Keywords
|
Induction motor, Characteristic Frequency, Fast Fourier Transform, MCSA. |
INTRODUCTION
|
Induction motors are a critical component of many industrial processes and are frequently integrated in commercially available equipment and industrial processes. Motor-driven equipment often provide core capabilities essential to business success and to safety of equipment and personnel. There are many published techniques and many commercially available tools to monitor induction motors to insure a high degree of reliability uptime. In spite of these tools, many companies are still faced with unexpected system failures and reduced motor lifetime. The studies of induction motor behaviour during abnormal conditions and the possibility to diagnose these conditions have been a challenging topic for many electrical machine researchers. MCSA is the best possible option: it is non-intrusive and uses the stator winding as the search coil. It is not affected by the type of load and other asymmetries. |
BEARING FAULTS TYPE
|
The faults occurs in motor bearing is generally due to the excessive load, rise of temperature inside the bearing, use of bad lubricant and so on [7]. The bearing consists of mainly of the outer race and inner race way, the balls and cage which assures equidistance between the balls. The different faults that may occur in bearing can be classified according to the affected element [3] [7]: |
Outer raceway defect |
Inner raceway defect |
Ball defect |
MOTOR CURRENT SIGNATURE ANALYSIS
|
Motor Current Signature Analysis (MCSA) is based on current monitoring of induction motor therefore it is not very expensive. The MCSA uses the current spectrum of the machine for locating characteristic fault frequencies. When a fault is present, the frequency spectrum of the line current becomes different from healthy motor. Such a fault modulates the air-gap and produces rotating frequency harmonics in the self and mutual inductances of the machine. It depends upon locating specific harmonic component in the line current [4] [5]. Therefore, it offers significant implementation and economic benefits. In the research work, Motor Current Signature Analysis (MCSA) based methods are used to diagnose the common faults of induction motor such as broken bar fault, short winding fault, bearing fault, air gap eccentricity fault, and load faults. The proposed methods in the research allows continuous real time tracking of various types of faults in induction motors operating under continuous and variable loaded conditions. The effects of various faults on current spectrum of an induction motor are investigated through experiments. |
EXPERIMENTAL SETUP
|
In order to diagnose the bearing fault of induction motor, same laboratory test bench is used as shown in Figure 2. It consists of single phase induction motor, current transformer, NI data acquisition card 9203 and Personnel Computer with software LabVIEW 2011. |
Induction motor specifications: |
0.25 hp, |
220/230 V, |
1.2 A |
