the conventional method of converter boost the input voltage but power factor correction cannot be achieved properly in the input side but in the proposed semi bridge less converter boost the input voltage and achieved the power factor correction. The proposed converter features is higher efficiency, eliminate the input ripple. The detailed converter description, steady-state operation and experimental results of both conventional and proposed method are presented and analysed. The converter is applicable for the automotive level I and II but is ideally suitable for level I residential charging application.
Keywords |
AC–DC power converters, boost converter, bridgeless power factor correction (PFC), current
sensing, and plug-in hybrid electric vehicle (PHEV) charger. |
INTRODUCTION |
A Plug-in-hybrid electrical vehicle (PHEV) is a hybrid vehicle with a storage system that can be recharged
by connecting a plug to an external power source. The power from the external is given to conventional
circuit it covert AC to regulated DC supply and this DC supply is given to the battery storage system for
storing the electrical energy, but main drawback of these conventional topologies is power factor correction
not achieved properly in the input side but proposed boost converter eliminate the above drawback and this
converter efficiency also high. These paper numbers of boost topologies listed below those are interleaved
boost converter, bridgeless boost converter, the dual boost converter, the semi-bridgeless boost converter
and the proposed phase-shifted semi-bridgeless (PSSB) boost converter. |
The two stage cascaded PFC ac-dc and dc-dc converters is the common choice for PHEV battery chargers,
where the power rating is high, lithium-ion batteries are used. But in single stage approach lead acid
batteries are suited because it has large ripples in the output current. |
INTERLEAVED PFC |
Interleaved boost converter is shown in Fig.1.The circuit contain four input diodes D1,D2,D3 and D4.In
positive half cycles D1 and D3 are conducting and In negative half cycles D2 and D4 are conducting. So that
input current is sum of the two inductor current as shown in fig. The input two inductor ripple currents are
out of phase. Due to boost switching action input ripples are eliminated. Furthermore switching of the
converter (two MOSFETs) are 180 deg out of phase with single PFC boost. The most drawback of this
circuit is introduces smaller input current ripples and resultant heat management issue for the input diodes
bridge rectifier. The capacitor used for the circuit is to eliminate the higher ripples. |
BRIDGELESS PFC |
The bridgeless boost topology, as shown in Fig.2, is the second topology considered for this application. |
Here gating signals are identical shown in fig 3.the two inductorsL1 and L2 at the input side are used to
