Keywords
|
Modeling, Distillation Column, Controllers, Simulation, LabVIEW. |
INTRODUCTION
|
Separation technology plays an important role in the process industry. Typical separation techniques include distillation, absorption, extraction etc, with distillation being the most frequently used in the chemical process industry. Distillation is the separation of a liquid mixture into its component parts or fractions based on the differences in their volatilities or boiling points. It is widely used in petroleum processing, petrochemical production, natural gas processing, coal tar processing, brewing, liquefied air separation, hydrocarbon solvents production and other industries where product separation of liquid mixtures is required; however its widest application is in the petroleum refineries. In the petroleum refineries the crude oil feedstock is a complex multi-component mixture which has to be separated into groups of compounds within relatively small range of boiling points or fractions. |
The crude oil distillation systems, including distillation columns and their heat recovery systems, is the first stage of processing in a petroleum refinery. It is a highly energy intensive process, consuming fuels at an equivalent of 1% to 2% of the crude oil processed. As the price of energy increases, considerable effort has been made to reduce the energy requirement of the crude oil distillation process. At the same time, increasing concerns about the environment resulted in stricter regulations on the emission of green house gases. Consequently, both economic and environmental issues are important factors in the design of crude oil distillation system. Inside crude oil distillation systems, the distillation columns have strong interactions with the associated heat recovery systems. Compared to the conventional design approach of crude oil distillation systems, the heat-integrated design approach is more likely to and a better solution, from which the minimized energy consumption can be obtained. Less energy consumption also means less gas emissions, which is beneficial for the environment. |
Crude oil distillation is the separation of hydrocarbons in crude oil into fractions based on their boiling points which lie within a specified range . The separation is done in a large tower that is operated at atmospheric pressure. The tower contains a number of trays where hydrocarbon gases and liquids interact. The liquids flow down the tower and the gases up. The fractions that rise highest in the column before condensing are called light fractions, and those that condense on the lowest trays are called heavy fractions. |
MATHEMATICAL MODEL AND ASSUMPTIONS
|
Various processes are involved in the industries and to make them efficient, controlling of these processes has to be done. Various control strategies are employed for the purpose. The plant, control system, actuator, feedback devices, Sensor, in whole, completes a process control system. Application of the control system to a plant is a two sided sword; the whole system can become unstable or inefficient if the control system is not appropriately designed. Since the components of the control system are very expensive, and design of the control system is a time consuming process, it makes real time testing of the application of the control system practically impossible. |
Thus an alternative technique exists in which the equations which govern the plant behaviour is first stated and then transfer equation which relate the plant output and the input is build. The controller is then designed mathematically and then analysed, with various testing tool available such as root locus techniques, Nyquist criterion, Routh Hurwitz method, Bode Plot analysis, for the various performance criterions. One of the most important tasks in the analysis and design of control system is Mathematical Modeling of the systems. The most common methods of the modeling of the linear systems are Transfer Function approach and the State Equation approach. |