1500(NL) r/min |
Current transformer specifications: |
Ratio 30 A/100 mA
|
Burden 2 VA |
Class 1 |
NI 9203 DAQ card specifications: |
±20 mA |
8 channels |
16 bits |
Ball bearing 6203-Z specifications:
|
Number of ball element: 8 |
Pitch diameter: 29.75 mm |
Ball diameter: 6.35 mm |
The bearing of the induction motor are single row, deep groove ball bearing, and type 6203-Z. Each bearing has eight balls. Experiments were conducted on three bearings: one of these is undamaged while two bearing were damaged. One bearing was drilled through outer race with „hole diameterâÃâ¬ÃŸ of 2 mm while another one bearing drilled through inner race with „hole diameter’ of 2 mm as illustrated in Figures 3 and 4. Bearings of type 6203-Z were drilled with help of Electric Discharge Machine (EDM) and were installed on motor. |
To detect the bearing fault, FFT based power spectrums were used. The spectrums were obtained using Virtual Instrumentation (VI). The VI was built up by programming in LabVIEW. The VIs was used both for controlling the test measurements and data acquisition, and for the data processing. The stator current is first sampled in the time domain and in the sequence; the power spectrum is calculated and analysed aiming to detect specific frequency components related to incipient faults. For each bearing fault, there is an associated frequency that can be identified in the spectrum. The faults are detected comparing the amplitude of specific frequencies with that for the same motor considered as healthy. Based on the amplitude in dB it is also possible to determine the degree of faulty condition. The currents that flow in the single phase induction motor are sensed by current transformer. It decreased the current to 3-4 mA. It is then further supplied to National Instrument Data acquisition card 9203. Data acquisition card is connected to USB 2.0 slot of personnel computer. Angular velocity of induction motor is measured by a digital tachometer. The |
“LabVIEW program” converts the sampled signal whose frequency is 1000 samples/s to the frequency domain using power spectrum algorithm. |
CHARACTERISTIC FREQUENCIES of BALL BEARING
|
Each defect present in a ball bearing assembly produces vibration at a basic frequency, or some complex combination of several basic frequencies. More severe defects may produce vibrations of greater amplitudes and result in harmonics. For defects on the raceway of a ball bearing, each time a roller hits the defective raceway, the corresponding ball pass inner raceway frequency fBPFI or ball pass outer raceway frequency fBPFO will be generated [5]. |
(1) |
(2) |
Where: |
n = Number of balls |
N = rotational speed in RPM |
d = Ball diameter |
D = Bearing pitch diameter |
β = Ball contact angle with the race |
RESULTS
|
