This paper identifies the synergies between wireless sensor networks (WSNs) and nonintrusive electricalsignal- based motor signature analysis and proposes a scheme of applying WSNs in online and remote energy monitoring and fault diagnostics for industrial motor systems. The main scope is to provide a system overview where the nonintrusive nature of the electrical-signal-based motor signature analysis enables its applications in a WSN architecture. Special considerations in designing nonintrusive motor energy monitoring and fault diagnostic methods in such systems are discussed. This paper also provides detailed analyses to address the real-world challenges in designing and deploying WSNs in practice, including wireless-link-quality dynamics, noise and interference, and environmental impact on communication range and reliability. The overall system feasibility is investigated through a series of laboratory experiments and field tests. First, the concept of a remote and online energy monitoring and fault diagnostic system is demonstrated using a simplified star-type IEEE 802.15.4 compliant WSN in the laboratory. Two well-established nonintrusive motor diagnostic algorithms are intentionally used to prove the feasibility. Next, the challenges of applying the proposed WSN scheme in real industrial environments are analyzed experimentally using field test results.
Keywords |
Energy efficiency, fault diagnostics, IEEE 802.15.4, link-quality indicator (LQI), motor current signature
analysis (MCSA), motor power signature analysis (MPSA), remote monitoring, and wireless sensor networks (WSNs). |
INTRODUCTION |
MOTOR SYSTEMS use nearly 70% of the total electric energy consumed by industry in the U.S. Among industrial motor
systems, three-phase induction motors are dominant because of their simple design, rugged performance, and easy
maintenance. It is estimated that about 40% of the induction motor failures are caused by bearing failures, 38% by stator
winding faults, 10% by rotor faults, and 12% by miscellaneous faults [1], [2]. |
Energy monitoring and fault diagnostics are critical for industrial motor systems to maintain safety, reliability, efficiency,
and uptime. Accurate monitoring and estimation of energy us-age condition of motor systems enable proper actions at
various levels to be taken to improve the overall system efficiency for energy savings. Early detection of motor system
failures through fault diagnostics and prognostics allows appropriate maintenance to be scheduled proactively to prevent
catastrophic motor failures, avoiding expensive economical losses associated with process downtime caused by motor
failures. Due to the increasing global energy crisis and maintenance staff scarcity over the past decades, many energyintensive
industries, such as prime metal, pulp and paper, mining, petroleum refinement, water treatment, etc., have shown
increasing needs for low-cost, easy-to-use, and remote systems for monitoring energy usage and equipment conditions.
Traditionally, energy monitoring and fault detection systems in industrial plants are realized in an offline fashion or in
wired systems formed by communication cables and various types of sensors [3]–[6]. The installation and maintenance of
these cables and sensors are usually much more expensive than the cost of the sensors themselves. |
The advances in wireless communications and highly integrated electronics have enabled the implementation of low cost, low-power, and multifunctional sensors and actuators. The deployment of large numbers of these sensors and
actuators resulted in the development of wireless sensor networks (WSNs) [7]. The collaborative operation of WSNs brings
significant advantages over traditional sensing, including flexibility, high fidelity, self-organization, aggregated intelligence
via parallel processing, low cost, and rapid deployment. These unique fea-tures make WSNs a promising platform for
online and remote implementations of energy monitoring and fault diagnostic sys-tems [9]. However, the realization of
these systems in industrial environment directly depends on energy efficient and reliable communication capabilities of the
deployed WSNs. |
This paper identifies the synergies between the WSNs and nonintrusive electrical-signal-based motor signature analysis
and proposes a scheme of applying WSNs in online and remote energy monitoring and fault diagnostics for industrial motor
systems. The main scope is to provide a system overview where the nonintrusive nature of the electrical-signal-based motor
signature analysis enables its applications in a WSN archi-tecture. Different from most of the existing simulation-based
studies, this research effort is guided by extensive laboratory and field experiments using IEEE 802.15.4 compliant WSN
platforms. This realistically addresses the challenges when applying WSNs in industrial environments, including wirelesslink-
quality dynamics, noise and interference, environmental impact on communication range, and selection of antennas. |
WSNs |
WSNs target primarily the low-cost and ultralow power consumption applications, with data throughput as
secondary considerations. Fuelled by the need to enable inexpensive WSNs for remote monitoring and control of noncritical functions
in the residential, commercial, and industrial applications, standardized low-rate wireless personal area networks (LRWPANs)
have emerged [9]. In 2003, the LR-WPAN standard became the IEEE 802.15.4 standard. |
The IEEE 802.15.4 is intended to address applications wherein existing wireless solutions are too expensive and the
performance of a technology such as Bluetooth is not required. While other wireless network standards aim to achieve long distance, large throughput, and high quality of service level, the IEEE 802.15.4 is designed to provide simple wireless
communications with relatively short range, limited power, relaxed data throughput, low production cost, and small size,
which, however, are sufficient to satisfy the requirements of most remote monitoring system for industrial applications. |
The IEEE 802.15.4 supports two frequency bands, which are a low band at 868/915 MHz and a high band at 2.4 GHz.