The Transfer function approach is valid only for the linear system and the state equation approach is valid for both, i.e., linear as well as non-linear systems. In reality, since all physical systems are non-linear to some extent, in order to use transfer functions and linear state equations the system must first be linearized, or its range of operation be confined to a linear range. Although the analysis and design of linear control system have been well developed, their counter parts for non-linear systems are usually quite complex. Therefore, the control systems engineer often has the task of determining not only how to accurately describe a system mathematically, but more importantly, how to make proper assumptions and approximations, whenever necessary, so that the system may be adequately characterized by a linear mathematical model. |
Equations of vapour liquid equilibrium:
|
To model this system some assumptions have been used, such as, the binary system (two components) has constant relative volatility throughout the column and theoretical (100% efficient) trays. A 100% efficient tray is a tray, in which vapour leaving a tray is in equilibrium with the liquid on the tray. So, the simple vapour liquid equilibrium is used, |
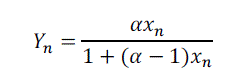 |
Where, |
XN = Liquid composition on the nth tray (mole fraction more volatile component) |
yn = Vapour composition on the nth tray (more fraction more volatile component) |
α = Relative volatility. |
Equations of condenser and reflux drum:
|
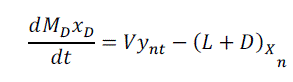 |
Equation of nth Tray:
|
 |
Equation of Top Tray:
|
 |
Equation of feed Tray:
|
 |
Equation of condenser:
|
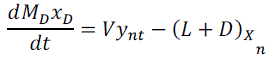 |
Tray efficiency is a strong function of the physical properties of the vapour and liquid streams. It is also affected, to a lesser extent, by the Sow rates and tray layout. In the latter case, only hole diameter, hole area and weir height have a small inSuence on the tray efficiency. The optimum design, which gives the maximum number of equilibrium stages in a column, is often obtained at minimum tray spacing and minimum number of Sow paths that satisfy the hydraulic design criteria. Based on above equations, the mathematical model of the distillation column has been designed in the LabVIEW. Top product (Distillate) composition and the bottom product composition are the output i.e. Controlled variables of the plant system, and the manipulate variables are the Reflux Rate (L) and the Vapour Boilup Rate (V). |
MODEL PARAMETERS USED IN THE CRUDE OIL DISTILLATION MODEL |
MODELING & CONTROL USING LabVIEW
|
In this dissertation modeling has been done in LabVIEW software. LabVIEW has dedicated software which only deals with the Control Design and Simulations of the different plant models and control system. This part of LabVIEW is very similar to the SIMULINK of the MATLAB by MathWorks Inc. SIMULINK contains different toolboxes which deals with simulations of the different system such as Hydraulic Systems, Electrical Systems etc. LabVIEW also has different toolboxes which include PID Toolbox, Fuzzy control Toolbox, and different toolbox which deals with simulations of the plant such as Linear Systems, Non linear System, Simulation Loop etc. This chapter discusses how the different equations depicting the behaviour of the distillation column, and how the controller for distillation column have been designed in the LabVIEW. |
