For the effective applications of the welded materials they do not melt or recast. So there is an emerging process which improvises the product quality which is nothing Friction Stir Welding process. During the FSW process, the non consumable tool rotates to plunge and travels along the weld line to produce a high quality of joint. FSW process eliminates the fusion welding problems such as crack, porosity and solidification shrinkage. The aim of the present work is to evaluate the microstructure and mechanical properties of friction stir welded AA6061 cast and wrought aluminium alloy joint. In FSW, the process parameters such as welding speed of 50 mm/min, rotational speed of 800 rpm and axial force of 8 kN was used to make the joint. Two samples were welded by keeping one sample of wrought alloy as an advancing side and cast alloy in retreating side and another sample of weld is produced by keeping the plate alternatively on both sides. The welded samples were characterized by using metallurgical microscopy and universal tensile testing machine. The changes in microstructures, micro hardness and tensile properties were discussed.
Keywords |
Friction stir welding, Microstructure, Mechanical properties. |
INTRODUCTION |
The friction stir welding (FSW) represents, actually, a new welding technology in the high performance aerospace and
automotive application [1]. When compared to traditional welding techniques, FSW strongly reduces the presence of
distortions and residual stresses [2–4]. |
In the friction welding process, joining is done with the help of frictional heat generated at the weld surfaces of the two
sheets to be joined with the specially designed rotating tool, which travels down the length of the contacting plates. This
produces a highly plastically deformed zone through the associated stirring action. From a joining point of view, the
deformation can be described as forging for the tool pressure and advancing and an extrusion along the pin due to its
rotation [1]. The localized thermo-mechanical affected zone is produced by frictional heat between the tool shoulder and the
plate top surface, as well as by plastic deformation of the material in contact with the tool [5]. |
The FSW process is a solid state joining process and therefore a solidification structure is absent in the weld. The
problems related to the presence of brittle inter-dendrites and eutectic phases are eliminated [6]. By developing such
technology, one of the most important fact is represented by the possibility of different aluminium alloy joints[7]. |
Many papers are present in the literature regarding this field. Some authors have demonstrated that the microstructure of
the weld nugget of strongly dissimilar aluminium alloys is mainly fixed at the retreating side of the material [8]. Murr et al.
[9] showed the properties of dissimilar cast aluminium alloys by FSW. Also the corrosion susceptibility of dissimilar
aluminium alloy joint was successfully studied [10]. |
The micro structural evolution of dissimilar welds as a function of processing parameters has been widely studied in
[11], showing the behaviour of AA6061–AA2024 materials. While extensive studies have been published on dissimilar
FSW joints, only very few papers exist regarding the fatigue properties of such kind of weld. Especially with reference to
the effect of welding parameters. |
In this present study, dissimilar formed Al alloys were joined by friction stir welding method with various welding
conditions. The both side of the stir zone divided into the retreating side and the advancing side from the relation between
the tool rotation direction and plate travel direction as shown in Fig. 1. The objective of present research is to evaluate the
microstructure andmechanical properties with the fixed location of each material, rotational speed and welding speed. |
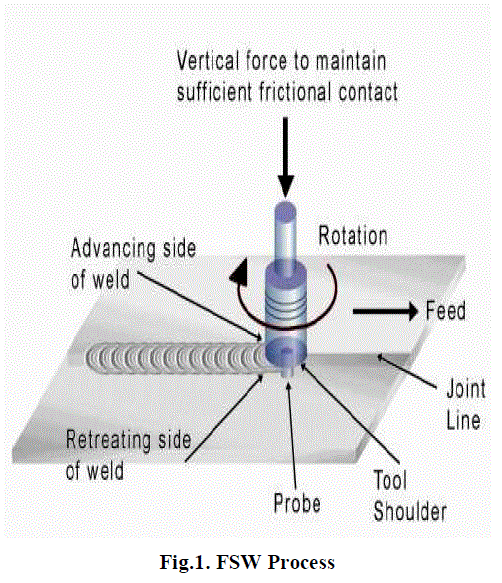 |
EXPERIMENTAL PROCEDURE |
The materials used in this study were 6061T-6 cast and wrought aluminium alloy which size is 100 mm in length, 50 mm
in width and 6 mm in thickness. The chemical compositions are listed in Table 1. |
FSW has many welding parameters, such as fixed location of materials, tool (including shoulder and probe) materials,
tool rotation speed, welding speed and the angle of the tool. In this study, only fixed location of material was changed and
other parameters were fixed at 800 rpm of the tool rotational speed, 50 mm/min of the welding speed and axial force of 8
kN. Tool was made of high carbon high chromium steel with shoulder diameter 18 mm, pin diameter 6 mm and hexagonal
pin length 5.8 mm. The welding tool was rotated in the clockwise direction and specimens, which were tightly fixed at the
backing plate, were travelled. |
The Vickers hardness value of the weld zone was measured on a cross-section and perpendicular to the welding direction
using a Vickers indenter with a 100 gf load for 10 s. The tensile test was carried out at room temperature using an Instrontype
testing machine withcross-head speed of 1.67 x 10-2 mm/s. To determine the tensile strength of the stir zone, tensile
test specimens were sectioned in the transverse direction to the weld line with an electrical discharge machine (EDM). |
Micro structural changes from the weld zone to the unaffected base metal were examined with optical microscopy (OM).
