Keywords
|
Embedded Design, IR Sensor, Microcontroller, prototype, Triac BT134. |
INTRODUCTION
|
In recent years, many researchers have been studied on infrared technology based device control by using microcontroller system [1]. Due to the different applicability and inherent limitations of embedded system design technologies, researchers have been working on different scenarios with enhanced designof calibration. In their paper, they used ATMEL AVR which was less compact and required to design dedicated infrared remote transmitter, besides the system was less flexible to modify for other control applications. Moreover, the power consumption and speed are the key factor for device applications. The control of the load and smooth operation are also the important factor. In this paper, we developed an embedded design of IR based device control by using Microcontroller IC PIC 16F690 system which has much lower power consumption, compact design and much faster conversion speed than ATMEL AVR. |
In addition, this embedded design is an advanced automation system developed to control the appliances in the house by manually and remotely. Both systems are installed in the same circuit which can control the same connected load separately. This designing completely automated switch board with the help of Infrared technology with manual switch to control the house hold connected devices. |
HARDWARE IMPLEMENTATION
|
In this system, devices are controlled through Infrared technology as well as manual switch which are interfaced with the controller. We can control any device by using this method. In this experiment, we controlled the ON/OFF switches through Infrared technology and manual switch. |
Fig.1 shows the functional block diagram of the total architecture of the system. The device consist of blocks namely IR transmitter, IR receiver, microcontroller, manual switch, and driver circuit |
In this block diagram shows the transmitter circuit which is works at 3V power supply, built around Dotted IC and operated by NEC protocol. Fig. 2 shows the NEC IR transmission protocol uses pulse distance encoding of the message bits. Each pulse burst (mark – RC transmitter ON) is 562.5μs in length, at a carrier frequency of 38 kHz (26.3μs). Logical bits are transmitted as follows: When Logical '0' – a 562.5μs pulse burst followed by a 562.5μs space, with a total transmits time of 1.125ms. When Logical '1' – a 562.5μs pulse burst followed by a 1.6875ms space, with a total transmit time of 2.25ms. Address and command are transmitted twice for reliability [2]. |
A command is transmitted only once, even when the key on the remote control remains pressed. Every 110ms a repeat code is transmitted for as long as the key remains down. This repeat code is simply a 9ms AGC pulse followed by a 2.25ms space and a 560μs burst. Its transmission wavelength lies between 900 to 1100nm (near IR range) that lies in the peak receptivity range of TSOP1738 receiver module. |
