Keywords
|
Conventional engine, LHR, LHR (EEE), Performance and Emissions. |
INTRODUCTION
|
Diesel engines are more efficient and known for its functioning in a vital role of both transportation and industrial sectors. In this connection care to be taken to study the energy conservation phenomenon for effective utilization of fuel available. It is a known factor that, these engines looses a part of its energy developed during combustion and in other thermodynamic processes. To minimize these losses, an attempt is made to study a low heat rejection concept as one of the measures. In LHR engines the effective utilization of generated heat takes place due to insulation of both piston and cylinder [3-5]. At the same time, the problems associated with high combustion temperatures involved with LHR engines are resolved. Heavy exhaust blow-down energy and high NOx emissions are two among them, which leads to decrease in thermal efficiency and inability to achieve legislation levels. |
In this work, an effort is made to minimize the losses by changing inlet cam design mechanism also along with other measures. The inlet cam design has modified for late closing of intake valve, to overcome blow-down losses [1-2]. In addition to this, the extended expansion concept has also incorporated to improve the thermal efficiency. |
The performance of the engine is evaluated mainly based on speed and load of the engine. The evaluation may be the combination of these two or keeping one constant and varying the other. It is to be noted that there is a certain speed, within this speed range of a particular engine at which the fuel injected per cylinder per cycle will be the maximum [6- 7]. At this point of speed maximum pressure is developed and exerted on the piston. For all practical purposes, the torque or engine capacity to do work will also be maximum at this point of speed. Hence the importance of speed in the performance evaluation of the engine is understood and chosen in the present work as the base parameter for evaluating and comparing conventional, LHR and LHR (EEE) engines. It is also includes the comparison of performance parameters such as brake power, brake mean effective pressure, brake thermal efficiency, brake specific fuel consumption and exhaust emissions such as nitric oxide concentration, unburned hydrocarbon, carbon monoxide and exhaust gas temperature with varying speeds of corresponding engines. |
EXPERIMENTAL SETUP
|
An experimental set-up is developed to conduct tests on a four cylinder, four stroke water cooled DI Diesel engine. The test engine is coupled with eddy current dynamometer. In addition to this, fuel measuring burette, air flow measuring U-tube manometer are also fitted to the test engine set up. A provision is also made to mount a piezoelectric pressure transducer flush with the cylinder head surface to measure the cylinder pressure. The experimental set-up layout is shown in Fig. 1.The equipment and instrumentation used in this work is briefly described below. All paragraphs must be indented. All paragraphs must be justified, i.e. both left-justified and right-justified. |
PERFORMANCE PARAMETERS
|
From Fig.2 - Fig.5 has shown the comparison of Brake Power, Brake Mean effective pressure, Brake thermal efficiency and Brake specific fuel consumption for conventional engine, LHR engine and LHR (EEE) engine. |
A. Brake Power |
The Fig.2 is shown the trend of Brake power as a function of speed. The Brake power was found to be higher for LHR (EEE) engine at all speeds than the conventional and LHR Engines. It was observed from the figure that the Brake power for LHR (EEE) engine is higher about 10% to 13.02% than the conventional engine and LHR (EEE) engine is higher about 4.10% to 6.73% than the LHR engine. This may be due to higher work done in LHR (EEE) engine when compared to conventional and LHR engine. |
B. Brake Mean Effective Pressure |