Because each material showed the different etching response to the Keller etchant, the microstructure of the weld zone was
easily distinguished 6061-T6 cast and wrought aluminium alloy. |
RESULTS AND DISCUSSION |
The dissimilar formed 6061-T6 cast and wrought aluminium alloys were successfully joined by the FSWand showed no
porosity and defects in both weld top and rear surfaces regardless of the welding conditions. |
Fig. 2 illustrates the images of friction stir weld plates with various welding conditions. From the different etching
response of each material, 6061-T6 wrought Al alloys appeared darker colored than 6061-T6 cast Al alloys in the stir zone.
In case cast Al alloys were fixed at the retreating side, more light colored regions that were estimated as that of 6061-T6
cast Al alloys occupied the large fraction in the stir zone. However, when wrought Al alloys were fixed at the retreating
side, the microstructure of the stir zone was mainly composed of that of 6061-T6 wrought Al alloys. Therefore, the
microstructure of the stir zone mainly depended on the materials fixed at the retreating side and some of the advancing sided
material. |
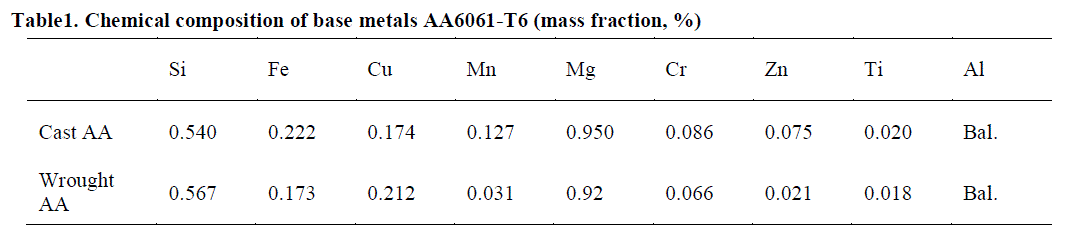 |
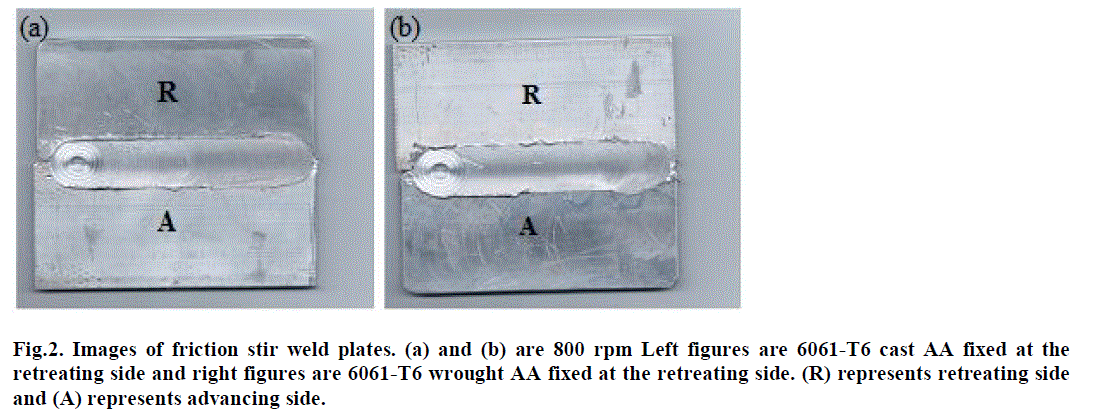 |
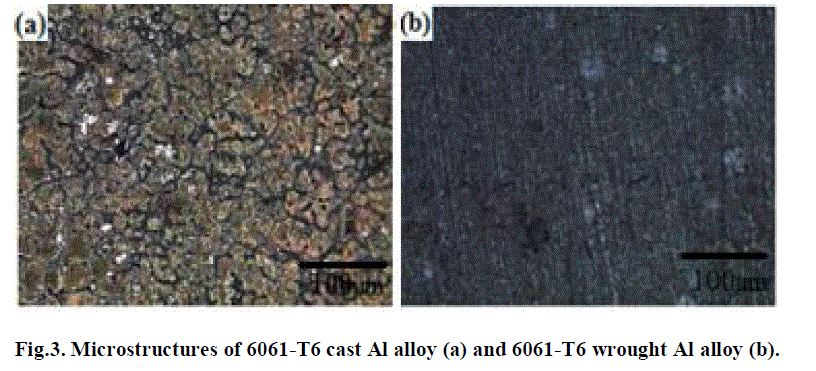 |
The onion ring patterns were obviously observed in part of the stir zone and characterized by the stacked structure of
each material. The area of the stir zone showed almost the same according to the fixed location of each material. However,
the area of the stir zone slightly decreased as increasing rotational speed due to the different the cooling rate.
