Keywords
|
Smart grid, Radio Frequency Identification (RFID), Power Line Communication (PLC), Power factor. |
INTRODUCTION
|
Today’s electrical infrastructure has remained electrical grid has been ageing infrastructure, the demand for electricity has gradually increased.The demand and consumption of electricity increased by 2.5% annually over the last 20 years. Today the electric power distribution network is very complex. Among the deficiencies are a lack of some ideas and switching mechanically causes slow response time. These have contributed to the blackouts happening over the past few years. Some additional inhibiting factors are the growing population,the demand for the energy, the global climate condition, equipment failures problem, the capacity limitations of electricity generation, energy storage problems, one-way communication and decrease in fossil fuels. |
Consequently, a new grid infrastructure is urgently needed to address these challenges. Smart grid is a modern electric power grid infrastructure to improve the efficiency, reliability and safety with smooth integration of renewable energy sources through automated control and modern two way communications technologies [9]. |
RFID (Radio Frequency Identification) or contactless IC card technology is widely used throughout the world. Its high-security system, used in a wide variety of applications such as cashless payment ticketing systems for transportation and home appliances. For example in departmental stores, the people can pay the payments more easier, by holding an IC card over a reader/writer. Radio-Frequency Identification (RFID) is an automatic identification method, relying on storing and retrieving data using devices called RFID tags or transponders. RFID includes RFID reader and RFID tag[8]. |
In traditional electricity billing system, a person from electricity board has to come to the consumers house and note down the reading of the electricity in units. The amount will be noted and consumer must pay the amount to the electricity board. If the consumer did not pay the amount, the person from electricity board again has to come and trip the supply to consumers. Inorder to avoid human necessary to do the billing and tripping process, a new technology were developed to enchance the grid to be smart.This paper proposes a new technique to make the present electrical grid system into very smart by using RFID based power line carrier technology with power factor maintenance in load side. The proposed system suggests a design of a system which can be used for data transmission between the consumer and suppliers by using RFID tag. The user should buy one RFID card from electricity board. The card number must be registered in the data base of the electricity board. |
The power factor plays an important role inorder to design an energy saving scheme in load side. The output of lagging power factor increases the power losses in the electrical network[7].The non -linear load will be the main cause for lagging power factor.The designed scheme is concerning about maintaining the power factor of load side. |
Power factor is the cosine of the angle between the voltage and current. The current and voltage is sensed by using current and voltage transformer. The phase angle between the voltage and the current is calculated by inbuilt computers in the microcontroller.These processes are continuously carried out in microcontroller and maintain the power factor automatically[1-2][5]. |
HARDWARE DESCRIPTION
|
Smart grid
|
Recently, smart grid (SG) is the buzz word, which has attracted attentions from engineers and researchers in both electric power and communication sectors. The concept of smart grid has appeared in recent literature in different techniques used to control the power grid operation. Some referred it is intelligent grid whereas some called it the grid of the future. The main objective of the smart grid concept is to provide the consumers with power in a more stable and reliable manner that the aging power grids of today may not be able to provide in the near future. Smart grid can be used a two-way communication between the suppliers and consumers of electric power. The bi-directional communication indicates the ability of smart grid to enable the end users to express their power requirement demands to the utility suppliers. |
