In this paper, an application of superconducting fault current limiter (SFCL) is proposed to limit the fault current that occurs in power system, SFCL is a device that uses superconductors to instantaneously limit or reduce unanticipated electrical surges that may occur on utility distribution and transmission networks. At the time of fault occurs in the line, a large surge of power can be sent through the grid resulting in a fault. These faults can result in damage to expensive grid connected devices. SFCL's eliminate or greatly reduce the financial burden on the utilities by reducing the wear on circuit breakers and protecting other expensive equipment. Utilities can reduce or eliminate the cost of circuit breakers and fuses by installing SFCL. As for a dispersed energy source, 10 MVA wind farm with three units connected and the total was simulated. Three phase faults have been simulated at different locations in smart grid and the effect of the SFCL and its location on the wind farm fault current was evaluated. Three wind farms were considered and their performance is also evaluated. Consequently, the optimum arrangement of the SFCL location in Smart Grid with renewable resources has been proposed and its remarkable performance has been suggested.
Keywords |
Fault current, microgrid, smartgrid, superconducting fault current limiter (SFCL), wind farm. |
I. INTRODUCTION |
Smart grid is a term used for future power grid whichintegrates the modern communication technology andrenewable
energy resources for the 21 st century powergrid in order to supply electric power which is cleaner,reliable, effervescent
and responsive than conventionalpower systems. Smart grid is based on the principle ofdecentralization of the power grid
network into smallergrids (microgrids) having distributed generation sources(DO) connected with them, One critical
problem due tothese integrations is excessive increase in fault currentdue to the presence of DO within a micro grid
[1],Conventional protection devices installed for protectionof excessive fault current in power systems,mostly at the high
voltage substation level circuit breakers tripped by over-current protection relaywhich has a response-time delay resulting
in powersystem to pass initial peaks of fault current [2].But, SFCL is a novel technology which has thecapability to quench
fault currents instantly as soon asfault current exceeds SFCL's current limiting thresholdlevel [3]. SFCL achieves this
function by losing itssuperconductivity and generating impedance in thecircuit. SFCL does not only suppress the
amplitudes offault currents but also enhance the transient stability ofpower system [4].Up to now, there were some research
activitiesdiscussing the fault current issues of smart grid [5], [6].But the applicability of SFCLs into micro grids was
notfound yet. Hence, in order to solve the problem ofincreasing fault current in power systems havingmultiple micro grids
by using SFCL technology is themain concern of this work.The utilization of SFCL in power system provide the
mosteffective way to limit the fault current and results inconsiderable saving from not having to utilize high capacitycircuit
breakers. |
With Superconducting fault current limiters (SFCLs) utilize superconducting materials to limit thecurrent directly or to
supply a DC bias current that affects the level of magnetization of asaturable iron core. Being many SFCL design concepts
are being evaluated for commercial expectations,improvements in superconducting materials over the last 20 years have
driven the technology[4]. Case in point, the discovery of high-temperature superconductivity (HTS) in 1986drastically
improved the potential for economic operation of many superconducting devices. Thisgrowth is due to the capability of
High temperate Sensitive materials to operate at temperatures around 70Kinstead of near 4K, which is required by conventional superconductors [10]. The advantage is thatrefrigeration overhead associated with operating at the higher
temperature is about 20 times lesscostly in terms of both initial capital cost, operational cost and maintenance cost. |
II.SIMULATION SET-UP |
Matlab/Simulink/SimPowerSystem was selected to design and implement the SFCL model. Simulink/SimpowerSystem has
number of advantages over its contemporary simulation software (like EMTP, PSPICE) due to its open architecture, a
powerful graphical user interface (GUI) and versatile analysis and graphics tools. Control systems designed in the
Matlab/Simulink can be directly integrated with SimPowerSystemmodels. A complete smart grid power network including
generation, transmission, and distribution with wind farm model was also implemented in it. |
A. Design of Power System |
Newly developed micro grid model was designed by integrating a 10 MVA wind farm with the distribution network.Two
more wind farms are connected with the power system model for the analysis of power system connected with multi energy
sources. The power system is composed of a 100 MVA conventional plant, connected through 3-phase synchronous
machine which is connectedwith 200 km long 154 kV distributed-parameters transmissionline through a step-up
transformer TR1. At the substation(TR2), voltage is stepped down from 154 kVto 22.9 kV.High power industrial load (6
MW) and low power domesticloads (1 MW each) are being supplied by separate distribution networks. The wind farm is
directly connected withthe branch (B1) through transformer TR3 and is providingpower to the domestic loads connected to
the distributing line. The 10 MVA wind farm iscombination of five fixed-speed induction-type wind turbines eachhaving a
rating of 2MVA. At the time of fault, the domestic loadis being provided with 3 MVA out of which 2.7 MVA is provided
by the wind farm.Four prospective locations for SFCL installation are marked like Location 1 as Substation, Location 2 as
Branch Network, and Location3 as Wind farm integration point with the grid and Location4 as Wind Farm. Generally,
conventional fault current protectiondevices are located in Location 1 and Location 2.The output current of wind farm the
output of Transformer3 in Fig. 1 for various FCL locations have been measured and analyzed inSection III for determining
the optimum location of SFCL in amicro grid. |
B. Resistive SFCL Model |
The three phase resistive type SFCL was modeled considering four fundamental parameters of a resistive type SFCL [9].