The Fig.3 illustrates the variation of brake mean effective pressure with respect to various speeds for a conventional, LHR and LHR (EEE) engine. In LHR (EEE) engine the BMEP increases of about 4.10 to 6.73% when compared to LHR engine and also it is observed that LHR (EEE) engine the BMEP increases of about 10.0% to 13.02% when compared to conventional engine. As the speed increases the BMEP increases and later decreases due to shorter ignition delay and maximum flame temperature and due to shorter time availability for completion of combustion as speed increases. |
C. Brake Thermal Efficiency |
The Fig.4 has shown the comparison of simulated and experimental brake thermal efficiency under identical conditions. The brake thermal efficiency was found to be higher for LHR (EEE) engine at all speeds than the conventional and LHR engines. This is mainly due to increase in brake power output for the given fuel input than the conventional and LHR engines. In LHR (EEE) engine maximum of 13.04% and 6.73% when compared to conventional and LHR engine. |
D. Brake Specific Fuel Consumption |
The Fig.5 has shown the comparison of simulated and experimental brake specific fuel consumption under identical conditions. It was seen from the graph that the BSFC of the LHR (EEE) engine is found to be decreased from the range of 10% to 13.02% for all speeds than the conventional engine and it is also observed that the LHR (EEE) engine is found to be decreased from the range of 4.10% to 6.73% when compared to LHR Engine. This was mainly due to increase in combustion efficiency so that the fuel consumption can be reduced for the required brake power output. |
EXHAUST EMISSIONS
|
From Fig.6 - Fig.9 has shown the comparison of nitric oxide concentration, unburned hydrocarbon, exhaust gas temperature and carbon monoxide for conventional, LHR and LHR (EEE) engines. |
As very high combustion temperatures are involved with LHR engines resulting in higher NOX formation. The following discussion is focused on NOX emissions along with other emissions. |
A. Nitric Oxide Concentration |
The Fig.6 illustrates the variation of nitric oxide concentration as a function of speed. It was seen from the graph that the percentage increase in the nitric oxide concentration in the case of LHR engine are about 34.42% and 7.07% compared to conventional and LHR (EEE) engine. The trend shows that the LHR engines are producing higher nitric oxide concentration. The increase in nitric oxide concentration in the case of LHR engines is because of the higher cylinder mean peak temperature. The decrease in nitric oxide concentration in the case of LHR (EEE) engine when compared to LHR engine is its ability to reduce temperature during the combustion cycle leads to lower formation rates due to its lower operating temperature because of its lower compression ratio. |
B. Unburned Hydrocarbon |
The Fig.7 has shown the comparison of unburned hydrocarbon as a function of speed. The curve shows that the UBHC emission for a Conventional engine is higher than LHR and LHR (EEE) engine. Operating temperature of LHR and LHR (EEE) engine reduce the quenching effect. |
C. Exhaust Gas Temperature |
The Fig.8 has shown the comparison of exhaust gas as a function of speed. The trend shows that the exhaust gas temperature for conventional engine is lower than LHR and LHR (EEE) engine. LHR engine is reducing the heat transfer to coolant water. Heat energy carried by exhaust gas is higher in the case of LHR engine. |
D. Carbon Monoxide |
The Fig.9 shows the comparison of carbon monoxide as a function of speed. The curve shows that the CO emission for a Conventional engine is higher by 4.8% and 16.6% compared to LHR Extended Expansion Engine and LHR engine. High operating temperature of LHR engine reduces the CO emission. |
CONCLUSION
|
• In the comparison of performance parameters and exhaust emissions for conventional engine, LHR engine and LHR extended expansion engine for all speeds are concluded as below. |
• The Brake power is higher for LHR and LHR Extended Expansion Engine at all speeds than the Conventional. |