A smart grid is a modernized electrical grid that uses information and communication technology to gather some ideas about the behaviours of suppliers and consumers in an automatic fashion to improve the efficiency and originality in the production and distribution of electricity. Smart grid reliable and real-time information becomes the key factor for reliable delivery of power from the suppliers to the consumers. The impact of equipment failures or damage, capacity constraints, and natural accidents which creates some problems in monitoring, diagnostics and protection of power system [9]. The communications system is the key component of the SG infrastructure. Different communications technologies can be used for data transmission between smart meters and electric utilities. In some cases wired communications have some advantages over wireless technologies such as low-cost and maintenance. The transmission path may cause the signal to attenuate. On the other hand, wired solution do not have interference problems and their functions are not dependent on batteries, as wireless solution often do. |
Basically, two types of information infrastructure are needed for information flowing a system of smart grid. Initial path is from sensor and electrical appliances to smart meter, the second is between smart meter and the utility’s data centers. As suggested in [9], the data flow can be accomplished through power line communication or wireless communications, such as ZigBee, Z-wave, and others. |
Power Line Communication
|
Smart Grid objectives include the integration of intermittent renewable energy sources into the electricity supply chain, securing reliable electricity delivery to the consumers.Power line communication (PLC) carries data on a conductor that is also used simultaneously for AC electric power transmission or electric power distribution to consumers. Power line communication (PLC) is a technique that uses the power lines to transmit high-speed (2–3 Mb/s) data signals from one device to the other. |
It has been the first choice for communication with the electricity meter due to the direct connection with the meter and successful implementations of AMI in urban areas where other solutions struggle to meet the needs of utilities. PLC systems based on the low voltage distribution network have been one of the research topics for smart grid applications in China [9]. |
Features of PLC
|
1.PLC can be considered as a promising technology for smart grid applications due to the fact that the existing infrastructure decreases the installation cost of the communications infrastructure. |
2.The standardization efforts on Power line communication networks, the high cost, omnipresent nature, and used in wide applications. Home area applications is one of the biggest applications for PLC technology. |
3.In this technology can be well suited to urban areas for smart grid applications, such as smart metering, monitoring and control applications, since the PLC infrastructure is already covering the areas that are in the range of the service territory of utility companies. |
Although there are strong wireless and wire line communication competitors, it is believed that power line communications (PLCs) will fulfill various communication tasks in upcoming Smart Grid deployments as PLC provides the natural upgrade from simple electricity conductors to hybrid and bidirectional electricity and data communication solutions. |
Radio Frequency Identification
|
Radio-frequency identification (RFID) is an automatic identification method, relying on storing and remotely retrieving data using devices called RFID tags or transponders. An RFID tag can be applied to a product and radio waves is used for identifying and tracking the users. The tag can be read from several meters away and beyond the line of sight of the reader. Electronically programmed with unique information. Many types of RFID systems are available in the market. Depending upon the frequency range they are classified as follows: |
1) Low-frequency (30 KHz to 500 KHz) |
2) Mid-Frequency (900KHz to 1500MHz) |
3) High Frequency (2.4GHz to 2.5GHz) |
These frequency ranges mostly depends on the length of the tag.For example, low frequency tag ranges from 3m to 5m, mid-frequency ranges from 4m to 16m and high frequency ranging from 5ft to 95ft. There are variety of frequencies or spectra through which RFID tags can communicate with readers. Again, there are trade-offs among performance,cost and application requirements. For instance, low-frequency tags are very cheaper than ultra highfrequency (UHF) tags, use only a small amount of power and are better able to penetrate nonmetallic substances. Scanning the objects with high water content, such as fruit, are at close range. |
