Keywords
|
Liquid Heating System, Heat Exchanger, Neuro Fuzzy controller(NFC),Adaptive Neuro Fuzzy Controller (ANFIS),Subtractive clustering, Liquid Temperature , Desire Temperature. |
INTRODUCTION
|
Heat exchangers are an essential ingredient in a wide range of industrial applications. Fast tracking of set point change, steady state step disturbance rejections are standard performance requirement for controllers of heat exchanger. |
The majority of Heat Exchanger used in Industry [1] operates in closed loop with standard proportional plus integral controllers. Heat exchanger system exhibit different time constants for heating and cooling and non-linear static characteristics |
Conventional control theory was based on mathematical models that described the dynamic behavior of process control systems. Fuzzy logic was a flexible approach to conventional controllers. Conventionally, the plants in an industry were controlled by PID controller with Ziegler- Nichols (Z-N) method. The conventional PID controller is not suitable for nonlinear systems [2]. FLC, which were based on human knowledge, were more flexible than conventional PID controllers [3]. |
Both Fuzzy and Adaptive control algorithms have built in mechanisms that make them well suited for functioning in modern control scenario[4][5] |
Since the Procyk and Mamdani self organizing controller [6], many Fuzzy adaptive systems were designed and some practical results were reported [7] [8].Fuzzy adaptive systems provide the advantage that both numerical and qualitative information are used in the construction and training stages. Furthermore Fuzzy systems are proven to be applied to approximate any continuous nonlinear function [8]-[11] |
JyhShing Roger Jang et.al. [12] Developed the architecture and learning procedure underlying ANFIS (adaptive neuro fuzzy inference system) which is a fuzzy inference system implemented in the framework of adaptive networks. ANFIS architecture is employed to model nonlinear functions by identifying nonlinear components in a control system |
In this paper, both NFC and ANFIS are designed for achieving the desired temperature in the Heat Exchanger. |
NFC is hybridization of Neural Network and Fuzzy system. It uses the back propagation algorithm for training neural network and decides structure by trial and error method. |
ANFIS also combines the advantages of Neural Network and Fuzzy system .It gives adaptive structure and uses hybrid learning laws which combines back propagation algorithm and least mean square algorithm. Furthermore, to reduce the complexity of a given problem, or to reduce the amount of data associated with a problem first clustering can be done and then Fuzzy Inference System (FIS) is generated. Therefore we tried NFC and ANFIS for controlling the temperature of Heat exchanger. |