The receiver circuit of the system which comprises of IR sensor TSOP1738, power supply and manual switches. The receiver and transmitter circuit should be aligned face to face so that the IR rays get interrupted when someone stands in between the two. As long as the IR beams falls on the sensor, its output remain low, transistor does not conduct. When anyone interrupts the IR beam falling on the sensor, its output goes high to drive the transistor into conduction. All the data collected about different users will be fed into the micro controller through IC PIC 16F690. |
The architecture of the system also controls the connected load through the manual switch which is directly interfaced with controller. Microcontroller will process this information and accordingly ON/OFF the devices. Fig. 3 shows the hardware implementation of receiver side which represents IC PIC 16F690, TSOP 1738, embedded system, Traic BT134, capacitance power supply system are used in this hardware. |
METHODOLOGY
|
Fig.4 shows the circuit design with manual switch of the system which was based on neutral connection cause of BT 134 has npntriac.That isdrive by neutrally. Power source is connected through non polar Capacitor which one pin is connected by neutral and other pin is connected by 24 volt power source. As per requirement of capacitor output, the voltages step down from 24V to 5V by using 5.1V Zener diode. This 5 volt operational voltage is required for operated inIC PIC 16F690. |
The Infrared signal comes from Transmitter side then the Receiver side gets the digital signal by using sensor TSOP 1738 [3]. When IR waves come from a source, with a centre frequency of 38 kHz incident on it, its output goes low. The output of TSOP is active low and it gives +5V in off state. TSOP module has an inbuilt control circuit for amplifying the coded pulses from the IR transmitter. A signal is generated when PIN photodiode receives the signals. This input signal is received by an automatic gain control (AGC). For a range of inputs, the output is fed back to AGC in order to adjust the gain to a suitable level. The signal from AGC is passed to a band pass filter to filter undesired frequencies. After this, the signal goes to a demodulator and this demodulated output drives an npn transistor. The collector output of the transistor is obtained at pin 3 of TSOP module. |
We used zero crossing detectors in this program for the accuracy of starting voltage. In alternating current, the zerocrossing is the instantaneous point at which there is no voltage present. In a sine wave or other simple waveform, this normally occurs twice during each cycle. Because abnormal voltages are harmful for circuit reliability. A zero crossing detector literally detects the transition of a signal wave form from positive and negative, ideally providing a narrow pulse that coincides exactly with the zero voltage condition. It is mentioned that the pulse width modulation (PWM) system was built in with this diode which controlled our analog device speed [4]. |