boost up the input voltage. This boost converter solves the heat management of the input diode rectifier
bridge, but it introduces increased EMI [22]-[24].Another disadvantage this topology is the floating input
line with respect to the PFC stage ground, which makes it impossible to sense the input voltage without a
low-frequency transformer. The operation of this converter is same as the dual-boost which can be described in below. |
DUAL BOOST PFC |
The dual-boost converter, as shown in Fig.4. The operation can be analyzed in two stages When the AC
input voltage goes positive, the gate of S1 is driven high and current flows from the input through the
inductor, storing energy. When S1 turns off, energy in the inductor is released as current flows through D1,
through the load and returns through the body diode of S2. During the-off time, the current through the
inductor L (i.e., during this time the inductor discharges its energy) flows in to the boost diode D1 and
close the circuit through the load. During the negative half cycle circuit operation is mirrored as
shown in S2 turns on, current flows through the inductor, storing energy. When S2 turns off, energy is
released as current flows through D2, through the load and back to the mains through the body diode of S1
back to the input mains. Note that the two Power MOSFETs are driven synchronously. The dual boost
topology reduces the gate loss, and at light loads. The light-load efficiency improvement comes at the
expense of the cost of an additional driver and increased controller complexity. |
SEMI BRIDGELESS PFC |
The semi-bridgeless configuration, as shown in Fig.6 In addition to diodes Da and Db which are slow
recovery diodes, resulting in two dc/dc boost circuits, one for each half-line cycle. During a positive half
line cycle, the first dc/dc boost circuit, L1 -D1–Q2 is active through diode Db, which connects the ac source
to the output ground. During a negative half-line cycle, the second dc/dc boost circuit, L2 -D2-Q1, is
active through diode D3, which connects the ac source to the output ground. It should be noted that
switches Q1and Q2, in both bridgeless PFC boost rectifiers can be driven with the same PWM signal,
which significantly simplifies the implementation of the control circuit. The drawback of the bridgeless
PFC boost rectifier in is that it requires an additional gate-drive transformer. |
PROPOSED CONVERTER |
The PSSB topology shown in Fig. 7 is proposed as a solution to simplify current sensing in bridgeless PFC
boost applications using the current synthesizer sensing method [27]. The gating signals of the MOSFETS are 180 deg out of phase shown in Fig.8, these proposed topologies over come all the
above problems like input electromagnetic interference (EMI), heat management issue for the input
diode bridge rectifiers and power factor correction problems. The main purpose of gate drive