This paper is organized as follow: Section I gives the introduction of different controlling techniques of heat exchanger and recently available related work. Section II explains the System hardware. Section III contains various controlling techniques. Section IV shows the performance and discussion and last Section V concludes the paper,followed by the references. |
LIQUID HEATING SYSTEM
|
The structure of the liquid heating system is illustrated in Fig.1. |
The condenser is a device, used for transferring the heat. The condenser consists of two tubes: inner tube and outer tube. The inner tube contains hot liquid, supplied by hot water tank and the outer tube contains cold liquid, supplied by cold liquid tank. The outer tube liquid temperature is controlled by the inner tube liquid of the system. The hot water tank contains heater circuit, stirrer and float type level sensor. The heater circuit consists of Resistance Temperature Detector (RTD), ON/OFF switch and heating coils. The hot liquid tank will continuously supply hot liquid through Automatic Control Valve (ACV), to maintain the heat ratio of the condenser, and which will be controlled by NFC and ANFIS based controller. The exhaust hot liquid is removed. The temperature of the condenser (outer tube) is detected by RTD and given to bridge circuit. The bridge circuit detects the temperature changes and applied to the instrument amplifier. This analog input is converted to digital and applied to the NFC and ANFIS for determining the liquid temperature ratio. The digital output of NFC and ANFIS is converted into analog and further used to control the valve by using pneumatic source. |
DETERMINATION OF LIQUID TEMPERATURE RATIO
|
NFC and ANFIS are used to calculate the liquid temperature ratio of the system. The ratio of liquid temperature is determined from the current temperature and the change of temperature. The formula for change of temperature is described as follows, |
 |
Neuro-Fuzzy Controller:
|
Determination of Liquid Temperature Ratio Using Fuzzy
|
The liquid heating system is operated based on multi-variable fuzzy control system. The operation of fuzzy control system is mainly relies on fuzzy rules, which are generated using fuzzy set theory.. The fuzzified error temperature and change of error temperature are applied to the decision making process, which contains a set of rules. Then, the defuzzification process is applied and the liquid temperature ratio is determined. The developed fuzzy rules are tabulated in Table 1. Using these fuzzy rules T FRis determined. |
Determination of Liquid Temperature Ratio Using NN
|
These algorithms are operated based on training dataset. From the fuzzy rules, the network training dataset are generated. Feed forward type NN is used for the model. The input layer consist of two inputs i.e., error temperature „ e âÃâ¬ÃŸand change of error temperature âÃâ¬ÃŸΔeâÃâ¬ÃŸ. The liquid temperature ratio „ T NNRâÃâ¬ÃŸ is the output of the NN. |
