Keywords
|
Messung PLC, Hardening and Tempering, Heat Treatment Plant, Mitsubishi HMI. |
INTRODUCTION
|
Industrial Automation has acquired importance owing to the ever-increasing demand for more productivity, better quality standard, better accuracy and optimum utilization of available resources and manpower. In India, Siddheshwar is one of the largest units that are the suppliers of Hardened and Tempered of steel working for Mahindra motors. In accordance with the huge productivity demands of their Shock Absorbing Units for Mahindra Motors, Siddheshwar India has planned a semiautomated machine that is served for hardening and tempering of steel bits in their production unit. The main aspect of the project is to automate the processing of steel materials which is a crucial step in the production of automobile materials like shafts, levels and gears. |
RELATED WORK
|
The related approaches consist design of semi-automated H&T furnace based on PLC. In this, the PLC based automated system controls three types of control functions, namely, Hydraulic control, Pneumatic control and Motor control. Hardening and tempering of steels is a procedure for modifying the metal's characteristics to better suit the job it has to perform. In the case of tool bits it enables them to machine other materials and still retain a sharp cutting edge, whilst in the case of work pieces it can materially alter their wear characteristics and tensile strength. Virtually all steel hardening processes involve the inclusion of particular carbon compounds either at the metal's surface or throughout the body of the metal via the application of heat. It's true that metals can also be 'work-hardened' or forged or laminated but the application of these processes will not be considered here [5]. Some types of steel have other trace elements such as cobalt and tungsten in addition to carbon which augment the ultimate hardness achieved and the temperature at which they can operate.[4] |
PREVIOUSLY EXISTING METHODS
|
The Methodology which was used prior to the semi-automated system included hand feeding of steel bits into and out of the hardening and tempering furnaces. This method required comparatively more labors and excessive hardwork in a risky environment as compared with the semi-automated system. The process demanded more man power as well as time requirement. Many such factors resulted in less production as per the requirement. Also, the safety issues were of a concern. The automated process was proposed due to failure in matching the demands of the market as well as due to the safety issues. The processing of steel bits by hardening and tempering is achieved by means of a Messung Nexgen 5000 PLC. It has about 1000 inputs and outputs. The programming is done by means of a ladder diagram. The following Table 1 illustrates the comparison of various key performance parameters between the previously existing and the currently existing method. |
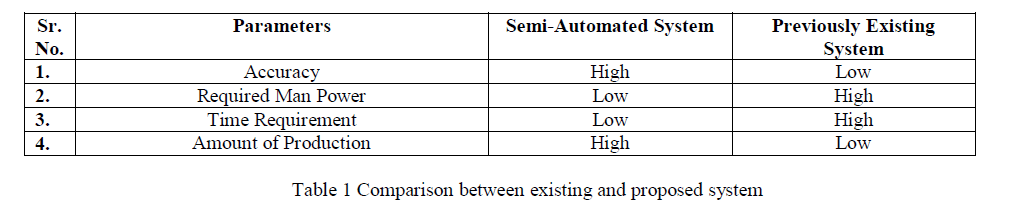 |