BT 134 triacs has Glass passivatedtriacs in a plastic envelope, intended for use in applications requiring high bidirectional transient and blocking voltage capability and high thermal cycling performance [5]. Typical VDRM Repetitive peak off-state applications include motor control, voltages industrial and domestic lighting, heating and static switching. Thecapacitive power supply was used for consuming power loss in this circuit. |
From TSOP 1738 sensor sends the IR signal to IC PIC 16F690 which Pins are connected through BT 134 Triac. BT 134Triacs are individually connected to the separate loads. User can transmit the signal to the receiver side for drive the loads by controlling BT134 Triac. This controlling language is installed to the microcontroller. User can drive the loads which they want by the system language without any interference. The power control device used here is a Triac BT134 being least expensive power switch to operate directly on the 110/240V mains. Thus it is the optimal switch for most of the low-cost power applications operating online. It can withstand a maximum load current typically 5A. Phase angle control technique is employed to control the load power. The output power is controlled by the phase delay of the Triac drive. This delay is referred to the zero crossing of the line voltage detected by Zero crossing detector circuit. This process repeated on each connected loads. |
It is also notable that this system controls the connected load through the infrared technology as well as manual switch system which are interfaced with controller via BT134 Triac.The design consists of a microcontroller, which is interfaced with the input and output modules, Order of switching the devices will be programmed predefined in the IC. |
SIMULATION RESULT
|
The micro controller along with its various interfaces requires software to work on. Assembly language software for the micro controller was developed using Micro C [6]-[8]. This consists of a project manager, text editor and simulator. Assembly language code was written using the text editor, and then compiled into hexadecimal form for downloading into the microcontroller. The simulator proteus was used for testing of program functions although this was very limited due to the nature of the simulator. |
If 80W load was connected through the dimmer channel and setting values to dimmer were incremented. After each new value was set, the voltage at that channel’s output was different which is measured with multimeter. The observed data is given in table 1. |
From table 1 it is observed that each channel of the dimmer output can take on any voltage between 10.7% and 98.7% of full scale and it can be used as transformer less variable power supply. The resolution for stepping voltage can be changed by adjusting the timer setting in microcontroller. |
At a cost of only 35% increases of power supply current for the microcontroller then achieve a net reduction in the circuit current drawn over to 63%. The results in a significant savings in power dissipated in the transformer less variable power supply. |