The data transfer is faster in ultra high frequencies which has a better range, when compare to all other frequencies. More power is needed to pass through the materials. So UHF tags are used in wood, paper, cardboard or clothing products.UHF tags might be better for scanning boxes of goods as they pass through a bay door into a warehouse. |
Data Capacity
|
The amount of data storage on a tag can vary, ranges from 16 bits on the low end to as much as several thousand bits on the high end. Of course, if the storage capacityis high the price per tag is high. |
Passive Versus Active
|
“Passive” tags have no battery and "broadcast" their data only when energized by a reader. That means they must actively polled to send information. "Active" tags are more capable of broadcasting their data using their own battery power. In general,the read ranges are much greater for active tags than they are for passive tags perhaps a read range of 100 feet or more than that, versus 15 feet or less for most passive tags.The read ranges of active tags and the extra capability however,this will be cost; they are several times more expensive than passive tags. |
Today, active tags are much more likely to be used for high-value items or fixed assets that may be trailers, where the cost is minimal compared to the item value, and very long read ranges are required. Most conventional supply chain applications, such as RFID-based tracking and agreement programs emerging in the consumer goods retail chain, will utilize the less expensive passive tags. |
Typical Applications of RFID
|
• Automatic Vehicle identification |
• Inventory Management |
• Work-in-Process |
• Container/ Yard Management |
• Document/ Jewellery tracking |
Merits Over Bar Coding
|
No "line of sight" requirements: Bar code reads can sometimes be limited or problematic due to the need to have a direct "line of sight" between a scanner and a bar code. RFID tags be able to read through materials without line of sight. |
More automated reading: RFID tags can be able to read automatically when a tagged product comes past or near a reader, reducing the labor required to scan product and allowing more proactive, real-time tracking. |
Improved read rates: RFID tags ultimately offer the promise of higher read data rates than bar codes, particularly in high-speed operations such as carton sortation. larger data capacity: RFID tags can be easily encoded with item details such as bunch and batch, weight, etc. |
"Write" capabilities: since RFID tags can be rewritten with new data as supply chain activities are completed, tagged products carry updated information as they move throughout the supply chain. |
Power Factor
|
The main objective of this proposed system is to design an energy saving scheme for an load side. This can be achieved by decreasing the network losses and improving the main electric load operation to a better stability level. The designed scheme is concerned with improving the powerfactor maintenance of the load side. Industrial power distribution networks encounters increase in power losses and increase in the type of load is accompanied with low power factor which leads to huge transfer of reactive power from the utility through the network. The main drawback of presence of non linear load is increase in the network losses and reduces the voltage level. It can result in poor reliability and higher energy costs. |
Power factor is defined as the ratio between real power or actual power to apparent power.The general definition can be applied to all cases. The actual amount of power being used or dissipated in a circuit is called true power. Reactive loads such as capacitors and inductors make up what is called reactive power. The linear combination of actual power and reactive power is called apparent power. |
In general Power system consist of inductive, resistive, and capacitive loads. Examples of resistive loads are kettles electric radiators and electric heaters.Similarly Inductive loads are arc furnance,induction motors and reactors and at last capacitive loads are capacitors, variable or fixed capacitor bank and overexcited synchronous motor.Low power factor is not create more problem in domestic’s area but it becomes a big challenges in industry where multiple large motors are used, there is requirement to correct the power factor. There are many benefits to having power factor correction [7]. |
In an AC circuits there exist a phase difference between voltage and current. The term is also known as power factor of the circuit. |