(A) Amount of Production: The amount of production in the previously existing method was severely low owing to the handheld process. The efficiency of the work, also, was not up to the mark. The automated control system implements an efficient algorithm for the overall synchronization of the sequence of operations. As a result, the amount of production is increased as compared to the previously existing method. |
(B) Quantity of Manpower: A comparison between the two systems indicates that more number of workers were needed in the previously existing methods. The automated method, however, demands less manpower which ultimately resulting in lower costs for manufacturing. |
(C) Time Consumed: The previous system implemented a time consuming method for hardening and tempering, that too with less accuracy and precision. The automated system does not have such constraints owing to the high speed switching operation performed by the PLC. |
(D) Accuracy: The Accuracy is a vital performance parameter which decides the overall efficiency of the system.The automated system perform the processing with the highest precision and accuracy as compared to the previously existing method. |
DESCRIPTION OF SYSTEM AND WORKING
|
Figure 1 shown below describes the basic block diagram of the proposed system |
 |
(A) Control Panel: The Control Panel block and the input signal conditioning circuit includes the various components like PLC, SMPS, Transformer, Relays, and Connectors. The PLC is the heart of the controlling action provided to the system. The PLC being used is Messung Nexgen-5232 PLC. It has about 1k inputs and outputs. The SMPS is used to provide a 24VDC supply to the PLC. The Transformer is used to power up the different components which require an AC supply. Finally, the relays and connectors serve the function of switching ON/OFF which is essential in the controlling action. |
(B) HMI: The Human Machine Interface is used to achieve an active communication between the system and the operator. The operator can set the values of various parameters like the rotating angle of the servo motor along with the various modes of rotation. The HMI provides information about various key parameters like the operating temperature, the count of the finished jobs and the mode of operation of the system. The HMI being used is a Smartline Sr. Ex. HMI. It has a STN monochrome Liquid Crystal Display, a 3.7’’ Diagonal Display along with various colored LED’s for indicating different states of the machine. |
(C) Hydraulic Control: The conditioned signal output is fed into one of the three output drives, i.e., Hydraulic drive. This kind of drive is normally used in case of working with heavy objects or jobs. Therefore, in our case, we use Hydraulic control for working with the pushers, as the pushers are subjected to push heavy jobs to the maximum of 20 jobs at a time, also sustaining subjective frictional force. Separate hydraulic pumps are used for every pusher so as to reduce the design complexity. |
(D) Pneumatic Control: The other type of drive to which the conditioned output signal from the PLC and HMI are fed is given to the Pneumatic control drive. Basically Pneumatics are used in complex automations in which compressed air is used as a feed input, but they are usually avoided when worked with heavy loads. Therefore, in our case, we use the Pneumatic controls for driving the Extractor forks, because these extractor forks are planned to deal with one job at a time, which the Pneumatic control can easily handle. |