We can find timer setting 65455 & measured value 218.2 at that time any connected load is on & full voltage activated. When load off, shown in Table 1 voltage was zero. If measure another load of 100W which was connected through the system then gets the accurate test result by oscilloscope is shown in Fig.5.It is revealed that when the pick value of sign wave was high, the square wave of the load also high and in this situation load is on. Otherwise load is off. |
By using this process we get the result of others connected loads which result verify by oscilloscope. From oscilloscope we seen, if our transmitted signal voltage will be matched our programming voltage that time we get the accurate output. |
In this system has designed by manual switch which interfaced to the microcontroller. The manual switch sends the ON/OFF commands to the microcontroller where loads are connected via the BT 134 Triac thenthe loads can be turned ON/OFF and see the output results directly which loads are connected through the system.This design provides a user friendly environment of the user to operate the devices effectively. |
CONCLUSION
|
Embedded Design of IR Based device control by Using microcontroller System has been studied. The simulation result showed that this system is lower power consumption, faster and operated by multiple loads which are connected through the system. These systems are simplicity, low cost, Easy to installation, less interference and small size. It might be used in home appliances in future. |
ACKNOWLEDGEMENTS
|
The author would like to acknowledge the help of K. M. A. Salam, North South University for help on gathering current information on Embedded System Design. |
|
Tables at a glance
|
 |
Table 1 |
|
|
Figures at a glance
|
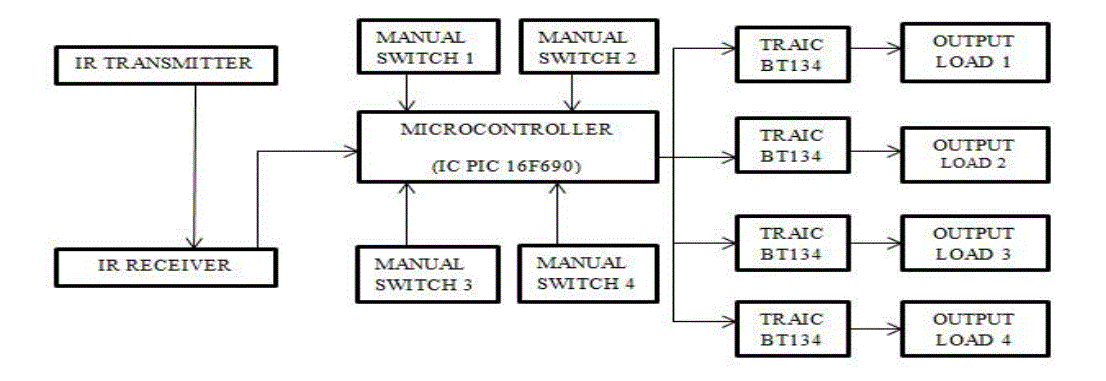 |
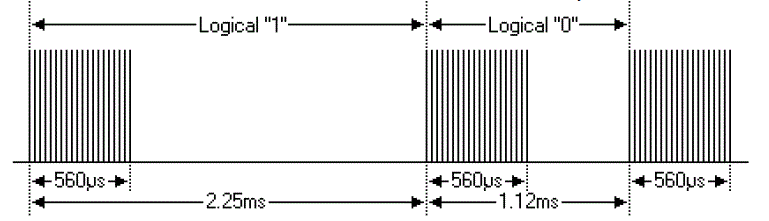 |
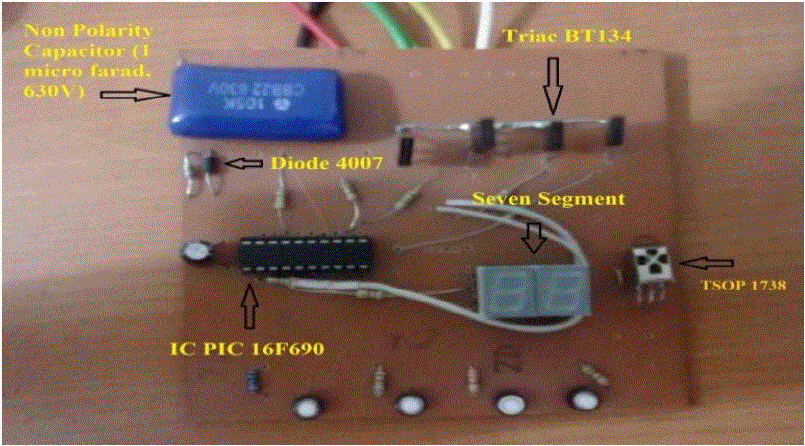 |
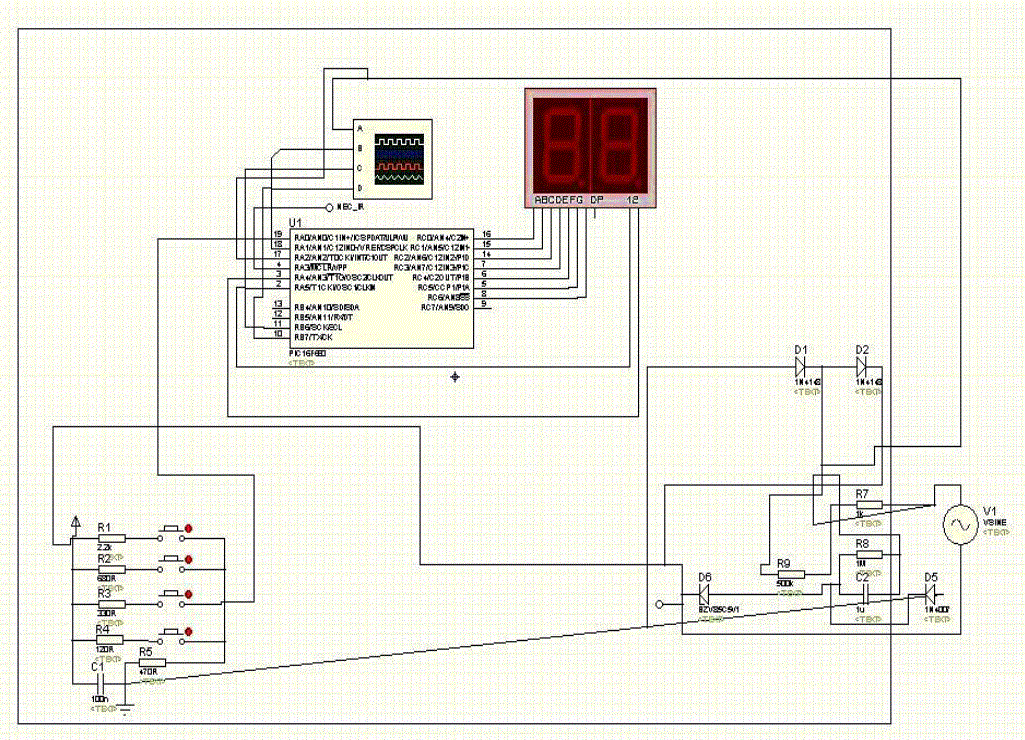 |
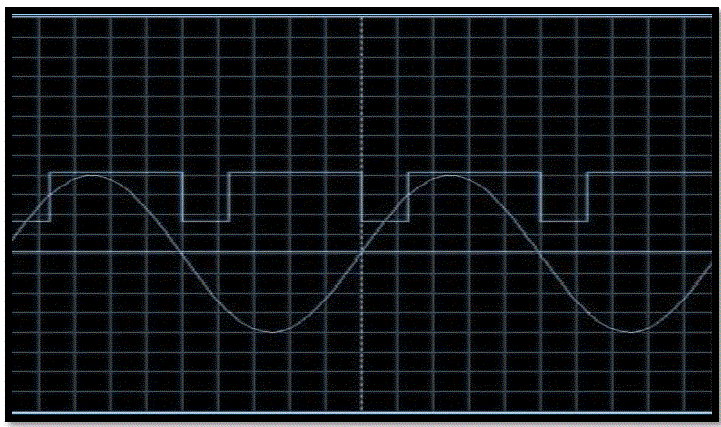 |
Figure 1 |
Figure 2 |
Figure 3 |
Figure 4 |
Figure 5 |
|
|
References
|
- ShahanazAyub, J.P.Saini, “Advances in Applied Science Research,” 1(2), pp. 76-83, 2010.
- Bergmans S., Oisterwijk, Sony SIRC Protocol [online], available at: http://www.sbprojects.com/knowledge/ir/sirc.htm.
- TSOP 1738 Datasheet, Available at: http://batronix.com/pdf/tsop17xx.pdf.
- Philips Semiconductors Application note, Power Control with Thyristors and Triacs [online], available at:http://www.fairchildsemi.com/an/AN/AN-3006.pdf
- BT 134 Triac Datasheet, available at: http://pdf.datasheetcatalog.com/datasheet/philips/BT134_SERIES_E_1.pdf.
- Tim wilmshurst, “Designing Embedded System with PIC Microcontroller,” Second Edition, 2010.
- Dr. Richard Bernatt,“Embedded C Programming and the Microchip PIC,” Volume 1, 2006.
- Chuck Hellebuyck, “A Beginner’s Guide to Embedded C Programming,” Lite C Compiler, 2008.
- JoonKee Cho, DongRyeol Park, and Yeon-ho Kim, “A method of remote control for home appliance using hand gesture,” IEEE Journal.
- C. Suh and Y.B. Ko, “Design and Implementation of Intelligent Home Control Systems,” IEEE Transactions on Consumer Electronics, Vol.54, No.3, Aug. 2008.
- Keller.T, Paczkowski, and R.Modelski J, “Using Bluetooth in a system for integrated control of home digital network devices,” IEEE journal.
|