Keywords
|
Polymer Matrix Composite, glass powder, epoxy resin. |
FABRICATION
|
The circular pipe is used as die. There are two plungers fabricated to compress the material at both the ends of the pipe. The plungers are turned from steel rods to the inner diameter of the pipe, so that tight fit can be obtained. The prepared die and plunger are shown in the fig.1 |
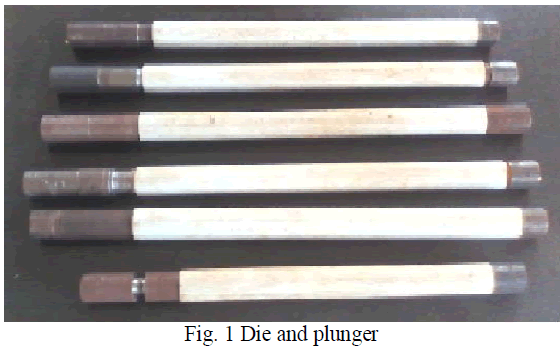 |
Two different composition samples are fabricated with the above combination of glass powder and epoxy. Sample 1 consists of 70% epoxy resin and 30% of glass powder. Then the hardener is added that composite. This mixture is mixed manually by using iron rod. |
By using the plunger, one end of the pipe is arrested and the mixture is poured into it. During the filling of material care must be taken to avoid blow holes and porosity. After filling of material in the pipe the other end of the pipe is also shut by another plunger. Then it is fixed in the lathe, one end of the pipe is fixed to the chuck, and on the other end compressive force is applied by the tail stock. Now the pipe is fully sealed against any movement. Then it is kept to dry in the same position for 1-2 days. |
After two days of dryness, the tailstock is taken back and the plunger is removed. During removal of plunger, ensure that its dried completely. For removal of the composite material from pipe, turning operation must be done. By turning the pipe, composite material is taken out. The specimen with 70%epoxy and 30% glass powder for removing from the pipe is shown in fig.2 |
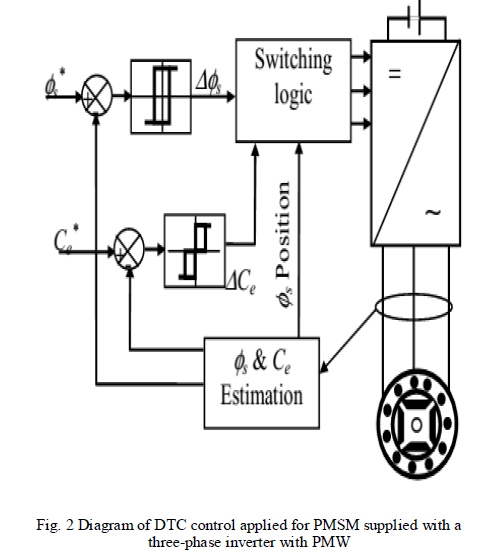 |
MICRO STRUCTURE ANALYSIS
|
Micro structure analysis reveals the structure of the prepared surface of material as shown in the microscope above 25* magnification. Microstructure strongly influences physical properties. Distribution of metal materials all over the specimen. Microstructure of glass powder with epoxy resin in the ratio of 30:70 is shown in the below figure.3. The white spots in the image shows the presence of glass powder and other portion of the image shows the epoxy resin. |
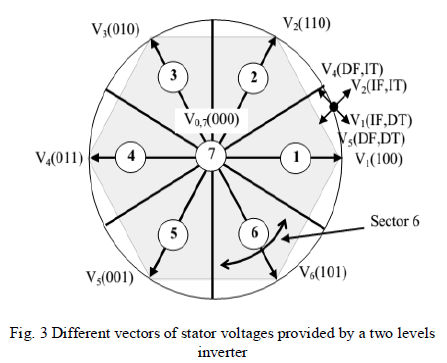 |
CONCLUSION
|
The glass powder is uniformly distributed in the epoxy resin, it will give a good mechanical property to the composite. The mechanical properties testings such as tensile test, impact test, hardness test are going to be carried out. |
ACKNOWLEDGEMENT
|
First I would like to thank god, and my family who supported me always. I express my sincere thanks to Dr. S. Sivasankaran, Ph.D., Associate Professor for his guidance in this project. |
References
|
- Alipio BC, David FC, Isabel RS, Juan CNM. Manuel AE. Comparison of batch, stirred flow chamber, and column experiments to study adsorption, Desorption and transport of carbofuran within two acidic soils. Chemosphere. 2012; 88(1): 106-120.
- Arnaud B, Richard C, Michel S. A comparison of five pesticides adsorption and Desorption processes in thirteen contrasting field soils. Chemosphere. 2005; 61(5): 668-676.
- Chunxian W, Jin-Jun W, Su-Zhi Z, Zhong-Ming Z. Adsorption and Desorption of Methiopyrsulfuron in Soils. Pedosphere. 2011; 21(3): 380-388.
- Chunxian W, Suzhi Z, Guo N, Zhongming Z, Jinjun W. Adsorption and Desorption of herbicide monosulfuron-ester in Chinese soils. J Environ Sci. 2011; 23(9): 1524-1532.
- Christine MFB, Josette MF. Adsorption-desorption and leaching of phenylurea herbicides on soils. Talanta. 1996; 43(10): 1793-1802.
|