The low band defines one channel with a raw data rate of 20 kb/s near 868 MHz and ten channels with a raw data rate of 40
kb/s near 915 MHz. The high band defines 16 channels with a raw data rate of 250 kb/s. This data rate is fairly enough
when multiple machines are monitored, where the processed data (such as the algorithm results, e.g., fault alarms) instead
of real-time continuous data (such as continuous motor raw data samples) are transmitted. For low-data-rate
implementations, the proposed system suggests that the sensor nodes transmit the locally processed algorithm results based
on the application requirements, i.e., in-network intelligent data processing, instead of sending the raw data to the sink node
directly. Thus, only necessary information is transported to the end user, and communication overhead is significantly
reduced. Furthermore, in the WSN implementation of this work, the 2.4-GHz high band is used. |
Although WSNs bring significant advantages over traditional sensing, the majority of sensor radios have been developed
for consumer-grade radio frequency (RF) applications; its op- eration in harsh industrial environments remains to be validated.
In this regards, the performance measurements of IEEE 802.15.4 radios in industrial environments are essential
before these radios are used for critical industrial applications. These measurements also provide valuable and solid
foundations for several sensor network protocols and guide design decisions and tradeoffs for industrial WSN applications
and ongoing efforts, such as the ISA-SP100 [10], which assesses the needs of a new RF standard for industrial use. This
paper provides an insight discussion and a field test study on their performance measurements in Section V. |
ENERGY MONITORING AND FAULT DIAGNOSTICS FOR |
INDUSTRIAL MOTOR SYSTEMS IN A WSN SCHEME |
The advantages of WSNs over traditional sensing make them a promising platform for remote
monitoring systems. Instead of proposing a new motor diagnostic method for a specific motor failure, the main focus of this
paper is to provide a system overview where the nonintrusive nature of the electrical-signal-based motor signature analysis
enables its applications in a WSN architecture. |
A. Integrating Motor Energy Monitoring and Fault Diagnostics Into WSN Scheme |
An overview of the proposed online and remote energy monitoring and fault diagnostic scheme for industrial motor
systems using WSNs is shown in Fig. 1. In industrial plants, electric power for motors is usually provided by individual
motor control centers (MCCs). Typically, motor electrical data, such as voltages and currents, are already available at the
MCC for control or protection purposes. Traditionally, communication cables need to be installed to collect data from the
MCCs or motors and send them to the central supervisory stations (CSSs). These communication cables could be
eliminated by the deployment of WSNs. It is necessary to point out that a typical plant usually has more than one MCC and
CSS. |
In the proposed WSN scheme, the motor terminal electrical data are collected at the MCCs, transmitted through WSNs,
and processed in the CSSs. Using these data, electrical-signal-based motor signature analysis methods, such as motor
current signature analysis (MCSA) and motor power signature analysis (MPSA) [11]–[13], can be used to monitor energy,
efficiency, and health condition of critical motor systems in an online, remote, and nonintrusive manner. An alternative
approach is to process the electrical data locally at the sensor level and transmit the process algorithm results (e.g., fault
alarms) over the WSN to reduce the data communication burden. This is discussed in more details later. In case that, in some applications, other sensor data, such as vibration, temperature, noise, etc., are readily available, such sensor data can
also be transferred to the CSSs through the WSNs. Although this is not the focus of the proposed scheme, these sensor data
can also be used for traditional sensor data analysis, and the results can be integrated with the results of electrical-signalbased
motor signature analysis for improved accuracy. Finally, the energy efficiency conditions and health conditions of the
motor systems are reported from the CSSs, and proper planning and maintenance decisions can be made. |
Due to the limitations of the WSN technology, such as long latency, relaxed data throughput, and limited reliability and
security, the objective of applying WSNs in an industrial environment is not to completely replace the existing wired
communication and control systems. Rather, the objective is to form a wireless and wired coexisting system, wherein the
noncritical tasks such as energy efficiency monitoring, oper-ating cost evaluation, and fault diagnostics are carried out by
the wireless part to reduce the overall cost, while the critical tasks (in terms of time requirement and cost) such as motor
controls and motor protections can still be performed by the wired system for reliability and timing considerations. |