transformer is used for the proposed method is used to increase the power rating and isolate the circuit
if any fault occur on the input side. The proposed converter steady state operation is described in the
below section. |
CONVERTER STEADY-STAT E OPERATION |
To analyze the circuit operation, the input line cycle is separated into positive and negative half-cycles,
as explained below. In addition, the detailed circuit operation depends on the duty cycle. Positive halfcycle
operation is provided for D > 0.5 in Section 1 and D < 0.5 in Section 2. |
A. Positive Half-Cycle Operation: |
Referring to Fig.7, during the positive half-cycle, when the ac input voltage is positive, Q1 turns on and
current flows through L1 and Q1 and continues through Q2 and then L2, returning to the line while
storing energy in L1 and L2. When Q1 turns off, the energy stored in L1 and L2 is released as current
flows through D1, through the load, and returns through the body diode of Q2/partially through Db back to
the input. |
B. Negative Half-Cycle Operation: |
Referring to Fig. 7, during the negative half-cycle, when the ac input voltage is negative, Q2 turns on and
current flows through L2 and Q2 and continues through Q1 and then L1, returning to the line while
storing energy in L2 and L1. When Q2 turns off, the energy stored in L2 and L1 is released as current
flows through D2, through the load, and returns split between the body diode of Q1 and Da back to the
input. |
C. Detailed Positive Half-Cycle Operation and Analysis for Duty cycle > 0.5: |
The detailed operation of the proposed converter depends on the duty cycle. During any half-cycle, the
converter duty cycle is either greater than 0.5 (when the input voltage is smaller than half of the output
voltage) or smaller than 0.5 (when the input voltage is greater than half of the output voltage). The three
unique operating interval circuits of the proposed converter are provided in Figs. 9–11 for duty cycles
larger than 0.5 during the positive half-cycle input. Waveforms of the proposed converter during positive
half-cycle operation with D > 0.5 are shown in Fig.12. To simplify the analysis, it is assumed that the
current splits between the bridge diode, the body diode, and the MOSFET channel equally. The intervals of
operation are explained here. |
Interval 1 [t0 −t1 ]: At t0 ,Q1/ Q2 are on, as shown in Fig.9 During this interval, the current in series
inductances L1 and L2 increases linearly and stores the energy in these inductors. The energy stored in
Co provides energy to the load. The return current is split among Db, Dq2, and Q2. |
Interval 2 [t1 −t2 ]: At t1 , Q1 is on, and Q2 is off, as shown in Fig.10 During this interval, the current
in series inductances L1 and L2 continues to increase linearly and store the energy in these inductors.
The energy stored in Co provides the load energy. The return current is split only between Db and Dq2. |
