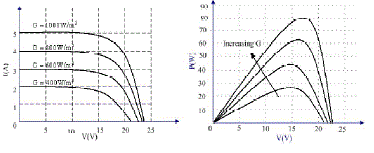 |
Figure 1 |
Figure 2 |
Figure 3 |
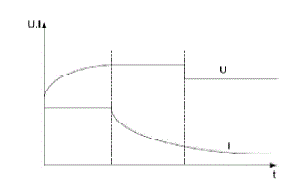 |
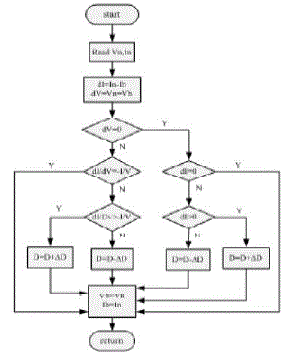 |
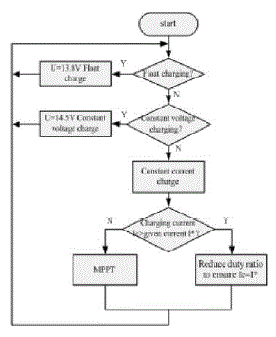 |
Figure 4 |
Figure 5 |
Figure 6 |
|
|
References
|
- Zhou Zhimin and JI Aihua, “Solar LED lamp design & application,” [M] Beijing, On Industrial Electronics, 2009.
- NageshwaraRao K, Suryanarayana K, Bhudeb, EMI/EMC test facility at research center imaratan overview, IEEE Trans. On Industry Applications, 1997
- A.K. Mukerjee and NiveditaDasgupta, “DC power supply used as photovoltaic simulator for testing MPPT algorithms,” Renewable Energy, 2007, (32) pp. 587-592.
- Johan H R Enslin, Mario S Wolf, Daniel B Snyman, “Integrated photovoltaic maximum power point tracking converter,” IEEE Trans. On Industrial Electronics, 1997, (6) pp. 43-45
- OuyangMingsan. “Study one the batteries management in stand alone photovoltaic system” [D] Hefei, Hefei University of Technology, 2004 pp. 49-59.
|