The training steps involved in neural network are as follows, |
Step 1: Initialize the input, output and weight of each neuron. Here, e and Δe are the inputs of the network and the liquid stream ratio „ T NNR âÃâ¬ÃŸis the output of the network. |
Step 2: The inputs of training dataset are e and ïÃÂÃâeto the classifier and determine the BP error as follows, |
 |
Step 3:Calculate the network output as follows, |
 |
Eqn. (3) and (4) represents the activation function of output layer and hidden layer respectively. |
Step 4: Adjust the weights of all neurons as w = w+ Δw, where, Δw is the change in weight, which can determined as |
 |
Step 5: Repeat the process from step 2, until BP error gets minimized to a least value i.e. |
 |
Once the process gets completed, the network is well-trained and it would be suitable for providing T NNR values for any error and change of error temperature. |
Hybridization of FLC and NN output
|
Hybridization is based on the performance improvement of the process system. The liquid stream ratio „TR âÃâ¬ÃŸ of the condenser is calculated for hybridizing the FLC output and NN output. Here, mean operation based hybridization is used for calculating the liquid stream ratio TR . The mean liquid stream ratioâÃâ¬ÃŸTR âÃâ¬ÃŸ is calculated as follows. |
 |
output. These mean liquid stream ratioâÃâ¬ÃŸ TR âÃâ¬ÃŸ is applied to the input of the condenser by adjusting the ACV .In this way, the temperature of the liquid heating system is to be maintained. |
Adaptive Neuro Fuzzy Controller-
|
The liquid heating system is operated based on subtractive clustering and adaptive neuro fuzzy inference system. The operation of adaptive neuro fuzzy control system is mainly relies on fuzzy rules, which are generated using subtractive clustering. |
Adaptive Neuro-Fuzzy Inference System
|
An ANFIS is a multilayer feed-forward adaptive network (Figure 2) in which each node performs a particular function (node function) on incoming signals as well as a set of parameters pertaining to this node. Subtractive clustering is used to generate fuzzy clusters. Each fuzzy cluster is mapped into a generalized predefined membership function. A square node has parameters while a circle node has none. In order to achieve a desired input-output mapping, these parameters are updatedaccording to given data and hybrid learning rule. |
ANFIS architecture is shown in figure 2, where nodes of the same layer have similar functions. Consider two inputs x and y which form two fuzzy if-then rules |
 |
The output of ith node in layer 1 is denoted as Oli Layer 1 - Every node i in this layer is an adaptive node with node function |
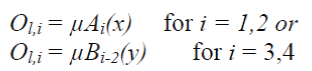 |
Ai(or Bi2) is a linguistic layer associated with the node. Here the membership function for A (or B) can be any parameterized membership function. We have used Gaussian membership function given by |
 |
Where {ci, ai} is the parameter set. These are called premise parameters. |