Interval 3 [t2 −t3 ]: At t2, Q1/Q2 are on again, and interval 1 is repeated, as shown in Fig. 9. During
this interval, the current in series inductances L1 and L2 increases linearly and stores the energy in these
inductors. The return current is again split among Db, Dq2, and Q2. |
Interval 4 [t3 −t4 ]: At t3, Q1 is off, and Q2 is on, as shown in Fig. 11. During this interval, the energy
stored in L1 and L2 is released to the output through L1, D1, partially Q2, Dq2, L2, and Db. |
D. Detailed Positive Half-Cycle Operation and Analysis for Duty cycle < 0.5: |
The three unique operating interval circuits of the proposed converter are given in Figs. 13–15 for duty
cycles less than 0.5 during the positive half-cycle. The waveforms of the proposed converter during these
conditions are shown in Fig. 16. The intervals of operation are explained here. |
Interval 1 [t0 −t1]: At t0 , Q1/ Q2 are off, as shown in Fig. 13. During this interval, the energy stored
in L1 and L2 is released to the output through L1, D1, partially Dq2, L2, and Db. |
Interval 2 [t1 −t2 ]: At t1 , Q1 is on, and Q2 is off, as shown in Fig. 14. During this interval, the
current in series inductances L1 and L2 continues to increase linearly and store the energy in these
inductors. The energy stored in Co provides energy to the load. The return current is split only between
Db and Dq2. |
Interval 3 [t2 −t3 ]: At t2 , Q1/Q2 are off again, and interval 1 is repeated, as shown in Fig. 13. During
this interval, the current in series inductances L1 and L2 decreases linearly, and the energy in these
inductors are released. The energy stored in L1 and L2 is released to the output through L1, D1, partially
Dq2, L2, and Db. |
Interval 4 [t3 −t4]: At t3 , Q1 is off, and Q2 is on, as shown in Fig. 15. During this interval, the energy
stored in L1 and L2 is released to the output through L1, D1, partially Q2, Dq2, L2, and Db. |
The operation of the converter during the negative input voltage half-cycle is similar to the operation of the
converter during the positive input voltage half-cycle. |
EXPERIMENTAL RESULTS |
The proposed PSSB boost PFC converter was designed In MATLAB R2009a software. |
The efficiency of the phase-shifted bridgeless boost converter, interleaved boost converter, and
conventional bridgeless boost converter are provided and in Fig.17 120V to 240 V input at 60Hz
MOSFET1 & MOSFET2 operating at 180 Deg out phase shift operation. The duty cycle of 0.6 to1% of
each MOSFET switching’s. In proposed method the two MOSFETs are operated at 180 deg out of phase it
enables the usage of advanced current synthesizing method. This phase shifting techniques cannot be used
either the bridgeless or dual boost topology because all controllers available for these topologies require
full input current shape sensing. Finally proposed topology achieved the power factor correction at input
