Keywords
|
Direct torque control, PI controller, particle swarm optimization. |
I.INTRODUCTION
|
AC induction motors are the most common motors used in industrial motion control systems, as well as in domestic applications. Simple and rugged design, low-cost, low maintenance and direct connection to an AC power source are the main advantages of AC induction motors. Controlling the speed of an induction motor is far more difficult than controlling the speed of a DC motor since there is no linear relationship between the motor current and the resulting torque in the case of a DC motor. There are several methods to vary the speed of an induction motor over a wide range. The most modern technique is direct torque control method (DTC). The DTC offers many advantages like fast torque response, no need of coordinate transformation and less dependence on the rotor parameters. The conventional PI (proportional, integral) control method is widely used in motor control system due to the simple control structure and easiness of design. However tuning the parameters of PI controller is a difficult task. To enhance the capabilities of traditional PI parameter tuning techniques, several intelligent approaches have been suggested such as genetic algorithms (GA) and the particle swarm optimization (PSO). |
algorithms (GA) and the particle swarm optimization (PSO). Particle Swarm Optimization (PSO) is one of the modern algorithms used to solve global optimization problems. Thus, to solve an optimization problem, PSO applies a simplified social model. Compared to other methods, application of the PSO is simple to implement, it can quickly find a number of high quality solutions, and has stable convergence characteristics. The PSO method is an excellent optimization methodology and a promising approach for solving the optimal PI controller parameters problem. |