(E) Motor Drive Control: The third type of drive to which the conditioned output signal is fed is the motor drive control. The motor drive controls are basically used to control the linearly driven as well as the non-linear bidirectional conveyor motors. The linear motors include the fans and blowers that are activated when the parts of the furnace show abnormal heat up. The other motors that drive the conveyors, pushers, extractor forks are also controlled by the motor drive control. |
WORKING OF THE SYSTEM
|
The following flowchart illustrates the working explained above: |
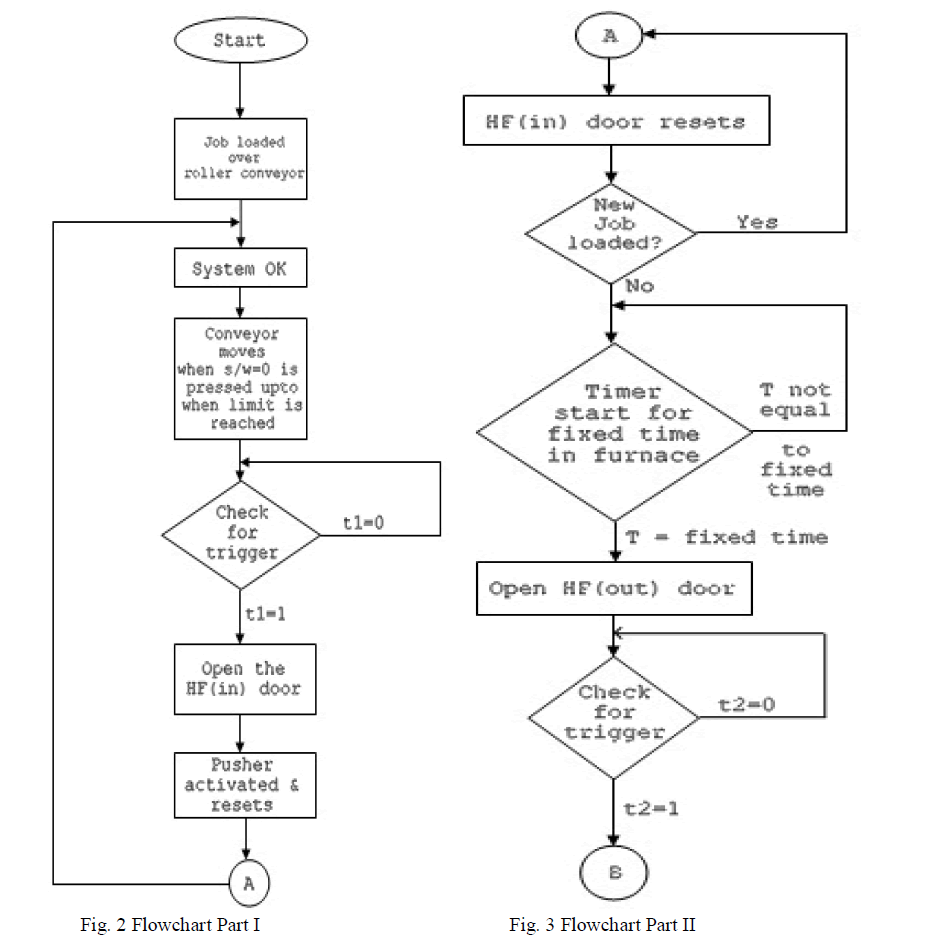 |
 |
HARDWARE IMPLEMENTATION
|
A. Input Devices – |
1) Sensors (K-type thermocouples) : Temperature is detected with the help of k-type thermocouples present in the furnace. |
2) Limit switches : Limit switches supply a signal to limit the backward movement of the pushers and extractors. |
B. Output Devices – |
1) Pushers : Pushers are used to push the job into the Hardening and Tempering furnaces. |
2) Extractors : Extractors are used to extract the job from the furnaces. |
3) Conveyors : The movement of the job from one furnace to the other is carried out with the help of conveyors. |
CONCLUSION
|
In this paper, we presented designing of a PLC based control system for Hardening and Tempering Furnace. The automated process efficiently reduces the man power required for the process and also increases the efficiency of hardening and tempering process of raw steel bits. The use of PLC for controlling action of the system effectively results in increased production, less time consumption and better safety for the employees. |
FUTURE SCOPE
|
The application can be extended for the hardening and tempering of different metals that require different temperatures for proper hardening and tempering and also the process can be made completely automatic that won’t require any human interruption. |
ACKNOWLEDGEMENT
|
We are grateful to our Internal Project guide, Mrs. Jayashri P. Joshi for her continuous support and motivation regarding the project. We also thank our External project Guide, Mr. Ganesh Toke for helping us solve the technical difficulties which were faced during the entire phase of the project. |
References
|
- Georg Frey and LotharLitz, “Formal Methods in PLC Programming”, IEEE Conference on Systems Man and Cybernetics SMC 2000, pp.1-4, 2000.
- Ai-min Li, Chuan-hui Zhang, Hai-lin Li, Zhi-yang Xu, Xiao-hui Chen, Guang-le Qin, Sheng-wei Ye, “Design of Automatic Welding Machine Basedon PLC”, Fourth International Conference on Intelligent Computation Technology and Automation 2011, pp 627-630, 2011.
- B. Mulman, T. Devinder, and W. Gi-Nam., “Generation of PLC Ladder Diagram Using Modular Structure”, International Conference onComputational Intelligence for Modelling, Vienna, pp. 1194-1198, Oct 2008.
- John Webb, “Programmable logic controller”, 2nd Edition, Macmillan Publishing Co.
- C D Johnson, “PLC Process Instrumentation and Technology”, 8th Edition, Tata McGraw Hill.
|