Fig. 3 shows the microstructures of the base metals. The dendrite microstructure of the 6061-T6 cast Al alloy (a) was
composed of primary α phase and Al–Si eutectic structure. The primary α phase occupied much more volume fraction than
Al–Si eutectic structure because 6061-T6 cast Al alloy included less Si contents than that of Al–Si eutectic point
composition. |
Fig. 4 shows the microstructures of the weld zone in case 6061-T6 cast Al alloy was fixed at the retreating side. The
advancing side of the stir zone (a) showed the fine and recrystallized grain structure of 6061-T6 wrought Al alloys. Its grain
size was much smaller than that of the 6061-T6 Al alloy base metal. Onion ring patterns (b) were continuously observed in
the retreatingside of the stir zone and randomly observed in the advancing side of the stir zone.Onion ring patterns were
composed of the lamellar like structure of stacked 6061-T6 cast Al and 6061-T6 wrought Al alloy in turn and shows the
same width respectively. The upper region of the stir zone (c) had a slightly elongated and recrystallized 6061-T6 wrought
Al alloys and thinly scattered Si particles. The exact central region (d) of the stir zone and other regions where the onion
ring patterns was not observed showed the homogeneously dispersed Si particles comparing that of 6061-T6 cast Al base
metal which the eutectic Si particles are partially distributed. |
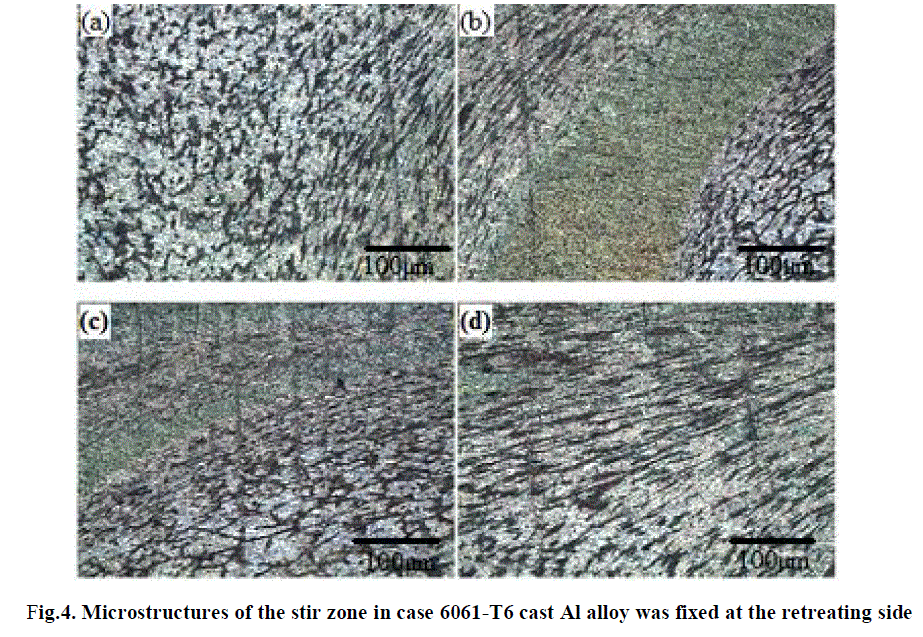 |
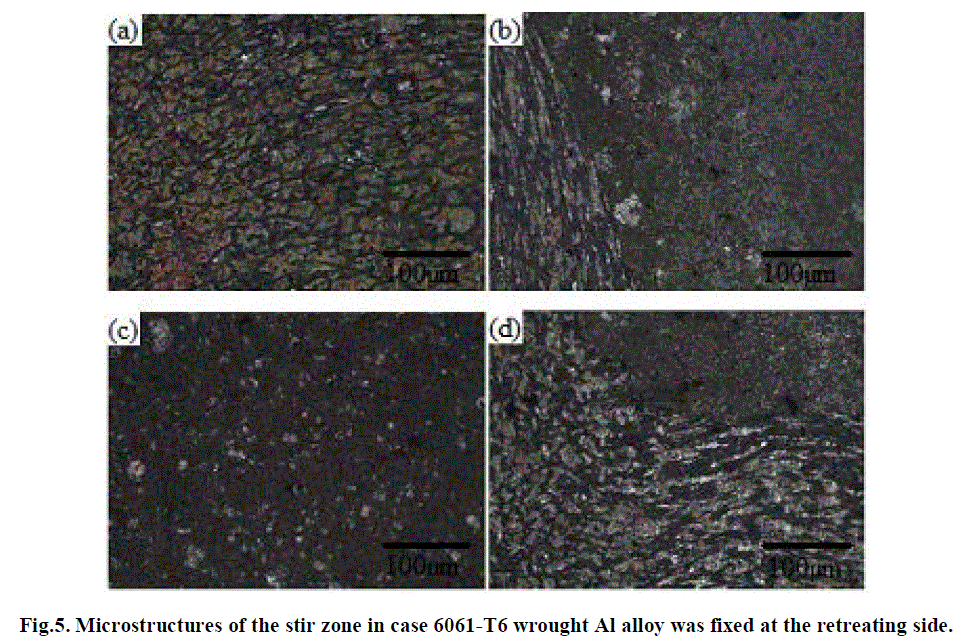 |
Fig. 5 shows the microstructure of the weld zone when 6061-T6 wrought Al alloy was fixed in the retreating side.
The transition region of the advancing side (a) had a microstructure relate to 6061-T6 cast Al alloy and the dispersed
Si particles aligned through the tool rotation direction. Lamellar-like onion ring patterns (b) were also observed in
the stir zone. But the width of each layer showed some difference compared to that of Fig. 4(b). |
The width of 6061-T6 wrought Al alloys layer is wider than that of 6061-T6 cast Al alloy. The region marked (c)
which was dominant structure of the stir zone showed fine and equiaxed grain structure of 6061-T6 wrought Al