II. MATHEMATICAL MODELING OF INDUCTION MOTOR
|
The induction motor has been modelled by using the following equations. |
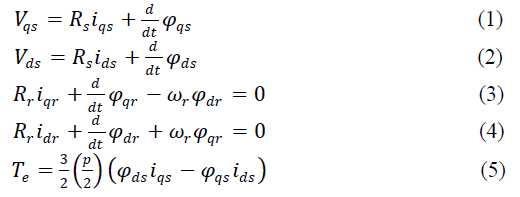 |
III.THREE PHASE VOLTAGE SOURCE INVERTER
|
The power circuit topology of a three-phase VSI is shown in Fig.1. S1 to S6 are the six power switches that shape the output, which are controlled by the switching variables a, a′, b, b′, c and c′. |
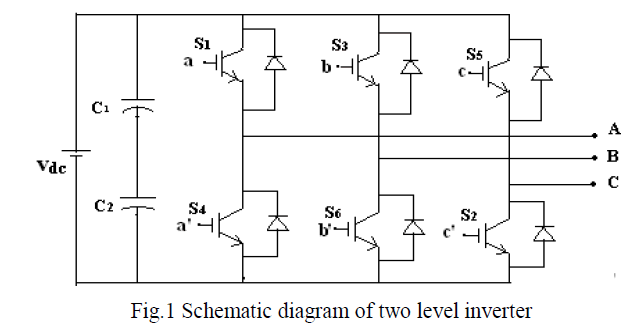 |
When an upper switch is on, i.e., when a, b or c is 1, the corresponding lower transistor is switched off, i.e., the corresponding a′, b′ or c′ is 0. Therefore, the on and off states of the upper switches S1, S3 and S5 can be used to determine the output voltage. The speed and electromagnetic torque of induction motor is controlled by the selection of optimal inverter switching modes. |
IV.DIRECT TORQUE CONTROL OF INDUCTION MOTOR
|
Block diagram of direct torque control of induction motor is shown in fig 2. |
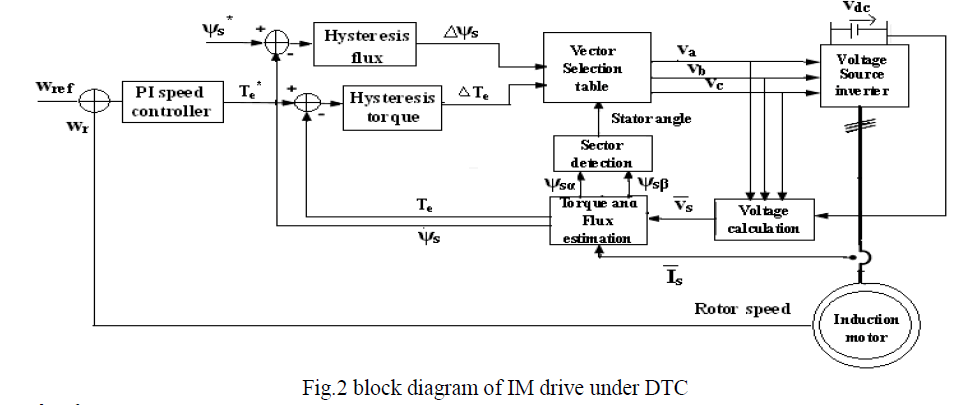 |
Principle of DTC |
The electromagnetic torque of 3-phase induction motor is given by, |
 |
Where ψr and ψs are the rotor and stator flux linkages and η is the angle between the fluxes and σ is the leakage coefficient. Block diagram of direct torque control of induction motor is shown in fig 2. The induction motor is fed by a three phase inverter consisting of six fast switching devices. |