B. Considerations of Energy Monitoring Methods in |
Proposed WSN Scheme |
Over the past decade, government agencies over the world have established regulations to promote energy utilization
efficiency and reduce carbon emissions in various energy-intensive industries. Obviously, to improve plant-level energy
efficiency, accurate monitoring of energy consumption, as well as energy efficiencies at machine level in the plant, is
necessary. |
Among all the energy monitoring functions, motor efficiency estimation is the most important. Over the years, many motor
efficiency estimation methods have been proposed [3]–[6]. A common problem of these methods is that either expensive
speed and/or torque transducers are needed for rotor speed or shaft torque measurements or a highly accurate motor
equivalent circuit needs to be developed from the motor parameters. Generally, these methods are too intrusive and are
often not feasible for in-service motor monitoring. To overcome these problems, the authors in [4] present a complete
survey on motor efficiency estimation methods, specifically considering the advances in nonintrusive speed estimation and
in-service stator resistance estimation techniques. A general approach of developing nonintrusive motor efficiency
estimation methods is also suggested, using only motor terminal electrical data. Following this approach, two nonintrusive
methods are developed for induction motor efficiency estimation using motor voltages and currents [15]. The nonintrusive
characteristic of such methods enables them to be applied in the proposed WSN scheme. |
C. Considerations of Fault Diagnostic Methods in |
Proposed WSN Scheme |
Motor fault diagnostics include the detection of eccentricities and misalignment, bearing faults, stator insulation faults,
rotor faults, winding thermal protection, and other related faults [1], [2], [11], [12]. |
Over the two past decades, an analysis of electrical parameters in an effort to diagnose impending problems with
mechanical elements has gained wide acceptance. To develop advanced methods that can monitor motor failures at an early
stage, advanced modeling and intelligent data processing techniques are commonly used, including motor modeling and
analysis, system identification and optimization, pattern recognition, stochastic and statistical process, and digital signal
processing methods [12]. Many of these methods are based on motor signature analysis, where the fault signatures in the
motor electrical data, such as currents, voltages, and power, are extracted to detect the faults of the motor systems. |
Similarly, electrical-signal-based motor signature analysis can be also applied to fault diagnostics of inverter faults,
including semiconductor switching device faults and capacitor faults [14], as well as mechanical fault of the loads attached
to the motor shafts [13]. The nonintrusive nature of these methods makes them the best candidates for remote motor
monitoring and diagnostic systems in a WSN scheme, where motors, motor controls, data acquisition, and data processing
and reporting often happen at distant physical locations. Faster processor need to be used for data storage and processing.
However, considering today’s cost of memory and processor, this approach is still optimistic. |
In addition to memory and processing limitations, recent experimental studies such as [16] and [17] have shown that, in
real WSN deployments, wireless link quality varies over space and time, deviating to a large extent from the idealized unit
disk graph models used in network simulation tools. Based on these empirical studies and measurements, it is also found
that the coverage area of sensor radios is neither circular nor convex, and packet losses due to fading and obstacles are
common at a wide range of distances and keep varying over time. Although these early studies have made many important
observations for the problems of reliable data transmission in WSNs, the challenges of integrating WSNs with online motor
monitoring and diagnostic systems are yet to be efficiently studied and addressed. Several of these key WSN
communication issues are discussed in more details and experimentally studied in Section V. |
EXPERIMENTAL VALIDATION OF REMOTE ENERGY MONITORING AND FAULT
DIAGNOSTICS IN WSN SCHEME |
The overall system feasibility of the proposed WSN scheme is investigated through a series of laboratory experiments
and field tests. In this section, the concept of a remote and online energy monitoring and fault diagnostic system is
demonstrated using a simple WSN with a star topology in the laboratory. Two well-established nonintrusive methods,
which are a non-intrusive air-gap torque (NAGT) method for motor efficiency estimation and a rotor eccentricity detection
method for mechanical fault diagnostics, are intentionally used as examples in this paper for validation purposes due to
algorithm maturity. |
A. Experimental Setup |
The laboratory experimental setup is shown in Fig. 2. A three-phase induction motor is line connected to a 230-V supply.