alloy and no scars of 6061-T6 cast Al alloy. The center region of the stir zone (d) showed swirl and vortex-like
patterns of each material, microscopically recrystallized 6061-T6 wrought Al alloys and thinly distributed Si
particles. |
Fig. 6 shows the cross-sectional hardness profile near the weld zone according to the fixed location of materials.
Hardness of the stir zone was lower than that of 6061-T6 wrought Al alloy, but higher than that of 6061-T6 castAl
alloy. Some previous report explained that the softening of the stir zone in case of precipitate hardened Al alloy like
6061-T6 wrought Al alloys mainly due to the precipitates behavior during the welding thermal cycle [12,13]. The
improved hardness of the stir zone in case of 6061-T6 cast Al alloys was caused by homogeneously distributed Si
particles [14]. The hardness of the stir zone showed higher value in case 6061-T6 wrought Al alloys were fixed at
the retreating side. This result can be explained by the dominant microstructure of the stir zone. |
Fig. 7 shows the transverse tensile strengths with each condition. The strengths of the stir zone in case 6061-T6
cast Al alloy was fixed at retreating side, showed 188MPa for ultimate tensile strength (UTS) and 112MPa for yield
strength (YS). The strengths of weld zone, in case 6061-T6 wrought Al alloy was fixed at retreating side, showed
206 MPa for UTS and 127MPa for YS. The higher strength of the weld zone was acquired when 6061-T6 wrought
Al alloy is fixed at the retreating side. |
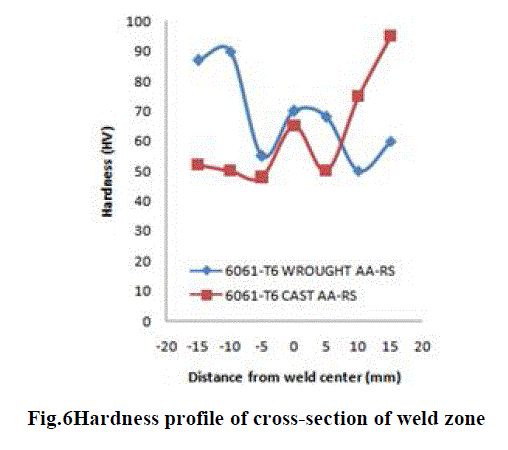 |
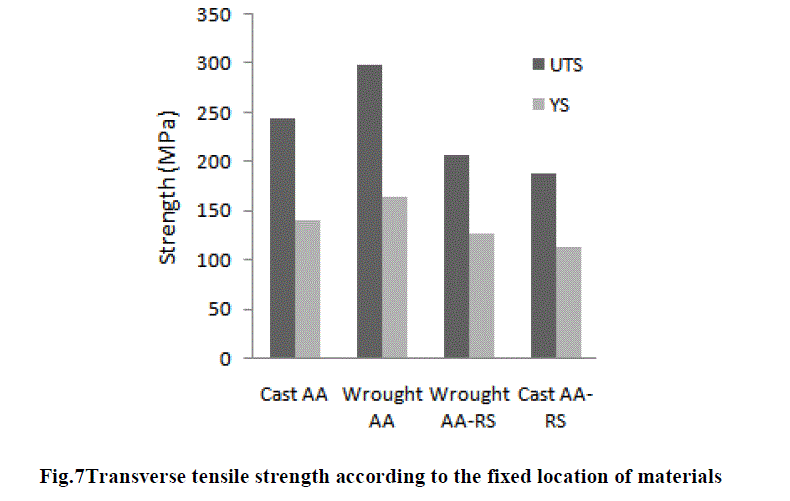 |
CONCLUSION |
1. Defect free dissimilar 6061-T6 cast and wrought aluminium alloy joint is obtained in the narrow range of welding
conditions. |
2. The microstructure of the stir zone was mainly depends on the retreating side material. |
3. The hardness and tensile properties of both the stir zone shows higher value when 6061-T6 wrought Al alloys
were fixed at the retreating side. This result relate to the complex microstructure of the stir zone. |
References |
- Mishra RS, Ma ZY. Friction stir welding and processing. Mater SciEng 2005;R50:1âÃâ¬Ãâ78.