The experiments have been performed to detect bearing faults in single phase induction motor using LabVIEW software. The power spectrum of healthy motor is obtained for all the cases as shown in Figures 5 and 8. The induction motor is tested with two defective bearings. Defective rolling element bearing generate eccentricity in the air gap with mechanical vibrations. The air gap eccentricity causes variation in the air gap flux density that produces visible changes in the stator current. These changes are determined in power spectrums of motor due to inner race fault and outer race faults. The outer race faults and inner race faults are diagnosed under no load and full load conditions by conducting some experiments. The results obtained from these experiments are given below: |
A. Inner Race Fault |
The motor is tested under no load condition with faulty bearing. The fault in bearing was made by drilling a hole of 2mm diameter in its inner race. It is observed from the power spectrums of motor that fault frequencies are not clearly visible at no-load condition because their magnitude is less. The power spectrum of faulty motor with 2mm hole in inner race of bearing under no load condition is shown in Figures 6. When the motor is tested again with same bearing under full load condition, it is observed that magnitude of fault frequencies are decreases but these are slightly difficult to identify in the power spectrum. The power spectrum of faulty motor with 2mm hole in inner race of bearing under full load condition is shown in Figures 9. The power spectrums for 2mm inner race fault of motor are shown in Figures 6 and 9 and their analysis for no load and full load is summarized in Table 1. |
B. Outer Race Fault |
The motor was also tested with outer race fault of bearing. Initially, the 2mm diameter of hole was drilled in the outer race of bearing and then it was installed in the motor. The power spectrum of faulty motor with 2mm hole in outer race of bearing under no load condition is shown in Figure 7. This figure shows that fault frequencies can be clearly identified in power spectrum at 77.55 Hz. Similar results are obtained from the experiment when the motor was tested with same fault under full load conditions. In this case, the fault frequencies are appearing at 77.34 Hz which is indication of outer race fault of bearing. Such frequencies are shown in Figure 10. Table 2 gives power spectrum analysis for induction motor with 2mm outer race fault. |
CONCLUSION
|
This work consists of experimental characterization of bearing faults in induction motors operating under no-load and full load conditions. The fault algorithm monitors the amplitude of fault frequencies and tracks changes in their amplitudes over time. A significant change in the amplitudes indicates a developing fault. Bearing fault is practically implemented and their effects on motor's current are studied with help of FFT signal conditioning technique. The NI LabVIEW software is used to study these effects. In bearing fault, harmonic shows a significant change when fault is applied. Defective rolling element bearings generate eccentricity in the air gap with mechanical vibrations. The air gap eccentricities cause vibrations in