Power factor=Active power(kw)/Apparent power(kvar) |
A purely resistive load (kettles ,electric radiators and electric heaters) would have a power factor of 1.0 (unity).If the circuit is inductive, the current value lags voltage value by 90 degree and the power factor is called as lagging power factor. If the circuit is capacitive then current value leads to the voltage value by 90 degree and power factor is said to a be leading power factor.The average power in an AC circuit is expressed in terms of rms current and voltage P= VI cos?. |
Non-Linear Load Power Factor
|
In recent years, some electrical power utility companies have experienced a significant increase in the quantity and magnitude of nonlinear loads being connected to their power systems. Loads such as fluorescent lights,induction motor,microprocessor-driven equipment, power supplies and variable speed drives are often relatively small and well dispersed to cause a major negative impact on the power system.This paper deals about the concept of nonlinear load. Subsequently, non linear load power factor is discussed with practical examples.In AC power distribution systems, harmonics occur during the normal electric current waveform is distorted by non-linear loads. Most loads in modern electrical distribution systems are inductive. Examples includes transformers, motors and induction furnaces. The induction motor must operate at a lagging power factor.This power factor is very low at no load and increases to about 85 to 90 percent at full load, the enlargement being caused by the increased real-power requirements with increasing load. The presence of air-gap between the stator and rotor of an induction motor greatly increases the reluctance of the magnetic circuit. Consequently, an induction motor draws a large magnetizing current to produce the required flux in the air-gap. |
(i)At no load, an induction motor draws a large magnetizing current and a small active component to meet the no-load loss.Therefore, the induction motor takes a high no-load current lagging the applied voltage by a large angle. Hence the power factor of an induction motor on no load is low about 0.1 lagging. |
(ii) When an induction motor is loaded, the active component of current increases while the magnetizing component remains about the same. Accordingly, the power factor of the motor is increased. However, because of the large value of magnetizing current, which is present in spite of load, the power factor of an induction motor even at full load rarely exceeds 0.9 lagging. |
Power factor maintenance is a technique of counter acting the undesirable effects of electrical loads that create a power factor that is less than one. Power factor modification may be applied either by an electrical power transmission utility to improve the stability and efficiency of the transmission network or correction may be installed by individual electrical customers to reduce to reduced the cost charges to them by their electricity suppliers[7]. Power factor maintenance is also reduce the penalty cost to the consumers. Auto transformer is used as a inductive load for varying the power factor. |
PROPOSED SYSTEM
|
Proposed System Block Diagram
|
Fig no 2. Block Diagram for Proposed System |
Performance of the Proposed System
|
This proposed system is divided into two parts: consumer and supplier. The consumer side consists of a energy meter,logic circuit, an RFID reader based on a microcontroller, and the supplier consists of a PC with data base of consumers. The RFID reader is used to read the credit ID in meter charging, the ID is sent to the supplier to check the ID’s information in the database and sends them back to the consumers where the microcontroller takes action based on that information. The microcontroller manages all the system work in the consumers. The ID and its information can be transmitted between each consumers and the supplier through Power Line Communication(PLC) and also this proposed system perform the signals are obtained from instrument transformer like potential and current transformers. Logic circuit is used to convert the square waveform to compatible waveform. Converted waveforms are fed into a counter, situated in the microcontroller. The counted pulses are changed into corresponding value of phase angle ?.Relay mainly performs the opening and closing of a connection of load through supply mains depending upon the amount present in the RFID card and the presence of non-linear load (inductive load) at a moment. |
Experimental Setup
|
