Keywords
|
Direct torque control (DTC), Induction motor (IM), sensor count reduction, single current sensor. |
INTRODUCTION
|
Direct torque control (DTC) of induction motors has gained popularity in industrial applications mainly due to its simple control structure from its first introduction in 1986. An electric motor drive controlled with the DTC technique exhibits performance similar to a field oriented drive despite a simpler structure. In fact, a DTC scheme achieves the closed-loop control of the motor stator flux and the Electromagnetic torque without using any current loop or shaft sensor. Many researchers are interested in this control technique because of its wide area applications used with various ac machine types as induction motor, PMSM, PM Brushless, and reluctance motor. |
The DTC scheme requires information about the stator currents and the dc -link voltage, which is used with the inverter, switches states, to estimate the values of stator flux and electromagnetic torque. The current feedback for the closed -loop control is usually obtained by sensing instantaneous phase currents by current sensors. In general, galvanically isolated current sensors such as Hall Effect sensors and current transducers are widely used in many applications. They are typically used on, at least, two outputs of the power inverter to provide current feedback signals. Such a kind of sensors performs well, but brings disadvantages to the overall drive system in terms of cost, Encumbrance and somehow nonlinearity. Recently, single current sensor operation has been proposed to reconstruct phase currents from the DC link current sensor. In this way, various approaches have been proposed in the literature. Some methods adjust the pulse -width modulation (PWM) signals to ensure that two-phase currents can be sampled in each control period. Other strategies introduce modifications of the modulation algorithm in order to guarantee the reliability of the measurements from the dc - link current sensors under all the operating conditions. Other interesting approaches are based on the estimation of the motor phase currents using prediction-correction algorithms, thus introducing additional computational burden to the drive system. Only a few papers deal with the DTC technique for induction motor and PMSM. The algorithm used in these works operates in two stages. First, it predicts the stator currents from a model of the motor and then adjusts the prediction on the basis of the sensed dc -link current. This algorithm requires an additional computation burden and the knowledge of the stator transient inductance. In this paper, we propose a low-cost single shunt current sensor induction motor (IM) DTC. The stator flux vector and the electromagnetic torque are directly calculated from the voltage and the current derived from a single dc-link voltage sensor (simple voltage divider) and a single dc -link current sensor (simple shunt resistor). The phase currents are estimated by two dc-link current measurement processes. This algorithm does not require additional computation burden or other motor parameter knowledge. |
BLOCK DIAGRAM
|
The block diagram of Low -Cost Direct Torque Control Algorithm for Induction Motor without AC Phase Current Sensors is shown in Fig. 1 |