Layer 2: Every node in this layer is a fixed node labeled π, whose output is the product of all the incoming signals. |
 |
Layer 3: Here, the ith node calculates the ratio of the ithruleâÃâ¬ÃŸs firing strength to the sum of all ruleâÃâ¬ÃŸs firing strengths. |
 |
Layer 4: Every node i in this layer is an adaptive node with a node function |
 |
Where wi is a normalized firing strength from layer 3 and {pi, qi, ri} is the parameter set of the node. These parameters are referred to as consequent parameters. |
Layer 5: The single node in this layer is a fixed node labeled Σ, which computes the overall output as the summation of all incoming signals: |
 |
In ANFIS, the parameters are associated with given membership function to tailor the input-output dataset. The input membership functions of a Sugeno model are non-linear (Gaussian Membership function) whereas the output membership functions are linear. So, while tuning the parameters from a given input/output dataset, it is most effective to use hybrid learning algorithm. Since, the input functions are non-linear, error Back-Propagation method is suitable. As output functions are linear Least Square Estimation method becomes effective. |
RESULT AND DISCUSSION
|
The liquid heating system is simulated in MATLAB working platform version 7.12. The performances of liquid heating system at different temperature variations are analyzed. The developed liquid heating system simulation model is illustrated in Fig.3. |
NFC Results
|
The error and change of error temperature are applied to FLC and the liquid temperature ratio is determined. Surface graph between the error, change in error and predicted output (model output) of NFC is shown in fig.4 |
The performances of output liquid temperature variation is described in Fig.5 |
The output liquid temperature variation of the liquid heating system after using the NFC is described below. The performance of liquid temperature ratio from the condenser are described in Fig.6. |
ANFIS Results
|
Error temperature and change in error temperature are the two inputs of ANFIS structure .The membership function of each input was tuned using the hybrid method. |
Input dataset is clustered using subtractive clustering before training. The radius used in ANFIS for clustering the data is 0.5. Numbers of epochs assigned are fifty. The ANFIS model is trained by using training data set. Goal for the error is set to 0.05. After training, final configuration for the FIS is generated. Structure of generated FIS is shown in figure 7 |
Surface graph between the error, change in error and predicted output (model output) of ANFIS is shown in figure 8. |
The output liquid temperature variation of the liquid heating system after using the ANFIS is described below. |
The performance of liquid temperature ratio from the condenser are described in Fig.10 |
CONCLUSION
|