Energy Meter generally produces electrical pulses proportional to the power consumed by the consumer and the power supply of microcontroller.Microcontroller calculates the energy inspired by the consumer utilizing the output of Energy Meter and act according to the programs loaded on the microcontroller. RFID Card interfaces with the microcontroller unit in which the amount recharged by the consumer are written.When the amount is reduced below 10 percentage, the alarm circuit will get on.Relay primarily performs the opening and closing of a connection of load through supply mains depending upon the amount present in the smart card at a moment and also when non-linear load is come into play.Magnitude of the voltage and current are fed into the microcontroller. It is used to measure the phase shift between the voltage and current. The cosine value of the electrical quantities like voltage and current are measured by using microcontroller. According to the power factor the same relays is closed or opened.The signal from microcontroller (either 0 or 1) is used to operate the relay. |
Features of Proposed System
|
• Remotely Connect / Disconnection of Power supplythrough PLC. Automation of all features including communication from the sub -station to the customer. |
• It involves less cost to communicate. PLC is a quick reaction. Once the power line are connected, identification and transaction can be done within 0.1 second. This system increases productivity. |
• The power factor maintenance is used to enlarge the stability of power system. |
CONCLUSION
|
In many technological innovations are taking place in this world, existing electricity billing process seems in India to be very obsolete and does not meet the latest technology available. In this plan, the above said process is totally automated and the communication is made possible entirely through the power line communication. This communication is bi-directional at a faster data rate through long distance. Hence it is beneficial to the customers as the system is made very user friendly. The EB billing procedure has the ability of fulfilling a set of needs for the user and the EB workers.This proposed power factor maintenance circuit experimentally tested with auto transformer. Electric energy is consumed in our day to day life. It is used in Industry applications.This experimental setup is used to maintain the power factor in load side. The power factor adjustment is used to maintain the stability of the power system. |
|
Figures at a glance
|
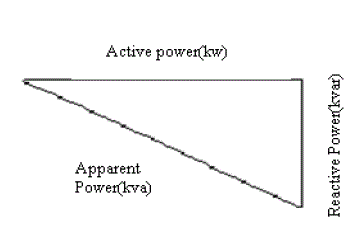 |
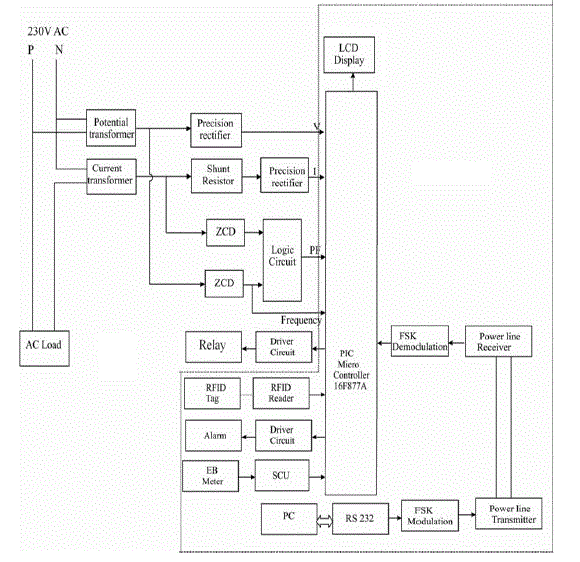 |
Figure 1 |
Figure 2 |
|
|
References
|
- AndrásFehér, Dr. ZoltánPuklus “Definitions and Measurement of Power Factor” 8th International Symposium of Hungarian Researchers on Computational Intelligence and Informatics.
- Fawzi Al-Naima ,BahaaJalil “ Building a Prototype Prepaid Electricity Metering System Based on RFID” International Journal of Electronics and Electrical Engineering ISSN : 2277-7040 Volume 1 Issue 1.
- G.Venkatesan, R. Arumugam, M.Vasudevan, S. Paramasivam and Vijayan 2006 “Modelling and Simulation of Novel Switched Reluctance Motor drive system with Power factor improvement, American journal of Applied Sciences 3(1):1649-1654 2006 ISSN 1546-9239, Science Publications.
- J. Vales-Alonso, V. Bueno-Delgado, E. Egea-Lopez, F. J. Gonzalez-Castano, J. Alcaraz, “Multiframe Maximum-Likelihood Tag Estimation for RFID Anticollision Protocols”, IEEE Transactions on Industrial sInformatics, vol. 7, 2011, pp. 487.
- Md. MejbaulHaque, Md. Kamal Hossain, Md. Mortuza Ali, Md. Rafiqul Islam Sheikh “Microcontroller Based Single Phase Digital Prepaid Energy Meterfor Improved Metering and Billing System” International Journal of Power Electronics and Drive System (IJPEDS)Vol.1, No.2, December 2011, pp. 139~147.
- M.Ravindran, V.Kirubakaran“Electrical Energy Conservation in Automatic Power Factor Correction by Embedded System” Energy and Power 2012, 2(4): 51-54.
- SapnaKhanchi, Vijay Kumar Garg “Power Factor Improvement of Induction Motorby Using Capacitors” International Journal of Engineering Trends and Technology (IJETT) – Volume 4 Issue 7- July 2013.
- TakanoriWashiro “Applications of RFID Over Power Line for SmartGrid” 2012 IEEE International Symposium on Power Line Communications and Its Applications.
- Vehebi,DilanSachin,Taskinkocak,SalihErgiit,CconcentinaBuccela,CarloCeloti,GerhardP.Hancke “smart grid Technologies: Communication Technologies and Standards” IEEE TRANSACTIONS ON INDUSTRIAL INFORMATICS, VOL. 7, NO. 4, NOVEMBER 2011.
|