The basic control algorithm of DTC is consisted with two independent hysteresis comparators producing the error signal of stator flux and electrical torque. And these error signals are incorporated with a switching table shown in table.1. The feedback signal for independent controllers come from the stator current and voltage space vectors. The voltage space vectors generated from inverter with the sensed dc link voltage the inverter drive signals. the angle of the stator flux vector is used to determine the voltage sector as shown on the fig 3. |
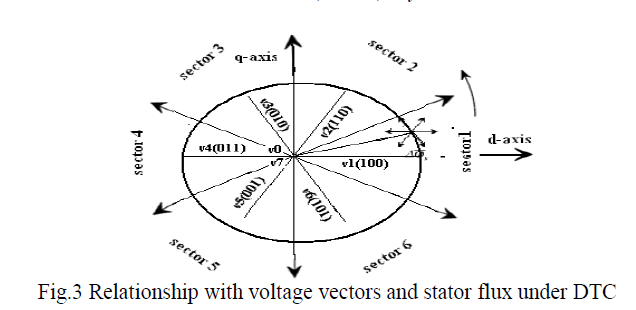 |
Six nonzero vectors (V1 - V6) shape the axes of a hexagonal as depicted in Fig. 2, and feed electric power to the load. The angle between any adjacent two non-zero vectors is 60 degrees. Meanwhile, two zero vectors (V0 and V7) are at the origin and apply zero voltage to the load. The eight vectors are called the basic space vectors and are denoted by V0, V1, V2, V3, V5, V6, and V7. Assuming the stator flux vector laid on the sector 1 of the d-q plane, V1, V2, V6 could be selected to increase the stator flux vectors. Conversely, V3, V4, V5 could be selected to decrease the stator flux vector. The zero (null) voltage vectors does not effect on the stator flux vector. Voltage vectors are selected to control the torque also. In general, V2 and V3 vectors can be selected to increase the torque and V5, V6, V0 vectors will decrease the torque. Table 1 shows voltage vector selection according to stator flux and torque errors. |
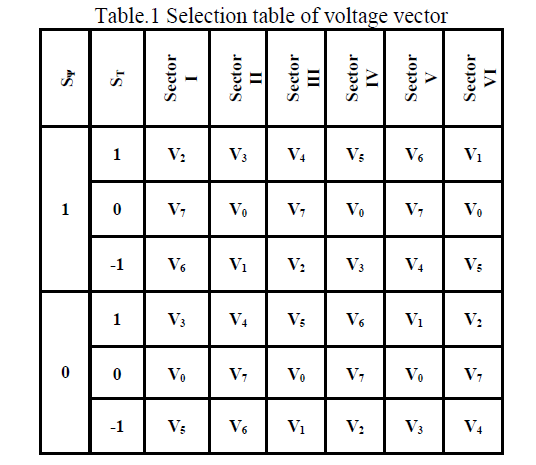 |
V. PARTICLE SWARM OPTIMIZATION
|