- Bussu G, Irving PE. The role of residual stress and heat affected zone properties on fatigue crack propagation in friction stir welded 2024âÃâ¬ÃâT351 aluminium joints. Int J Fatigue 2003;25:77âÃâ¬Ãâ88.
- John R, Jata KV, Sadananda K. Residual stress effects on near threshold fatigue crack growth in friction stir welded aerospace alloys. Int J Fatigue 2003;25: 939âÃâ¬Ãâ948.
- Jata KV, Sankaran KK, Ruschau J. Friction-stir welding effects on microstructure and fatigue of aluminum alloy 7050âÃâ¬ÃâT7451.Metall Mater Trans 2000;31A:2181âÃâ¬Ãâ2192.
- Guerra M, Schmidt C, McClure JC, Murr LE, Nunes AC. Flow patterns during friction stir welding. Mater Charact 2003;49:95âÃâ¬Ãâ101.
- Rhodes CG, Mahoney MW, Bingel WH. Effects of friction stir welding on microstructure of 7075 aluminium. Scripta Mater 1997;36:69âÃâ¬Ãâ75.
- Cavaliere P, Cerri E, Squillace A. Mechanical response of 2024âÃâ¬Ãâ7075 aluminium alloys joined by friction stir welding. J Mater Sci 2005; 40:3669âÃâ¬Ãâ3676.
- Lee WB, Yeon YM, Jung SB. The mechanical properties related to the dominant microstructure in the weld zone of dissimilar formed Al alloy joints by friction stir welding. J Mater Sci 2003;38:4183âÃâ¬Ãâ4191.
- Murr LE, Rodriguez NA, Almanza E, Alvarez CJ. Study of friction stir welded A319 and A413 casting alloys. J Mater Sci 2005;40:4307âÃâ¬Ãâ4312.
- BalaSrinivasan P, Dietzel W, Zettler R, Dos Santos JF, Sivasan W. Stress corrosion cracking susceptibility of friction stir welded AA7075âÃâ¬ÃâAA6056 dissimilar joint. Mater SciEng 2005;A392:292âÃâ¬Ãâ300.
- Ouyang JH, Kovacevic R. Material flow and microstructure in the friction stir butt welds of the same and dissimilar aluminium alloys. J Mater Eng Perform 2002;11:51âÃâ¬Ãâ63.
- Sato YS, Kokawa H, Enomoto M, Jorgan S. Microstructural Evolution of 6063 Aluminum during Friction-Stir Welding.Metall Mater Trans A 1999;30:2429.
- Murr LE, Liu G, McClure JC.A TEM study of precipitation and related microstructures in friction-stir-welded 6061 aluminium. J Mater Sci 1998;33: 1243.
- Lee WB, Yeon YM, Jung SB. The joint properties of dissimilar formed Al alloys by friction stir welding according to the fixed location of materials. ScriptaMaterialia (2003);49: 423âÃâ¬Ãâ428.
|