side and boosts the output voltage with higher efficiency at the output side. |
CONCLUSION |
A high-performance PSSB ac–dc boost PFC converter topology has been proposed to simplify t he currentsensing
technique for t he semi-bridgeless PFC converter. The converter features high efficiency at lightload
and low-line conditions, which is critical to minimize the charger size, cost, charging time, and amount
and cost of electricity drawn from the utility.Theconverter power factor was also provided at full load for
120V and 240 V input. The power factor is greater than 0.99 from 50% load to full load. The proposed
converter achieves a peak efficiency of 98.8% at 265 V input and 1 kW output power. |
Figures at a glance |
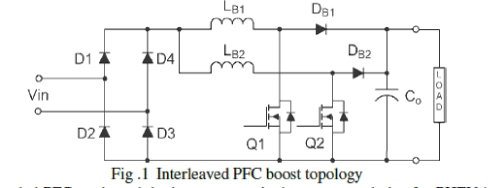 |
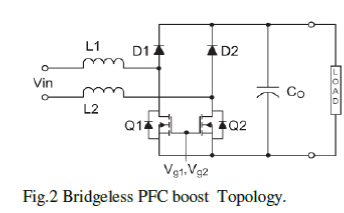 |
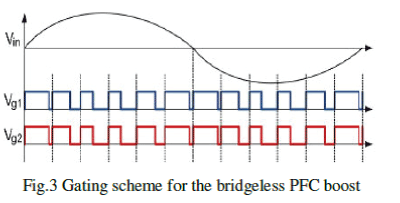 |
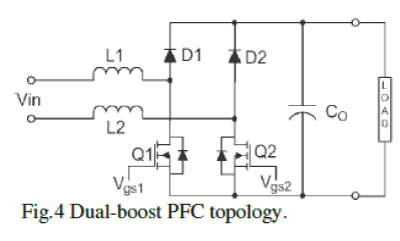 |
 |
Figure 1 |
Figure 2 |
Figure 3 |
Figure 4 |
Figure 5 |
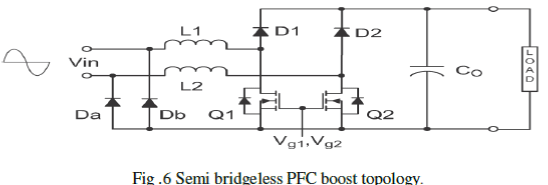 |
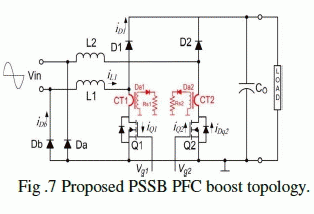 |
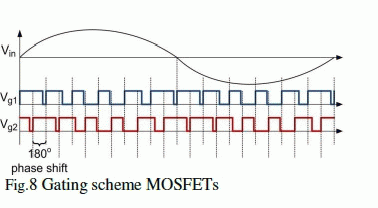 |
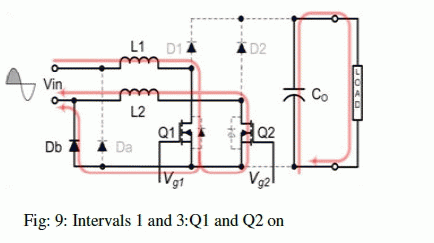 |
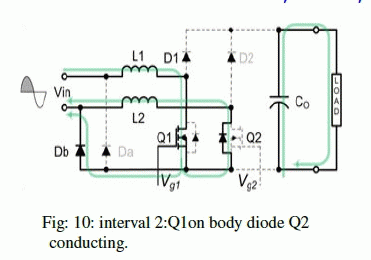 |
Figure 6 |
Figure 7 |
Figure 8 |
Figure 9 |
Figure 10 |
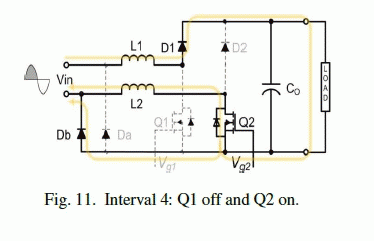 |
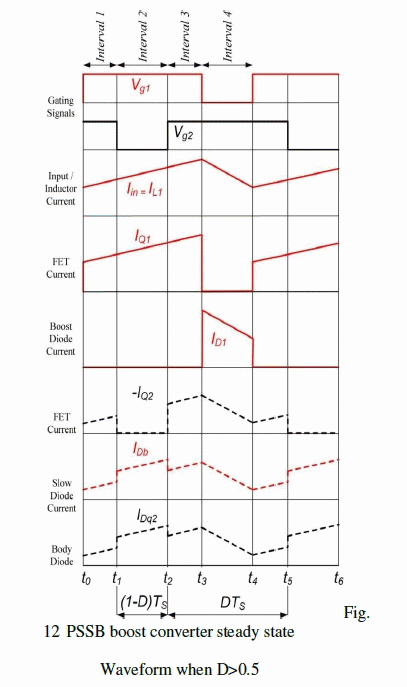 |
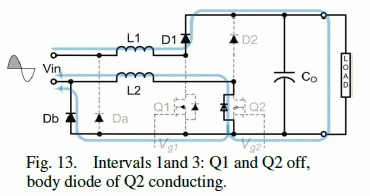 |
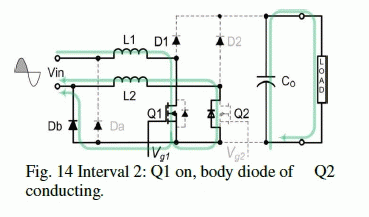 |
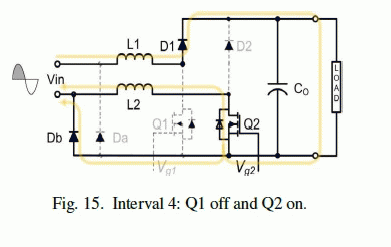 |
Figure 11 |
Figure 12 |
Figure 13 |
Figure 14 |
Figure 15 |
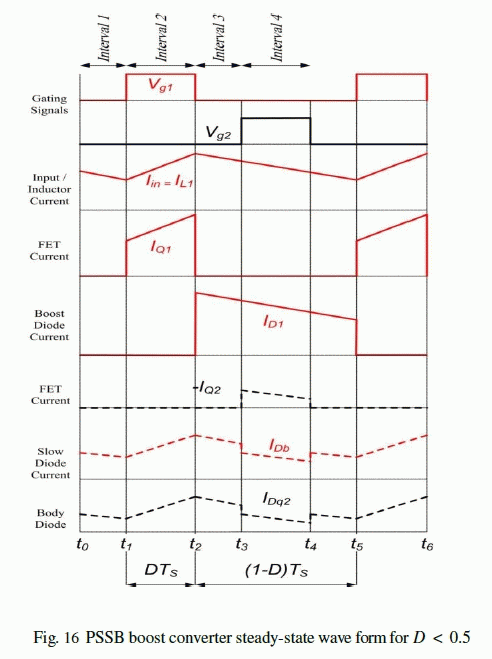 |
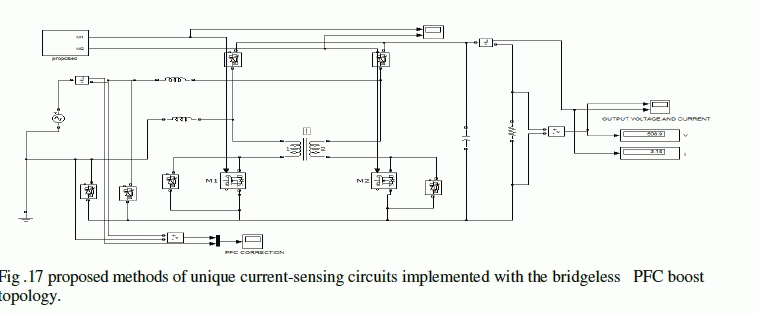 |
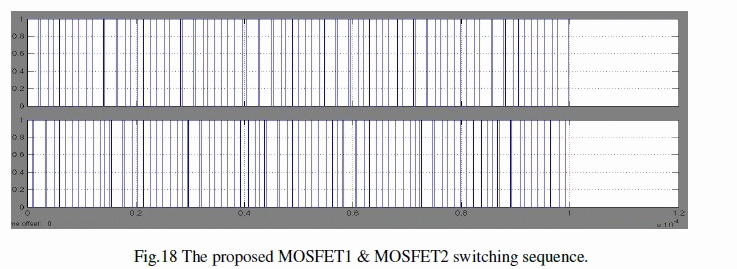 |
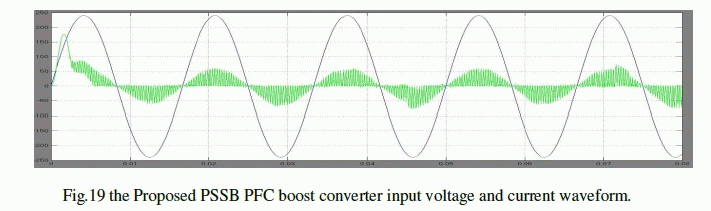 |
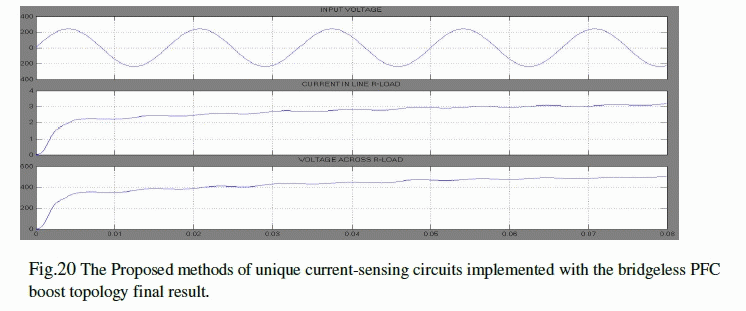 |
Figure 16 |
Figure 17 |
Figure 18 |
Figure 19 |
Figure 20 |
|
|
References |
- Y. J. Lee, A. Khaligh, and A. Emadi, ?Advanced integrated bidirectional AC?DC and DC?DC converter for plug-in hybrid electric vehicles,?IEEE Trans. Veh. Technol., vol. 58, no. 8, pp. 3970?3980, Oct. 2009.
- K. Morrow, D. Karner, and J. Francfort, ?Plug-in hybrid electric vehicle charging infrastructure review,? U.S. Dept. Energy?Veh. Technol. Program,Washington, DC, 2008.
- L. Petersen and M. Andersen, ?Two-stage power factor corrected power supplies: The low component- stress approach,? in Proc. IEEEAPEC, 2002, vol. 2, pp. 1195?1201.
- B. Singh, B. N. Singh, A. Chandra, K. Al-Haddad, A. Pandey, and D. P. Kothari, ?A review o single phase improved power quality AC?DCconverters,? IEEE Trans. Ind. Electron., vol. 50, no. 5, pp. 962?981, Oct. 2003.
- M. O?Loughlin, ?An interleaved PFC preregulator for high-power converters,? in Proc. Texas Instrum. Power Supply Design Semin., 2007, pp. 5-1?5-14.
- Y. Jang and M. M. Jovanovic, ?Interleaved boost converter with intrinsic voltage-doubler characteristic for universal-line PFC front end,? IEEETrans. Power Electron., vol. 22, no. 4, pp. 1394?1401, Jul. 2007.
|