Particle swarm optimization is a heuristic global optimization method put forward originally by Doctor Kennedy and Eberhart in 1995. It is developed from swarm intelligence and is based on the research of bird and fish flock movement behaviour. |
PSO has two primary operators; velocity and position update. In this paper the main objective of PSO is minimization of speed error. Fig.4 shows the block diagram for PI controller and the corresponding objective function is as shown in equation (7) and (8). |
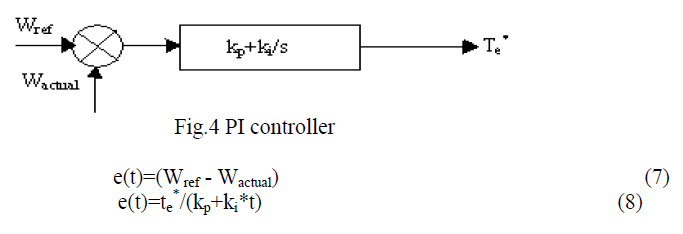 |
VI.PSO ALGORITHM
|
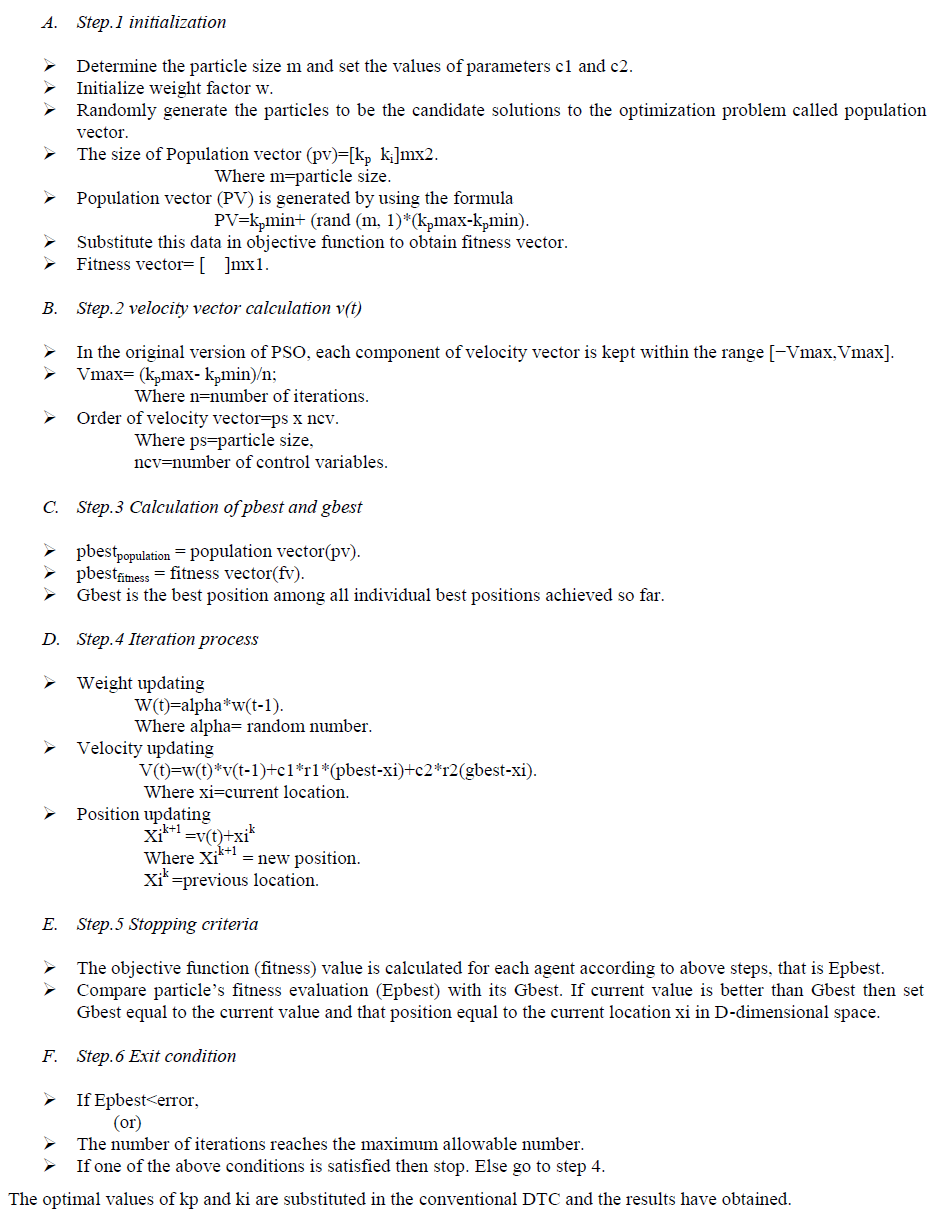 |
VII.RESULTS AND DISCUSSION
|
The optimized values obtained from PSO program is substituted in DTC system and the results have observed. To validate the performance of PSO based DTC different load torques has been applied as shown in fig 5(a), 6(a), 7(a), and 8(a). The motor speed waveforms related to the PSO based DTC in comparison with conventional PI based DTC are as shown in fig 5(b), 6(b), 7(b), 8(b). |
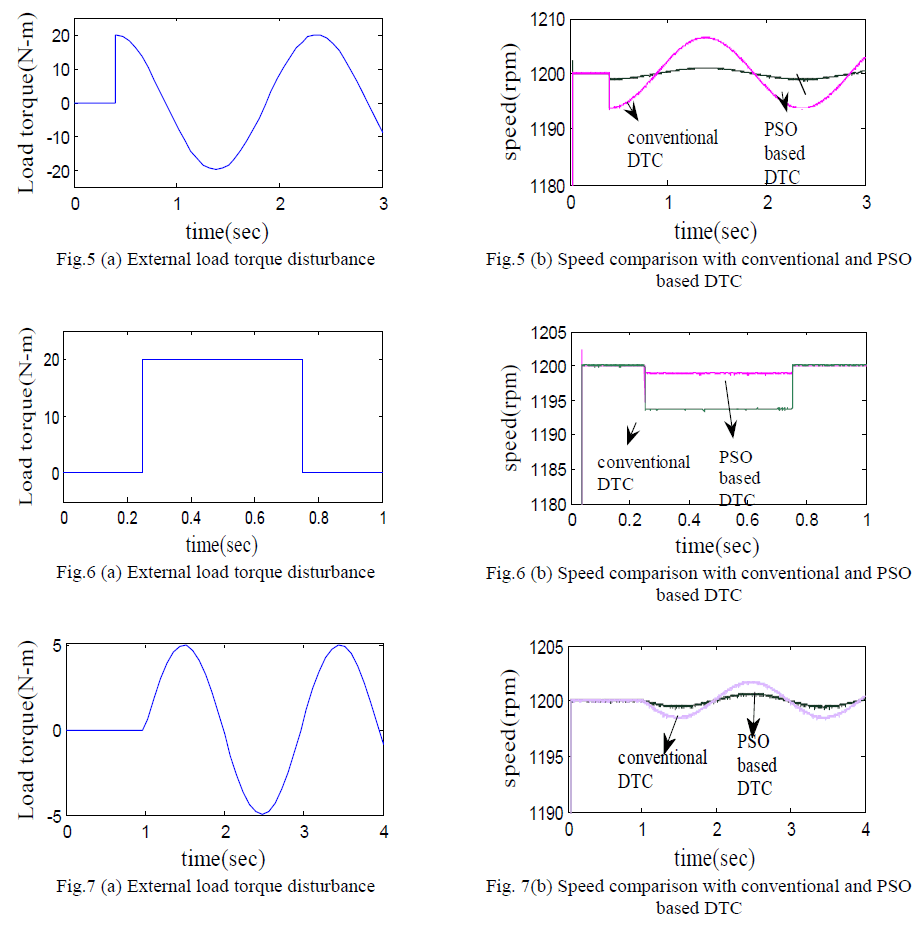 |
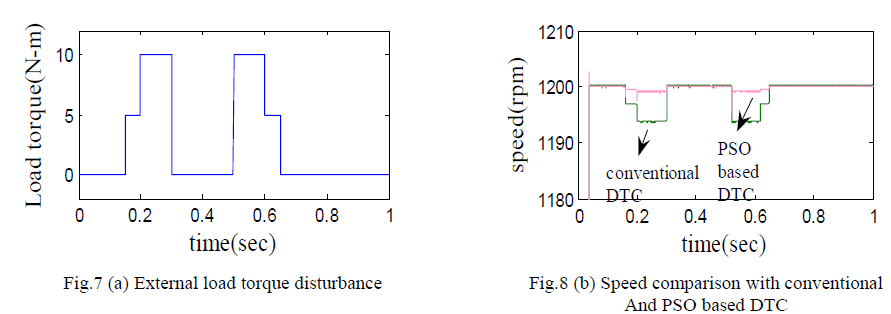 |
It has been observed that the speed performance of a PSO based DTC is better when compared with the conventional DTC. |
VIII.CONCLUSIONS
|
In this paper, the proposed PSO based DTC control scheme has been implemented. The simulation results of this method have improved the speed performance of the induction motor irrespective of the load torque fluctuations. The proposed PSO method has optimized the parameters of PI controller by minimizing the speed error. It can be concluded that the PSO algorithm employed in DTC of induction motor has resulted in the optimal generation of kp, ki values. This proposed method has finally improved the dynamic speed behaviour of the induction motor when compared with that of a Conventional PI controller based DTC of Induction motor. |