These parameters and their selected values are: 1) transition or response time=2msec,2) impedance between 0.01ohms and
20ohms, 3) triggering current=550A and 4) recovery time=10msec. Its working voltage is 22.9 kV. Fig. 2 shows the SFCL model developed in Simulink/SimPowerSystem. The SFCL model working is explained as follows.
First, SFCLmodel calculates the RMS value of the passing current and thencompares it with the characteristic table [1].
Second, if a passingcurrent is larger than the triggering current, SFCL resistanceincreases to maximum impedance level in a
pre-definedresponse time. When the current level falls down than thetriggering current value the system waits until the
recovery timeand then goes into normal state.
SFCL has been located at substation (Location 1) and for a distributiongrid fault, various SFCL impedance values versusits
fault current reduction operation has been plotted. Maximumfault current (No SFCL case) is 7500 A at 22.9 kV for this
simulation. |
III.SIMULATION RESULTS |
Three scenarios of SFCL’s possible locations were analyzedfor four different fault occurring points and no fault in the
power system depictedin Fig. 1. As per the first assumtion the single SFCL was locatedat Location 1 Substation. Second,
single SFCL was located atLocation 2 Branch Network. Third, single SFCL was locatedat Location 3 Wind farm
integration point with the grid. |
A. Fault in the Distribution Grid (Fault 1) |
In the case of SFCL located at Location 1 Substation orLocation 2 Branch Network.Fault current contribution fromthe wind
farm was increased and the magnitude of fault currentis higher than No SFCL situation. These critical observationsimply
that the installation of SFCL in Location 1 and Location 2, instead of reducing itincreased the DG fault current. Thissudden
rise of fault current from the wind farm is caused by the abrupt change of power system’s impedance. The SFCLat these
locations (Location 1 or Location 2) entered into currentlimiting mode and reduced fault current coming from
theconventional power plant due to rapid increase in its resistance.Therefore the wind farm which is other power source and
alsocloser to the Fault 1 is now forced to supply larger fault currentto fault point (Fault 1).In the case when SFCL is
installed at the integration pointof wind farm with the distribution grid, marked as Location 3 in Fig. 1, fault current in
thewind farm has been successfully reduced. SFCLgives 68% reduction of fault current from wind farm and alsoreduce the
fault current coming from conventional power plantbecause SFCL is located in the direct path of any fault currentflowing
towards Fault 1. |
With dual SFCL installed at Location 1 and Location 4,45% reduction in fault current is observed.Eventhough two SFCLs
were installed, fault currentreduction of wind farm is lower than what was achieved by the single SFCLinstalled at Location
3. By observing the simulation results it wasknown that the installation of two SFCLs at both Location 1 andLocation 4 is
economically and technically not feasible. |
Fig.3. five different fault conditions considered at location 1 (a) without any fault, (b) fault at location 1, (c) fault at location
2, (d) fault at location 3, (e) fault at location 4 |
B. Fault in Customer Grid (Fault 2) |
Fig. 5 shows a comparison between fault current from thewind farm (measured at output of TR3) for differentSFCL
locations in the case when a three-phase-to-ground faultwas initiated in the customer grid Fault 2 in Fig. 1.Fault 2 is
comparatively a small fault as it occurred in lowvoltage customer side distribution network. The results observedare similar
to what were observed in the case of distribution grid(Fault 1) as explained in Section III-A.Once again the best results are
obtained when a single SFCLis located at Loc 3 which is the integration point of thewind farm with the distribution grid. |
C. Fault in Transmission Line (F3) |
The Fault 3 in Fig. 1 indicates the rarely occurring transmissionline fault which results in very large fault currents. Fig. 6
showsa comparison between fault current from the wind farm (measuredat output of TR3 in Fig. 1) for different Super
conducting fault current limiter (SFCL) locations inthe case when a three-phase-to-ground fault was initiated in
thetransmission line (Fault 3 in Fig. 1).When a fault occurs in transmission line, fault current fromthe conventional power