The voltages and currents are slightly unbalanced with unbalance factors less than 10% and reflect the actual motor
working condition. The key motor parameters are 7.5 hp, four poles, NEMA-A, 230 V, 18.2 A, 1755 r/min, 1.04-Ω stator
resistance, 0.865 nominal power factor, and 89.5% nominal efficiency. A dc generator connected to resistor banks serves as
dynamometer. The shaft torque is measured by an in-line torque transducer. The speed is measured by an optical encoder. It
uses IEEE 802.15.4 compliant CC2420 radio components. |
The WSN in the proposed scheme enables the motor terminal electrical data to be transmitted to the CSSs. In the
experiments, five-channel motor data are transmitted to CSS over the WSN: two line-to-line voltages νab and νbc, two phase
currents ia and ib, and a measured shaft torque Tsh, which is used to compute the actual motor efficiency for a verification
purpose. The signals of all channels are scaled into 0 to 5 V and sampled with a 12-b analog-to-digital (A/D) converter at 4-
kHz sampling rate. The accuracy of these transmitted waveforms depends on many factors, such as the accuracy and
linearity of the voltage and current transducers, the resolution of A/D conversion, and the reliability of the wireless
communication. |
B. Energy Monitoring—Motor Efficiency Estimation |
During the experimental validation, an NAGT method is used to demonstrate energy monitoring using the proposed WSN scheme, because of its proven accuracy and ease of implementation [15]. The air-gap torque Tag is estimated from the
motor line voltages (νab and νca), phase currents (ia and ib), stator resistance Rs, and the number of poles p |
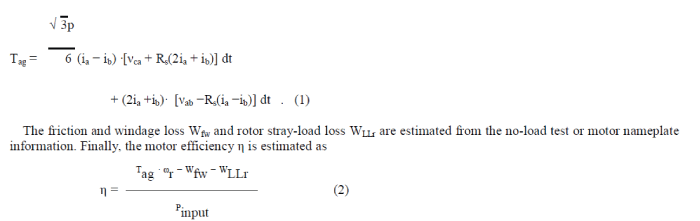 |
where ωr is the rotor speed estimated from the motor current or directly measured, and Pinput is the average instantaneous
input power calculated from the input voltages and currents. The actual motor efficiencies are directly calculated from the
measured speed and shaft torque and are used to verify the accuracy of the estimated motor efficiencies. The details of the
NAGT method are available in [15]. A significant benefit of this method is that the efficiency estimation is completely
based on motor terminal electrical data and motor nameplate information. Such nonintrusive nature enables its application
in the proposed WSN scheme. |
Fig. 3 shows the estimated and measured motor efficiencies under various load conditions. It can be observed that the
remotely estimated motor efficiencies at the CSS agree closely (at ±2% error) with the measured motor efficiencies,
particularly during normal load range (i.e., 40% to 90% of rated load). Moreover, the proposed WSN scheme also gives
relatively accurate efficiency estimates at under loaded and overloaded conditions, which are also useful information for
industrial motor energy management. The accuracy of the estimated Fig. 3. Comparison of estimated and measured motor
efficiencies. Efficiency in the proposed WSN system also agrees well with the ±2% error when the NAGT method is tested
directly with the motors, as reported in [15]. |
C. Fault Diagnostics—Detection of Rotor Eccentricities |
A substantial portion of induction motor faults is rotor ec-centricity related. As one of the simplest and most mature fault
diagnostic methods, a rotor eccentricity detection method is selected to demonstrate motor fault diagnostics using the
proposed WSN scheme [13]. In general, the online detection of rotor eccentricity primarily depends on the monitoring of
fundamental side band harmonics located at fe ± frm, where fe is the fundamental frequency and frm is the rotor rotational
frequency. |
In the experiment, the same motor and WSN setup in Section IV-A is used. The static eccentricity is created by first
machining the bearing housings of the end bell eccentrically and then placing a 0.01-in shim in the end bell to offset the
rotor. The dynamic eccentricity is created by first machining the motor shaft under the bearings eccentrically and then
inserting a 0.01-in offset sleeve under the bearings. A fast Fourier trans-form is applied to a 10-s single-phase stator current
accumulated from multiple records received at the CSS over the WSN. When the motor is running at 1752 r/min (fe ≈ 60
Hz and frm = 29.2 Hz), the current spectrum is shown in Fig. 4, where the frequency component magnitudes are shown in a
log scale. Fig. 4 clearly shows that a significant amount of characteristic sideband harmonics appears in the current spectrum located at fe ± frm. These two current signatures explicitly indicate the existence of a rotor eccentricity fault. |
CONCLUSION AND FUTURE WORK |
The advantages of WSNs over traditional sensing have made them a promising platform for remote monitoring systems.
