The transient surface cooling of a hot stainless steel surface is obtained by a water jet impingement cooling method. The surface is electrically heated up to the initial temperature of 800 C. Water flow rate is kept constant so that jet Reynolds number remains at Re=24000. Nozzle exit to surface spacing has been changed in a range of z/d = 4-16. For larger surface temperature drop change in nozzle exit to surface spacing does not affect the surface cooling time significantly. However, for lesser surface temperature drop particularly at higher range of surface temperature, surface cooling time is approximately 15 % higher with z/d =4.
Keywords |
Jet impingement, stagnation point, transient cooling, heat transfer |
INTRODUCTION |
The rapid quenching of hot surfaces has become one of the main processes in many industrial applications. The common
application are the cooling of high temperature gas turbines and combustor walls, paper industries, textile and films drying,
annealing and cooling of metals, glass manufacturing, thermal control of high-density electronic equipment and many more.
The Jet impingement is one of the methods to achieve the quenching with high rate of cooling. There are many parameters
that affect jet impingement quenching phenomena that are jet configuration, jet size, fluid flow rate or Reynolds Number,
Fluid temperature, Surface temperature, Jet exit to surface spacing, Surface orientation and roughness etc [1,2, 3].
The coolant fluids used in jet impingement are mainly air and water but some research has also been reported with
fluorocarbons (FC) and Freons [4, 5]. However, water has been used extensively for the cooling of the hot surfaces
particularly in the steel industries. The selection of fluid basically depends on rate of heat removal desire from the hot
surfaces. Field of jet impingement cooling is not new, numbers of experimental [1-5] and analytical [6, 7] and work has
been published so far that covers wide area of research. |
Present investigation has explored the effect of jet exit to surface spacing on the cooling of stainless steel surface of 800 °C
temperature. The time varying surface temperature is recorded at the stagnation point for water jet impingement cooling.
Water jet of 2.5 mm diameter and 22 ± 1 °C has been impinged on the hot surface with the flow rate of 2.75 lpm. The jet
exit to test surface spacing is varied in the range of z/d = 4-16. |
EXPERIMENTAL SET UP |
The experiments were performed for the cooling of a hot stainless steel horizontal surface using tap water at 22±1 °C
temperature. The schematic of the experimental set up is shown in the Figure 1. Initially water was collected in a reservoir
(9) and supplied to the jet nozzle (1) with the help of a water pump (8). A flow control valve (7) and a turbine flow meter
(6) were installed on the water supply line. The nozzle was mounted on a main frame (5) of a work table (2). The hot test
surface was placed on a work table (2) underneath to the nozzle. The positioning of the test surface was done with a lateral
and transverse movement handle provided on the work table. The water jet of 2.5 mm diameter was impinged through a
straight tube nozzle (1) on the hot test surface. A ungrounded K-type thermocouples was attached on the back side of the
test surface and were connected to the Data Acquisition System (3). Initially, the test surface was heated up to 800 °C using
a high current and low voltage auto-transformer arrangement. Two copper bus bars from the terminal of auto-transformer
were attached on both sides of the test surface to minimise the voltage drop between the transformer and the test surface.
The nozzle exit to test surface spacing was varied by moving the nozzle in vertical direction. The vertical movement of nozzle was obtained with a rack pinion arrangement provided on the main frame and the nozzle position was observed on a