References
|
- Bo zhou, “Application of particle swarm optimization on DTC for induction motor”, IEEE DOI 10.1109/ICNC.2008.300
- O.S. EI-Laban , H.A. Abdel Fattah, H.M.Emara, and A.F.Sakr, “partical swarm optimized direct torque control of induction motors”. IEEETrans, 2006.
- M. A. Abido, “optimal power flow using particle swarm optimization”, electrical power and energy system vol.24,pp. 563-571,2002
- IoanCristianTreela. “the particle swarm optimization algorithm”: convergence analysis and parameter selection. Information processing Lett.,85(2003)317- 325.
- AhmudIwanSolihin, Lee Fook Tack and MoeyLeapKean. “Tuning of PID controller using particle swarm optimization” (PSO). 2011.
- Hassan FarhanRashag, S.P.Koh, Ahmed N. Abdalla, nadia M. L. Tan, K. H. Chong and S. K. Tiong, “ DTC torque ripple minimizationbased on PSO-PID controller”. Scientific research and Essay.,vol. 7,pp(15), 1564-1572, 2012.
- J. Kennedy and R. C. Eberhart, “ Particle Swarm Optimization,” in Proc. IEEE Int. of Neural Networks, Piscataway, NJ, USA, 1942-1948,1995.
- R. C. Eberhart and Y.Shi,“Guest editorial,” IEEE Trans. Evol. Comput. (Special Issue on Particle Swarm Optmization), vol. 8, pp. 201-203 no. 3, Jun. 2004.
- Eberhart R C, Shi Y. (1998). Comparison between genetic algorithms and Particle Swarm Optimization. Porto VW. SaravananN,WaagenD,etal.Evolutionary Programming VII.S.l.]:Springer,1998:611-616.
|