• In LHR and LHR Extended Expansion Engine the brake mean effective pressure increases as the speed increases and later decreases when compared with conventional engine due to shorter ignition delay and maximum flame temperature and due to shorter time availability for completion of combustion as speed increases. |
• The brake thermal efficiency is higher for LHR and LHR Extended Expansion Engine at all speeds than the Conventional engine. This is mainly due to increase in brake power output for the given fuel input than the conventional engine. |
• Though the trend of the brake specific fuel consumption results are same for all the stages of the engine it was noted from the experimental results that the brake specific fuel consumption of the LHR and LHR Extended Expansion Engine is decreased for all speeds than the Conventional engine. This was mainly due to increase in combustion efficiency so that the fuel consumption can be reduced for the required brake power output. |
• The simulated values of the performance parameters discussed above are well comparable with the experimental values. Simulation is carried out in ‘C’ programming. |
• It observed that the percentage increase in the nitric oxide concentration in the case of LHR engine compared to Conventional and LHR Extended Expansion Engine. The trend shows that the LHR engines are producing higher nitric oxide concentration. The increase in nitric oxide concentration in the case of LHR engines is because of the higher cylinder mean peak temperature. |
• The decrease in nitric oxide concentration in the case of LHR Extended Expansion Engine when compared to LHR engine is its ability to reduce temperature during the combustion cycle leads to lower formation rates due to its lower operating temperature because of its lower compression ratio. |
• The UBHC emission for a Conventional engine is higher than LHR and LHR Extended Expansion Engine. Operating temperature of LHR and LHR Extended Expansion Engine reduce the quenching effect. |
• The exhaust gas temperature for Conventional engine is lower than LHR and LHR Extended Expansion Engine. LHR and LHR Extended Expansion engine is reducing the heat transfer to coolant water. Heat energy carried by exhaust gas is higher in the case of LHR engine. |
• The CO emission for a Conventional engine is higher by compared to LHR Extended Expansion Engine and LHR engine. High operating temperature of LHR engine reduces the CO emission. |
Figures at a glance
|
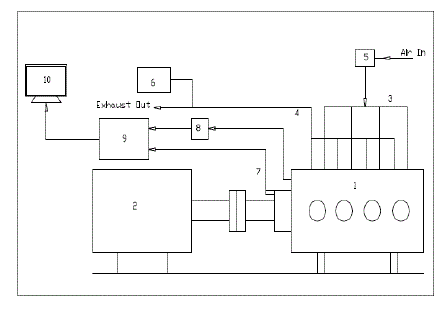 |
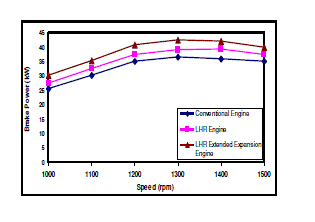 |
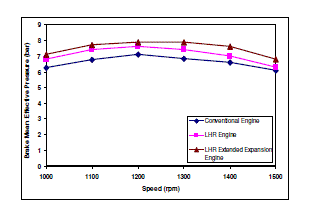 |
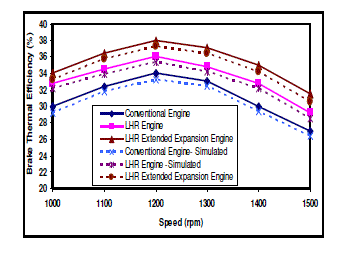 |
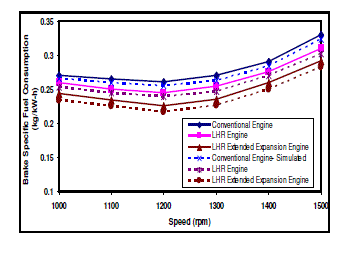 |
Figure 1 |
Figure 2 |
Figure 3 |
Figure 4 |
Figure 5 |
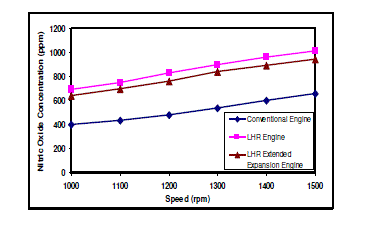 |
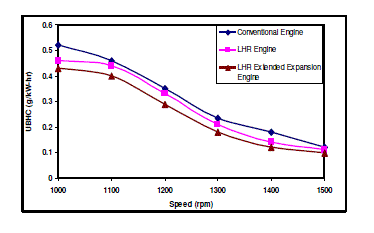 |
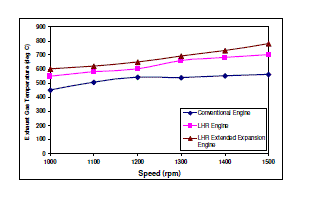 |
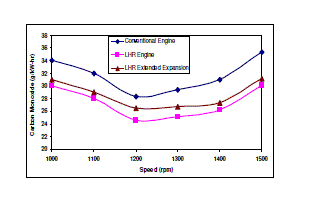 |
Figure 6 |
Figure 7 |
Figure 8 |
Figure 9 |
|
References
|
- Tuttle J. H., “Controlling Engine Load by Means of Late Intake Valve Closing“, SAE Paper No: 800794, 1980.
- Tuttle J. H., “Controlling Engine Load by Means of Early Intake Valve Closing“, SAE Paper No: 820408, 1982.
- Jaichandar S. and Tamilporai P., “Low Heat Rejection Engines – An Overview, SAE Paper No: 2003-01-0405, 2002.
- Lavanya N., “Tamilporai P., Chandrasekaran.S and Jancirani.J, Simulation of Expanded and Exhaust Cam in LHR DI DieselEngine,Proceeding of the 19th National Conference on I.C.Engines and Combustion“, Annamalai University, pp: 547-554, 2005.
- Mohd F.Shabir, S. Authars, S. Ganesan, R. Karthik and S Kumar Madhan, “Low Heat Rejection Engines“ – Review, SAE Paper No: 2010-01-1510, 2010.
- Murthy P.V.K, Murali Krishna M.V.S., SitaramaRajuA,Vara Prasad C.M. and Srinivasulu N.V., “Performance Evaluation of Low HeatRejection Diesel Engine with Pure Diesel“, International Journal of Applied Engineering Research, Dindigul Vol:1, No:3, pp: 428-451, 2010.
- B. Rajendra Prasath, P. Tamilporai and Mohd.F. Shabir, Analysis of Combustion, “Performance and Emission Characteristics of Low HeatRejection Engine using Biodiesel“, International Journal of Thermal Science, Vol:49, pp:2483-2490, 2010.
|