vertical scale. |
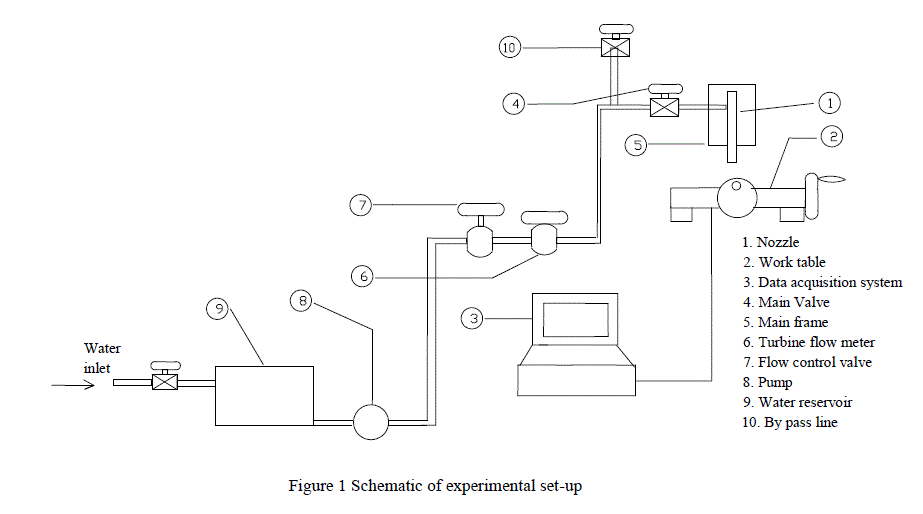 |
The test section was a 140 mm long, 30 mm wide and 3 mm thick Stainless steel surface. The mineral insulated K-type
ungrounded thermocouple of 0.25 mm sheath diameter was spot welded at the geometric centre of the test surface. The
geometrical centre of test surface was always kept the beneath of jet centre. The back side of the test surface was made
perfectly insulated by applying ceramic insulation and the Teflon base. |
The resistance heating of test section was done slowly up-to the initial surface temperature of 800 oC by regulating auto
transformer. The voltage drop across the sides of test surface was measured using digital voltmeter. The current through the
test section was recorded with the help of an ammeter and a current transformer (CT) arrangement. The surface
temperature during transient cooling was recorded by using a data acquisition system and the water flow rate through the
nozzle was measured with the help of a turbine flow meter. The transient temperature data with time were recorded at the
rate of 100 samples per seconds. The water flow rate was manipulated through a flow control valve to maintain the
constant flow rate of coolant. The jet Reynolds number at the nozzle exit for a constant flow rate, jet diameter and water
properties can be obtained by following equation (1) |
(1) |
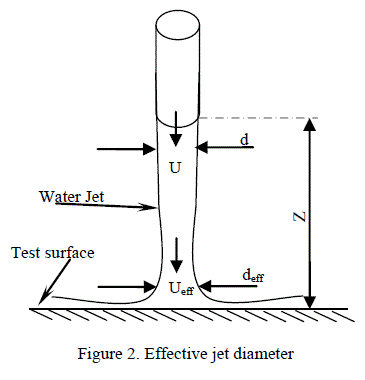 |
Due to the effect of gravity, with the rise in the nozzle exit to the test surface spacing, the effective jet velocity at the test
surface increases. The rise in effective jet velocity, Ueff, near the test surface results in the contraction of the jet diameter.
The effective jet diameter is the diameter of impinging jet at the test surface as shown in Figure 2. The effective jet velocity
at the stagnation point on the test surface can be obtained by using the Equation (2). Whereas, the effective jet diameter
near the test surface can be determined by the Equation (3). |
(2) & (3) |
The uncertainty in each of the measurement is shown in Table-1. The uncertainties in the radial position of thermocouples
were 0.1mm, since, the thermocouple diameter was 0.25 mm, the uncertainty in the thermocouple position became 0.25
mm. |
A number of experiments were performed for nozzle exit to surface spacing, z/d = 4-16, at a constant jet Reynolds number
of 24000. The operating ranges of experimental parameters have been shown in the Table -2. |
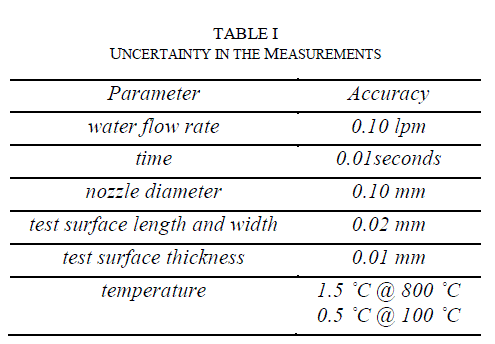 |
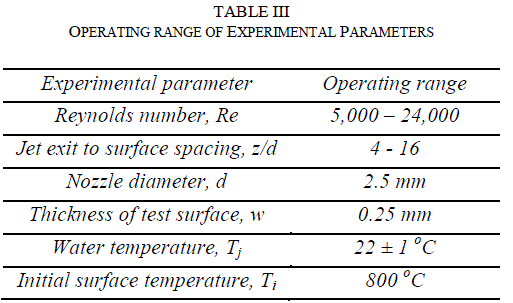 |
RESULT AND DISCUSSION |
Initially, with the recorded time varying surface temperature data the cooling curves for the hot test surface are obtained for
different nozzle exit to test surface spacing. The cooling curves for jet Reynolds number of 24000 and nozzle exit to
surface spacing in a range of z/d = 4-16 are shown in the Figure 3. It has been observed that the change in nozzle exit to
surface spacing does not affect the surface cooling curves significantly. The hot surface takes approximately 4.6 seconds to
obtain the 100 °C temperature from its initial surface temperature of 800°C at z/d =4. Whereas, at other investigated
nozzle exit to surface spacing the corresponding drop in surface temperature is obtained within 4.45 seconds. This variation
in the cooling time is within 3 % of cooling time at z/d = 4. |
It is also observed with Figure 3 that the surface cooling at higher nozzle exit to surface spacing is quicker particularly for
the higher range of surface temperature. At z/d = 8-12 the surface takes 500 °C within 1 seconds from its initial surface
temperature of 800 °C. Whereas, the corresponding drop in surface temperature is obtained in approximately 1.15 seconds. |
This result also reflects that at z/d=4 the cooling is delayed by 15 % as compare to higher nozzle exit to surface spacing
particularly for higher surface temperature.