This distillation column model has been divided in six (6) parts. To simulate the model, each has been arranged and interconnected in a specified manner according to the differential equations, as the outputs of many equations serve as the input to some other equations. Different parts/subsystems and their block diagram programming, are as following, |
CONTROL STRATEGIES
|
A controller generates the control signal based on the control strategy employed and the input variable. The input variable to a controller is the error i.e. difference between the There are various types of process control strategies such as: |
• Feed back control |
• Feed forward Controller |
• Cascade Controller |
• Adaptive Controller |
• IMC based Controller |
• Robust Controller etc. |
In all above techniques the Feedback controller is the oldest. The combinations of the above said controllers are also employed to enhance the performance of the overall control system. Like, Feed forward controller, feedback controller, cascade controller are usually employed cumulatively so as to reject disturbance and control the process variable effectively. Feedback controllers have different types, the most frequently used one is, |
ïÃÂö Proportional Integral Derivative controller |
Top product (Distillate) composition and the bottom product composition are the output i.e. Controlled variables of the plant system, and the manipulate variables are the Reflux Rate (L) and the Vapour Boilup Rate (V).Here in the reflux drum side we have two valve opening one for reflux flow and the other for distillate flow these are in a split range controller used in the process where the system acts upon. When we need and higher flow rate in the distillate side the control valve raises at the distillate side and closes at the reflux side. |
RESULT AND DISCUSSION
|
CONCLUSION
|
In this dissertation a mathematical model and a suitable control strategy has been applied. The mathematical model in the present work is based on the molar concentrations of the components in the product streams and according to them a controller has been employed. The present work can be further explored in areas, such as, instead of the molar concentrations, the mass flows can be used to develop a model for the column and hence a controller to make the distillation process energy efficient and effective. More advanced controllers such as robust controller, Fuzzy Controller, and Neural Controller can also be studied for their feasibility to be employed with distillation column dynamics. |
Tables at a glance
|
|
Figures at a glance
|
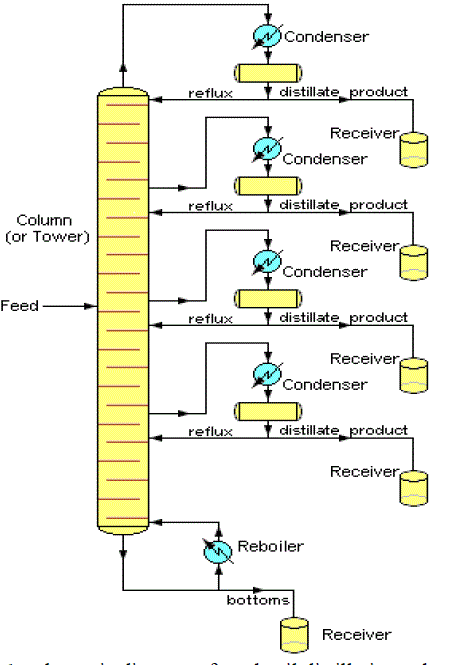 |
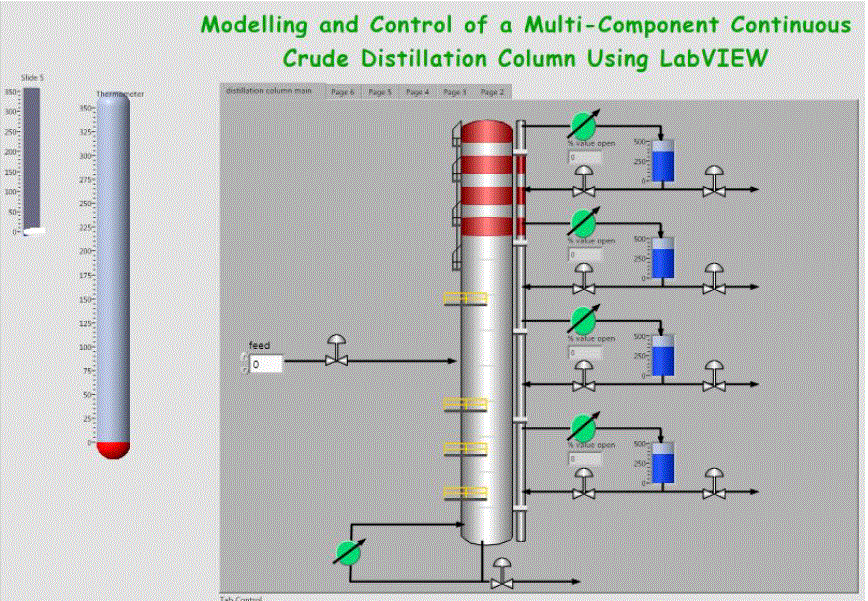 |
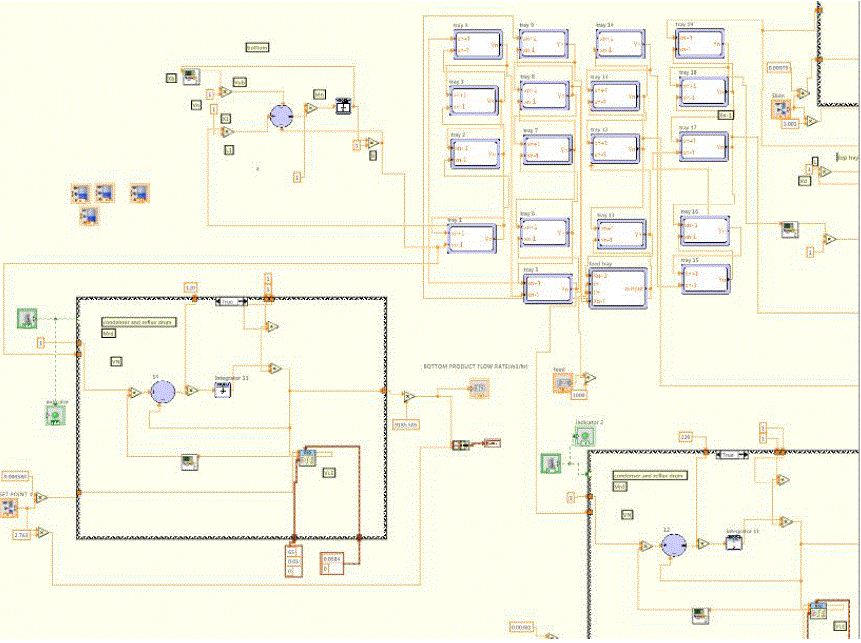 |
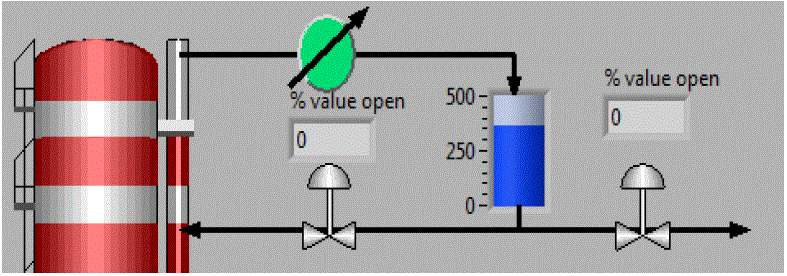 |
Figure 1 |
Figure 2 |
Figure 3 |
Figure 4 |
|
References
|
- AKPA, Jackson Gunorubon and UMUZE, Omonigho Deprive: Simulation of a Multi-component Crude Distillation Column.
- Zalizawati Abdullah , Norashid Aziz, Zainal Ahmad: Nonlinear Modelling Application in Distillation Column
- Jiann – Shiou Yang, “Optimization-Based PI/PID Control for a Binary Distillation Column”, American Control Conf., June, 2005, pp. 3650 –3655.
- Makaremi and B. Labibi,“Control of Distillation Column – A Decentralized Approach”, Proc. of IEEE Int. Conf. on Control Application,Oct. 2006, pp. 711 – 714.
- M. Adel, I. Elamvazuthi and N.H.B.B. Mohd. Hanif, “Monitoring and Controlling System for Binary Distillation Column”, Proc. of IEEEStudent Conf. On Research and Development, Nov. 2009, pp. 453 – 456.
- Raji P. and Binu L.S., “Sliding Mode Control of a Binary Distillation Column”.
|