plant as well as the wind farm wouldflow towards fault point. For the wind farm condition, fault currentwould flow in
reverse direction through the substation and intothe transmission line to fault . Thus, on the contrary to theprevious results
obtained in Sections IIIA and IIIB, SFCL positionedat Location 1(Substation) or Location 2 (Branch Network)reduces the
fault current in wind farm. This result comesfrom the fact that SFCL is installed directly in the path of reversecurrent being
generated by the wind farm towards faultpoint. |
The majority of faults in a power system might occur in the distribution grid and the SFCL designed to protect micro-grid
should not be expected to cater for the transmission line faults (Fault 3). An important aspect to be noted here is that wind
farms on distribution side can contribute fault currents to transmission line faults and this phenomenon must be considered
while designing the protection schemes for the smart grid. When the SFCL was strategically located at the point of
integration of the wind farm with the grid Location 3, the highest fault current reduction was achieved. Performance of
SFCL at this location was even better than dual SFCL located at Location 1 and Location 4 at a time. Thus the multiple
SFCLs in a microgrid are not only costly but also less efficient than strategically located SFCL. Moreover, at Location 3
fault current coming from the conventional power plant was also successfully limited. |
Further this is extended by adding another two wind farms to the existing. Once again the process is repeated and the
location of SFCL is analyzed.The analysis is carried out at only fault F1 condition. Here also the fault is created at 0.4s of
run time. The analysis concludes that SFCL works effectively when placed at location 3 in three wind farmsystems. |
IV.CONCLUSION |
This paper presented an analysis for possible positioningthe SFCL in rapidly changing modern power grid. A
completepower system along with three micro gridscascaded to the grid was modeled and transient analysis forthree-phaseto-
ground faults at different locations of the gridwere performed with SFCL installed at key locations.It has been observed
that SFCL should not be installed directlyat the substation or the branch network. This placementof SFCL result in
abnormal fault current contribution from thewind farm. Also number of SFCLs in micro grid are inefficientboth in
performance and cost. The optimal location of SFCL ina power grid which limits all fault currents and has no
negativeeffect on the DG source is the point of integration of the windfarm with the power grid. |
Figures at a glance |
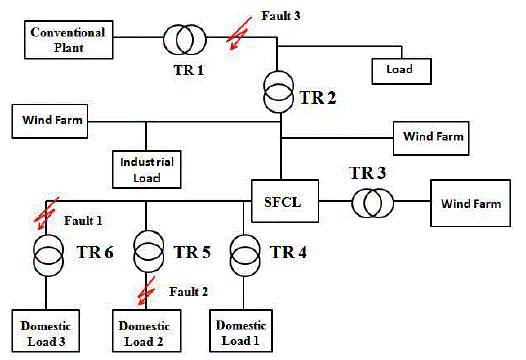 |
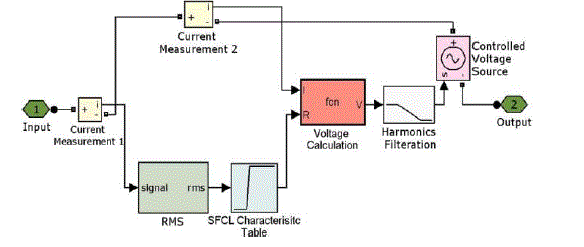 |
 |
Figure 1 |
Figure 2 |
Figure 3 |
 |
 |
 |
Figure 4 |
Figure 5 |
Figure 6 |
|
|
References |
- Umer A. Khan, J. K. Seong, S. H. Lee, S. H. Lim, and B. W. Lee, Member, IEEE, “Feasibility Analysis of the Positioning of Superconducting Fault Current Limiters for the Smart Grid Application Using Simulink and SimPowerSystem,” IEEE Trans. Applied Superconductivity, vol. 21, no. 3, june 2011.
- T. Jamasb, W. J. Nuttall, and M. G. Pollitt, Future Electricity Technologiesand Systems. Cambridge: Cambridge Univ. Press, 2006, pp.83–97, 235– 246.
- B. C. Sung, D. K. Park, J. W. Park, and T. K. Ko, “Study on a seriesresistive SFCL to improve power system transient stability:Modeling,simulation and experimental verification,” IEEE Trans. Industrial Electron.,vol. 56, no. 7, pp. 2412–2419, Jul. 2009.
- Litos Strategic Communication, “The Smart Gird: An Introduction,” 2008.
- R. Strzelecki and G. Benysek, Power Electronics in Smart ElectricalEnergy Networks. London, U.K.: Springer-Verlag London Ltd.,2008, pp. 203– 213.
- J. Driesen, P. Vermeyen, and R. Belmans, “Protection issues in microgridswith multiple distributed generation units,” in Power ConversionConf., Nagoya, April 2007, pp. 646–653
- W. Friedl, L. Fickert, E. Schmautzer, and C. Obkircher, “Safety and reliabilityfor smart-, micro-, and islanded grids,” presented at theCIREDSeminar: SmartGrids for Distribution, Jun. 2008, Paper 107.
- L. Dessaint, K. Al-Haddad, H. Le-Huy, G. Sybille, and P. Brunelle, “Apower system tool based on simulink,” IEEE Trans. Industrial Electron.,vol. 46, no. 6, pp. 1252–1254, Dec. 1999.
- K. Maki, S. Repo, and P. Jarventausta, “Effect of wind power baseddistributed generation on protection of distribution network,” inIEEEDevelopments in Power System Protection, Dec. 2004, vol. 1, pp.327–330.
|