In Fig.1 AC supply is the input supplied to the rectifier circuit. The rectifier circuit convert the AC supply to the DC supply and given to the filter circuit which filter the pulsating DC supply in to the smooth supply and supply the output to the inverter circuit. The inverter circuit consists of many switches it is drive by the driver circuit. The driver circuit has two functions one is to isolation and another for amplification. It can be used to amplify the 5V pulses to 12V for using transistor technology and provided isolation by using opto coupler. The pulse generator produces the pulses for the transistor by using PIC microcontroller. The PIC microcontroller produces a switching signal. The output of inverter is AC which is used to drive the Induction Motors. A low-cost single shunt current sensor induction motor (IM) DTC. The stator flux vector and the electromagnetic torque are directly calculated from the voltage and the current derived from a single dc -link voltage sensor (simple voltage divider) and a single dc -link current sensor (simple shunt resistor). The phase currents are estimated by two dc-link current measurement processes. This algorithm does not require additional computation burden or other motor parameter knowledge. |
BASIC DTC OPERATION
|
DTC uses a simple switching table to determine the most opportune inverter state to attain a desired output torque. By means of current and voltage measurements, it is possible to compute approximately the instantaneou s stator flux and output motor torque. The control algorithm based on flux and torque hysteresis controllers determines the voltage required to drive the flux and torque to the desired values within a fixed time period. The fundamental functional blocks used to implement the DTC scheme are represented in Fig.2. |
The stator flux vector –•s and the torque produced by the motor, •em , can be estimated using (1) and (2) respectively. |
(1) |
(2) |
These equations only require the knowledge of the previously applied voltage vector Vs, measured stator current Is, stator resistance Rs, and the motor poles number p. Once the electromagnetic torque and stator flux magnitude are estimated, a hysteresis control is done and the voltage vectors to be applied are obtained from a switching table. |
The stator voltage polar components (V s•, V s• ) on perpendicular (•,•) reference frame result from measured dc-link voltage Udc and the switching controls logical states Sa ,Sb, and Sc are given by |
(3) |
and stator current components (Ia, Ib) |
(4) |
The stator resistance can be assumed constant. During a switching period, the voltage vector applied to the motor is constant. By integrating the back electromotive force (EMF), the stator flux can be estimated using (5). |
(5) |
During the switching period, each voltage vector is constant and is then rewritten as |
(6) |
where Ts is the control loop period. The magnitude of the stator flux can be estimated by |
(7) |
We can find the flux vector zone using the stator flux components (φsα, φsβ). By using the flux components, current components and IM number of poles, the electromagnetic torque can be calculated by |
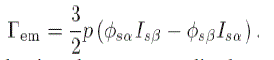 |
A six equally spaced voltage vectors having the same amplitude and two zero voltage vectors are the only switching combinations, which can be chosen for an inverter operation. The selection of a voltage vector is made to preserve the torque and the stator flux inside the hysteresis bands limits. |
SINGLE CURRENT SENSOR DTC SCHEME
|
The basic DTC scheme (see Fig. 2) requires two current sensors at least. The proposed DTC scheme described in this paper uses only one shunt resistor for dc-link current measurement as revealed on Fig. 3. For this purpose, a suitable method to reconstruct the phase currents and voltages is devised with a simple modification of the basic DTC scheme using zone shift strategy. Two modifications of the basic DTC are used for estimating the three-phase currents from a single dc -link current sensor. On the first modification, the control system should be able to generate more voltage vectors. |