This diverse behaviour of surface cooling for different nozzle exit to surface spacing is inline to the other reported results
of Agrawal et al. [1, 2] and Stevens and Webb [8]. These investigators has also reported that the surface heat transfer
performance with jet impingement cooling is not affected significantly by the change in nozzle exit to surface spacing. The
surface heat transfer performance under steady state and transient state varied within 5-10 %.
The present result can be attributed that for a free surface jet impingement configuration i.e. a water jet surrounded by air,
does not have tendency of surrounding air entrainment. Thus the characteristics and structure of a free surface jet does not
deformed before reaching to the target surface. Since, other operating parameters pertaining to the jet and the test surface
remains invariable, therefore, surface cooling is not affected significantly by change in nozzle exit to surface spacing alone.
The minor rise in surface cooling at higher nozzle exit to surface spacing, i.e. z/d 8-16 may be due to rise in effective jet
velocity, Ueff, at the test surface. The jet velocity at the hot test surface increases with the rise in nozzle distance away from
the test surface due to gravity effect (Eq. 3). It has also been reported in literature that with the rise in jet velocity heat
transfer performance of the cooling surface increases [3]. Perhaps this is the reason for enhanced surface cooling at higher
z/d. |
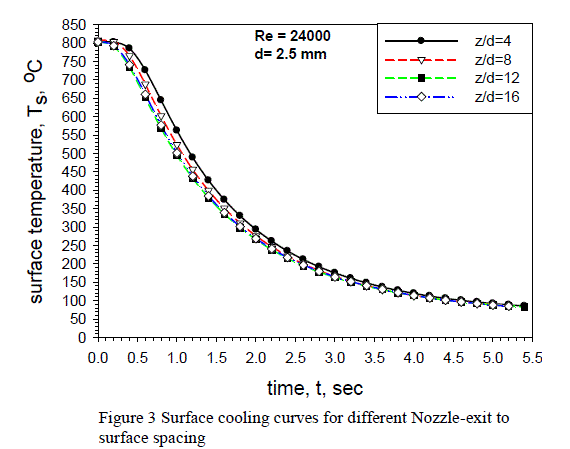 |
CONCLUSION |
The surface cooling of a hot stainless steel surface is experimentally investigated for the stagnation point. At jet Reynolds
number of 24000 and for 800 °C initial surface temperature it is observed that for larger drop in surface temperature, the
cooling time is not affected by the change in nozzle exit to surface spacing. However, for lesser surface temperature drop
particularly at higher surface temperature, surface cooling time with nozzle exit to surface spacing is approximately 15 %
lower. |
References |
- C. Agrawal, R. Kumar, A. Gupta, B. Chatterjee, Rewetting and maximum surface heat flux during quenching of hot surface by round water jet impingement, International Journal of Heat and Mass Transfer 55 (2012) 4772-4782.
- C. Agrawal, R. Kumar, A. Gupta, B. Chatterjee, Effect of jet diameter on the rewetting of hot horizontal surfaces during quenching, Experimental Thermal and Fluid Science, 44 (2012) 25-37.
- A.K. Mozumder, M. Monde, P.L. Woodfield, M.A. Islam, Maximum heat flux in relation to quenching of a high temperature surface with liquid jet impingement, International Journal of Heat and Mass Transfer 49 (2006) 2877âÃâ¬Ãâ2888.
- M.A. Ruch, J.P. Holman, Boiling heat transfer to a Freon-113 jet impinging upward onto a flat heated surface, International Journal of Heat and Mass Transfer 18 (1975) 51-60.
- J. Womac, S. Ramadhyani, F.P. Incropera, Correlating equations for impingement cooling of small heat sources with single circular liquid jets,ASME Journal of Heat Transfer 115 (1993) 106-115.
- H. Fujimoto, N. Hatta, R. Viskanta, Numerical simulation of convective heat transfer to a radial free surface jet impingement on a hot solid, Heat and Mass Transfer 35 (1999) 266 âÃâ¬Ãâ 272.
- C.F. Ma, Y.H. Zhao, Analytical study on impingement heat transfer with single phase free surface circular liquid jets, Journal of Thermal Science 5 (1996) 271 -277
- J. Stevens, B.W. Webb, Local heat transfer coefficients under an axisymmetric single- phase liquid jet, ASME Journal of Heat Transfer 113 (1991) 71- 78.
|