the air gap flux density that produces visible changes in the stator current spectrum. The signal processing technique (FFT) is applied to detect the bearing fault of motor. Experimental results show that the characteristic frequencies could not seen in the power spectrum if outer race fault and inner race fault is small in size. As severity of fault increases, the characteristic frequencies become visible. The results also show that, for defective bearing having 2 mm diameter hole, the inner race and outer race fault frequencies are slightly difficult to identify in power spectrum at no load condition. As load is increased, fault frequencies become visible. |
ACKNOWLEDGMENT
|
express my sincere thanks to my mentor, Mrs. Meera A. Khandekar for her expert guidance, encouragement and motivation during the development of this work, without which this work would not have developed to its present form. I am thankful to Dr. S. L. Patil for his support and help. Last but not the least; I am grateful for the endurance from my family and friends who silently supported me. |
Tables at a glance
|
 |
 |
Table 1 |
Table 2 |
|
|
Figures at a glance
|
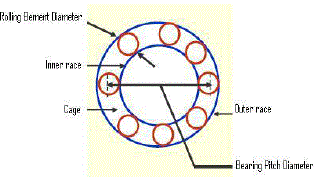 |
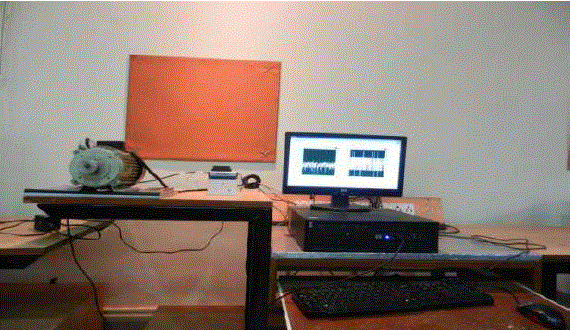 |
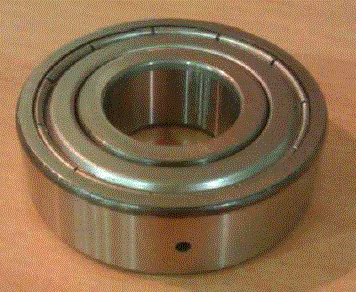 |
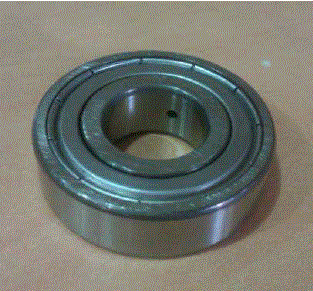 |
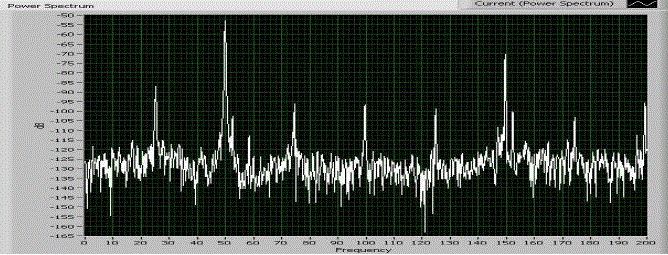 |
Figure 1 |
Figure 2 |
Figure 3 |
Figure 4 |
Figure 5 |
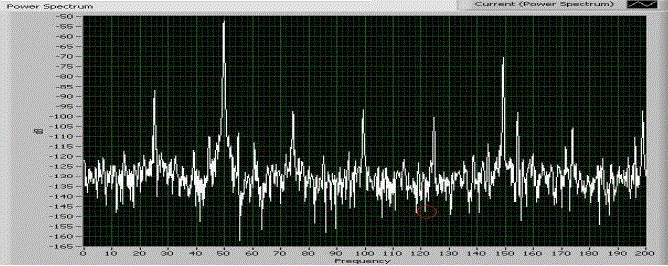 |
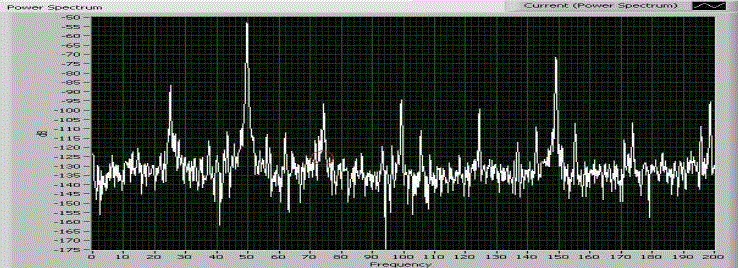 |
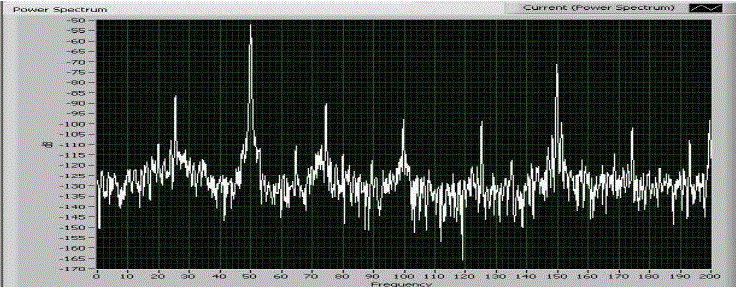 |
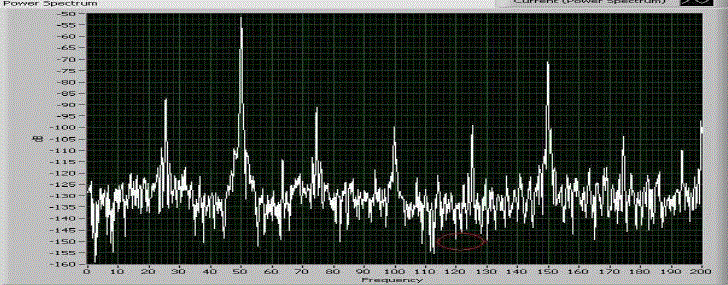 |
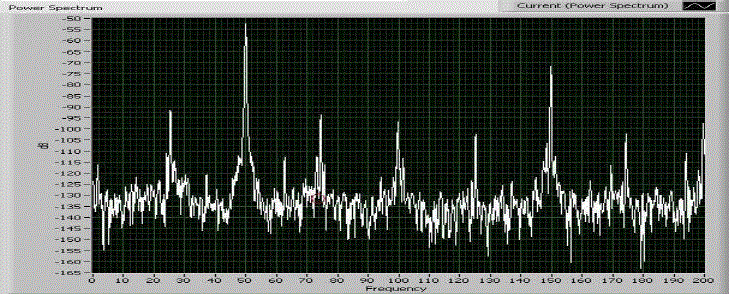 |
Figure 6 |
Figure 7 |
Figure 8 |
Figure 9 |
Figure 10 |
|
|
References
|
- AkshatSinghal, Meera A. Khandekar “Bearing Fault Detection In Induction Motor Using Fast Fourier Transform” IEEE International Conference on Advanced Research in Engineering and Technology 2013.
- P. F. Allbrecht, J. C. Appiarius, and R. M. McCoy, et al, “Assessment of the reliability of motors in utility applications – updated,” IEEE Transactions on Energy Conversion, Vol. 1, No. 1, pp. 39-46, 1986.
- Riddle J, “Ball bearing maintenance”, Norman, OK University of Oklohama Press, 1955.
- W. T. Thomson and R. J. Gilmore, “Motor current signature analysis to detect faults in induction motor derives-Fundamentals, data interpretation, and industrial case histories, proceedings of 32nd Turbo machinery symposium, Texas, A&M university, USA, 2003..
- Benbouzid, M. E. H., “A review of induction motors signature analysis as a medium for faults detection”, IEEE Transactions on Industrial Electronics, Vol. 47, October, No.5, pp. 984-993, 2000.
- Randy R. Schoen, Th omas G. Habetler, Farrukh Kamran and Robert G. Bartheld, “Motor bearing damage detection using stator current monitoring”, IEEE Transactions on Industry Applications, Vol. 31, No 6, pp. 1274-1279, 1995.
- Eschmann P, Hasbargen L, Weigand K, “Ball and roller bearings: Their theory, design, and application” (London: K G Heyden), 1958.
|