This goal can be achieved approximately by applying, at each cycle period, different voltage vectors for prefixed time intervals, leading to a discrete space vector modulation (DSVM) technique. By using this modulation strategy, new voltage vectors can be synthesized with respect to those used in the basic DTC technique. It has been verified that subdividing the cycle period in two equal time intervals leads to a substantial reduction of current sensors without the need for too complex switching tables. |
Using the DSVM technique with two equal time intervals, 12 new voltage vectors can be generated; we use only six active voltage vectors in our proposed DTC scheme as represented in Fig. 4.The red vectors represent the synthesized voltage vectors. |
As the zone shift strategy, one other modification results in improving the DTC by using a new lookup table and adjusting the six stator flux sectors of the conventional DTC. The first sector is taken from 0âÃâæ to 60âÃâæ (see Fig. 4), instead of −30âÃâæ to 30âÃâæ. The new operation table of the modified DTC is presented in Table I. |
SIMULATION RESULT AND DISCUSSION
|
MATLAB/SIMULINK model-based on power system toolbox was developed to examine the proposed control algorithm and the phase-current reconstruction feasibility |
The simulink model is shown in Fig. 5. The simulation of the proposed Low-Cost Direct Torque Control Algorithm for Induction Motor without AC Phase Current Sensors is obtained and the performance curves are plotted. These are illustrated below. The Fig 6 shows the input voltage waveform. Fig 7 shows the Stator current waveform and rotor speed waveform. |
INPUT & OUTPUT WAVEFORMS
|
The input voltage waveform for Low-Cost Direct Torque Control Algorithm for Induction Motor without AC Phase Current Sensors is AC voltage from supply is shown in Fig. 6. |
The Stator current waveform and rotor speed waveform is shown in Fig.7. |
CONCLUSION
|
In this paper, a new low-cost DTC scheme for IM drives has been presented using a single shunt resistor inserted in the dc-link path, for phase current reconstruction. The proposed method reconstructs the stator currents needed to estimate the stator flux magnitude and the electromagnetic motor torque, by means of a simple modification in the basic DTC scheme; 30âÃâæ zone shift strategy is applied. To generate the six active voltage vector needed for dc-link current measure without changing the DTC strategy, a two-intervals discrete space vector modulation technique is used. The effectiveness of the proposed DTC algorithm using a single shunt resistor was verified by computer simulations and experimentally on a three-phase induction motor, rated at 1.1 kW. |
Tables at a glance
|
 |
Table 1 |
|
Figures at a glance
|
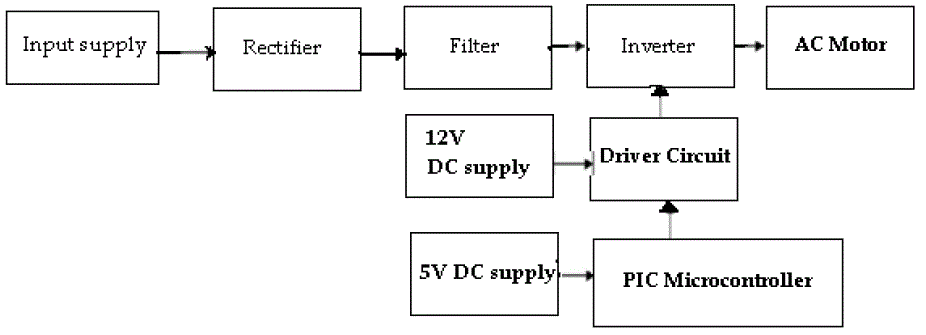 |
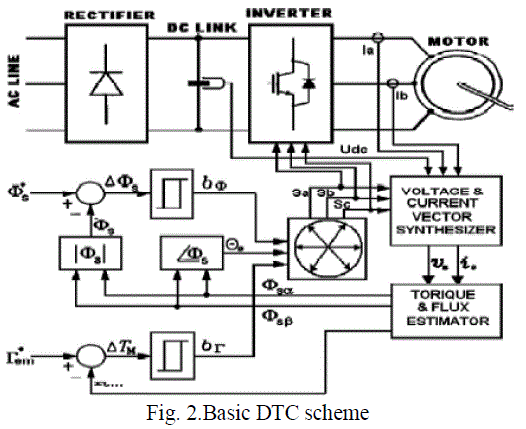 |
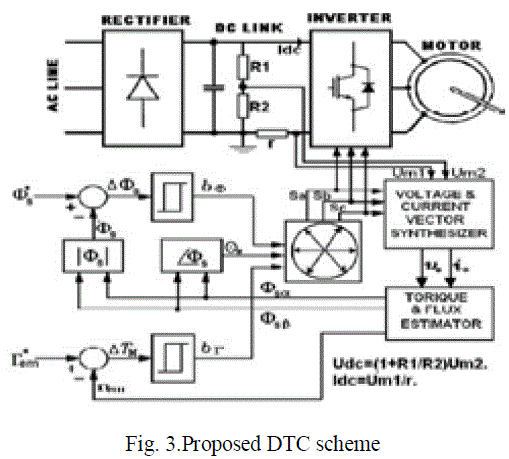 |
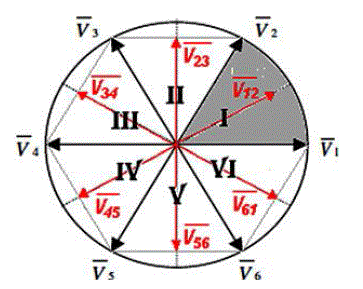 |
Figure 1 |
Figure 2 |
Figure 3 |
Figure 4 |
 |
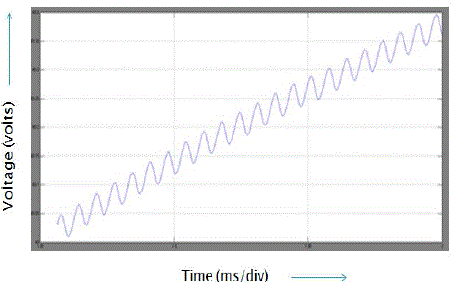 |
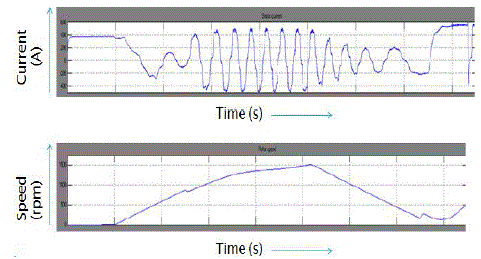 |
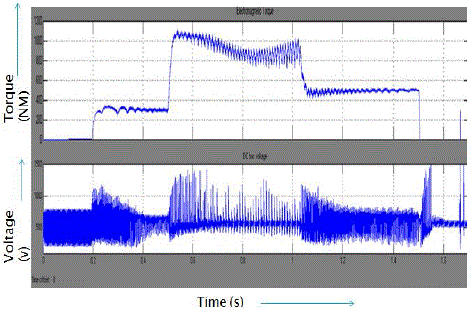 |
Figure 5 |
Figure 6 |
Figure 7 |
Figure 8 |
|
References
|
- Takahashi and T. Noguchi, “A new quick-response and high-efficiency control strategy of an induction motor,” IEEE Trans. Ind. Appl
- S. A. Zaid, O. A. Mahgoub, and K. El-Metwally, “Implementation of a new fast direct torque control algorithm for induction motor drives,” IET Electr. Power Appl.
- C. Patel, R. P. P. A. Day, A. Dey, R. Ramchand, K. K. Gopakumar, and M. P. Kazmierkowski, “Fast direct torque control of an open-end induction motor drive using 12-sided polygonal voltage space vectors,” IEEE Trans. Power Electron.
|