In this paper, the NFC and ANFIS based model for Heat exchanger system has been designed for maintaining the desired liquid temperature. The model of system is simulated and the output performances are analyzed. The overall performance of both NFC and ANFIS controller is exceptionally accurate. Both need prior analytical information. The ANFIS Performance is slightly better. In addition ANFIS has an adaptive structure therefore no trial and error method is required to decide a structure. The most important point is, it uses different learning algorithms to learn the linear and non linear data. Simulation results have shown that the ANFIS controller has a broader class of nonlinear systems. |
Tables at a glance
|
 |
Table 1 |
|
|
Figures at a glance
|
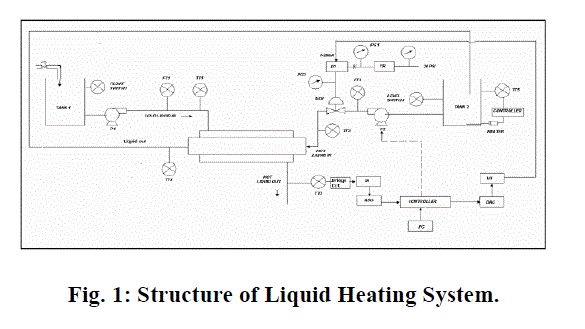 |
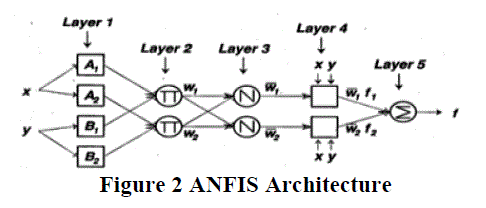 |
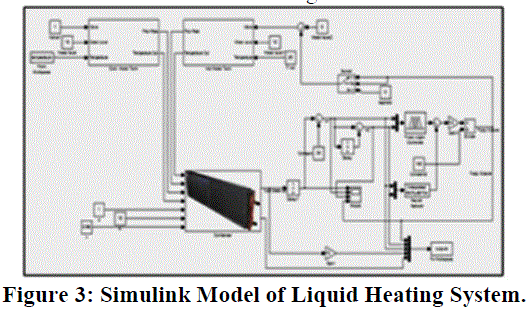 |
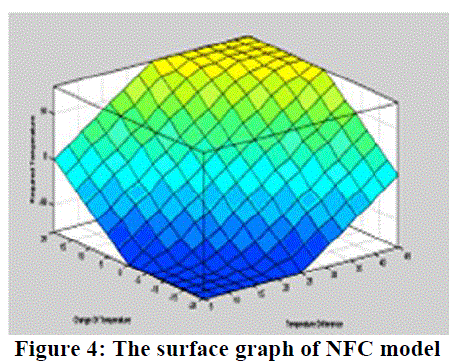 |
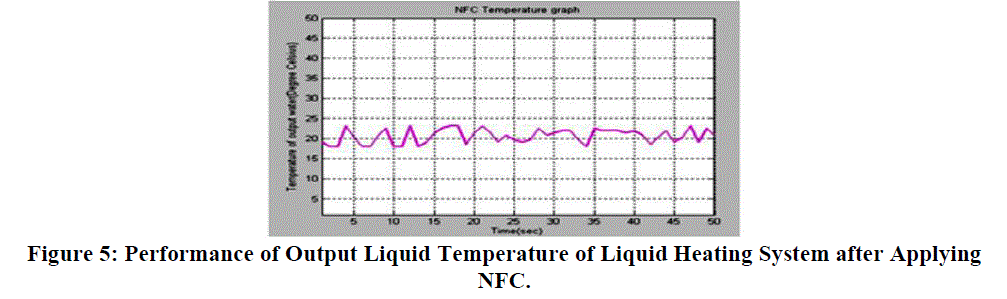 |
Figure 1 |
Figure 2 |
Figure 3 |
Figure 4 |
Figure 5 |
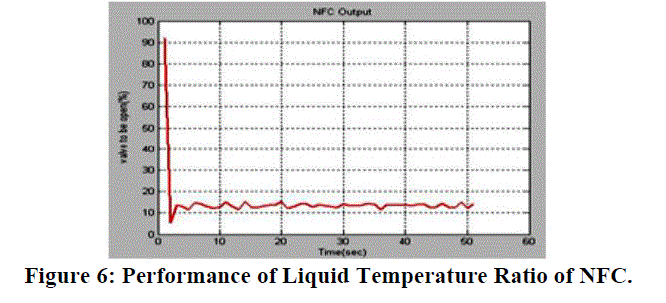 |
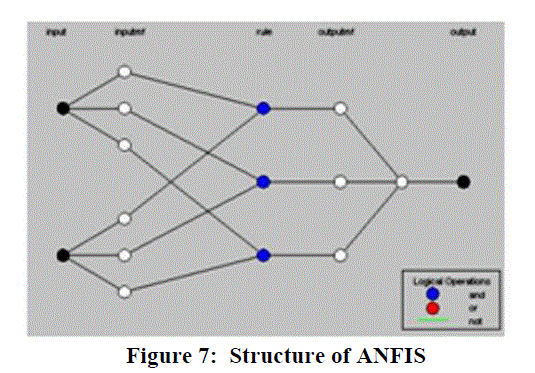 |
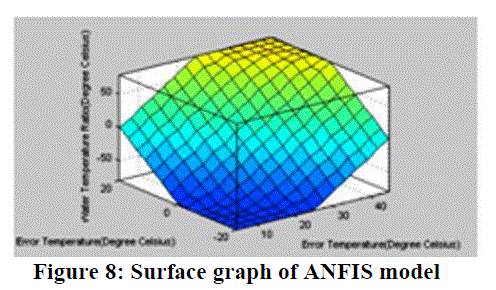 |
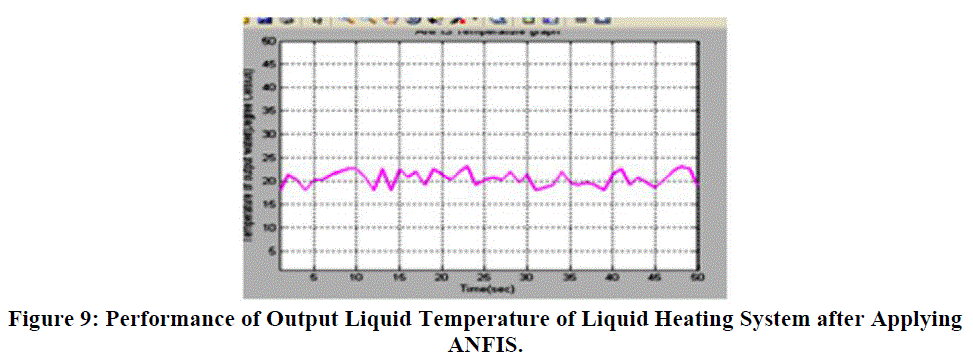 |
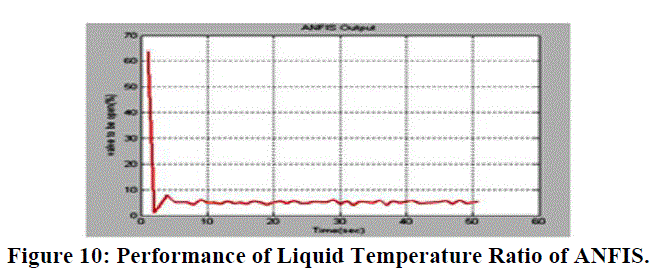 |
Figure 6 |
Figure 7 |
Figure 8 |
Figure 9 |
Figure 10 |
|
|
References
|
- F.G.Shinskey,Process Control Systems,New York:McGraw-Hill,1979.
- K. S. Tang, Kim Fung Man, Guanrong Chen, Sam Kwong, “An Optimal Fuzzy PID Controller”. IEEE Transactions on Industrial Electronics, Vol.48, No.4, pp.757-765, August 2001
- Bambang Suprianto, Mochamad Ashari and Mauridhi Hery Purnomo, “Control system for non identical dc-dc converters using adaptive neuro fuzzy inference system”, International Journal of Academic Research, Vol.3. No.2. pp.716-721, March 2011
- S.Chiu,S.Chand,D.Moore and A.Chaudhary.” Fuzzy Logic for control of roll and moment for a flexible wing craft”. IEEE Control Syst.Mag.,vol 11 no.4,pp42-48,1991.
- S.M.Smith and D.J.Comer,”Automated calibration of a fuzzy logic controller using a cell state space algorithm.” IEEE ControlSyst. Mag.,vol 11,no.5, pp. 18-28,1991.
- T.Procyk and E.Mamdani,âÃâ¬ÃŸA linguistic self-organizing process controller,âÃâ¬ÃŸ Automatica, vol.15,pp. 15-30 ,1979.
- M.Jamshidi,N.Vadiee,andT.J.Ress,Fuzzy Logic and Control. Upper saddle River,NJ:Prentice- Hall,1993.
- K.M.Passino and S.Yakovich,Fuzzy control.Reading,MA:Addision-Wesley,1998.
- L.X.Wang.Adaptive Fuzzy Systems and Control:Design and Stability Analysis Upper saddle River,NJ:Prentice-Hall,1994.
- H.Ying.”Sufficient conditions on genral fuzzy systems as function approximators,âÃâ¬ÃŸ Automatica, vol.30,pp. 521-525 ,1994.
- J.J.Buckly,”Seguno type controllers are universal controllers,”Fuzzy sets Syst., vol 53,pp. 299-303,1995.
- Jyh – Shing Roger Jang , “ANFIS: Adaptive Network Based Fuzzy Inference System,” IEEE Transactions On Systems,Man and Cybernetics, Vol.23, No 3, p.p 665-679, May-June 1993.
|