The motor energy efficiency and health conditions are estimated using only motor terminal electrical data through WSNs in
an online, remote, and nonintrusive manner. The feasibility of the proposed scheme has been demonstrated through a series
of laboratory experiments and field tests. This paper has also addressed the challenges when applying the proposed WSN
scheme in industrial environments, including wireless-link-quality dynamics, noise and interference, and environmental
impact on communication range and reliability. In summary, the following key contributions have been made in this paper. |
1) An online and remote energy monitoring and fault diagnostic system in a WSN scheme has been proposed, and its
feasibility has been demonstrated. The nonintrusive nature of the proposed scheme is well aligned with the current
trend of electrical-signal-based motor fault diagnostics, such as the motor current/power signature analysis
(MCSA/MPSA). |
The spatiotemporal impacts of industrial environments on the proposed WSN scheme have been experimentally
investigated. The empirical measurements have demonstrated that the average LQI values provided by WSN radio
components are closely correlated with PRR and can be used as a reliable metric for wireless-link-quality assessment
during the deployment of the proposed WSN scheme. |
Future work in this area includes sensor fusion of various sensor measurements, a detailed performance analysis of
WSNs in industrial environments, and an investigation of the impact of network-error-control mechanisms and different
heterogeneous resources, such as transmission power, network bandwidth and processing power, on overall system
performance, and optimal placement of these resources in the network. |
Figures at a glance |
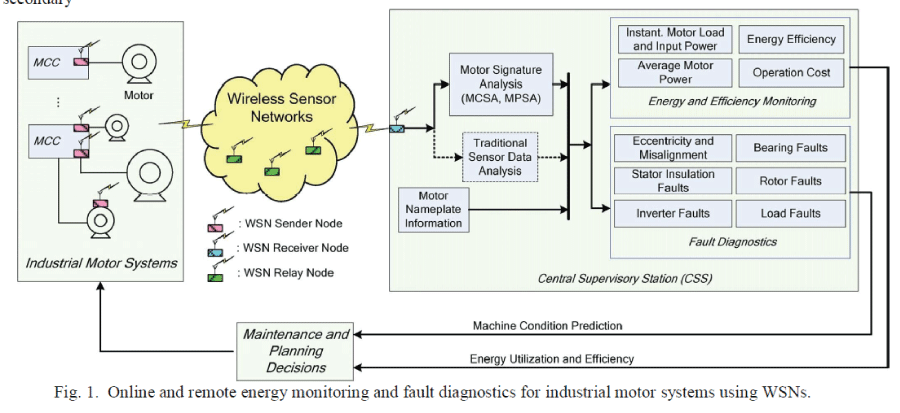 |
Figure 1 |
|
|
References |
- R. N. Bell, D. W. McWilliams, P. O’Donnell, C. Singh, and S. J. Wells, “Report of large motor reliability survey of industrial and commercial installations—Part I,” IEEE Trans. Ind. Appl., vol. IA-21, no. 4, pp. 853– 864, Jul./Aug. 1985.
- R. N. Bell, C. R. Heising, P. O’Donnell, C. Singh, and S. J. Wells, “Report of large motor reliability survey of industrial and commercial installations—Part II,” IEEE Trans. Ind. Appl., vol. IA-21, no. 4, pp. 865– 872, Jul./Aug. 1985.
- IEEE Standard Test Procedure for Polyphase Induction Motors and Gen-erators, IEEE Std. 112-1996, Sep. 1996.
- B. Lu, T. G. Habetler, and R. G. Harley, “A survey of efficiency-estimation methods of in-service induction motors,” IEEE Trans. Ind. Appl., vol.42, no. 4, pp. 924–933, Jul./Aug. 2006.
- A. Wallance, A. Von Jouanne, E. Wiedenbrug, E. Matheson, and J. Douglass, “A laboratory assessment of in-service and nonintrusive motor efficiency testing methods,” Elect. Power Compon. Syst., vol. 29, no. 6, pp. 517–529, Jun. 2001.
- J. Hsu, J. Kueck, M. Olszewski, D. Casada, P. Otaduy, and L. Tolbert, “Comparison of induction motor field efficiency estimation methods,” IEEE Trans. Ind. Appl., vol. 34, no. 1, pp. 117–125, Jan./Feb. 1998.
- I. F. Akyildiz, W. Su, Y. Sankarasubramaniam, and E. Cayirci, “Wireless sensor networks: A survey,” Comput. Netw., vol. 38, no. 4, pp. 393–422, Jan. 2002.
|